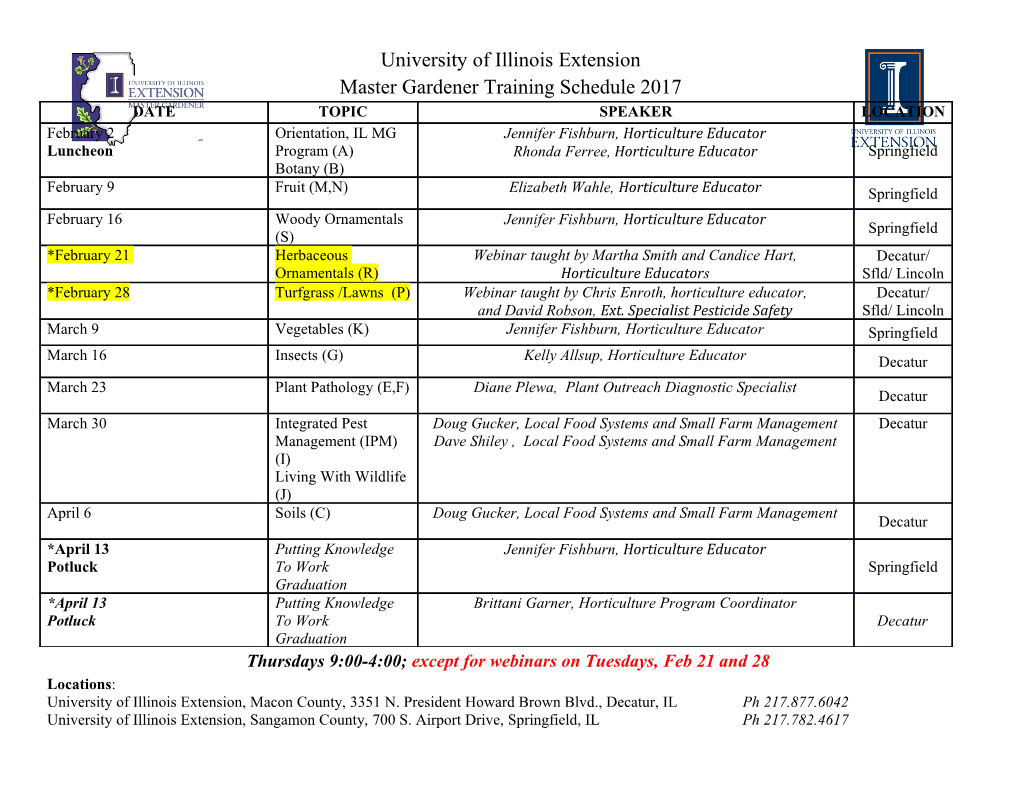
INFLUENCE OF NITRIDING MECHANISMS ON SURFACE ROUGHNESS OF PLASMA AND GAS NITRIDED/NITROCARBURIZED GRAY CAST IRON The differences in he mechanism of plasma (ion) nitrogen atoms in statu nascendi and nitriding has been studied ex- their chemisorption according to the mechanisms of nitrogen tensively during the past 40 reaction[13, 14]: transfer between plasma years[1-12]. There is general T 2NH3 —> 2Nad+3H2 agreement that nitrogen ions and (ion) nitriding and gas + + + + radicals such as N , N2 , NH , NH2 , nitriding have various as well as fast neutral nitrogen mol- The differences in nitrogen-transfer ecules play a significant role in ni- mechanisms between the two practical consequences. trogen transfer. This occurs either by methods have various practical con- For example, gas nitriding generating active nitrogen atoms on sequences. For example, plasma ni- the cathodic part surface[6], or by at- triding is considered as a low ni- increases the surface taching to iron atoms sputtered from triding-potential method, unable to roughness of gray cast the surface and redeposited back on produce a thick compound zone[13], the cathode in the form of nitrides[4]. and plasma nitriding does not pene- iron. Proper identification The gas-nitriding mechanism using trate small holes, cavities, etc., and, of the advantages and ammonia is less controversial and therefore, the process can be used for has been considered as a catalytic re- hardening sintered low-density iron disadvantages of these [15, 16] action of ammonia with iron which parts . This characteristic of two methods could leads to the formation of the active plasma is also used to advantage in significantly improve their use. Edward Rolin’ski** Advanced Heat Treat Corp. Monroe, Mich., and Waterloo, Iowa A. Konieczny* U.S. Steel Automotive Center Troy, Mich. Gary Sharp** Advanced Heat Treat Corp. Monroe, Mich., and Waterloo, Iowa **Member of ASM International and member, ASM Heat Treating Society *Member ASM International View of a large stamping die undergoing plasma nitriding in a vacuum chamber. HEAT TREATING PROGRESS • MARCH/APRIL 2007 01 Ra 126.99 microin. (3.25 mm) Rmax 951.57 microin. (24.17 mm) P Profile Leveled Lc/Ls = Off 2,500.0 0.0 a Microin. -2,500.0 Pick-up TK300 Lt = 0.200 in. Vt = 0.020 in./s 0.200 Ra 121.67 microin. (3.09 mm) Rmax 989.84 microin. (25.14 mm) P Profile Leveled Lc/Ls = Off 1,000.0 b 0.0 Microin. -1,000.0 Pick-up TK300 Lt = 0.200 in. Vt = 0.020 in./s 0.200 Ra 35.67 microin. (0.91 mm) c Rmax 322.87 microin. (8.20 mm) P Profile Leveled Lc/Ls = Off 500.0 0.0 Microin. d -500.0 Pick-up TK300 Lt = 0.200 in. Vt = 0.020 in./s 0.200 Fig 2 — Profilograms of samples after gas nitrocarburizing at 1050ºF, or 566ºC (a), gas nitriding at 968ºF, or 520°C (b), and plasma nitrocarburizing at 1050ºF, or 566°C (c). mechanical masking. By comparison, bination of cast mechanical proper- gas nitriding can produce a com- ties and damping, which are very im- pound zone (white layer) of practi- portant in large, 20-30,000-lb cally any thickness by controlling the (9-13,600 kg) tooling. High-quality nitriding potential using hydrogen finishing of such tools to Class