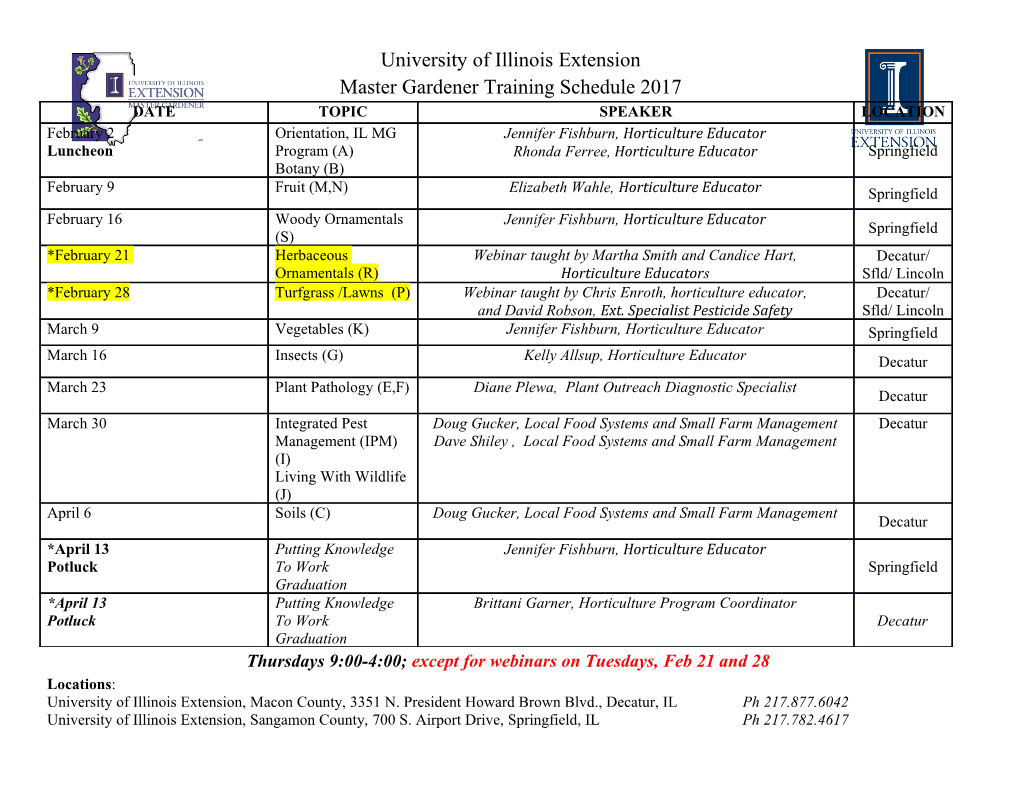
ST 435/535 Statistical Methods for Quality and Productivity Improvement / Statistical Process Control Introduction to Statistical Process Control Statistical Process Control (SPC) uses seven major tools: 1 Histogram or stem-and-leaf plot; 2 Check sheet; 3 Pareto chart; 4 Cause-and-effect diagram; 5 Defect concentration diagram; 6 Scatter diagram; 7 Control chart. Control charts play a central role. 1 / 14 Introduction to Statistical Process Control Introduction ST 435/535 Statistical Methods for Quality and Productivity Improvement / Statistical Process Control Chance and Assignable Causes of Quality Variation Variability All processes, whether production of goods or provision of services, show variability in quality characteristics. Chance causes of variation \Background noise", the cumulative effect of many small unavoidable causes, results from chance causes. A process that shows only chance causes of variation is said to be in statistical control. 2 / 14 Introduction to Statistical Process Control Chance and Assignable Causes of Quality Variation ST 435/535 Statistical Methods for Quality and Productivity Improvement / Statistical Process Control Assignable causes of variation Larger changes with identifiable sources may result in unacceptable performance. They are called assignable causes of variation. A process that shows assignable causes of variation is said to be out of control. Control charts are the basic tool for distinguishing in-control versus out-of-control processes. 3 / 14 Introduction to Statistical Process Control Chance and Assignable Causes of Quality Variation ST 435/535 Statistical Methods for Quality and Productivity Improvement / Statistical Process Control Statistical Basis of the Control Chart Control chart for a hypothetical in-control process: ● ● ● ● ● ● ● ● ● ● ● ● ● ● ● ● The green line is the center line, the average value when in control. The red lines are the upper control limit (UCL) and lower control limit (LCL). 4 / 14 Introduction to Statistical Process Control Statistical Basis of the Control Chart ST 435/535 Statistical Methods for Quality and Productivity Improvement / Statistical Process Control The control limits are chosen so that, when in control, almost all values fall between them. A point that falls outside the control limits triggers some action: Investigation; Possible corrective action. The control chart may show a change in behavior even before a point falls outside the control limits: ● ● ● ● ● ● ● ● ● ● ● ● ● ● ● ● 5 / 14 Introduction to Statistical Process Control Statistical Basis of the Control Chart ST 435/535 Statistical Methods for Quality and Productivity Improvement / Statistical Process Control Control charts and hypothesis tests Deciding whether a process is in control or out of control resembles a hypothesis test. If the null hypothesis were \process is in control", and we tested it with a typical α-level like 5%, we would wrongly reject it 1 time in 20. Control lines are usually chosen to have a far lower probability of interrupting an in-control process. \Three sigma" limits are a common choice. 6 / 14 Introduction to Statistical Process Control Statistical Basis of the Control Chart ST 435/535 Statistical Methods for Quality and Productivity Improvement / Statistical Process Control Example: Flow width in semiconductor fabrication Process mean is 1.5µm and process standard deviation is 0.15µm. Samples of sizep n = 5 are taken once per hour, so the standard error ofx ¯ is (0:15= 5 = 0:0671)µm. In the control chart, the center line is at 1.5µm and the three-sigma control limits are UCL = 1:5 + 3 × 0:0671 = 1:7012 and LCL = 1:5 − 3 × 0:0671 = 1:2988: If flow width is normally distributed, the probability of a point falling outside the control lines when the process is in control is 0.0027. 