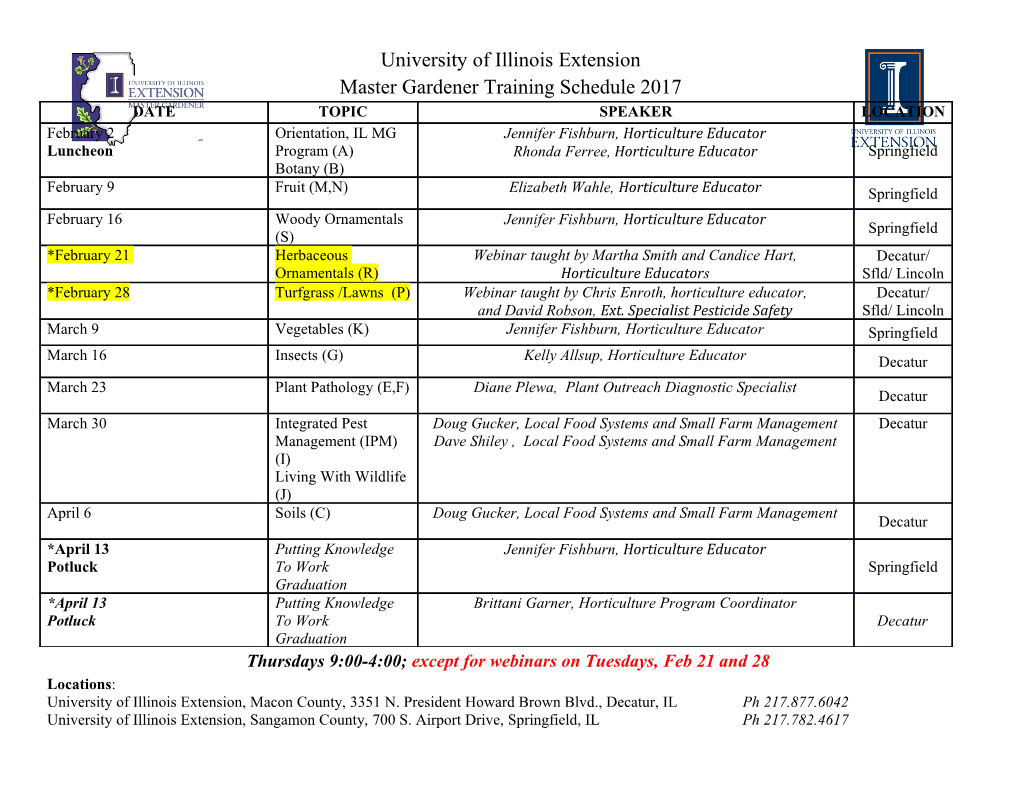
Purdue University Purdue e-Pubs Birck and NCN Publications Birck Nanotechnology Center 7-6-2011 Single-Step Fabrication and Characterization of Ultrahydrophobic Surfaces with Hierarchical Roughness Susmita Dash Birck Nanotechnology Center, Purdue University, [email protected] Niru Kumari Birck Nanotechnology Center, Purdue University, [email protected] Mercy Dicuangco Birck Nanotechnology Center, Purdue University, [email protected] Suresh V. Garimella Birck Nanotechnology Center, Purdue University, [email protected] Follow this and additional works at: http://docs.lib.purdue.edu/nanopub Part of the Nanoscience and Nanotechnology Commons Dash, Susmita; Kumari, Niru; Dicuangco, Mercy; and Garimella, Suresh V., "Single-Step Fabrication and Characterization of Ultrahydrophobic Surfaces with Hierarchical Roughness" (2011). Birck and NCN Publications. Paper 1507. http://dx.doi.org/10.1115/IPACK2011-52046 This document has been made available through Purdue e-Pubs, a service of the Purdue University Libraries. Please contact [email protected] for additional information. Proceedings of the ASME 2011 Pacific Rim Technical Conference & Exposition on Packaging and Integration of Electronic and Photonic Systems InterPACK2011 July 6-8, 2011, Portland, Oregon, USA InterPACKIPACK202011-11-5205204646 SINGLE-STEP FABRICATION AND CHARACTERIZATION OF ULTRAHYDROPHOBIC SURFACES WITH HIERARCHICAL ROUGHNESS Susmita Dash, Niru Kumari, Mercy Dicuangco and Suresh V. Garimella Cooling Technologies Research Center, an NSF IUCRC School of Mechanical Engineering and Birck Nanotechnology Center Purdue University West Lafayette, Indiana 47907-2088 USA [email protected] ABSTRACT , thereby controlling the extent of the liquid-air interface. Hydrophobic surfaces with microscale roughness can be Sub-micron scale roughness coupled with micro-level rendered ultrahydrophobic by the addition of sub-micron scale roughness can render a surface ultrahydrophobic and impart roughness. A simple yet highly effective concept of fabricating improved non-wetting properties in comparison to single-tier hierarchical structured surfaces using a single-step deep roughness. Ultrahyrophobic surfaces are non-wetting surfaces reactive ion etch process is proposed. Using this method the characterized by high contact angles (>150⁰), a low sliding complexities generally associated with fabrication of two-tier angle, and low contact angle hysteresis [2-4]. Hierarchical roughness structures are eliminated. Experiments are roughness is commonly encountered in nature; the extreme conducted on two double-roughness surfaces with different water-repellent characteristic of lotus leaves arises from a surface roughness, achieved by varying the size of the double-roughness structure consisting of nanoscale waxes on microscale roughness features. The surfaces are characterized microscale bumps [5]. in terms of static contact angle and roll-off angle and compared with surfaces consisting of only single-tier microscale Surfaces with such extreme hydrophobicity have important roughness. The robustness of the new hierarchical roughness applications in the development of artificial self-cleaning surfaces is verified through droplet impingement tests. The surfaces and developing water-proof clothing [6] and offer a hierarchical surfaces are more resistant to wetting than the wide range of promising applications including their use in single roughness surfaces and show higher coefficients of microfluidic-based technologies such as lab-on-chip devices, restitution for droplets bouncing off the surface. The droplet microelectromechanical systems (MEMS), and microarray dynamics upon impingement are explored. biochips. An important heat transfer application consists of developing surfaces for dropwise condensation. Dropwise 1. INTRODUCTION condensation is desirable in many heat transfer applications since the heat transfer coefficient associated with dropwise The contact angle of a droplet when placed on a surface is condensation is an order of magnitude higher than that by determined by surface energy as well as surface morphology filmwise condensation. Dropwise condensation is, however, [1]. The morphology of the surface determines whether a not readily achieved on single-tier roughness structures [7]. It droplet will remain in a Cassie (non-wetting) or a Wenzel was recently demonstrated that condensation on hierarchical (wetting) state (Figure 1a and Figure 1b respectively). roughness structures leads to condensation in the form of drops Superhydrophobicity may be imparted to a surface by carefully [8]. Since hydrophobic surfaces resist the formation of a liquid engineering the surface topology and controlling the ratio of film, surface corrosion is also mitigated. areas of the top surface of the pillars to the total base surface 1 Copyright © 2011 by ASME Downloaded From: http://proceedings.asmedigitalcollection.asme.org/ on 12/17/2013 Terms of Use: http://asme.org/terms single-roughness substrates. Droplet impingement experiments are then carried out for the two double-roughness surfaces to test the robustness of their hydrophobicity. Droplet dynamics on the double-roughness surfaces are explored and compared with droplet behavior on surface with single-roughness elements. 