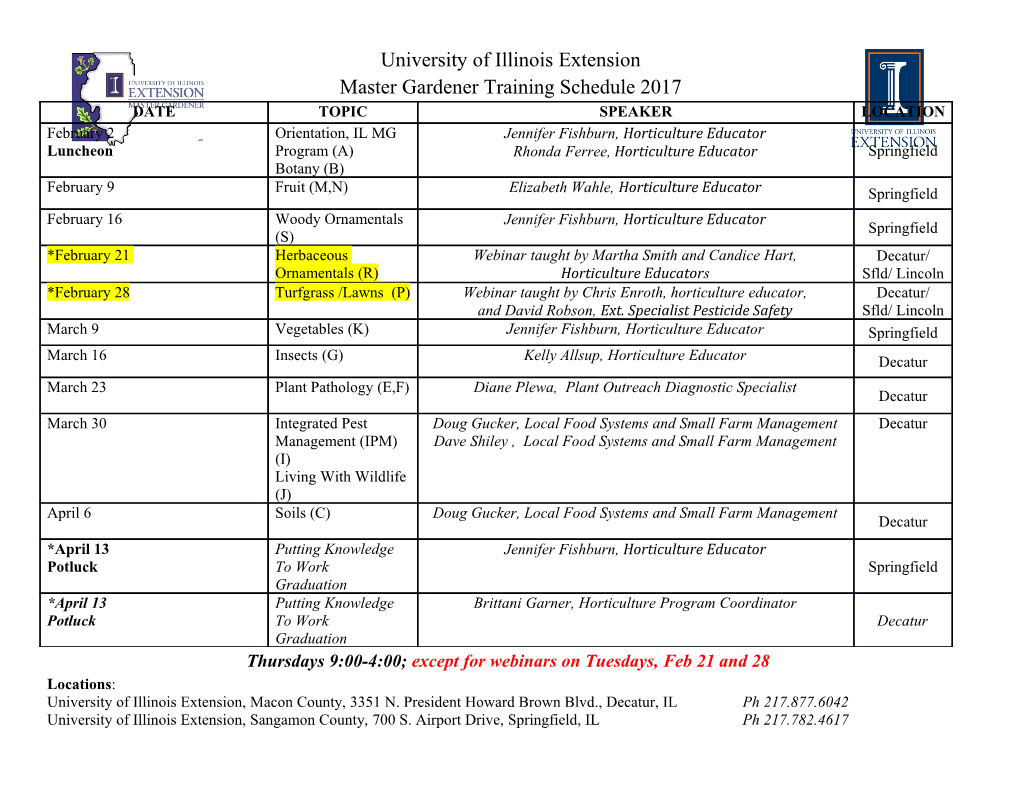
Design of the Suspension System for a FSAE Race Car Sergio Valencia Arboleda 201126788 Faculty advisor: Juan Sebastián Nuñez Gamboa Faculty co-advisor: Andres Gonzalez Mancera Towards the degree of: Bachelor in Mechanical Engineering Universidad de Los Andes Mechanical Engineering Department May 2016 1 Contents Chapter 1. Introduction 1.1 Project Background 1.2 Problem definition Chapter 2. Objectives & Design Methodology 2.1 Objectives 2.2 Design Methodology Chapter 3. Literature Review 3.1 The suspension of an FSAE and its objective 3.2 FSAE suspension elements 3.3 Full vehicle Parameters 3.4 Vehicle Dynamic Load Transfer 3.5 Tire Relative Angles 3.6 Suspension Behaviours 3.7 Steering Behaviours 3.8 Formula SAE Suspension Requirements Chapter 4. Preliminary Design decisions 4.1 Benchmark Information 4.2 Rims & Tires 4.3 Vehicle´s Overall Weight Estimation 4.4 Center of Gravity Estimation 4.5 Type of Suspension 4.6 Vehicle´s Basic Dimensional Parameters 4.7 Overall Performance Targets & Design Recommendations Chapter 5. Modelling the suspension in Autodesk Inventor® 5.1 Chassis Geometry 5.2 Geometric Suspension Design Chapter 6. Suspension Geometry evaluation using MatLab® 6.1 Previous Geometric analysis 6.2 Objective of the code 6.3 Analysis Methodology 6.4 Front Suspension Static Analysis 6.5 Relationship Between the variables and the parameters 6.6 Front Suspension Results 6.7 Rear Suspension Static Analysis 2 6.8 Rear Suspension Results 6.9 Final Considerations Chapter 7. Suspension modelling & evaluation in Adams/Car® 7.1 Introduction to Adams/Car® 7.2 Modelling the suspension in Adams/Car® 7.3 Suspension Actuation Analysis and Design 7.4 Front Suspension DOE 7.5 Rear Suspension DOE 7.6 Full vehicle Analysis 7.7 Final Configuration of the suspension 7.8 Design Evaluation Chapter 8. Conclusions and future work 7.1 Conclusions 7.2 Future work References Appendix A. FSAE Lincoln electric vehicles information Appendix B. Hoosier Tire Information Appendix C. Keiser Rim Information Appendix D. MatLab® Code Appendix E. Front Suspension MatLab® analysis results Appendix F. Rear Suspension MatLab® analysis results Appendix G. Front & Rear suspension: Wheel rate Appendix H. Full Vehicle DOE Results Appendix I. Front Suspension Results: Final Parameters Appendix J. Rear Suspension Results: Final Parameters 3 List of Figures: Figure 1. Chassis Render (taken from: Sarmiento, 2015 pg. 60) Figure 2. Types of Independent suspension configurations Image A. Pull rod Suspension (taken from: Kiszko, 2011 pg. 58) Image B. Push rod Suspension (taken from: Farrington, 2011 pg. 122) Image C. Direct Actuation of the shock absorber (taken from: http://trackthoughts.com/wp- content/uploads/2010/11/M0401751.jpg) Figure 3. ADAMS/Car® fsae_2012 Front Suspension Assembly Figure 4. ADAMS/Car® fsae_2012 Rear Suspension Assembly Figure 5. ISO International Vehicle axis system (taken from: http://white- smoke.wikifoundry.com/page/Heave,+Pitch,+Roll,+Warp+and+Yaw) Figure 6. Roll Center height diagram (Taken from Chang, 2012 pg. 2) Figure 7. Instant Roll Center (Taken from: Jazar, 2014 pg. 527 ). Figure 8. Vehicle Roll Axis (Taken from: http://dreamingin302ci.blogspot.com.co/2013/06/flckle-roll-center.html) Figure 