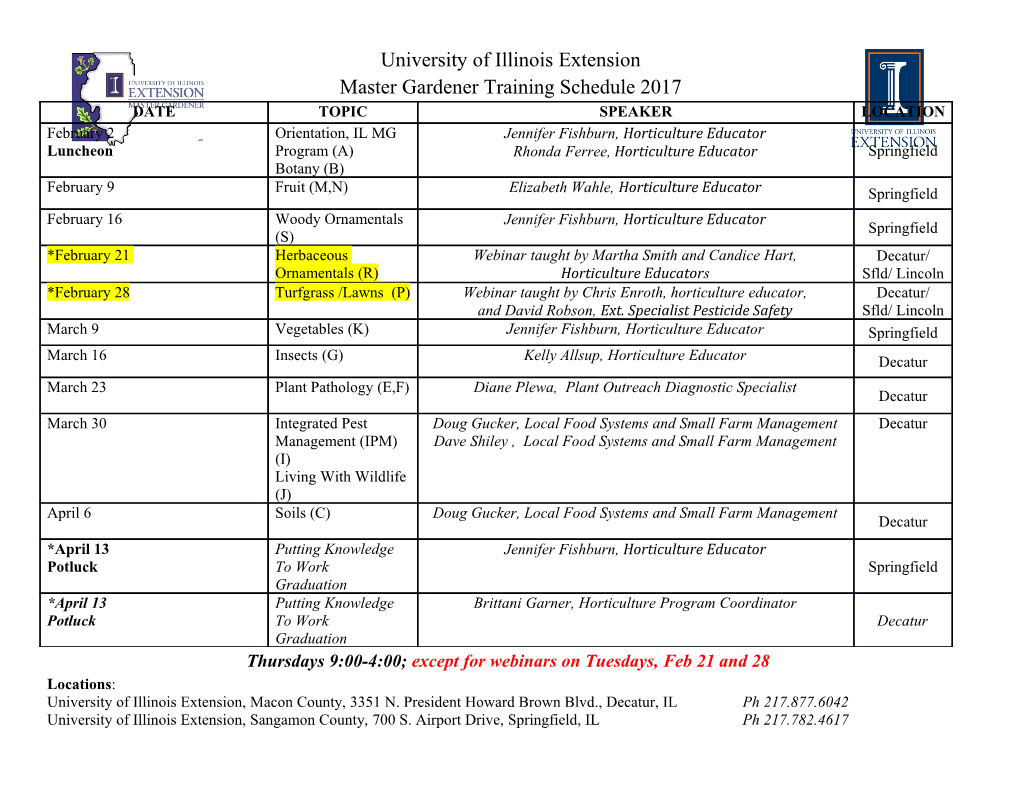
Carbon Dioxide Sequestration by Mineral Carbonation Wouter J. J. Huijgen Promotoren: prof. dr. R.N.J. Comans hoogleraar milieugeochemie Wageningen Universiteit prof. dr. G.J. Witkamp hoogleraar apparatenbouw voor de procesindustrie Technische Universiteit Delft Promotiecommissie: dr. P. Piantone BRGM, Frankrijk prof. dr. ir. W.H. Rulkens Wageningen Universiteit prof. dr. C.J. Spiers Universiteit Utrecht prof. dr. ir. C.A.P. Zevenhoven Åbo Akademi, Finland Dit onderzoek is uitgevoerd binnen de onderzoekschool SENSE. CARBON DIOXIDE SEQUESTRATION BY MINERAL CARBONATION PROEFSCHRIFT Ter verkrijging van de graad van doctor op gezag van de rector magnificus van Wageningen Universiteit, prof. dr. M.J. Kropff, in het openbaar te verdedigen op vrijdag 12 januari 2007 des namiddags te vier uur in de Aula. Carbon dioxide sequestration by mineral carbonation Huijgen, W.J.J. Thesis, Energy research Centre of the Netherlands, The Netherlands ISBN: 90-8504-573-8 Contents CONTENTS Summary 5 Samenvatting 11 Introduction and outline of thesis 19 Background 21 Carbon capture and storage 21 Mineral carbonation 23 Purpose and content of this thesis 26 Chapter 1 Carbon dioxide sequestration by mineral carbonation: Literature review 29 1.1 Introduction 32 1.2 Selection solid feedstock 33 1.2.1 Selection element 33 1.2.2 Selection mineral 33 1.3 Process routes mineral carbonation 38 1.3.1 Pre-treatment feedstock 38 1.3.2 Direct carbonation Mg/Ca-ores 40 1.3.3 Indirect carbonation Mg/Ca-ores 45 1.3.4 Carbonation processes industrial residues 52 1.4 Selection process route 54 1.5 Other aspects mineral CO2 sequestration 55 1.5.1 Process lay-out 55 1.5.2 Energy consumption & costs 56 1.5.3 Other environmental issues 57 1.6 Conclusions 59 Chapter 2 Mineral CO2 sequestration by steel slag carbonation 61 2.1 Introduction 64 2.2 Experimental section 66 2.2.1 Materials processing 66 2.2.2 Materials characterization 67 2.3 Results and discussion 69 2.3.1 Feedstock analysis 69 2.3.2 Mineralogy 70 2.3.3 Calcium speciation 70 2.3.4 Process variables 72 2.3.5 Reaction mechanisms 75 Annex 2.1 Supporting information 79 1 Chapter 3 Carbonation of steel slag for CO2 sequestration: Leaching of products and reaction mechanisms 81 3.1 Introduction 84 3.2 Materials and methods 85 3.2.1 Steel slag carbonation experiments 85 3.2.2 Characterization of leaching processes 86 3.2.3 Selective chemical extractions 87 3.2.4 Geochemical modelling 87 3.3 Results and discussion 89 3.3.1 Calcium and silicon 92 3.3.2 Magnesium, strontium, and barium 93 3.3.3 Reactive Al-, Fe-, and Mn-(hydr)oxide surfaces 95 3.3.4 Oxyanions and heavy metals 96 Annex 3.1 Supporting information 98 A.3.1.1 Effect of grinding 100 A.3.1.2 Effect of prior leaching in the autoclave reactor 100 A.3.1.3 Implications of leaching on the re-use possibilities of (carbonated) steel slag 101 Chapter 4 Mechanisms of aqueous wollastonite carbonation as a possible CO2 sequestration process 107 4.1 Introduction 110 4.2 Materials and methods 112 4.2.1 Wollastonite characteristics 112 4.2.2 Carbonation experiments 114 4.3 Results and discussion 117 4.3.1 Reaction mechanisms 117 4.3.2 Comparison to other carbonation feedstock 123 4.3.3 Process improvement 125 4.4 Conclusions 125 Annex 4.1 pHstat of (carbonated) wollastonite 126 Annex 4.2 Effect of salts 128 Annex 4.3 Development of aqueous wollastonite carbonation process 130 Chapter 5 Energy consumption and net CO2 sequestration of aqueous mineral carbonation 135 5.1 Introduction 138 5.2 Methods and assumptions 139 5.2.1 Process simulation 139 5.2.2 Feedstock batches 143 5.2.3 Carbonation degree 144 5.2.4 CO2 sequestration efficiency 145 5.3 Results and discussion 147 5.3.1 Wollastonite 147 2 Contents 5.3.2 Steel slag 152 5.3.3 Sensitivity analysis 154 5.3.4 Discussion 158 5.4 Conclusions 159 Annex 5.1 Supporting information 161 A.5.1.1 Purge fraction of process water recycling 161 A.5.1.2 CO2 loss 163 A.5.1.3 Comparison to other process studies and feedstock 163 Chapter 6 Cost evaluation of CO2 sequestration by aqueous mineral carbonation 165 6.1 Introduction 168 6.2 Materials and methods 170 6.2.1 Mineral carbonation process 170 6.2.2 Cost evaluation 172 6.3 Results and discussion 176 6.3.1 Wollastonite 176 6.3.1.1 Investment costs 176 6.3.1.2 Mineral CO2 sequestration costs 180 6.3.1.3 Sensitivity analysis and process optimisation 181 6.3.2 Steel slag 185 6.3.3 Comparison to other cost analyses 186 6.3.4 Discussion 188 6.4 Conclusions 189 Epilogue 191 Conclusions individual chapters 193 Discussion & conclusion 195 Further research 197 Notation 201 References 205 Dankwoord 219 Curriculum vitae 223 Publications 227 3 4 6 Summary SUMMARY The increasing atmospheric carbon dioxide (CO2) concentration, mainly caused by fossil fuel combustion, has lead to concerns about global warming. A possible technology that can contribute to the reduction of carbon dioxide emissions is CO2 sequestration by mineral carbonation. The basic concept behind mineral CO2 sequestration is the mimicking of natural weathering processes in which calcium or magnesium containing minerals react with gaseous CO2 and form solid calcium or magnesium carbonates: (Ca,Mg)SiO3 (s) + CO2 (g) ® (Ca,Mg)CO3 (s) + SiO2 (s) Potential advantages of mineral CO2 sequestration compared to, e.g., geological CO2 storage include (1) the permanent and inherently safe sequestration of CO2, due to the thermodynamic stability of the carbonate product formed and (2) the vast potential sequestration capacity, because of the widespread and abundant occurrence of suitable feedstock. In addition, carbonation is an exothermic process, which potentially limits the overall energy consumption and costs of CO2 emission reduction. However, weathering processes are slow, with timescales at natural conditions of thousands to millions of years. For industrial implementation, a reduction of the reaction time to the order of minutes has to be achieved by developing alternative process routes. The aim of this thesis is an investigation of the technical, energetic, and economic feasibility of CO2 sequestration by mineral carbonation. In Chapter 1 the literature published on CO2 sequestration by mineral carbonation is reviewed. Among the potentially suitable mineral feedstock for mineral CO2 sequestration, Ca-silicates, more particularly wollastonite (CaSiO3), a mineral ore, and steel slag, an industrial alkaline solid residue, are selected for further research. Alkaline Ca-rich residues seem particularly promising, since these materials are inexpensive and available near large industrial point sources of CO2. In addition, residues tend to react relatively rapidly with CO2 due to their (geo)chemical instability. Various process routes have been proposed for mineral carbonation, which often include a pre-treatment of the solid feedstock (e.g., size reduction and/or thermal activation). The only available pre-treatment option that has proven to be energetically and potentially economically feasible is conventional grinding. 