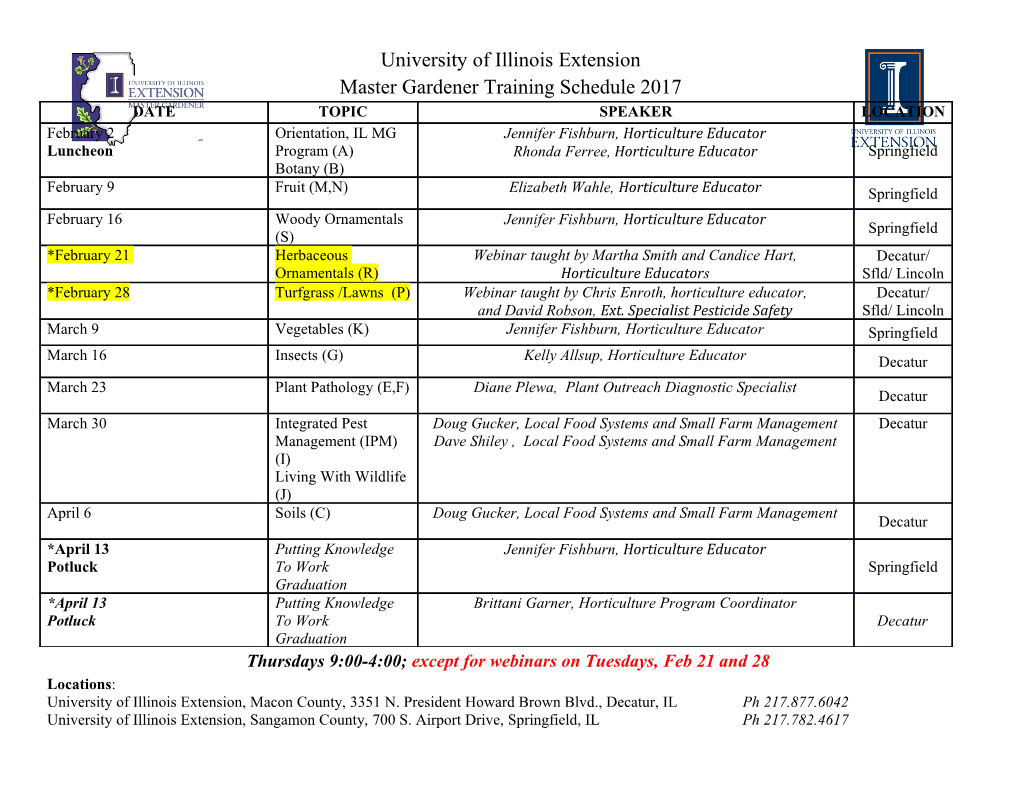
Energy 111 (2016) 884e892 Contents lists available at ScienceDirect Energy journal homepage: www.elsevier.com/locate/energy Catalytic and thermal depolymerization of low value post-consumer high density polyethylene plastic* * Bidhya Kunwar a, , Bryan R. Moser b, Sriraam R. Chandrasekaran a, ** Nandakishore Rajagopalan a, Brajendra K. Sharma a, a Illinois Sustainable Technology Center, Prairie Research Institute, University of Illinois, Urbana-Champaign, IL 61820, USA b United States Department of Agriculture, Agricultural Research Service, National Center for Agricultural Utilization Research, Peoria, IL 61604, USA article info abstract Article history: The feasibility of catalytic and non-catalytic pyrolytic conversion of low value post-consumer high Received 15 July 2015 density polyethylene (HPDE) plastic into crude oil and subsequent distillation was explored. Translation Received in revised form of optimized conditions for catalytic and non-catalytic pyrolysis from TGA to a bench-scale system was 25 April 2016 validated using another kind of plastic (HDPE). The properties of the plastic crude (PC) oil and residue Accepted 5 June 2016 were studied for boiling point distribution; molecular weight distribution; elemental composition; and thermal degradation. The plastic crude oils had properties similar to conventional crude oil. The resulting PC oils were distilled into motor gasoline, diesel #1, diesel #2, and vacuum gas oil fractions. An increase Keywords: TGA in gasoline and diesel-range fractions was observed with Y-zeolite and MgCO3 catalysts, respectively. Pyrolysis Diesel and vacuum gas oil fractions were the major products in the absence of catalyst. The distillate Catalyst fraction was characterized for fuel properties, elemental composition, boiling point, and molecular Gasoline weight distribution. The fuel properties of the diesel-range distillate (diesel fraction) were comparable to Diesel those of ultra-low sulfur diesel (ULSD) fuel. Market demand, growth, and value of end products will Ultra-low sulfur diesel dictate which process, non-catalytic or catalytic (Y-Zeolite/MgCO3), is best suited for providing the product portfolio for a particular scenario. © 2016 Elsevier Ltd. All rights reserved. 1. Introduction landfills is not the most efficient way of carbon utilization. Thermochemical conversion is an attractive route to produce Polyethylene (PE) and polypropylene (PP) are two major plastics fuels from these waste plastics while diverting them from landfills used widely in packaging, electronics, storage, and personal care [1]. The plastic fuels have fuel properties comparable to fossil fuels products due to their low cost, durability, and versatility [1]. Proper [3]. PE and PP are polymers containing only carbon and hydrogen. end-of-life management of these waste plastics is a serious prob- Therefore, unlike biofuels, the need for further upgrading of plastic lem throughout the world, as only about one percent of plastics are fuels can be avoided. The plastic fuels have high calorific value and recycled [2]. The disposal of plastics in landfills poses a major are non-acidic and non-corrosive due to the absence of water and environmental concern, because they may take centuries to oxygen, unlike biofuel [3e7]. Sharma et al. obtained approximately degrade naturally and they currently occupy a large volume of 20% motor gasoline, 41% diesel #1, 23% diesel #2, and 