9. Different Toe Angle´s (Taken from: Jazar, 2014 pg. 528) Figure 10. Caster angle geometry (Taken from: http://www.autozone.com/repairguides/Toyota-Celica-Supra-1971- 1985-Repair-Guide/FRONT-SUSPENSION/Front-End-Alignment/_/P-0900c1528007cc57) Figure 11. Camber angle geometry (Taken from: http://www.autozone.com/repairguides/Pontiac-Fiero-1984-1988- Repair-Guide/Front-Suspension/Front-End-Alignment/_/P-0900c152801dace). Figure 12. Kingpin angle & scrub radius geometry (Taken from: http://www.mgf.ultimatemg.com/ ) Figure 13. Jacking Force estimation (Taken from: Smith, 1978 pg. 39) Figure 14. Tire´s slip angle (Taken from: Milliken & Milliken, 1995 pg. 54) Figure 15. Oversteer & Understeer (Farrington, 2011 pg. 33) Figure 16. Vehicle Fundamental dimensions Figure 17. Rollover stability test (Taken from http://www.bbc.co.uk/news/uk-england-northamptonshire-14184535) Figure 18. FSAE Hoosier tire (Taken from: https://www.hoosiertire.com/Fsaeinfo.htm ). Figure 19. Keiser Kosmo Forged (Taken from: http://keizerwheels.com/ ) Figure 20. Center of gravity location of the actual chassis Figure 21. First layout of the major components Figure 22. Second layout of the major components Figure 23. Third layout of the major components Figure 24. Equal Length & Parallel arms configuration (Taken from: Farrington, 2011 pg. 22) Figure 25. Unequal Length & Parallel arms (Taken from: Farrington, 2011 pg. 22) Figure 26. Unequal Length & Non-Parallel arms (Taken from: Farrington, 2011 pg. 22) Figure 27. Chassis design Figure 28. Chassis with the modifications in the rear section Figure 29. First iteration of the suspension geometry attached to the chassis Figure 30. Chassis possible modifications Figure 31. Roll Center Height and KPI angle estimation using the graphical method Figure 32. Coordinate system & Hardpoints assignation (Wolfe, 2010). Figure 33. Relationship between the Variables & Parameters Figure 34. yl vs Roll Center Height (RCH in inches) Figure 35. Results after iterating the Upper A-arm width (Z coordinate of Hardpoints 1 & 2). Figure 36. ADAMS/Car® fsae_2012 full vehicle assembly Figure 37. First design iteration of the FRONT_UNIANDES assembly Figure 38. First design iteration of the REAR_UNIANDES assembly Figure 39. First design iteration of the FSAE_UNIANDES assembly Figure 40. Equivalent Coordinate system (MatLab & ADAMS/Car). Figure 41. Origin of the coordinate system in ADAMS/Car® Figure 42. Öhlins TTX25 MkII (50 mm). (Taken from: http://www.kaztechnologies.com/fsae/shocks/ohlins-fsae- shocks/). Figure 43. Suspension actuation mechanism (Front & Rear assemblies) 4 Figure 44. HYPERCO FSAE springs (Taken from: http://www.kaztechnologies.com/fsae/springs/) Figure 45. Location of each of the 5 input factors (Front Suspension) Figure 46. Simulation conditions during the Front Suspension DOE Figure 47. Opposite Wheel travel simulation Figure 48. Influence of the factors respect the Roll Center vertical displacement (Front suspension) Figure 49. Influence of the factors respect the Roll Center lateral displacement (Front suspension) Figure 50. Influence of the factors respect the Camber gain (Front suspension) Figure 51. Influence of the factors respect the Toe gain(Front