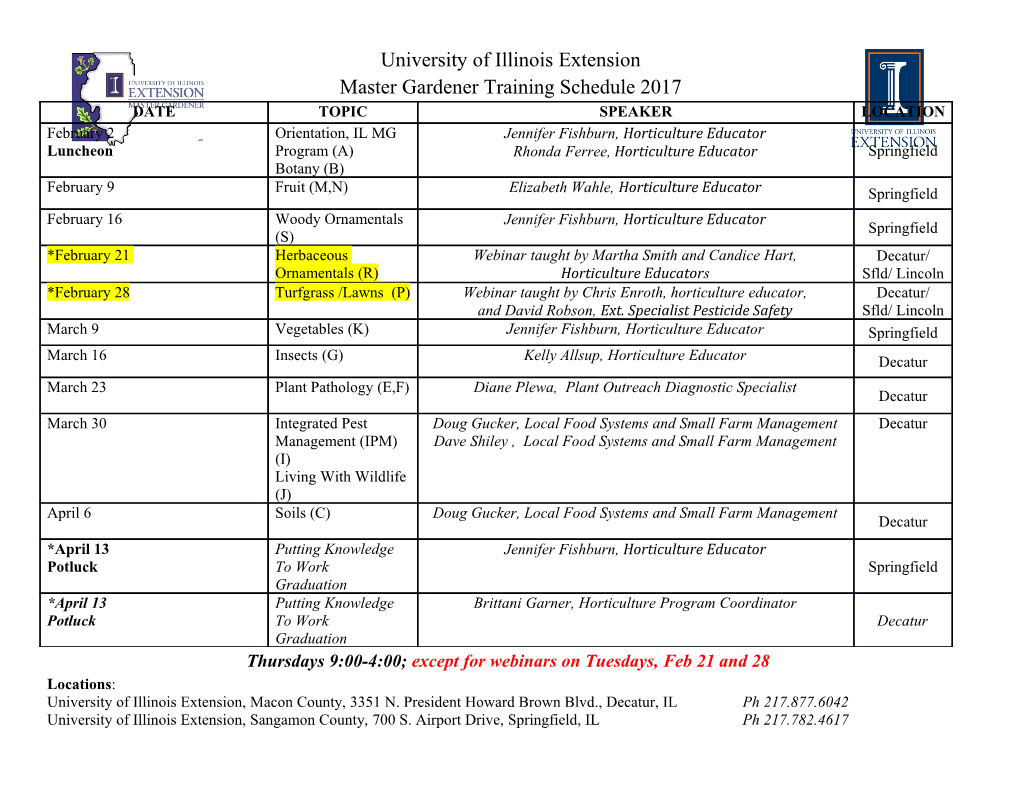
A Novel Reciprocating Sleeve Axial Diesel Engine, “The Shepherd Engine” Adjunct Professor Stephen F Johnston PhD ME GCHE FIEAust CPEng Applied Technology Institute, Unitec NZ Abstract The paper outlines key features and explores some of the potential benefits of a novel axial, reciprocating sleeve, two stroke diesel engine design being developed by New Zealand inventor and innovator Gray Shepherd, with support from Unitec NZ. A proof of concept model has been demonstrated, and current work is on developing an engine which could meet global and European emission standards required by years 2008 - 2015. The Applied Technology Institute at Unitec is providing facilities and support. The paper discusses earlier engine designs and patents with broad similarities to Shepherd’s. The Shepherd engine dispenses with many of the components in a conventional engine, including connecting rods, crankshaft and valve drive train. Other design features significantly increase engine efficiency and power-to-weight ratio. The paper describes the advantages of the design, particularly its mechanical simplicity and its reduced number of working parts. Some of the issues in the commercialisation of new kinds of engine technologies are explored in the context of the experience of the Powell Engine Company. The paper concludes with suggestions on possible development paths for the engine. Its commercial prospects appear to be enhanced by concerns about fuel security and global climate change. Keywords Axial engines, ceramics, crankless engines, design and development, diesel engines, patents, invention, innovation, Shepherd, Unitec. Introduction In a diesel engine the fuel is injected into a combustion chamber, where it is ignited by the elevated temperature of the compressed air and burns at essentially constant pressure. In a conventional commercially available diesel engine, a connecting rod and crank arrangement is used to transform the reciprocating piston motion into rotary motion. The geometry of this arrangement is less than ideal. Because of the angle between the centreline of the piston and the centreline of the connecting rod while power is being transmitted, there is a significant sideways force between the piston and the cylinder wall. Making the connecting rod longer (theoretically it should approach infinite length) reduces the angle and therefore the sideways force, but also increases the height and weight of the engine. The sideways force is generally supported by the skirt of the piston, the section below the piston rings. This arrangement requires lubrication of the sliding contact area between the piston and the cylinder, and can be the cause of significant frictional energy losses. The piston, the cylinder and the engine structure, all have to be strong enough to support the sideways forces. Allowing space within the engine for the crank to rotate also makes the engine relatively large and heavy. Engineers have long sought to develop more compact and efficient engine designs. 1 Axial engines are one approach to eliminating the connecting rod and crankshaft. In this type of engine the pistons and cylinders are parallel to the output shaft. One arrangement is to group a number of cylinders around an output shaft, with the pistons driving the output shaft via a swash- or wobble-plate. The tilted circular swash plate is not quite perpendicular to the shaft so that, as it rotates, points on it experience relative axial and circumferential motion, and it can be used to convert the reciprocating motion of a piston to rotary motion of the output shaft. Setright (1975, p. 99) noted that a steam engine designed along these lines was patented in 1875. Setright acknowledged the attractions of the axial engine – its compactness, low frontal area, high power to weight ratio, simplicity in general arrangement, and potential for perfect balance, given appropriate attention to the number and disposition of cylinders. Setright also noted that difficulties had been experienced with lubrication and with access to the principal working parts for maintenance, but recognised that newer materials and technologies (some of them discussed later in this paper) may well overcome these difficulties (op cit p. 104). Historically, the best known and most technically successful example of the axial engine is probably the Michell engine, which was ultimately defeated by global economic factors rather than by technical ones. The Michell Crankless Engine A.G.M. Michell (1870-1959) was a Melbourne engineer who made a major contribution to Australian shipping. Sydney Walker, an employee of Michell’s Crankless Engines Limited Melbourne, documented Michell’s work. Based on his research on the mechanical properties of liquids, and his mathematical studies of fluid motion, viscosity and lubrication, Michell developed the Michell tilting-pad thrust bearing, which he patented in 1905. The key feature of the tilting-pad bearing is that, as a plane surface (for example a collar on a propeller shaft) moves past the pad, it draws in a wedge-shaped film of oil between the