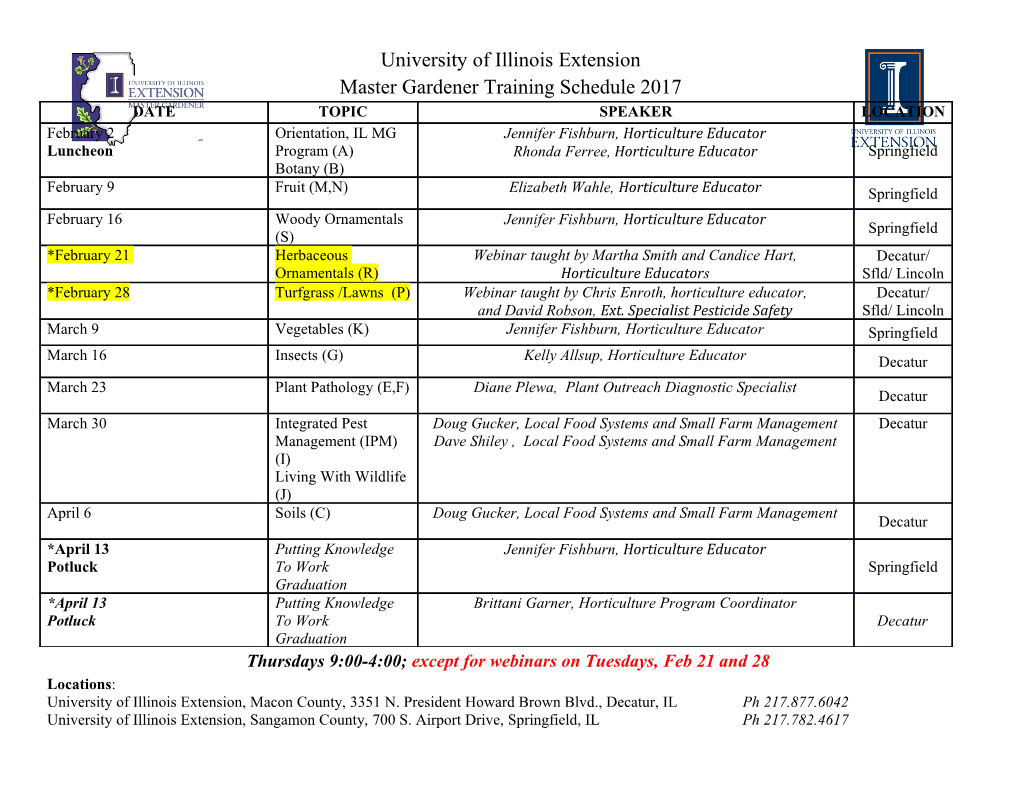
June 2009 Rev – 1.1 Photodetector Sensor Board SP1202S03RB User’s Guide © 2009 National Semiconductor Corporation. 1 http://www.national.com Table of Contents 1.0 Introduction..........................................................................................................................................3 2.0 Board Assembly ...................................................................................................................................3 3.0 Quick Start ...........................................................................................................................................3 4.0 Functional Description .........................................................................................................................5 4.1 Operational Modes.................................................................................................................5 4.1.1 The Computer Mode.........................................................................................5 4.1.2 The Stand-Alone Mode ....................................................................................5 4.2 Signal Conditioning Circuitry................................................................................................5 4.2.1 The Transimpedance Amplifier.......................................................................5 4.2.2 Light Source.......................................................................................................5 4.3 Power Supply.........................................................................................................................5 4.4 ADC Reference Circuitry.......................................................................................................5 4.5 ADC clock .............................................................................................................................6 4.6 Digital Data Output................................................................................................................6 4.7 Power Requirements and Settings..........................................................................................6 5.0 Installing and Using the Photodetector Sensor Board..........................................................................6 5.1 Board Set-up ..........................................................................................................................6 5.2 Quick Check of Analog Functions.........................................................................................6 5.3 Quick Check of Software and Computer Interface Operation ...............................................6 5.4 Troubleshooting.....................................................................................................................7 6.0 Board Specifications ............................................................................................................................7 7.0 Example Hardware Schematic .............................................................................................................8 8.0 Example Bill of Materials ....................................................................................................................9 Appendix: Summary Tables of Test Points and Connectors.....................................................................10 Summary Tables of Test Points and Connectors (cont'd) ..........................................................................11 2 http://www.national.com 1.0 Introduction 2.0 Board Assembly The Photodiode Sensor Board (SP1202S03RB), This Photodetector Sensor Board comes as a bare along with the Sensor Signal Path Control Panel board that must be assembled. Refer to the (Sensor Panel) software and SPUSI2 USB example Bill of Materials for a description of Interface Dongle are designed to ease the design of component values. The values for the photodiode circuits using various photodiodes with National’s circuit are calculated using WEBENCH Sensor amplifiers and Analog-to-Digital converters (ADCs). Designer. The values for the LED driver are not Use the WEBENCH® Photodiode Sensor Designer calculated by Sensor Designer. to determine appropriate ICs and passives to achieve your signal path requirements: 3.0 Quick Start http://www.national.com/analog/webench/sensors/p Refer to Figure 1 for locations of test points and hotodiode major components. This Quick Start procedure See Figure 1 for component placement and Figure provides 5V excitation for the sensor. 