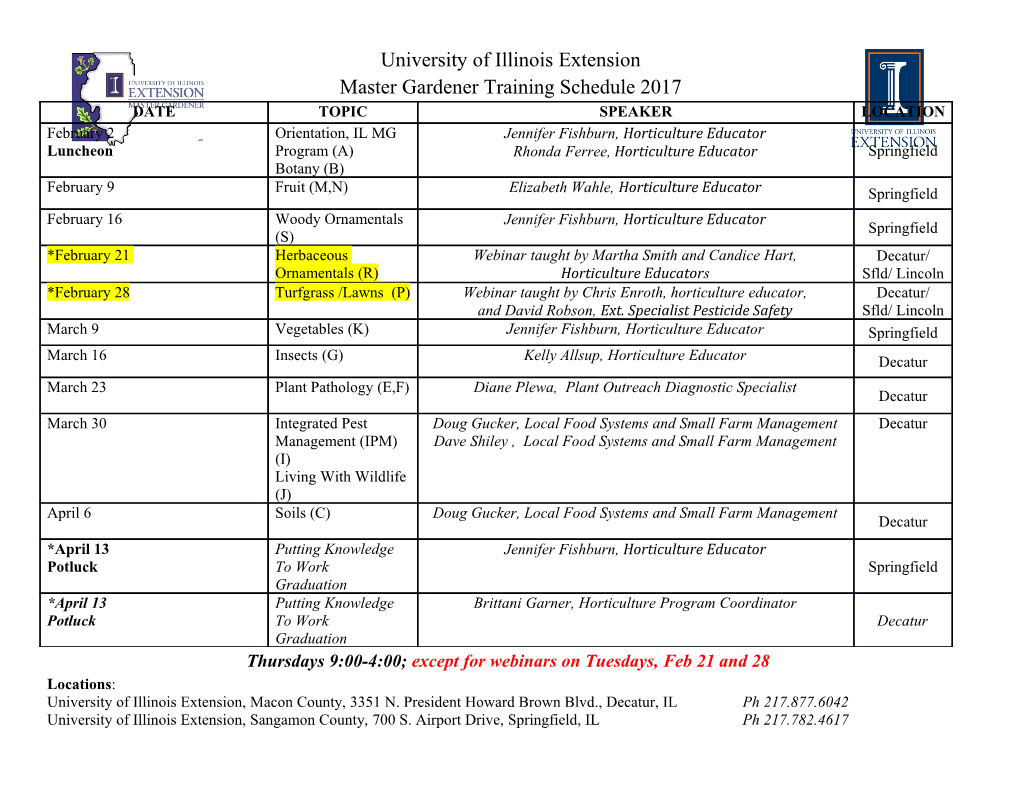
SPE-128 THE CATALYSIS OF POTASSIUM CARBONATE SOLUTIONS IN CARBON DIOXIDE ABSORPTION By A. G. Eickmeyer, Chemical Engineering Consultant Prairie Village, Kansas ABS~:RACT bing. The activity o£ hot potassium car­ THEORY AND DEPINITIONS Downloaded from http://onepetro.org/speatce/proceedings-pdf/61fm/all-61fm/spe-128-ms/2087284/spe-128-ms.pdf by guest on 01 October 2021 bonate solutions has been £ound to be a function of contaminants, having a de­ The absorption of an acid gas in leterious effect, and catalysts, which any alkaline solution is classed as activate the solution. A small amount chemi-sorption, that is, absorption ll of "Catacarb catalyst cancels the e£­ accompanied by chemical reaction. The £ect o£ contamination and larger amounts rate o£ chemical reaction determines give a much more active solution than the size of the towers required by the pure potassium carbonate. In commercial process. plant tests in existing carbonate Unlike caustic, a carbonate solu­ plants, the Catacarb Process resulted tion has very few hydroxyl ions to re­ in increased capacity, reduced steam act directly with CO , Therefore, it usaze, and less residual CO , In 2 2 is believed that CO2 must £irst become new plant construction, ~ ss equipment ·hydrated, or react with water to £orm and utility requirements o£ the Catacarb carbonic acid, which in turn reacts Process permit savings in capital in­ with a carbonate ion to form two bi­ vestment and operating costs. carbonate ions. INTRODUC '1'1 ON (1) CO2 • H2 0 = H2 CO 3 The hot potassium carbonate £r~cess, developed by the Bureau o£ Mines, ,-, has been applied extensively in recent years to CO 2 removal in the puri£ica­ Con£irmation o£ the reaction with tion of hydrogen and natural Gas. Most water is the finding, both in commercial of the hot carbonate units are in ammonia plant operations and laboratory experi­ plants, but use of the process for ments, that dilute solutions Which have treating natural gas, including sour a higher concentration of £ree water, gas, is increasing. The equipment in­ are more active than concentrated car­ volves the £amiliar absorber and re­ bonate solutions. The term "£ree generator. The usual process c cles water" takes into account the well­ have been previously described. 3 known fact that potassium ions are As compared with amine scrubbing highly hydrated, although the exact the main advantages o£ hot carbonate ratio o£ compined water to potassium are the elimination of heat exchange is uncertain4 and probably varies equipment and the lower steam and cool­ with concentration. ing water requirements. The disadvan­ As in any practical chemical tage of a hot carbonate system is the process, we are concerned with equi­ inability to secure a satis£actory de­ librium and with kinetics. Equilib­ gree o£ clean up in the scrubbed gas rium for the potassium carbonate­ except with very large towers, a more bicarbonate-C02-water system has been complicated process cycle or even a reported.S We now focus our attention second absorber operated at high pres­ on hereto£ore neglected kinetios or sure. solution activity, whioh is the rela­ ll This paper deals with "Catacarb , tive