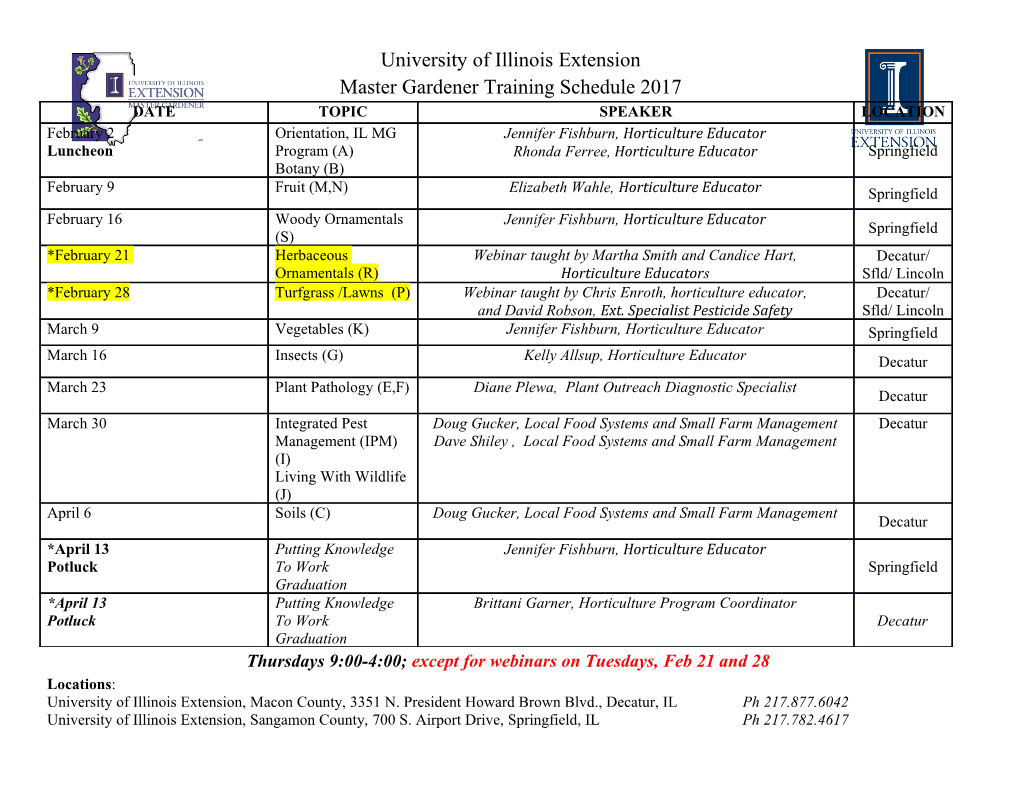
METHANOL, a Multi Source and Multipurpose Energy Carrier Alternative IEA Bioenergy / IETS: System and Integration Aspects of Biomass-based Gasification Gothenburg November 19, 2013 Ingvar Landälv Senior Project Manager LTU 1 AGENDA • Turning alkali in the feedstock to an advantage – Why has Chemrec focused Black Liquor so long? – Is technology ready for commercialization? – Can the BLG developments be used for other applications? • Future Energy System Scenarios – The need to look at the total cost of a new energy system – An example from the marine sector – An example from the HD vehicle sector • Summary 2 11/25/20 2 13 Today’s commercial Forrest Industry has two main legs TODAY Forest Logs Pulp Wood Saw- mill RecoveryPulp Boiler Wood Mill Products Pulp Mill Pulp NewNew ValueValue StreamsStreams fromfrom ResidualsResiduals && SpentSpent PulpingPulping LiquorsLiquors 3 BLG is a transformative technology converting pulp mills to biorefineries making efficient use of the third fraction from the forest TOMORROW Forest Logs Pulp Forest Wood Residual Saw- mill RecoveryPulpCombined Recovery Boiler Wood Milland Fuel Generation Products Pulp Mill Fuel Pulp NewNew ValueValue StreamsStreams fromfrom ResidualsResiduals && SpentSpent PulpingPulping LiquorsLiquors 4 BL Energy is a large renewable energy source in some areas of the World e.g. Sweden Nr Mill owner, name Nominal Current Year of capacity capacity start-up Approx: 1 Billerud, Karlsborg 1250 1500 1980 2 SCA, Munksund 600 1965 5000 MW 3 Smurfit Kappa, Lövholmen 1450 1950 1972 4 SCA, Obbola 1000 2007 Black Liquor 5 Husum, M-Real 750 1100 1965 1 6 Husum, M-Real 700 2000 1978 2 3 7 Husum, M-Real 1100 1300 1988 8 Domsjö, Domsjö 375 1958 Close to 20 9 Domsjö, Domsjö 375 1964 10 Dynäs, Mondi 915 1978 large plants 4 11 Östrand, SCA 3300 2006 5 6 7 8 9 12 Iggesund, Holmen 520 900 1966 10 13 Iggesund, Holmen 520 900 1967 11 14 Vallvik, Rottneros 760/1000 1200 1974/1999 15 Korsnäs, Korsnäs 865 1330 1968 1213 16 Korsnäs, Korsnäs 1550 1550 1987 14 17 Skutskär, StoraEnso 585 650 1967 15 16 18 Skutskär, StoraEnso 1900 2800 1976 17 18 19 19 Frövi, Korsnäs 520 1260 1970 20 23 20 Skoghall, Stora Enso 2200/(3350) 2005 22 21 21 Gruvön, Billerud 2500/(3300) 2000 24 22 Billingsfors, Munksjö 230 330 1976 25 23 Bäckhammar, Wermland Paper 570 750 1976 24 Aspa, Munksjö 510 1200 1973 27 26 25 Skärblacka, Billerud 1250 1850 1976 26 Värö, Södra 2500 2002 28 27 Mönsterås, Södra 4000 1996 5 28 Mörrum, Södra 2000 22605 1995 1 1 BL Energy is a substantial energy source in some states in the US e.g. Georgia More than 100 suitable pulp mills In North America with 200-400 MW of Black Liquor per plant In the World: approx. 80 000 MW Black Liquor or 250 – 300 large 6 plants 6 Chemrec technology generates good quality raw syngas with three main process steps: Gasification, Quenching and Cooling GAS COOLER Black liquor GASIFICATION Cooling water Atomising medium Boiler feed water* OK raw syngas Oxygen REACTOR LP- steam* SEPARATION PARTICULATE OF GAS AND REMOVAL AND SMELT Raw gas GAS COOLING MP- QUENCH steam* Green Condensate liquor Weak wash * Cooling water 7 in DP1 BL to BioDME: Well proven Concept by Chemrec and LTU in the Pilot Plant in Piteå Raw MeOH Black storage Liquor OK raw syngas BioDME DP-1 Plant O2 Active WG Amine MeOH DME Distil- C Abs Shift Wash Synth. Synth. lation 8 Development Plant for Oxygen-blown