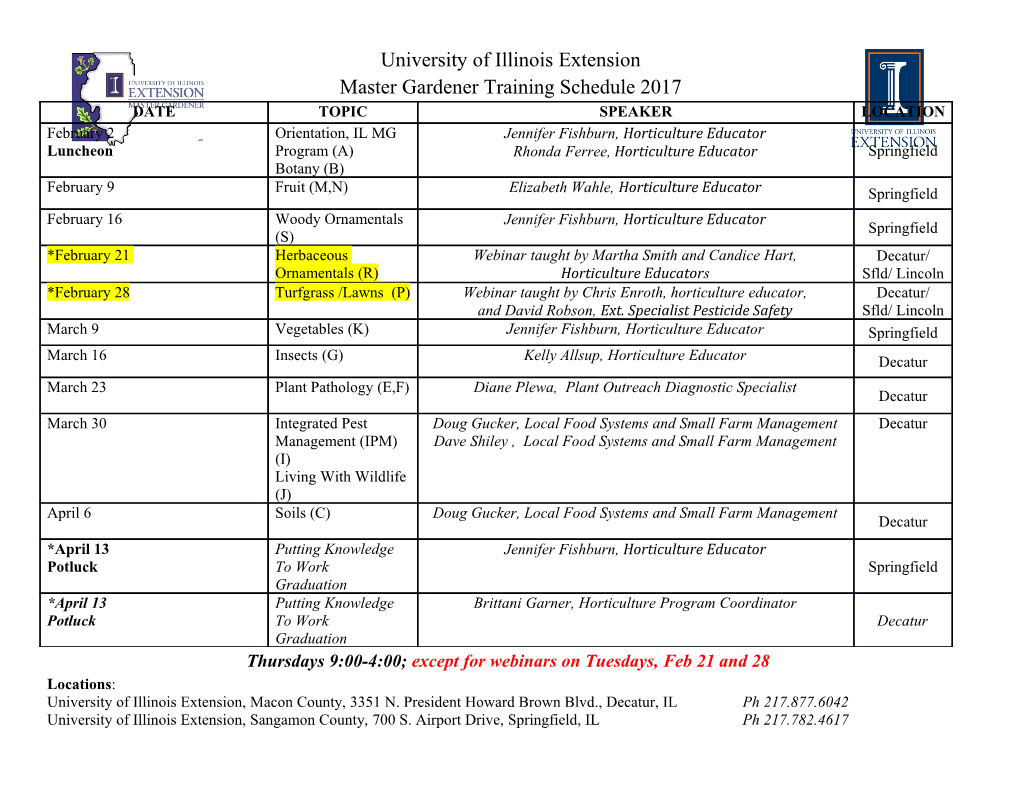
I would like to dedicate this thesis to my children Alexander and Sophia, my wife Oksana and my family for their support over the years. University of Birmingham Research Archive e-theses repository This unpublished thesis/dissertation is copyright of the author and/or third parties. The intellectual property rights of the author or third parties in respect of this work are as defined by The Copyright Designs and Patents Act 1988 or as modified by any successor legislation. Any use made of information contained in this thesis/dissertation must be in accordance with that legislation and must be properly acknowledged. Further distribution or reproduction in any format is prohibited without the permission of the copyright holder. University of Birmingham MECHANICAL ENGINEERING FACULTY Thermal Management and control of a Homogeneous Charge Compression Ignition (HCCI) Engine by George Constandinides A thesis submitted to The University of Birmingham For the degree of DOCTOR OF PHILOSOPHY The University of Birmingham School of Engineering October 2013 2 Abstract Abstract Homogeneous Charge Compression Ignition (HCCI) is the process which a relatively homogeneous mixture of air and fuel auto ignites through compression. HCCI engines can have high thermodynamic cycle efficiencies, with low levels of emissions of nitrogen oxides (NOx) and particulate matter (PM). However due to the nature of the combustion the operating envelope is quite small compared to conventional internal combustion engines. An efficient powertrain system centred on a supercharged HCCI (Homogeneous Charge Compression Ignition) engine with on-board thermal management was developed that extends the operating envelope of an HCCI engine. To achieve controlled auto-ignition across a wide range of engine conditions, a system for management of flow and temperature was installed at the air intake to enable the necessary regulation of temperatures and pressures at the inlet ports. The system includes a heat exchanger to heat the charge air, a supercharger to boost the charge air pressure, supercharger bypass and finally an intercooler, so that a wide range of combinations of pressures and temperatures can be achieved at the intake ports. In order to facilitate this control, a complete simulation model of the thermal system for a pressure-boosted multi-cylinder HCCI engine was developed that investigates the physical behaviour of the HCCI test engine and auxiliary components and can easily be implemented for a forward predicting control strategy. This work presents a dynamic mass and enthalpy balance model running in real time for the air intake system of the multi-cylinder HCCI gasoline engine and auxiliary components. The model is capable to calculate heat flux, mass flow, pressure and gas temperature distribution for the whole engine thermal management system however it does not take into account the turbulent nature of flow especially where hot and cold gas mix. 3 Abstract Therefore an elaborate CFD model of the Thermal Management system has been compiled for evaluation of the computed flow field and analysis of the thermal system performance by the use of the CFD tool ANSYS CFX. Furthermore utilising the Thermal Management System, the upper operating range was increased by using an intercooler and supercharging the inlet air. Special care had to be exerted while cooling the charge air as the appropriate amount of energy for auto-ignition had to be delivered to initiate HCCI combustion. Applying inlet air heating was regarded as to be one of the most popular ways of reducing the achieved load under HCCI combustion, however during the presented tests the impact of heating on the lowest achievable load seems to be somehow reduced. In order to expand the low HCCI boundary even further, the combined effect of heating and throttling of inlet air has been incorporated. By applying both of these techniques the lowest achievable load during HCCI combustion was increased by 0.25 (of NMEP) from the baseline at 1000rpm and by 0.5bar (of NMEP) from the baseline at 1500rpm. Unfortunately, this approach is accompanied with the penalty of higher fuel consumption. Finally an HCCI control strategy has been proposed aiming to reduce emissions and in particular NOx and HC. It has been shown that by applying thermal management on both load regimes (the lowest and the highest) an improvement in both NSNOx and NSHC emissions was achieved. 4 Acknowledgments Acknowledgments The author gratefully acknowledge financial help of EPSRC, DTI and Jaguar Cars and would like to extend special thanks to all staff in The University of Birmingham and Jaguar Cars for their effort and support in this project. Furthermore the author would also like to show his grateful appreciation to Professor Mirosław L. Wyszyński for his guidance and supervision during his PhD course. Furthermore I’d like to thank my friend and colleague Dr Jacek Misztal for his assistance during the experimental phase of this work. Dr Jonahan Hartland from Jaguar Cars is also greatly appreciated, for his guidance, help and support during the early development of this project. Last, Technical support by Peter Thornton, Carl Hingley and Lee Gauntlett from The University of Birmingham was highly valuable and appreciated. 