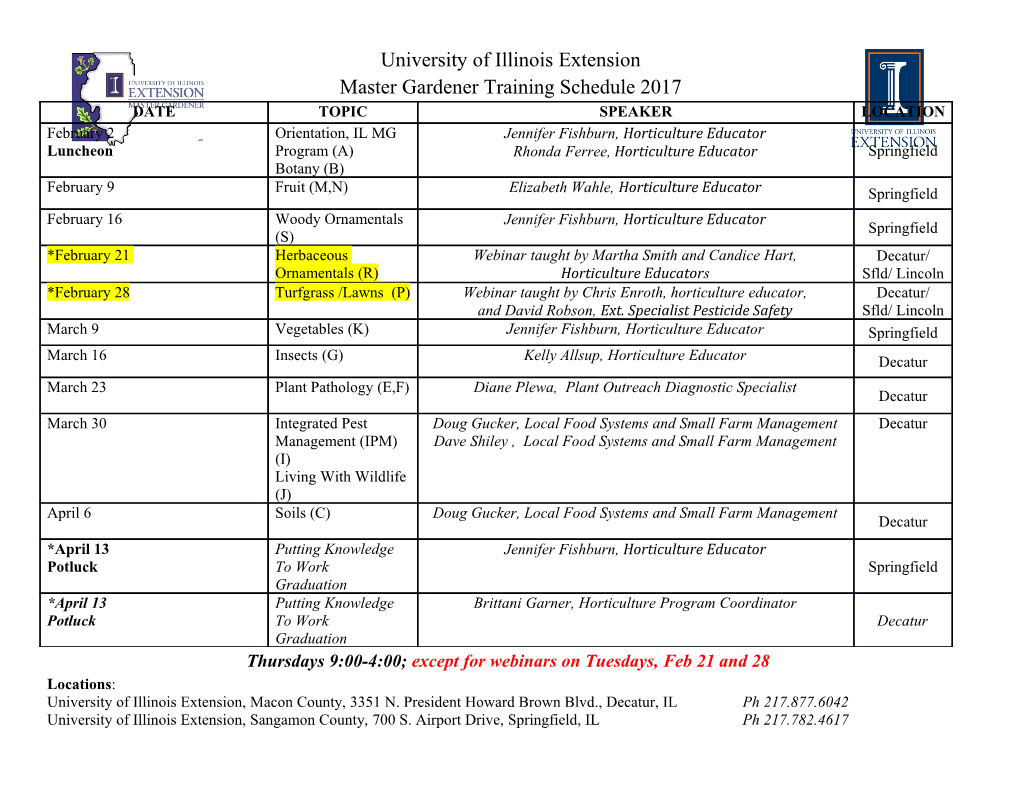
Mechatronics, Electrical Power, and Vehicular Technology 03 (2012) 65-72 Mechatronics, Electrical Power, and Vehicular Technology e-ISSN: 2088-6985 p-ISSN: 2087-3379 Accreditation Number: 432/Akred-LIPI/P2MI-LIPI/04/2012 www.mevjournal.com A REVIEW OF ATOMIC LAYER DEPOSITION FOR NANOSCALE DEVICES REVIEW DEPOSISI LAPISAN TIPIS UNTUK PERALATAN SKALA NANO Edy Riyanto a, b, c, *, Estiko Rijanto b, Budi Prawara b a State Key Laboratory for Modification of Chemical Fibers and Polymer Materials, College of Material Science and Engineering, Donghua University, Shanghai 201620, People’s Republic of China b Research Centre for Electrical Power & Mechatronics, Indonesian Institute of Sciences, Komp LIPI Jl Cisitu 21/54D, Gd 20, Bandung 40135, Indonesia c Plasma Physics & Application Laboratory, College of Science, Donghua University, Shanghai 201620, People’s Republic of China Received 14 October 2012; accepted 31 October 2012 Published online 18 December 2012 Abstract Atomic layer deposition (ALD) is a thin film growth technique that utilizes alternating, self-saturation chemical reactions between gaseous precursors to achieve a deposited nanoscale layers. It has recently become a subject of great interest for ultrathin film deposition in many various applications such as microelectronics, photovoltaic, dynamic random access memory (DRAM), and microelectromechanic system (MEMS). By using ALD, the conformability and extreme uniformity of layers can be achieved in low temperature process. It facilitates to be deposited onto the surface in many variety substrates that have low melting temperature. Eventually it has advantages on the contribution to the wider nanodevices. Key words: thin coating, atomic layer deposition, nanoscale devices. Abstrak Atomic layer deposition (ALD) adalah teknik penumbuhan lapisan tipis yang menggunakan reaksi kimia jenuh antara gas pendahulu untuk mendapatkan deposisi lapisan skala nano. Teknik ini menjadi subyek yang sangat menarik saat ini untuk deposisi lapisan sangat tipis pada berbagai aplikasi seperti mikroelektronik, photovoltaic, dynamic random access memory (DRAM) dan sistem mikroelektromekanik (MEMS). Dengan menggunakan ALD keseragaman dan penglarasan dari lapisan dapat dicapai pada temperatur proses yang rendah. Deposisi lapisan dengan teknik ini dapat digunakan pada beragam substrat yang memiliki temperatur leleh yang rendah. Keuntungan dari ALD adalah teknik deposisi ini memiliki kontribusi yang luas untuk aplikasi peralatan skala nan.o Kata kunci: lapisan tipis, atomic layer deposition, peralatan skala nano. I. INTRODUCTION Semiconductor (CMOS) transistors, DRAM Atomic layer deposition (ALD) is a memory, MEMS/NEMS, energy conversion, technology which can be used to fabricate a very photovoltaics, and display devices [8-12] that high-quality thin films based on alternate self- require precise control of film properties in limiting surface chemical reactions which have thickness, uniformity, and conformability. extreme uniformity on the three-dimensional Atomic layer deposition is a technique which structures, high density, low porosity, freedom is originally developed to produce thin films for from defect [1-4], with conformality and precise electroluminescent displays, but was later thickness control [5-7]. It has been applied in the adopted for other substrate as well [13]. This numerous advanced technologies for the technique is a thin film growth technique