7 / 14 Introduction to Statistical Process Control Statistical Basis of the Control Chart ST 435/535 Statistical Methods for Quality and Productivity Improvement / Statistical Process Control Control chart design Specification of a control chart: Sample size; Control limits; Frequency of sampling. Together with the process capability (mean and standard deviation), these determine p = P(out-of-control flagjin control): 8 / 14 Introduction to Statistical Process Control Statistical Basis of the Control Chart ST 435/535 Statistical Methods for Quality and Productivity Improvement / Statistical Process Control The average run length (ARL) is the average number of points on the chart before a point falls outside the control limits: 1 ARL = : p Example: Flow width in semiconductor fabrication Since p = 0:0027, the ARL is (1/0.0027 = 370). Since samples are taken once per hour, the average time to signal is 370 hours of operation. If successive sample means are independent, the run length has a geometric distribution with the given mean. 9 / 14 Introduction to Statistical Process Control Statistical Basis of the Control Chart ST 435/535 Statistical Methods for Quality and Productivity Improvement / Statistical Process Control Rational Subgroups Samples should be taken in a way that gives the best chance of detecting an out-of-control process. For example, to detect a drift in the mean, the sample values should be collected close together in time, to reduce within-sample variability. On the other hand, a sample drawn randomly over the sampling interval is more representative of all items produced. 10 / 14 Introduction to Statistical Process Control Statistical Basis of the Control Chart ST 435/535 Statistical Methods for Quality and Productivity Improvement / Statistical Process Control The Rest of the Magnificent Seven Of the other six main tools: Histograms, stem-and-leaf plots, and scatter plots are familiar statistical tools; The check sheet, Pareto chart, cause-and-effect diagram, and defect concentration diagram are useful tools for displaying and analyzing quality problems. 11 / 14 Introduction to Statistical Process Control The Rest of the Magnificent Seven ST 435/535 Statistical Methods for Quality and Productivity Improvement / Statistical Process Control Implementing SPC in a Quality Improvement Program \The objective of an SPC-based variability-reduction program is continuous improvement..." \SPC is not a one-time program to be applied when the business is in trouble and later abandoned." \Quality improvement that is focused on reduction of variability must become part of the culture..." 12 / 14 Introduction to Statistical Process Control SPC in a Quality Improvement Program ST 435/535 Statistical Methods for Quality and Productivity Improvement / Statistical Process Control Applications of SPC and Quality Improvement Tools in Transactional and Service Businesses SPC was developed in manufacturing, and manufacturing continues to be a prominent area of application. Many of the ideas and tools are also useful in managing the quality of services. 13 / 14 Introduction to Statistical Process Control Applications in Service Businesses ST 435/535 Statistical Methods for Quality and Productivity Improvement / Statistical Process Control Some differences: Service businesses may not have a natural measurement system to easily define quality; Observability of the process may be low; Service processes involve people, both as providers and customers of the service, and people are more variable than machines. The Define step in the DMAIC process plays a correspondingly more prominent role. 14 / 14 Introduction to Statistical Process Control Applications in Service Businesses.
Details
-
File Typepdf
-
Upload Time-
-
Content LanguagesEnglish
-
Upload UserAnonymous/Not logged-in
-
File Pages14 Page
-
File Size-