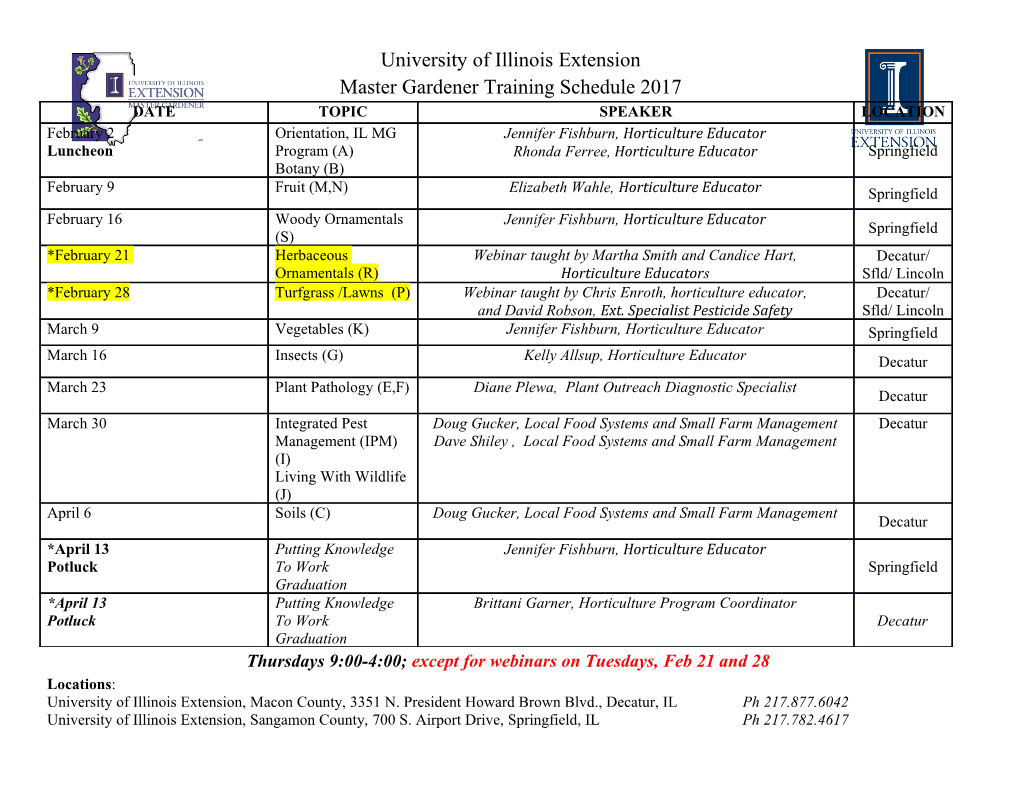
Microstructural Evolution in the HAZ of Inconel 718 and Correlation with the Hot Ductility Test The results of hot ductility tests indicate that heat treatment significantly alters the hot cracking susceptibility of alloy 718 BY R. G. THOMPSON AND S. GENCULU ABSTRACT. The nickel-base alloy 718 imposed on the metal to simulate the that hot cracking resulted from intergran­ was evaluated to study the role of pre­ HAZ conditions of a given welding pro­ ular wetting by the liquated precipitates. weld heat treatment in reducing or elimi­ cess (Ref. 1). The metal is fractured at a Yeniscavich (Ref. 3) reached conclu­ nating heat-affected zone hot cracking. predetermined point in the thermal cycle sions similar to Weiss et al. in studies of Three heat treatments were studied using to test the mechanical response of the EN 82 filler metal used with Inconel 600 the Gleeble hot ductility test. A modified HAZ microstructure. Data from these base metal. A primary difference be­ hot ductility test was also used to follow tests are plotted as ductility versus tem­ tween these two studies involved the the evolution of microstructure during perature. The hot ductility response of liquation mechanism. Yeniscavich pro­ simulated welding thermal cycles. The many metals during the heating portion posed a eutectic-melting intergranular microstructural evolution was correlated of the thermal cycle appears to have phase chemistry which remained molten with the hot ductility data in order to several features in common; these are: during cooling well below the bulk soli­ evaluate the mechanism of hot cracking 1. Rapid loss of ductility with the onset dus temperature. Owczarski, Duvall and in alloy 718. of intergranular fracture. Sullivan (Ref. 6) studied Udimet 700 and The correlation of hot ductility with 2. A nil ductility temperature (NDT) Waspaloy employing the hot ductility microstructure showed that recrystalliza­ characteristic of the material. technique. They, like Weiss et al. and tion, grain growth, and dissolution of 3. A nil strength temperature (NST) Yeniscavich, found incipient intergranular precipitates did not in themselves cause roughly corresponding to the metal's melting to be associated with enhanced any loss of ductility during cooling. Ductil­ bulk solidus temperature. hot crack susceptibility. They concluded ity loss during cooling was not initiated The hot ductility response of a metal that constitutional liquation of MC-type until the constitutional liquation of NbC during cooling from the peak HAZ tem­ carbides resulted in intergranular liquid. particles was observed in the microstruc­ perature is usually considered indicative However, unlike the above mentioned ture. Laves-type phases were found pre­ of its susceptibility to hot cracking (Ref. studies, Owczarski et al. concluded liqua­ cipitated in the solidified grain boundaries 2). If the metal regains its ductility over a tion did not begin until above the NDT on but were not found to correlate with any short temperature range, it is usually heating. The initial loss of ductility on ductility loss parameter. insensitive to HAZ hot cracking. If the heating and intergranular fracture mode were suggested to be intrinsic material Mechanisms are reviewed which help metal's ductility remains close to zero characteristics reminiscent of the equico- to explain how heat