A- e or oxygen sensors and modern auto- surface requirements after thermo- matic methods[19-21]. Also, gas ni- chemical treatment is of paramount triding can be used for hardening importance to achieve good, long parts having small holes, such as lasting performance in manufac- those in diesel injector plungers, and turing applications. Surface quality nitriding the entire surface of any requirements are even more critical product. Proper identification of the for tools designated for stamping respective advantages and disadvan- modern materials such as advanced tages of the two methods could sig- high strength steels (AHSS), in- f nificantly improve their use. cluding DP490 dual-phase steel. Fig 1 — Surface of gray cast iron samples The differences in plasma and gas Therefore, post-nitriding roughness after gas nitrocarburizing at 1050ºF, or 566°C (a and b), gas nitriding at 968ºF, or 520°C (c nitriding are demonstrated on must be kept to a minimum and any and d), and plasma nitrocarburizing at common gray cast irons, which are finishing operations should not be too 1050ºF (e and f). frequently used for tooling in many costly. The authors observed that gray stamping operations[22]. This inex- cast iron dies become rougher after pensive material offers a good com- gas nitriding and require more fin- 02 HEAT TREATING PROGRESS • MARCH/APRIL 2007 ishing than the plasma-nitrided dies, Table 1 — Details of the nitrocarburizing (NC) which has a high possibility of being a result of differences in the nitriding and nitriding (N) experiments mechanisms of the two methods. Process Process parameters Plasma NC Temperature, ºF (ºC) 1050 (566) Experimental Time, h 15 All experiments were performed %N2 50 on G3500[22] gray cast iron samples Gas NC Temperature, ºF (ºC) 1050 (566) having the following chemical com- Nitriding Potential, atm-1/2 3 position in wt%: Carburizing potential, Kc (W) 0.31 Time, h 20 2.8-3.2C, 1.5-2.2 Si, 0.7-1.0 Mn, Gas N Temperature, ºF (ºC) 968 (520) 0.35-0.50 Cr, 0.35-0.50 Mo, <0.7 Cu, Nitriding potential, atm-1/2 2 <0.15 S, <0.15 P, bal. Fe Time, h 24 Samples were ground using metal- Results face roughness with very few open lographic polishing papers, finishing High-temperature (1050ºF or 566°C) microgrooves and cavities in the sur- with 600× grit. Plasma nitrocarbur- gas nitrocarburizing caused a signif- face (Figs. 1 and 2). Data on surface izing was performed in a nitrogen icantly rougher surface. Steps taken roughness after processing are and hydrogen gas mixture con- to minimize the problem included shown in Table 2. Rmax for the taining 2% methane. Controllable gas trying nitriding instead of nitrocar- plasma-nitrided surfaces, although nitriding was performed in an am- burizing and using a lower pro- much lower than after gas nitriding, monia, nitrogen, and hydrogen gas cessing temperature (968ºF, or 520°C are still comparatively high for mixture, and also with carbon ) and lower nitriding potential. These stamping tool applications. However, dioxide in the case of the nitrocarbur- processing conditions reduced sur- it should be noted that these picks are izing cycle. The gas nitriding system face roughness compared with the made of a