high pressure BL gasification • Located at the SmurfitKappa mill in Piteå, Sweden • Oxygen-blown and operated at 30 bar(g) • Capacity 20 metric tons per day of black liquor solids (3 MW(th)) • Used for technical development and design verification • Started up 2005 –Now in operation more than 21 000 hours (10/2013). • Raw syngas converted to BioDME since 2011 (about 6000 h) • Operations: 10 operators in 5 shifts 9 Accumulated BioDME Production is close to 600 tons in October 2013 500 H G 400 F D E 300 A - Authority inspection C B - Maintenance 200 C - Holidays B D - Repair of ceramics Produced BioDME, ton E - New equipment 100 F - Catalyst replacement, change of owner A G - Maintenance H - Replacement of ceramics & catalyst 0 jul.13 jul.12 jan.13 jan.12 jun.13 jun.12 okt.12 feb.13 feb.12 apr.13 apr.12 maj.13 maj.12 sep.12 dec.12 dec.11 aug.13 aug.12 nov.12 mar.13 mar.12 10 Chemrec technology ready for industrial scale and can be built by world-class EPCs with adequate risk allocation • EPC 1: …one of few mature and New Bern, 1st gen, 47 000 hrs feasible technologies for large-scale production … to produce fuels from forest-based biomass ...” • EPC 2: “...in principle willing to provide customary EPC wrap around guarantees ...” • EPC 3: “...LSTK service with customary Piteå, 2nd gen, >21 000 hrs wrap around guarantees... ” • Oil major evaluation (10 experts): “No showstoppers for industrial scale-up”. • Piteå demo plant producing methanol and DME using commercial processes. 11 Chemrec Status as per January 2013 Dec 31, 2012: Chemrec Piteå companies including pilot plants sold by Chemrec AB to LTU Holding AB, Jan 1, 2013: 17 pilot plant staff employed by LTU. Dec 31, 2012: License agreement between licensor Chemrec AB & HaldorTopsøe with LTU and LTU Holding. Technology rights stay with licensors. Jan 30, 2013: Consortium Agreement between parties involved in continued R&D. Chemrec has reduced staff awaiting long term stable regulations for advanced biofuels. Two Chemrec Stockholm staff temporarily on leave assigned to LTU Continued operation of the plants as part of LTU Biosyngas Program SULPHUR Black Liquor ABSORPTION C.W Atomizing medium BFW White/Green Liquor Oxygen GAS COOLER GASIFIER LP- BFW St. CLEAN Raw Syngas SYNGAS MP-Steam QUENCH FLARE GREEN Condensate LIQUOR 12 Weak Wash 10/18/20091 16 LTU Biosyngas Centre Program 13 The BL to BioDME facility is the backbone in the LTU Biosyngas Centre Program Black Liquor BioDME DP-1 Plant O2 Active WG Amine MeOH DME Distil- C Abs Shift Wash Synth. Synth. lation 14 LTU Biosyngas Program planned for 2013-2016 WP1 Pilot scale experiments WP2 Catalytic gasification WP3 Solid fuel gasification Powder WP3 ETC EF WP4 Novel syngas cleaning gasifier WP5 Catalytic conversion WP6 Containment materials Torrefied Mtrl Others WP7 Field tests WP8 Electrofuels and new concepts Cleaning Pyrolysis oil BioMeOH WP2 WP4 Black Membranes WP7 Liquor 25-30 bar > 100 bar BioDME WP6 DP-1 Plant Active WG Amine MeOH DME Distil- C Abs Shift Wash Synth. Synth. lation WP1 CO, H Catalytic WP5 O 2 H 2 2 Process WP8 Development Electro- Existing lysis CO2 facilities Fuel Cells Future development The Renewable H2O Syngas Highway 15 Biomass flow from the forest can be increased adding pyrolysis oil to the black liquor flow TOMORROW (3) Forest Logs Forest Pulp Residues PO Wood Production Saw- mill RecoveryPulpCombined Recovery Boiler Wood Milland Fuel