5 Nomenclature Nomenclature Abstract .................................................................................................................................................... 3 Acknowledgments .................................................................................................................................... 5 Nomenclature ........................................................................................................................................... 6 List of Figures .......................................................................................................................................... 9 List of Tables .......................................................................................................................................... 11 Algebraic Symbols and Abbreviations Table ......................................................................................... 12 List of Publications ................................................................................................................................. 16 Chapter 1. Introduction ....................................................................................................................... 17 1.1 Introduction to HCCI and Thermal Management ............................................................. 17 1.2 Thermal Management Objectives and HCCI Control ....................................................... 18 1.3 Jaguar V6 HCCI Engine ................................................................................................... 19 1.4 Thermal Management for HCCI ....................................................................................... 19 1.5 Thermal Management Study and Control Strategy Implementation. ................................ 20 1.6 Objectives and Approaches ............................................................................................... 23 1.7 Thesis Outline ................................................................................................................... 25 Chapter 2. Literature Review .............................................................................................................. 28 2.1 Impact of Fuel type on HCCI Combustion ....................................................................... 32 2.2 Means of HCCI Control .................................................................................................... 33 2.3 Charge Air Thermal Conditions Control and Effects on HCCI Combustion .................... 34 2.4 Effect of Compression Ratio on HCCI mode .................................................................... 38 2.5 Effect of Boost Pressure on HCCI mode .......................................................................... 39 2.6 Gas Emissions on HCCI mode .......................................................................................... 41 2.7 Fuel Reforming on HCCI mode ........................................................................................ 47 Chapter 3. Engine Thermal Management System .............................................................................. 51 3.1 Physical Thermal System .................................................................................................. 51 3.2 Reformed Exhaust Gas Recirculation (REGR) ................................................................. 52 3.3 Thermal Management System Design Rationale .............................................................. 52 3.3.1 Intake air heating ....................................................................................................... 53 3.3.2 Preliminary Matlab/Simulink heat exchanger model ................................................. 58 3.3.3 Eaton M24 Supercharger ........................................................................................... 61 3.4 Thermal Management System Experimental System........................................................ 62 3.4.1 Jaguar V6 HCCI Engine ............................................................................................ 62 3.4.2 Cam Profile Switching System .................................................................................. 65 3.4.3 Supercharger .............................................................................................................
Details
-
File Typepdf
-
Upload Time-
-
Content LanguagesEnglish
-
Upload UserAnonymous/Not logged-in
-
File Pages246 Page
-
File Size-