loose deposit of the nitrides was equipped with a hydrogen nitrocarburized samples, but surface from plasma, which do not adhere too sensor and automatic control of the roughness was still unsatisfactory. strongly to the surface and can be nitriding potential. Process parame- By comparison, plasma processing easily removed by a simple polishing ters are shown in Table 1. resulted in a significantly lower sur- operation with a soft-wire brush. HEAT TREATING PROGRESS • MARCH/APRIL 2007 03 Table 2 — Surface roughness data of samples after various treatments Initial Gas Plasma Temperature, ºF (ºC) 1050 (566) 968 (520) 1050 (566) Ra, Measurement 1 3.31 203.64 121.67 35.67 microin. 2 2.63 245.67 143.24 28.73 3 2.05 126.99 130.98 36.92 4 3.89 135.71 90.20 35.44 5 2.72 138.32 106.44 29.53 Pick Measurement 1 5 145 119 145 0.020 in. count, 2 5 165 94 152 picks/in. Fig 4 — Photomicrograph of the near-sur- 3 0 114 102 157 face area of gray cast iron sample taken from 4 0 127 114 170 25,000-lb (11,350 kg) stamping die after in- 5 0 119 107 170 dustrial gas nitrocarburizing. Gas nitrocar- burizing parameters: 1000°F (538°C) for 12 h, nitriding potential and carburizing poten- Compound zones formed in the gas tials not determined. Etchant: 2% nital. Note nitrocarburized and nitrided samples severe decarburization of the near-surface had a very uneven thickness with an layer with a network of kish graphite flakes inconsistent compact portion and tree- and a deep penetration of the compound zone like roots along the flakes of graphite (white layer) along the flakes. and between surface cracks and im- created during the machining oper- perfections (Fig. 3). Total penetration ations performed on the as-cast sur- of the internal structure by these roots face in the process of the final of the compound zone exceeded sev- shaping of the die geometry result a 0.005 in. eral times the thickness of the com- from the physical differences be- pact portion of the zone. Therefore, tween graphite and the mostly the specific volume of the near-sur- pearlitic matrix. Graphite flakes face layer became locally larger than allow easy free machining of cast that of the base matrix, which resulted iron by introducing discontinuities in the areas of increased volume to ex- in the metal matrix[24, 25]. Therefore, tend above the original surface. Fur- during machining, chips are broken thermore, the cracking and plastic de- rather than plastically deformed or formation in this region added to the smeared over the surface by the cut- roughening effect. ting tool. As a result of the clear-cut In the as-plasma-treated sample, machining, surface voids and cracks b 0.005 in. the compound zone was very uni- are not filled with the metallic com- form and compact without any sig- ponents of the matrix, but rather nificant defects. with graphite, or they stay open. Also, the interface between graphite Industrial Case Studies flakes and the matrix may not be as In industrial applications, the neg- coherent near the surface as in the ative effects of gas nitriding of gray core.
Details
-
File Typepdf
-
Upload Time-
-
Content LanguagesEnglish
-
Upload UserAnonymous/Not logged-in
-
File Pages6 Page
-
File Size-