16% vacuum expensive landfill space [2]. In addition, leaving that carbon in gas oil-range fractions from distillation of crude oil obtained from non-catalytic pyrolysis of HDPE at 440 C [3]. A recent study by Kaimal and Vijayabalan showed that oil synthesized from the waste plastic has similar properties to that of diesel [8]. It has also been * Disclaimer: Mention of trade names or commercial products in this publication shown that the waste plastic oil can be used in engines without any fi is solely for the purpose of providing speci c information and does not imply modifications [8]. One thermochemical conversion process is py- recommendation or endorsement by the U.S. Department of Agriculture. USDA is an equal opportunity provider and employer. rolysis which is a thermal degradation method in which larger * Corresponding author. polymeric chains and biomass are broken into smaller hydrocar- ** Corresponding author. bons in absence of air/oxygen [9e15]. A wide distribution of hy- E-mail addresses: [email protected] (B. Kunwar), [email protected] drocarbons is obtained with changes in temperature and reaction (B.K. Sharma). http://dx.doi.org/10.1016/j.energy.2016.06.024 0360-5442/© 2016 Elsevier Ltd. All rights reserved. B. Kunwar et al. / Energy 111 (2016) 884e892 885 time [16]. For instance, as the temperature increases to approxi- and then these optimized conditions were demonstrated on one mately 700 C, the weight percent of gaseous products increases kind of plastic (polypropylene) in a pyrolysis system. The objective [7]. in that previous study was to demonstrate translation of optimized However, thermochemical conversion requires high energy conditions from TGA to a bench-scale system. In the current study, which often renders it to be not economically feasible [16]. Eco- we validated that approach, where optimization conducted on nomics can be improved, though, through the use of a catalyst milligram scale using TGA was translated to bench scale on a ki- during pyrolytic conversion [16]. Lowering the reaction tempera- logram scale, using another kind of plastic, i.e. hard-to-recycle post- ture is always desirable to reduce energy input. Since catalysts consumer HDPE plastic storage boxes. These low value post- lower the activation energy required for pyrolysis, thereby reducing consumer HPDE plastic storage boxes are hard to recycle because the reaction temperature, which leads to reduction in energy they do not recombine well with other plastics during the recycling consumption, reaction time, and narrowing product distribution process and do not melt easily at lower temperatures. An alterna- [17]. The choice of the specific catalyst is significant because it af- tive disposal route for these materials is conversion to fuels through fects yield and product selectivity [14]. For example, zeolites have pyrolysis, there by increasing the carbon utilization efficiency. been shown to increase the yield of gasoline-range hydrocarbons Therefore, this study focused on understanding the effects of from 47% to 70% [14]. Common catalysts used in thermochemical catalyst type (acidic or basic), time, and temperature on the yield conversion include fluid catalytic cracking (FCC), reforming, and and quality of crude oil. The results from the study are important to activated carbon catalysts [14]. FCC catalysts include zeolite enhance the understanding of energy recovery through catalytic [4,6,14,18], silica-alumina [19], and clay [4,20]. Aside from chemical pyrolysis route from feedstocks that would otherwise be disposed properties, the physical properties of the catalysts (such as surface in landfills. Plastic crude (PC) oil thus produced had a heating value area, pore size, pore volume, pore size distribution, pore structure, of approximately 50 MJ/kg and contained roughly 85% carbon and etc) are also very important. Zeolites have high acid strength, high 14% hydrogen, which is similar to commercial motor gasoline and stability, and low coke formation, but their pore size (<1.0 nm) may diesel [3]. Furthermore, PC oils obtained from the pyrolysis of HDPE become a limitation for big molecules [6,13,21]. The most widely storage boxes were distilled into motor gasoline, diesel #1, diesel used catalysts are zeolite-based, such as HZSM-5, Hb, and zeolite #2, and vacuum gas oil-range fractions and their properties were HY. MgCO3 has been studied as a basic catalyst for polyethylene studied and shown to meet ASTM specifications for petrodiesel. cracking [6,21]. MgCO3 has been shown to yield 50% gasoline and 50% diesel [14,21]. 2. Materials and methods Product yield and composition depends on a combination of suitable choice of catalyst, temperature, and particle size [22]. The 2.1. Materials product obtained from thermochemical conversion of PE and PP consists of a mixture of naphtha, gasoline, and light gas oil-range Waste HDPE storage boxes were collected from Eagle Enter- fractions. The yield of gasoline-range hydrocarbons increases prises Recycling Inc (Galva, IL) and were shredded to a particle size with increasing pyrolytic temperature but the yield of gaseous of ~5 mm diameter using an AEC Nelmor (Blade Machinery, Inc., Elk products also increases. Kyaw et al. obtained the highest yield of Grove Village, IL) shredder. All chemicals and reagents used in this liquid fuel (76%) and gases (28.52%) at 370 C from mixed plastics study were obtained from Sigma-Aldrich Corp (St Louis, MO) and [23]. Kamal et al. studied pyrolysis of mixed plastics containing were used as received. ~60% PE, ~30% PP, and remaining other plastics at two different temperatures 900 C and 425 C [24]. They found that there was a 2.2. Thermogravimetric analysis (TGA) of HDPE to determine difference in the calorific values of the product with 46.8 MJ/kg at optimum pyrolysis temperature 900 C and 41.8 MJ/kg at 425 C. The higher temperature reduced the levels of potentially carcinogenic compounds such as boric acid Thermal degradation of waste HDPE plastics was studied using a and cyclopentanone [24]. Olefin content has been reported to model Q50 TGA (TA Instruments, Schaumberg, IL) under an inert decrease with increasing reaction temperature [9]. atmosphere of pure nitrogen with a flow rate of 60 mL/min. TGA As mentioned previously, the product distribution can be experiments were designed to determine optimal operating con- manipulated by the suitable choice of a catalyst. Some catalysts ditions and suitable catalysts for HDPE depolymerization. A sample have selectivity toward gasoline-range hydrocarbons while others size of approximately 18e20 mg was used for each study. For cat- have selectivity toward diesel [16]. For example, HZSM-5 increases alytic studies, a sample-to-catalyst ratio of 10:1 was maintained gasoline yield relative to other catalysts [4].
Details
-
File Typepdf
-
Upload Time-
-
Content LanguagesEnglish
-
Upload UserAnonymous/Not logged-in
-
File Pages9 Page
-
File Size-