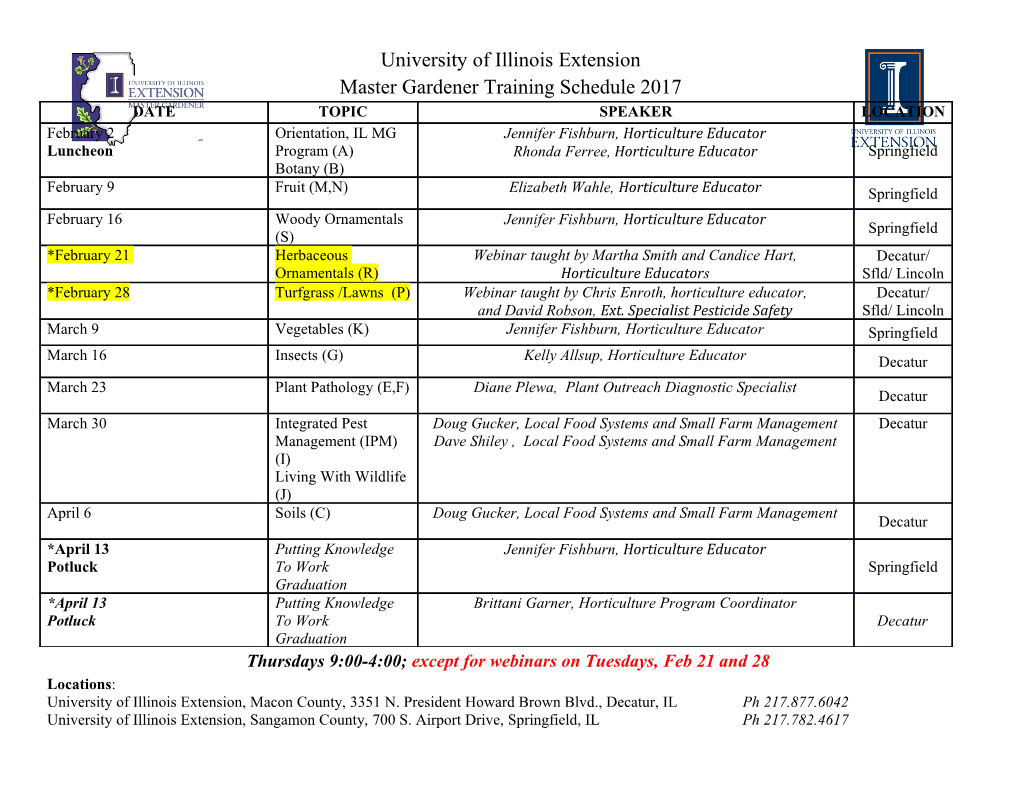
Guest Lecture On Advanced Manufacturing Processes Prepared By Prof. Shinde Vishal Vasant Assistant Professor Dept. of Mechanical Engg. NDMVP’S Karmaveer Baburao Thakare College of Engg. Nashik Contact No- 8928461713 E mail:- [email protected] Website:- www.vishalshindeblog.wordpress.com 03/10/2016 PROF.V.V.SHINDE NDMVP'S KBTCOE NASHIK 1 Grinding Process • Grinding is a material removal and surface generation process used to shape and finish components made of metals and other materials. • The precision and surface finish obtained through grinding can be up to ten times better than with either turning or milling. 03/10/2016 PROF.V.V.SHINDE NDMVP'S KBTCOE NASHIK 2 Grinding • Grinding is a surface finishing operation where very thin layer of material is removed in the form of dust particles. • Thickness of material removed is in range of 0.25 to 0.50 mm. • Tool used is a abrasive wheel. 03/10/2016 PROF.V.V.SHINDE NDMVP'S KBTCOE NASHIK 3 Types Of Grinding Machine • There are many forms of grinding, but the four major industrial grinding • Surface grinding • Cylindrical grinding • Centerless grinding • Internal grinding • Electrochemical grinding • Belt grinder • Bench grinder • Tool and cutter grinder • Gear grinder 03/10/2016 PROF.V.V.SHINDE NDMVP'S KBTCOE NASHIK 4 Major Advantages And Applications Of Grinding Advantages • Dimensional accuracy • Good surface finish • Good form and locational accuracy applicable to both hardened and unhardened material Applications • Surface finishing • Slitting and parting • De-scaling , De-burring • Stock removal (abrasive milling) finishing of flat as well as cylindrical surface • Grinding of tools and cutters and re-sharpening of the same. 03/10/2016 PROF.V.V.SHINDE NDMVP'S KBTCOE NASHIK 5 Grinding Wheel Materials • Most abrasives used in industry are synthetic. Aluminum oxide is used in three quarters of all grinding operations, and is primarily used to grind ferrous metals. • Next is silicon carbide, which is used for grinding softer, non-ferrous metals and high density materials, such as cemented carbide or ceramics. • Superabrasives, namely cubic boron nitride or "CBN" and diamond, are used in about five percent of grinding. Hard ferrous materials are ground with "CBN", while non-ferrous materials and non-metals are best ground with diamond. 03/10/2016 PROF.V.V.SHINDE NDMVP'S KBTCOE NASHIK 6 Standard Shapes Of Grinding Wheels • Straight wheel • Cylinder • Tapered • Recessed one side • Straight cup • Recessed both sides • Flaring cup • Dish • Saucer • Mounted wheels 03/10/2016 PROF.V.V.SHINDE NDMVP'S KBTCOE NASHIK 7 03/10/2016 PROF.V.V.SHINDE NDMVP'S KBTCOE NASHIK 8 Selection Of Grinding Wheel For grinding a job the right grinding wheel is to be selected. The selection of a grinding wheel will depend on the following factors. • Material to be ground • Amount of stock to be removed • Finish required • Area of contact • Wheel speed • Work speed • Personal factor • Method of cooling 03/10/2016 PROF.V.V.SHINDE NDMVP'S KBTCOE NASHIK 9 Standard Marking System for Aluminum-Oxide and Silicon-Carbide Bonded Abrasives 03/10/2016 PROF.V.V.SHINDE NDMVP'S KBTCOE NASHIK 10 Standard Marking System for Cubic-Boron- Nitride and Diamond Bonded Abrasives 03/10/2016 PROF.V.V.SHINDE NDMVP'S KBTCOE NASHIK 11 Grinding Fluid The Grinding fluid serves three main functions : • Reduces Wheel wear. • Cools the w/p. • Flushes away the chips. 