pad and the collar. A series of tilting pads could be mounted around the shaft. The bearing load is supported by the pressure in the wedge-shaped oil film, eliminating metal-to-metal contact and greatly reducing friction. Applied to the problem of transmitting propeller thrust from a propeller shaft to a vessel, the Michell thrust bearing reduced friction by 90 to 95 per cent, and allowed bearing pressures ten times greater than for the traditional bearing designs. It also permitted much higher sliding speeds - from five to thirty times greater than had previously been permissible. (Walker 1972, p. 5) Michell formed Crankless Engines Ltd in 1920 and set out to design and develop a range of crankless machines, including engines intended for automobiles. In 1923 an eight- cylinder automobile engine was built for demonstration overseas and another was installed in a Buick chassis in Melbourne. Michell continued to develop the design, and a new five-cylinder crankless engine was completed in 1927. However: “…although both Ford and General Motors agreed that the engine had a performance that was some ten per cent better than conventional car engines of the time, the cost of retooling and re-equipping plants for its manufacture was too great to warrant serious consideration of its adoption. The economic downturn of the late 2 1920s was a further discouragement and in 1928 Michell’s Melbourne company closed down.” (McPhee 1993, pp. 39-40) The Michell crankless engine used pairs of opposed axial cylinders, spaced around and parallel to the output shaft. In each pair of cylinders there was a double-ended piston unit, which straddled the periphery of the swash-plate. For each piston unit, a pair of tilting- pad bearings, one on each side of the swash plate, transmitted the driving force to the swash plate, with minimal frictional resistance. At least three pairs of cylinders were required for satisfactory balance. (Judge 1975, p. 440) One of Michell’s 1923 engines (UK Patent 118098 July 1917) was returned to Australia and donated to the Museum of Victoria by the Speco Division of Kelsey & Hayes Company, Ohio U.S.A. It is now exhibited in the ground floor entrance to the Department of Mechanical and Manufacturing Engineering of Melbourne University, on loan from the Museum. The Shepherd Engine In 2003 an Auckland inventor, Gray Shepherd, began to design and develop an axial diesel engine which could convert reciprocating motion to rotary and not use a crankshaft. The proof of concept engine as shown in figure one has now been demonstratable since Nov 2005. Easy starting and throttle control has been achieved with the unexpected outcome of minimal requirements for lubrication. This is because there is no side load on the cylinder wall during the combustion cycle. The applications for the Shepherds engine appear to be widespread. Automotive, industrial, agricultural, power generation, large ship engine manufacturers Gray is hoping that with shared resources and collaboration the Shepherd engine will be developed as a benefit to mankind. Some benefits of the Shepherd engine (i) One of the highest power to weight ratios of any engine. Lightweight materials such as aluminium and ceramics can be used throughout. (ii) Low centre of gravity and low height compared to crankshaft engines. (iii) Fewer moving parts. No cylinder head or cylinder head gasket, no crankshaft, connecting rods, camshaft, valve springs, tappets, pushrods, etc. (iv) Compression ratios’ can be altered according to load. Because the pistons are fixed, each of the two pistons have the ability to be moved incrementally. Diesel combustion characteristics can be changed to reduce nitrous oxide and exhaust emissions. (v) High torque at low RPM. (vi) Low RPM, half that of similar horsepower crankshaft engines. (vii) Two stroke diesel but does not require a Roots blower or cam driven exhaust valves. No turbocharger required. 3 (viii) No gear box required to match engine revs to rev requirements of a propeller when used in marine applications. Propeller shaft RPM as low as 50 RPM (ix) Multiple engines can be fitted for greater horsepower in large ship applications requiring thousands of horsepower. Engines can also be removed and replaced in a matter of days not weeks. Catastrophic failure in a crankshaft engine can result in months of lost profits due to the degree of difficulty in removing a crankshaft out of the engine room due to its size. Figure 1 shows close up, a photo of the demonstratable engine. The main support sleeve supports two fixed pistons, one at each end. Diesel is injected on each cycle through injectors in each piston and combustion of the diesel drives the cylinder sleeve backward and forwards. Each pair of cam followers applies a force onto the slope of the cam. The resultant force causes the main rotating sleeve (flywheel) to rotate. Two reciprocations of the cylinder sleeve are required to complete one rotation of the rotating sleeve since there are two lobes.
Details
-
File Typepdf
-
Upload Time-
-
Content LanguagesEnglish
-
Upload UserAnonymous/Not logged-in
-
File Pages14 Page
-
File Size-