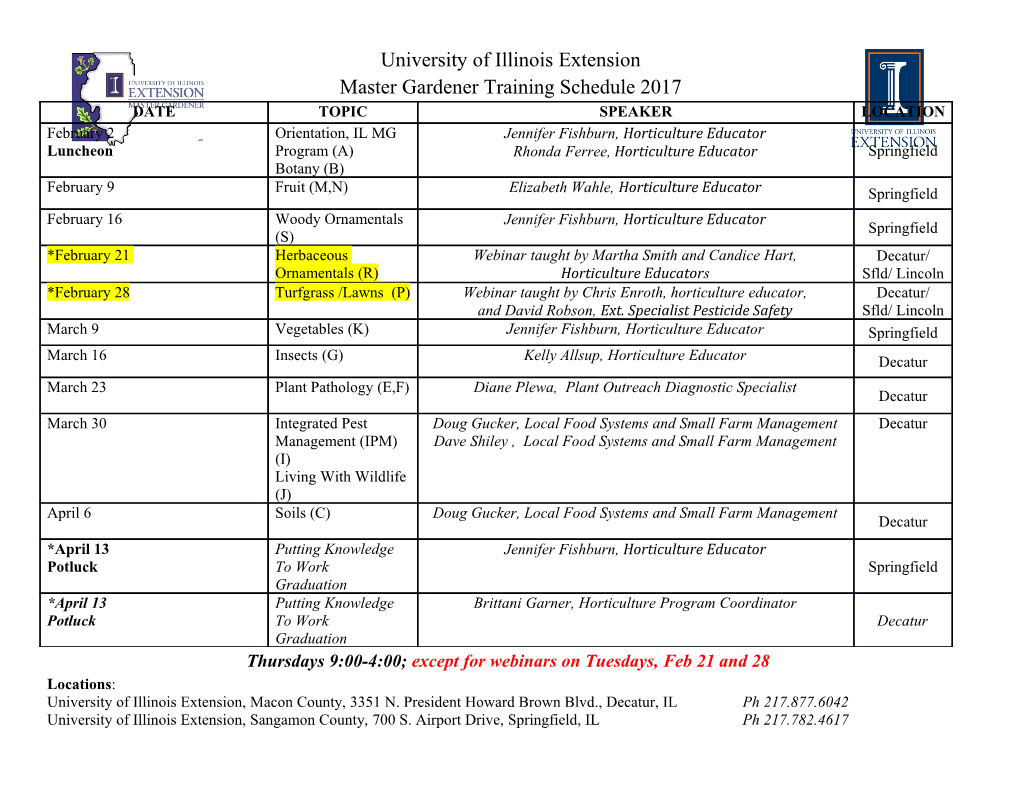
SUMMARY OF BLOWOUT PREVENTER (BOP) FAILURE MODE EFFECT CRITICALITY ANALYSES (FMECAs) FOR THE BUREAU OF SAFETY AND ENVIRONMENTAL ENFORCEMENT 2650788-FMECA-FS-E3 1 Issued for BSEE Review 4-29-2013 Report No. Revision Purpose of Revision Date This work was performed by American Bureau of Shipping and ABSG Consulting Inc. for the Bureau of Safety and Environmental Enforcement (BSEE) under the terms of BSEE Contract Number M11PC00027 THIS PAGE WAS INTENTIONALLY LEFT BLANK ii LIST OF CONTRIBUTORS: ABS Consulting Randal Montgomery Kamran Nouri Andrew Quillin James Rooney ABS Harish Patel iii THIS PAGE INTENTIONALLY LEFT BLANK iv SUMMARY As part of the Blowout Preventer (BOP) Maintenance and Inspection for Deepwater Operations study (Bureau of Safety and Environmental Enforcement [BSEE] Contract Number M11PC00027), American Bureau of Shipping (ABS) and ABSG Consulting Inc. (ABS Consulting) performed three Failure Mode, Effect, and Criticality Analyses (FMECAs) on specific BOP subsystems and equipment. The three FMECAs were performed by three different teams, which consisted of personnel from the operating company, drilling contractors, and original equipment manufacturers (OEMs). This draft report summarizes and compares the results of the three FMECAs and represents the study deliverable associated with Task 6.2.2.4 as outlined in the contract. The objectives of each FMECA were to (1) establish the relationship between a specific subsystem/equipment failure and a loss of system functionality; (2) identify the critical failures by using risk-ranking methods; and (3) align the current Maintenance, Inspection, and Testing (MIT) practices and their associated frequencies with each functional failure and the associated subsystem and equipment failures. This report presents the objective and scope of the FMECA studies and this summary report; a discussion of the FMECA methodologies used; a comparison of the results from the three FMECAs; and the transmittal of the updated FMECA reports. Section 2 of this report provides an overview of the FMECA methodologies used for the three studies and discusses the differences in the three study approaches. Specifically, all three studies employed a functional-level FMECA followed by an equipment-level FMECA. The functional-level FMECAs were used to establish the end effects of functional failures and to link these functional failures to specific equipment-level failure modes. The equipment-level FMECAs were conducted to identify the impact of major equipment and component failures on the BOP performance by evaluating equipment-level failure modes, identifying specific equipment-level causes, identifying the safeguards to prevent or detect the failure modes, and ranking the criticality of failure modes. In addition, the equipment-level FMECAs were used to align MIT activities with equipment-level failure modes and specific equipment failures. Section 3 of this report contains a comparison of the results from the three FMECAs. In this section, the risk-ranking and maintenance task results are compared. Specifically, comparisons of equipment-failure mode risk, frequ`ency of occurrence, and detectability are provided. Comparisons of the maintenance tasks associated with equipment/failure modes and frequency of being applied as a protection are included as a part of the maintenance task results. This report summarizes and compares the results of the three FMECAs. Section 4 provides concluding remarks on (1) the FMECA methodologies and (2) the study results. The comparison of the risk ranking and MIT activities identified trends related to: v Most Important Equipment Failures Most Frequently Occurring Equipment Failures Hardest to Detect Failure Modes Most Frequently Listed MIT Items As a Means to Detect or Prevent Failures The most important equipment failures were: Blind Shear Rams (in all three FMECAs) Casing Shear Rams (in two of the three FMECAs) Connectors (in two of the three FMECAs) Blue and Yellow POD hydraulics (in two of the three FMECAs) Choke and Kill Lines and Valves (in two of the three FMECAs) Pipe Rams (in two of the three FMECAs) Hydraulic Supply Lines (in two of the three FMECAs) Subsea Accumulators (in two of the three FMECAs) The most frequently occurring equipment failures were found to be: Control Systems (both the electric or hydraulic portions) (in all three FMECAs) Pipe Rams (in two of the three FMECAs) Choke and Kill Lines and Valves (in two of the three FMECAs) Blind Shear Rams (in two of the three FMECAs) The hardest to detect failures were related to the following equipment: Autoshear System (in all three FMECAs) Connector (in two of the three FMECAs) Rigid Conduit (in two of the three FMECAs) Finally, a sort and review of the MIT tasks listed as a means to detect or prevent equipment failures found the following