03/10/2016 PROF.V.V.SHINDE NDMVP'S KBTCOE NASHIK 12 Grinding Process Grinding is an abrasive machining process that uses a grinding wheel as the cutting tool. 03/10/2016 PROF.V.V.SHINDE NDMVP'S KBTCOE NASHIK 13 Surface Grinding Surface grinding uses a rotating abrasive wheel to remove material, creating a flat surface. 03/10/2016 PROF.V.V.SHINDE NDMVP'S KBTCOE NASHIK 14 Surface Grinding • It is machine basically used to grind flat surface. • Job is mounted to a table which moves longitudinally as well as in transverse direction. • Manual feed or power feed. • Work piece is clamped to the table by operating magnetic chuck. • Required grade of grinding tool is fixed to spindle. • Grinding operation is carried out be operating both table traverse wheel and vertical feed hand wheel. 03/10/2016 PROF.V.V.SHINDE NDMVP'S KBTCOE NASHIK 15 03/10/2016 PROF.V.V.SHINDE NDMVP'S KBTCOE NASHIK 16 Types Of Surface Grinding Machine Basically there are four different types of surface grinding machines characterised by the movement of their tables and the orientation of grinding wheel spindles as follows: • Horizontal spindle and reciprocating table • Vertical spindle and reciprocating table • Horizontal spindle and rotary table • Vertical spindle and rotary table 03/10/2016 PROF.V.V.SHINDE NDMVP'S KBTCOE NASHIK 17 Surface grinding • In surface grinding, the spindle position is either horizontal or vertical, and the relative motion of the work piece is achieved either by reciprocating the work piece past the wheel or by rotating it. The possible combinations of spindle orientations and work piece motions yield four types of surface grinding processes illustrated in the figure 03/10/2016 PROF.V.V.SHINDE NDMVP'S KBTCOE NASHIK 18 Horizontal And Vertical Grinding Machines • This machine may be similar to a milling machine used mainly to grind flat surface. However, some types of surface grinders are also capable of producing contour surface with formed grinding wheel. A: rotation of grinding wheel B: reciprocation of worktable C: transverse feed D: down feed 03/10/2016 PROF.V.V.SHINDE NDMVP'S KBTCOE NASHIK 19 Cylindrical Grinding • It is a process of grinding curved surfaces. • Surface may be straight or tapered. • Work piece is mounted on two centers, one is tailstock centre and the other is headstock centre. • Head stock center may or may not revolve. 03/10/2016 PROF.V.V.SHINDE NDMVP'S KBTCOE NASHIK 20 Cylindrical Grinding 03/10/2016 PROF.V.V.SHINDE NDMVP'S KBTCOE NASHIK 21 Cylindrical Grinding • In this operation, the external or internal cylindrical surface of a work piece are ground. In external cylindrical grinding (also center-type grinding) the work piece rotates and reciprocates along its axis, although for large and long work parts the grinding wheel reciprocates. • In internal cylindrical grinding, a small wheel grinds the inside diameter of the part. The work piece is held in a rotating chuck in the headstock and the wheel rotates at very high rotational speed. In this operation, the work piece rotates and the grinding wheel reciprocates. 