treatment controls over a wide temperature range on cool­ hesive temperature and thus dependent the hot crack susceptibility of alloy 718 as ing, it is usually hot-crack sensitive. Such on both material and test variables. measured in the hot ductility test. observations have been reported previ­ ously for various nickel base alloys (Refs. Partial intergranular melting, similar to Introduction 2-4). (Kreischer [Ref. 5] has reported that reported in the hot ductility litera­ another interpretation criteria for certain ture, has been observed and reported The hot ductility test is often used to stainless steels based on the recovery of for a number of alloys. Partial melting in evaluate a metal's susceptibility to heat- tensile strength during cooling rather than the region adjacent to the weld fusion affected zone (HAZ) hot cracking. The ductility.) zone has been described for cupronickel test consists of a thermal cycle, including Hot crack susceptibility varies greatly in (Ref. 7), Inconel 600 (Refs. 8, 9), and both heating and cooling, which is various alloys, and the identification of HY-80 (Refs. 10, 11). The relationship of the mechanisms responsible for HAZ hot this zone to hot crack sensitivity has been crack susceptibility is a primary concern. investigated with respect to a number of minor alloying and tramp elements in Paper presented at the 64th Annual AWS Alloy chemistry and microstructure have Convention held in Philadelphia, Pennsylvania, been an intense area of study relative to Inconel 600 (Refs. 8, 9) and cupronickel during April 24-29, 1983. hot crack susceptibility. Weiss, Crotke (Ref. 12). It was found that elements such and Stickler (Ref. 4) proposed that consti­ as sulfur and phosphorus increased hot R. G THOMPSON, Assistant Professor, and S. tutional liquation of intergranular precipi­ crack susceptibility through their influ­ GENCULU, Graduate Student, are with the Department of Materials Engineering, School tates in Inconel 600 resulted in an inter­ ence on the solid-liquid interfacial energy of Engineering, The University of Alabama, granular failure mode and loss of both (Ref. 8), i.e., wetting angle. Studies by Birmingham, Alabama. ductility and strength. They concluded Savage, Nippes and Mushala (Refs. 13, WELDING RESEARCH SUPPLEMENT 1337-s 14) have also investigated the role of intragranularly and intergranularly adja­ mm) thick stainless steel with an energy copper-rich intergranular liquid in hot cent to niobium-rich MC-type carbides. input of 70,000 joules/in. (2,756,000 J/m) crack susceptibility. These studies point Welding hot cracks in Inconel 718 have (Ref. 2, 26). This thermal cycle was out the universal nature of the relation­ been studied by R. Vincent (Ref. 27) using imposed on 718 filler metal of the com­ ship between intergranular liquid forma­ convergent beam electron diffraction position given in Table 1. This was tested tion and HAZ hot cracking. and energy dispersive x-ray techniques. in the as-received, solution annealed, and It is now well established that the He found that HAZ cracks were intimate­ age hardened conditions as given in susceptibility to HAZ hot cracking is re­ ly associated with NbC carbides and Table 2. All tests were performed in air. lated to the development of an intergran­ Laves phase. The Laves phase was an AB2 The small diameter —0.061 in. (1.5 mm) — ular liquid phase in the HAZ during weld­ hexagonal type with an atomic composi­ filler metal helped to facilitate the rapid ing. The interrelationship between liquid tion of 29% Nb and 65% Ni, Cr, and Fe. quench rates desired for microstructural and hot cracking naturally suggests a The studies on 718 indicate that hot evaluation. review of solidification cracking literature. cracking susceptibility is intimately related Hot ductility curves were generated in Papers by Pumphrey and lennings (1948) to the formation of intergranular liquid the usual way (Ref. 2) using the 0.061 in. (Ref. 15), C. S. Smith (1948) (Ref. 16), W. films in a manner similar to that proposed (1.5 mm) diameter filler metal as the test M. Williams and Smith (1952) (Ref. 17), J. for other alloys. Studies on Inconel 718 specimen with a 1.0 in. (25.4 mm) length A. Williams and Singer (1966) (Ref. 18) also defined the importance of its second of specimen between the grips. Micro- and Borland (1979) (Ref. 19) help summa­ phase microstructure on the develop­ structures were developed to corre­ rize the recent history of research on ment of the intergranular liquid. spond with the hot ductility data points in solidification cracking. Previous studies have examined the the following manner. A specimen was It is readily seen that research on solid­ microstructure-hot ductility relationship thermally cycled in the Gleeble as if a hot ification cracking has centered on the role through postmortem evaluation of speci­ ductility test was being made. However, of intergranular liquid in the cracking mens whose microstructure was charac­ instead of the fracture event occurring at process. The approach pioneered by teristic of the specimen's cooling rate a predetermined temperature, the speci­ Smith (Ref. 16) and most often used to rather than any particular ductility mea­ men was rapidly quenched to preserve describe the distribution of intergranular sure. This has been true for alloy 718 in the microstructure. Quenching was liquid is the dihedral angle. The dihedral both simulated welding conditions using accomplished by stopping the current angle that the intergranular liquid makes the hot ductility test and in prototype flow to the specimen and simultaneously with the bulk solid has been shown to welds. The present paper presents a inundating the specimen with water. The effect of this quench procedure on cool­ correlate with cracking (Ref. 20) and be a study of microstructural evolution and ing rate is compared to other cooling function of temperature (Refs. 18, 21-23), correlates this to hot ductility data. This rates obtained using non-quench proce­ stress (Refs. 23, 24), and trace elements was done for three preweld microstruc­ dures in Fig. 1. (Ref. 21). Note that these variables, with tures from a single 718 heat. Such an the exception of stress, have also been approach helps to explain some observa­ Microstructures developed by the shown to control HAZ hot cracking. It tions made on postmortem microstruc­ imposed cycle were revealed by might be anticipated that the susceptibili­ tures and also ties together information mechanically polishing the samples ty to HAZ hot cracking is dependent on from previous studies on the role of through 0.3 micron (0.0003 mm or the distribution of intergranular liquid.
Details
-
File Typepdf
-
Upload Time-
-
Content LanguagesEnglish
-
Upload UserAnonymous/Not logged-in
-
File Pages9 Page
-
File Size-