rate of approach to equilibrium. the catalytic process for CO 2 removal. In the Catacarb Process a catalyst 1s COMMERCIAL PLANT SOLUTIONS used to activate a carbonate solution in the absorption and desorption o£ A number o£ commercial carbonate carbon dioxide, thus overcoming the plant solutions have been analysed and above disadvantage o£ carbonate scrub- found to be more or less contaminated RP"R-128 with potassium salts of relatively converted gas, containing about 23% CO2 , strong acids, particularly potassium­ enters the absorber hot and saturated formate and sulfate. Such contaminants wi th steam. have a depressing effect on solution Comparisons are made before and activity. In other words, they are after Catacarb in three pairs of runs. activity poisons, as shown in Figure 1, In the first pair the CO? removal capa­ where the activity for five commercial city was increased by 40;0 while using plants is correlated. In order to the same amount of steam and rr~intaining eliminate the effect of differences in a 1% residual CO2 in the outlet gas. solution strength from plant to plant, Also the steam economy, that is pounds the activity of each solution has been of steam per thousand cubic feet of determined on the basis of 100 repre­ CO2 removed, was much improvec;l. Ste8J1l senting the activity of pure potassium economy was emphasized in the next pair carbonate solution of the same strength. of runs. vJith Catacarb, the steam was The contaminants are the results reduced until the residual CO2 reached Downloaded from http://onepetro.org/speatce/proceedings-pdf/61fm/all-61fm/spe-128-ms/2087284/spe-128-ms.pdf by guest on 01 October 2021 of reaction with other components of a 2.7% about the sa,ue as the 2.97~ ob- - the gas being scrubbed. Not only car­ tained during an uncatalyzed test peri­ bonate but all types of alkaline scrub­ od. Even though the gas rate was about bing solutions used for purifying manu­ 20% higher the steam economy was im­ factured hydrogen are more or less con­ proved by 4~b frOl,l 161 to 91 #/}1CF. taminated with formate as a result of In the third pair of runs at the same a very slow reaction of carbon monoxide gas rate, the residual CO was reduced 2 with hydroxyl -ions. Kinetic studies by 705'~ from 2.35& to 0.6~~. indicate that this undesired reaction The process cycle of commercial is catalyzed by traces of oxygen in the plant B is cooled split stream absorp­ gas. Sulfate results from oxidation of tion at 300 PSIG. The inlet gas con­ traces of hydrogen sulfide, which can tains abov.,t 15% CO2 , The towers of originate in direct contact coolers by Plant B were too snort for good per­ the action of sulfate-reducing anaerobic formance of a plain carbonate system. bacteria. Traces of oxygen also come The objectives in using Catacarb ~ere from air-saturated water in direct primarily to reduce the residual % contact coolers. Therefore, the use C02 and secondarily to improve the of a closed cooling system eliminates steam economy. It will be noted from both nuisances. Table 2 that, with only 5% Catacarb, 50% less residual CO was obtained CATACARB PROCESS while using 20% less 2 steam. Also the 10% lower cirCUlation rate gave an An extensive search for a