7 Two main types of process routes can be distinguished: (1) direct routes in which carbonation takes place in a single step process, either in a gas-solid or a gas-liquid-solid process, and (2) indirect routes in which the Ca is first extracted from the silicate matrix and subsequently carbonated in a separate process step. The aqueous route in which Ca-silicates are directly carbonated in an aqueous suspension at elevated temperature and CO2 pressure is selected as the most promising process route for further investigation. The following key issues for further research are identified: the reaction rates and mechanisms of mineral carbonation as well as its energy consumption and sequestration costs. Another important aspect of mineral carbonation is the destination of the carbonated products. In Chapter 2 the mechanisms of aqueous steel slag carbonation are studied experimentally. Process variables, such as particle size, temperature, and carbon dioxide pressure are systematically varied and their influence on the carbonation rate is investigated. The maximum carbonation degree reached is 74% of the Ca content in 30 minutes at 19 bar CO2 pressure, 100 °C, and a particle size of <38 µm. The two most important factors determining the reaction rate are particle size (<2 mm to <38 µm) and reaction temperature (25-225 °C). The carbonation reaction is found to occur in two steps: (1) leaching of calcium from the steel slag particles into the solution and (2) precipitation of calcite on the surface of these particles. The first step and, more in particular, the diffusion of calcium through the solid matrix towards the surface, appears to be the rate-determining reaction step. The Ca-diffusion is found to be hindered by the formation of a CaCO3-coating and a Ca-depleted silicate zone during the carbonation process. In Chapter 3 the mechanisms of aqueous steel slag carbonation are further investigated, together with the environmental properties of the (carbonated) steel slag. Steel slag samples are carbonated to a varying extent and leaching experiments and geochemical modelling are used to identify solubility-controlling processes of both major and minor elements that are present in the slag. Carbonation is shown to reduce the leaching of alkaline earth metals (except Mg) by conversion of Ca-phases, such as portlandite, ettringite, and Ca-(Fe)- silicates into calcite, possibly containing traces of Ba and Sr. The leaching of vanadium increases substantially upon carbonation, probably due to the dissolution of a Ca-vanadate. The increased reactive surface area of Al- and Fe- (hydr)oxides after carbonation tends to reduce the leaching of sorption- controlled trace elements.
Details
-
File Typepdf
-
Upload Time-
-
Content LanguagesEnglish
-
Upload UserAnonymous/Not logged-in
-
File Pages236 Page
-
File Size-