that fabrication of nanoscale thin films such as relies on two sequential, self-limiting surface microelectronics, Complementary Metal oxide reactions between gas phase precursor molecules and a solid surface as illustrated in Fig. 1 [14-17]. * Corresponding Author. Tel: +62-22-2503055 The films formed by sequential pulsing of two or E-mail: [email protected] © 2012 RCEPM - LIPI All rights reserved doi: 10.14203/j.mev.2012.v3.65-72 66 E. Riyanto et al. / Mechatronics, Electrical Power, and Vehicular Technology 03 (2012) 65-72 molecules react with hydroxyl (-OH) groups attached to the surface, until a saturation of available reaction sites is reached. In the second half-reaction the surface is oxidized by water vapor (thermal ALD) or in oxygen plasma (plasma-assisted ALD) to form aluminum oxide [22]. Precursor chemistry plays a key role in ALD, the precursor must of course be volatile and Fig.1. A schematic drawing of the AB reaction sequence thermally stable. These are may be gases, liquids, during atomic layer deposition process [19, 20]. or solids. Precursors must chemisorb on the more reactants, using purging with inert gas surface or react rapidly with the surface group between the precursor pulses to avoid gas-phase and react aggressively with each other. In that reactions [17]. Due to self-limited film growth way, it is possible to reach the saturation stage in mechanism, the film deposited by ALD has a short time (less than 1 s) and thereby ensure a shown excellent step coverage and conformality reasonable deposition rate [21]. This paper aims [6], because the reactions are driven to to provide information on the latest developments completion during every reaction cycle [18]. The in thin film deposition technology by atomic surface is exposed to reactant A, which react to layer deposition method and its application. initial surface sites. Then, after the product from reaction A are purged, the surface is exposed to II. DESCRIPTION OF SYSTEM reactant B. This reaction regenerates the initial functional groups and prepares the surface for the A. The Schematic of ALD System next exposure to reactant A. Fig. 2 shows the ALD flow reactor designed The thickness is grown to the desired for the substrate coating. Two separate precursor thickness by repeating this AB sequence [19, 20]. chambers are connected to the main reactor The reactor is purged with an inert gas between separately by valves 4, respectively. Each the precursor pulses [21]. With a proper precursor tube is connected with inert gas that is adjustment of the experimental conditions the controlled by a mass flow controller. The process proceeds via saturative steps [21]. Under pressure inside the reactor is monitored by such conditions the growth is stable and the pressure measurement gauges. Valve 10 and the thickness increase is constant in each deposition vacuum pump are used for controlling the cycle [21]. As the reactions are self-limiting, pressure inside the reactor. ALD does not require line-of-sight for deposition Fig. 3 shows the schematic illustration of the and high surface area to volume structures, and constructed ALD. The ALD consist of the complex geometries can be conformally coated reaction chamber part and the supply part for [19, 20]. In the case of Al2O3 ALD, in the first reactants, carrier gases and purge gases. The half-reaction trimethylaluminum (Al(CH3)3) illustration of the Fig. 2 are as follow, (1) Reaction chamber, (2) Shower