03/10/2016 PROF.V.V.SHINDE NDMVP'S KBTCOE NASHIK 22 External Cylindrical Grinding 03/10/2016 PROF.V.V.SHINDE NDMVP'S KBTCOE NASHIK 23 Internal Cylindrical Grinding Internal grinding is used to grind the internal diameter of the workpiece. Tapered holes can be ground with the use of internal grinders that can swivel on the horizontal. 03/10/2016 PROF.V.V.SHINDE NDMVP'S KBTCOE NASHIK 24 03/10/2016 PROF.V.V.SHINDE NDMVP'S KBTCOE NASHIK 25 Plunge Cut Grinding Infeed (Plunge) Grinding is used to grind work pieces which have projections or shoulders, multiple diameters or other irregular shapes which preclude the use of through feed grinding. For example :- Grinding of crank shaft. 03/10/2016 PROF.V.V.SHINDE NDMVP'S KBTCOE NASHIK 26 Centerless Grinding Machine • It is used to grind curved surface work piece which are long and slender. • Work piece rests on a work-rest blade and is backed by a second wheel called as regulating wheel. • Grinding wheel pushes the work piece down the work-rest blade against the regulating wheel. • Center less grinding differs from centered grinding operations in that no spindle or fixture is used to locate and secure the work piece. • The work piece is secured between two rotary grinding wheels, and the speed of their rotation relative to each other determines the rate at which material is removed from the work piece. 03/10/2016 PROF.V.V.SHINDE NDMVP'S KBTCOE NASHIK 27 Center less Grinding 03/10/2016 PROF.V.V.SHINDE NDMVP'S KBTCOE NASHIK 28 Thread Grinding Figure - Thread grinding by (a) traverse and (b) plunge grinding. 03/10/2016 PROF.V.V.SHINDE NDMVP'S KBTCOE NASHIK 29 Electrochemical Grinding • The wheels and work piece are electrically conductive. • Wheels used last for many grindings - typically 90% of the metal is removed by electrolysis and 10% from the abrasive grinding wheel. • Capable of producing smooth edges without the burrs caused by mechanical grinding. • Does not produce appreciable heat that would distort work piece. • Decomposes the work piece and deposits them into the electrolyte solution. The most common electrolytes are sodium chloride and sodium nitrate. 03/10/2016 PROF.V.V.SHINDE NDMVP'S KBTCOE NASHIK 30 Applications • Grinding turbine blades • Grinding honeycomb metals for aerospace application • Sharpening hypodermic needles • Machining carbide cutting-tool inserts • ECG is used to remove surface defects from parts where excessive material removal and residual stresses are undesired, such as re-profiling locomotive gears 03/10/2016 PROF.V.V.SHINDE NDMVP'S KBTCOE NASHIK 31 Electrochemical Grinding 03/10/2016 PROF.V.V.SHINDE NDMVP'S KBTCOE NASHIK 32 Specification Of Grinding Wheel i. Abrasives ii. Bond iii. Grit/grain size iv. Grade v. Structure of wheels 03/10/2016 PROF.V.V.SHINDE NDMVP'S KBTCOE NASHIK 33 Specification of Grinding wheel • Specification of a grinding wheel ordinarily means compositional specification. Conventional abrasive grinding wheels are specified encompassing the following parameters. – The type of grit material – The grit size – The bond strength of the wheel, commonly known as wheel hardness – The structure of the wheel denoting the porosity i.e. the amount of inter grit spacing – The type of bond material – other than these parameters, the wheel manufacturer may add their own identification code prefixing or suffixing (or both) the standard code.
Details
-
File Typepdf
-
Upload Time-
-
Content LanguagesEnglish
-
Upload UserAnonymous/Not logged-in
-
File Pages65 Page
-
File Size-