suspension) Figure 52. Location of each of the 6 input factors (Rear Suspension) Figure 53. Simulation conditions during the Rear Suspension DOE Figure 54. Influence of the factors respect the Roll Center vertical displacement Figure 55. Influence of the factors respect the Roll Center Lateral displacement Figure 56. Influence of the factors respect the Camber gain Figure 57. Influence of the factors respect the Toe gain Figure 58. Vehicle trajectory while performing a Step-steer simulation Figure 59. Simulation Conditions: Step-steer Figure 60. Influence of the factors respect the Lateral Acceleration Figure 61. Influence of the factors respect the Chassis Roll Figure 62. Influence of the factors respect the Yaw rate Figure 63. Influence of the factors respect the Vehicle Slip Angle Figure 64. FRONT_UNIANDES final configuration Figure 65. REAR_UNIANDES final configuration Figure 66. FSAE_UNIANDES vehicle vs fsae_2012 vehicle Figure 67. Straight line acceleration conditions Figure 68. Vehicle´s pitch angle vs simulation time (FSAE_UNIANDES vs fsae_2012) Figure 69. Vehicle´s pitch angle vs Longitudinal acceleration (FSAE_UNIANDES vs fsae_2012) Figure 70. Front and Rear normal forces (FSAE_UNIANDES) vs simulation time Figure 71. FSAE_UNIANDES longitudinal acceleration vs simulation time Figure 72. Lane change simulation conditions Figure 73. Chassis roll ange vs lateral acceleration (FSAE_UNIANDES vs fsae_2012 Figure 74. Lateral Acceleration vs simulation time (FSAE_UNIANDEs vs fsae_2012) Figure 75. Constant Radius simulation conditions Figure 76. Vehicle´s Side Slip Angle vs simulation time (FSAE_UNIANDES vs fsae_2012) Figure 77. Tire normal forces vs simulation time (FSAE_UNIANDES) Figure 78. Internal combustión engine vs electric engine: Torque vs rpm (taken from: https://simanaitissays.com/2013/07/20/tranny-talk/) Figure 79. Vehicle side-slip angle (taken from: http://www.racelogic.co.uk/_downloads/vbox/Application_Notes/Slip%20Angle%20Explained.pdf) 5 List of Tables: Table 1. FSAE Lincoln Electric vehicles parameters (2015) Table 2. Hoosier tire specifications Table 3. Weight estimation of the vehicle Table 4. Types of Batteries used in the FSAE electric vehicles (Info taken from: http://batteryuniversity.com/learn/article/types_of_lithium_ion). Table 5. Center of Gravity estimation for each configuration Table 6. Vehicle´s Dimensional Parameters Table 7. Recommended values for the suspension parameters* Table 1. Front Suspension Input Variables domain Table 2. Front Suspension Parameters domain Table 10. Front Suspension Results (New domain for each Hardpoint) Table 11. Rear Suspension Input Variable Domain Table 12. Desire RCH domain for the rear suspension Table 13. Rear Suspension Results (New domain for each Hardpoint Table 14. Suspension parameters needed for the analysis Table 15. Final values for the front & rear suspension mechanism Table 16. Input factors Front suspension Assembly Table 17. Input factors Rear suspension Assembly Table 18. Input factors Full vehicle suspension Assembly Table 19. Final Parameters for the FRONT_UNIANDES and REAR_UNIANDES suspension
Details
-
File Typepdf
-
Upload Time-
-
Content LanguagesEnglish
-
Upload UserAnonymous/Not logged-in
-
File Pages101 Page
-
File Size-