2. SAMPLE PREPARATION AND EXPERIMENTAL SETUP (a) (b) The fabrication procedure developed in the present work eliminates the typical two-step process to create double Figure 1. Schematic illustration of droplet wetting states: roughness structures. The surfaces fabricated consist of silicon (a) Cassie, and b) Wenzel. pillars as the larger roughness element. Photoresist residue is formed on the pillars during the deep reactive ion etch process; The wide range of applications of hierarchical hydrophobic this residue is in the form of ~ 1 µm strands stacked on top of surfaces has encouraged active research in this field. Different the silicon pillars and provides the second-tier roughness. The methods of fabricating such hierarchical surfaces [2, 9] to attain advantage of this method is that a double-roughness surface is ultrahydrophobicity have been demonstrated. The fabrication obtained after a single deep reactive ion etch step. All of double-roughness structures typically involves the fabrication for this work was carried out at the Birck fabrication of the larger-sized features on a substrate (by Nanotechnology Center at Purdue University. standard lithography methods) followed by the deposition of smaller-sized roughness elements on these larger features [2, 9, Silicon wafers with 1 µm thermally grown oxide layers 10]. Efforts at fabricating and testing robust superhydrophobic were used as the substrates. A layer of positive photoresist AZ surfaces which can be easily fabricated and commercially used 1518 was spin-coated and lithographically patterned on the continue to be reported. wafer. A wet-etch process is used to selectively etch the oxide layer from the surface. The oxide layer along with the Analytical and experimental research has corroborated the photoresist acts as the etch mask for the deep reactive ion etch strong effect of surface morphology on the impact behavior of a process. The etching process results in the creation of silicon water droplet and its ability to bounce off the surface [6, 11- pillars. At the same time, the high temperature and ions 14]. Jung and Bhushan [6] demonstrated better water produced in the plasma interact with the photoresist and cause repellency on hierarchical surfaces as compared to single it to distort and form small roughness elements on the pillars roughness elements. They formulated an expression for the which lead to a second-tier roughness. The etch rate for silicon critical velocity of the droplet (based on the capillary pressure was observed to be approximately 4 µm per minute. A and Bernoulli pressure) beyond which it transitions to a Wenzel minimum of 4 minutes of etch time was required for the state on textured surfaces. Varanasi et al. [15] developed a formation of the second-tier roughness structures. The surfaces pressure-balance model to arrive at a condition for droplet are then spin coated with 0.1% solution of Teflon-AF 1600 infiltration into the air gap between the surface structures. (DuPont, Wilmington, DE) in FC-77 (3M, St. Paul, MN) to Denser textured surfaces were expected to provide greater impart hydrophobicity. The thickness of the Teflon layer is capillary pressure and superior resistance to Wenzel wetting of approximately 50 nm and hence the overall roughness of the impacting droplets. primary roughness as well as the sub-micron roughness is not affected by the Teflon coating. The single-roughness surfaces 1 The purpose of the present work is to explore a one-step and 2 used for comparison against the results from double- fabrication methodology for double-roughness surfaces and roughness surfaces are fabricated with the primary geometrical eliminate the complexity involved in producing the second parameters same as those for the double-roughness surfaces 1 layer of sub-micron roughness. Pillars of square cross section and 2 respectively using the negative photoresist SU-8 with are carefully engineered so that the single-roughness features standard lithography. The pillars are subsequently coated with inherently maintain the droplets in a stable Cassie state. The Teflon to impart superhydrophobicity. The pillar geometry of double-roughness surfaces are fabricated with the same primary the two double-roughness surfaces fabricated is provided in roughness
Details
-
File Typepdf
-
Upload Time-
-
Content LanguagesEnglish
-
Upload UserAnonymous/Not logged-in
-
File Pages9 Page
-
File Size-