head, (3) 8 Substrate holder, (4) Reactant canister, (5) 7 Carrier & purge gas, (6) Diaphragm valve, (7) Vacuum gauge, (8) Mass flow controller, (9) Inlet Outlet Control system. The typically gas flow mechanism of the 6 9 existing ALD systems are generally classified 5 5 10 4 4 11 3 2 1 Fig. 2. Schematic of ALD process (1.precursor A, 2.precursor B, 3.gas cylinder, 4.precursor control valve, 5.control valve, 6.check valve, 7.substrate, 8.ALD chamber, 9.pressure gauge, 10.needle valve, 11.vacuum pump). Fig. 3. Schematic illustration of the ALD construction [23]. E. Riyanto et al. / Mechatronics, Electrical Power, and Vehicular Technology 03 (2012) 65-72 67 into two categories, these are the laminar gas III. GROWTH THEORY flow type which have advantages on the high The requirements of the amorphous materials material utilization efficiency and minimization growth are the surface mobility of the adsorbed of the reaction volume with inherently precursor fragment should be so low that the disadvantages on the thickness non-uniformity precursor fragment is localized at the point where due to source depletion at inlet area makes it it first adheres to the surface, as well as the unsuitable for large area deposition, on the other network of reactive sites should provide more hand the shower-head type has uniform source location possibilities than the atomic arrangement flux, but a long purge time due to the large for the film material. This can be achieved if the reaction volume and the low conductance of the adsorbed precursor fraction is capable of forming shower-head hole makes it difficult to realize a bonds to both bridging and terminating atoms. pure ALD process [24]. An experimental example for film formation under such condition could be growth of Al2O3 B. Reaction Mechanism by Al(CH3)3 and H2O. This system has a The mechanisms that have been identified for flexibility in the network of reactive sites in the bonding gaseous reactants on solid supports in a way that Al(CH3)x may form relatively strong saturating manner are illustrated with molecule bonds to both terminating and bridging oxygen MLn used as an example. In MLn, M is a central atoms, and thus disturb a repetitive construction metal atom, L is a ligand attached to it and n is pattern needed in order to form a crystalline the number of ligands. MLn can be represented material [17]. Al(CH3)3 [25]. Al2O3 ALD is a particularly robust and well- The most common example of saturating gas- defined ALD system [14], and can be considered solid reactions is ligand exchange reaction, where a rather typical and “ideal” ALD process [26]. the reactant molecule (ML ) is split and one of its n Al2O3 ALD films can be pinhole-free as ligands (L) combines with a surface group (a) to demonstrated by electrical instruments and can form a volatile compound that is released as a be deposited on polymer substrates [14]. One basic condition for a successful ALD process is ׀׀ gaseous reaction product (aL) [25]. Symbol denotes the surface. that the binding energy of a monolayer chemisorbed on a surface is higher than the (MLn-1 + aL (g) (1 – ׀׀ (a + MLn (g – ׀׀ binding energy of subsequent layers on top of the Water and trimethylaluminum are commonly formed layer, that it can be controlled by the used as precursors in the deposition of Al2O3 by reaction temperature.
Details
-
File Typepdf
-
Upload Time-
-
Content LanguagesEnglish
-
Upload UserAnonymous/Not logged-in
-
File Pages8 Page
-
File Size-