2 for the example board schematic. The circuit for 1. Place the J1 jumper across pins 2 & 3. This the photodiode sensor consists of a applies a negative 5VDC bias to the transimpedance amplifier (current to voltage photodiode. converter) for operation in the photoconductive mode. Also, the board has circuitry to drive a light 2. Place the J3 jumper across pins 2 & 3. This source (LED) which can be mounted in close sets the ADC reference voltage to 4.096VDC. proximity to the photodiode. The LED current can 3. Place the J4 jumper across pins 2 & 3. This be either continuous or switched with the current sets the –VCC to -5VDC. Do not use this level adjustable using a multi turn potentiometer. setting for an Op Amp that has a VCC of 5VDC or less. The values for the LED driver are not calculated by Sensor Designer. The idea here is to provide a 4. Connect the Differential Pressure Sensor Board generic driver stage, allow the user to select a light to the SPUSI2 board via 14-pin header J2. source and adjust the current accordingly. The light 5. Connect a USB cable between the SPUSI2 source is not included in the kit. It should be chosen board and a PC USB port. GRN LED D1 on the to be commensurate with the photodiode Photodiode Sensor Board and D1 on the wavelength and optical sensitivity. SPUSI2 board should come on if the PC is on. The outputs are a voltage output for the 6. If not already installed, install the Sensor Panel photocurrent (received optical power and a voltage software on the PC. Run the software. output for the LED current (transmitted optical power). 3 http://www.national.com Figure 1. Component and Test Point Locations J3 J1 J4 TP2 TP8 TP9 TP1 VREF Bias -VCC GND VREF CS* Analog Select Select Select TIA Out TP10 GND TP14 DIN TP13 VCC3V J2 SPUSI2 Conn. TP12 DOUT TP11 SCLK TP5 Isense + VR1 J5 S1 TP7 TP6 TP4 TP3 Current Generator LED Generator Isense - GND Current Adjust In On/Off In Meter Analog Out 4 http://www.national.com 4.0 Functional Description Because the photodiode has capacitance, RF and The Photodiode Sensor Board component and test CDIODE form a pole in the noise gain transfer point locations are shown in Figure 1. The board function. This can create stability issues and is schematic is shown in Figure 2. compensated for by CF. WEBENCH Sensor Designer calculates the value of CF for a 45 0 4.1 Operational Modes phase margin to insure stability. This board may be use in one of two modes: the 4.2.2 Light Source Computer Mode using the SPUSI2 USB Interface Provisions for a light source for test purposes are Dongle or the Stand-Alone Mode without the use of on the board. the SPUSI2 USB Interface Dongle and a PC. The user can select an LED with appropriate 4.1.1 The Computer Mode wavelength and output power to compliment the The board is intended for use in the Computer photodiode selection. It may be necessary to Mode, where a SPUSI2 board is used with it and modify component values in the LED driver to the SPUSI2 board is connected to a PC via a USB optimize performance. port. Power to both boards is provided via USB. S1 is provided as an ON/OFF control for the LED 4.1.2 The Stand-Alone Mode drive circuit. It controls the gate voltage of an NCH The Stand-Alone Mode does not use the SPUSI2 MOSFET. In the open position, the mosfet is board to capture data and upload it to a PC. To use conducting and the current source is enabled. the board this way, the user must provide +5V at Also connected to the gate of the mosfet is a pin 14 of header J2 as well as provide ADC clock connector for a signal generator. A switching signal and Chip Select signals to the ADC at pins 3 and 1, can be connected here to observe the transient respectively, of J24. ADC data output is available at response of the transimpedance amplifier. The rise pin 5 of J2. Test Points may also be used to times and switching frequencies are somewhat insert/read these signals. The range of frequencies limited by the current source components and the for the ADC clock is 500KHZ to 1 MHz. The CS rate mosfet switch so the user may want to install can be as low as desired, as but no faster than 17 different components to achieve higher times the ADC clock rate. performance for the current source in this mode. 4.2 Signal Conditioning Circuitry The current source consists of U3, Q1, VR1 and R7. The op amp will make sure the voltage at the The output of the TIA (transimpedance amplifier) is CT of VR1 appears on the inverting pin. This on TP1. This is a voltage that is proportional to voltage then appears across R7 (minimal VON for photocurrent. The values for RF and CF are Q2). ILED = VR1CT/R7. Turning VR1 clockwise calculated by the WEBENCH Sensor Designer. RF increases LED current. The differential amplifier U2 is determined by the full scale input voltage of the measures the current flowing in the LED by ADC and the maximum output photocurrent of the measuring the Voltage drop across R4. This photodiode. CF is determined based on photodiode voltage drop is scaled by the gain
Details
-
File Typepdf
-
Upload Time-
-
Content LanguagesEnglish
-
Upload UserAnonymous/Not logged-in
-
File Pages14 Page
-
File Size-