Generation Products Pulp Mill Fuel Pulp 1611/25/20 1 13 6 WP2: Co-gasification BL/PO – some impressions from the lab TGA and DTF lab activities PO/BL mixing study during spring 2013 • Lignin precipitation needs to be considered above 20-25% PO • No solids up to 20% PO 17 WP 2: Co-gasification of BL and PO offers many potential advantages All calculations thus assume that BL/PO can be gasified at same temperature as BL is today. Syngas Capacity increases Energy efficiency for gasification about 100% by adding about of added PO is 80-85% 25% PO to the BL (by weight) 400% 100% 95% 350% 90% 300% 85% energy) 250% 80% SF‐LHV total 200% 75% CGE (syngas H2CO total 70% 150% SF‐LHV incr PO 65% H2+CO incr PO 100% Production 60% 50% 55% 0% 50% 0% 10% 20% 30% 40% 50% 0% 10% 20% 30% 40% 50% PO mix (part of total feed) PO mix (part of total feed) Figure shows simulated increased Figure shows simulated gasifier production of final liquid biofuel product energy efficiency of total mixed feed at fixed BL feed (i.e. for specific mill) (solid) and for added PO (dashed) 18 WP 2: Key physical properties of PO/BL mixtures are promicing based on lab tests Viscosity Surface tension 1 000,00 Hanging droplet 100°C 45 100,00 40 35 s) 10,00 30 (mN/m) 0% 25 10% viscosity(Pa 20% 20 1,00 tension 30% Black liquor Shear 15 10% pyrolysis oil Surface 10 0,10 20% pyrolysis oil 5 30% pyrolysis oil 0 0,01 0 102030405060 0,1 1 10 100 1000 10000 100000 Shear rate(s‐¹) Time (s) 19 WP2: Drop tube furnace experiments shows carbon conversion of PO/BL mixtures to be at least as good as BL alone Gasification ash microscopy (same magnification) BL at 1000˚C BL at 1200˚C PO(20) /BL(80) at 1000˚C 20 WP2: Techno-economic study co-gasification - preliminary results indicate good profitability • Case study: Rottneros Vallvik – medium sized pulp mill – good data from black liquor gasification study available • Methanol plant alternatives evaluated – Black liquor gasification ~200 MW BL – Two co-gasification alternatives • Extend methanol production by adding 25% and 50% pyrolysis oil • Preliminary results indicate very favorable production cost for realistic pyrolysis oil price scenarios – Economies of scale and high efficiency contribute 21 WP2: Techno-economic study co-gasification - preliminary results indicate good profitability • Case study: small/medium sized pulp mill • Methanol plant alternatives – Black liquor gasification ~200 MW BL – Two co-gasification alternatives – 25% and 50% pyrolysis oil MeOH production cost 9000 MeOH production cost Realistic price scenario • First plant CAPEX@10% annuity 8000 • Nth plant will give lower CAPEX 7000 Pessimistic price scenario 6000 MeOH price reference levels for low-blend 5000 into gasoline 4000 • Pessimistic 6500 SEK/t based on 2011 3000 Rotterdam EtOH price volume equivalence • Realistic 8500 SEK/t projection based on Case 25 2000 RED and proposed ETD 1000 Case 50 (biofuel mandate) MeOH production cost [SEK/ton] 0 300 400 500 600 700 800 900 1000 PO cost [SEK/MWh] 22 Potential to test Liquid Organic Waste (LOW) in the LTU Green Fuels Plant Powder ETC EF gasifier Torrefied Mtrl Others Pyrolysis oil Cleaning BioMeOH LOW Black Membranes Liquor 25-30 bar > 100 bar BioDME DP-1 Plant Active WG Amine MeOH DME Distil- C Abs Shift Wash Synth.
Details
-
File Typepdf
-
Upload Time-
-
Content LanguagesEnglish
-
Upload UserAnonymous/Not logged-in
-
File Pages60 Page
-
File Size-