to be the most frequently listed MIT tasks: Function Test (in all three FMECAs) Pressure Test (in all three FMECAs) Dimensional/Ultrasonic Testing (in two of the three FMECAs) Rebuilding/Replacing Equipment (in two of the three FMECAs) These result trends provide information related to the more important equipment failures (in terms of risk, frequency of occurrence, and failure detectability) and MIT tasks. vi TABLE OF CONTENTS Section Page SUMMARY .......................................................................................................................................... v TABLE OF CONTENTS .................................................................................................................. vii LIST OF TABLES .............................................................................................................................. ix LIST OF FIGURES ............................................................................................................................ ix LIST OF ACRONYMS ...................................................................................................................... xi 1.0 INTRODUCTION .................................................................................................................... 1 1.1 Objectives ............................................................................................................................... 1 1.2 FMECAS Scopes .................................................................................................................... 1 1.3 FMECA Team Members and Meeting Schedule .................................................................... 5 1.4 Report Organization ................................................................................................................ 8 2.0 DISCUSSION OF FMECA METHODOLOGIES ................................................................ 9 2.1 Overview of the FMECA Methodology ................................................................................. 9 2.1.1 Functional -Level (Top-Down) FMECA ....................................................................... 11 2.1.2 Equipment-Level (Bottom-Up) FMECA ........................................................................ 11 2.1.3 Evaluation and Ranking of Equipment Failure Modes (Criticality/Risk Ranking) ...... 11 2.2 Discussion of FMECA Methodology Differences................................................................ 12 3.0 COMPARISON OF FMECA RESULTS ............................................................................. 15 3.1 Overview of Comparison Approach ..................................................................................... 15 3.2 Criticality/Risk Ranking Comparison ................................................................................... 15 3.3 MIT Comparison .................................................................................................................. 25 4.0 CONCLUDING REMARKS ................................................................................................. 29 4.1 FMECA Methodologies ........................................................................................................ 29 4.2 Study Results ........................................................................................................................ 29 APPENDIX A – RPN SCORING SYSTEM .................................................................................. A-1 APPENDIX B – FMECA METHODOLOGY DIFFERENCES ................................................. B-1 APPENDIX C – FMECA 1, 2, AND 3 REPORTS ........................................................................ C-1 vii THIS PAGE INTENTIONALLY LEFT BLANK viii LIST OF TABLES Table Description Page 1-1 Summary of BOP and Associated Control Systems ............................................................. 2 1-2 Equipment-Level FMECA Major Component Boundaries ................................................ 4 1-3 IP FMECA Team Members ................................................................................................... 6 1-4 ABS and ABS Consulting FMECA Team Members ............................................................ 6 1-5 FMECA Study Dates ............................................................................................................... 7 3-1 Failure Modes with Highest RPN Scores ............................................................................ 17 3-2 Failure Modes with Worst Occurrence Ratings ................................................................. 19 3-3 Failure Modes with Worst Detection Ratings ....................................................................
Details
-
File Typepdf
-
Upload Time-
-
Content LanguagesEnglish
-
Upload UserAnonymous/Not logged-in
-
File Pages295 Page
-
File Size-