non­ u~expected benefit, since it was pos­ toxic catalyst for the hydration of sible to shut down one of two opera­ carbon dioxide resulted in the develop­ ting pumps, thus sav'ing about ~50 .00 ment of "Catacarb". Catacarb proved per day in electricity. to be very effective in activating carbonate solutions in both absorp­ INTERPRETATION OF PLANT DATA tion and desorption of CO2 • The ef­ fect of various amounts of Catacarb In Table 2 the lean solution is on the activity of two commercial sho~~ to decrease in percent conversion plant solutions is shown in Figure 2. to bicarbonate with an increase in From this it appears that only one or Catacarb. This -1::; concrete evidence two percent of Catacarb would have can­ that Catacarb is effective in catalyzing celled the effect of contamination, and the desorption of carbon dioxide as that 8-10% makes actual plant solutions well as absorption. The better re­ several times as active as pure potas­ generated solution makes possible better sium carbonate. absorption in turn. The benefits of Catacarb have been Referrin~ again to Table 1, it demonstrated on a commercial scale by is noted that the residual CO with 2 plant tests ~n two different existing Catacarb varies with steam economy carbonate systems. Table 1 shows the or the ratio of steam to circulation benefits obtained from about 7% Catacarb rate. It follows that, if two stage in Plant A, which employed the simplest regeneration were use·d thus giving a type of process cycle, that is single high steam to solution ratio for the stage absorption at 360 PSIG with no minor stream, a much lower residual cooling of the solution. The gas flow CO would be obtained. Also it rate is measured before the shift con­ 2 should be noted that, with the activ­ verter in which an expansion of about ity bottleneck relieved, a more fa­ 25% in dry gas volume occurs. The vorable absorption temperature pat- 94 SPE-128 tern can be used in new plant design CONCL USI ONS to give better clean up. In the plant tests only 5-7% Catacarb was 1. The solution activity ~~d the per­ enough to give the desired results. formance of a hot carbonate system are Lab tests indicate fUrther bene~it a~fected adversely by formate and sul­ ~rom 10-15% Catacarb, which would be fate contamination, and beneficially used in new plant design. by the addition of Catacarb catalyst. ECONOMICS 2. Nominal amounts of Catacarb added to existing carbonate systems resulted Because of the above-'design in increased capacity, steam economy, factors, a single Catacarb system can and better clean up of the scrubbed gas. secure results in CO2 removal which ~wo heretofore required separate Downloaded from http://onepetro.org/speatce/proceedings-pdf/61fm/all-61fm/spe-128-ms/2087284/spe-128-ms.pdf by guest on 01 October 2021 scrubbing systems. For example, in 3. The use of the Catacarb Process is often economically attractive in the manufacture o~ hydrogen with a double shi~t of carbon monoxide con­ the design of new units and in the version, it has been common practice conversion of existing scrubbing systems.
Details
-
File Typepdf
-
Upload Time-
-
Content LanguagesEnglish
-
Upload UserAnonymous/Not logged-in
-
File Pages4 Page
-
File Size-