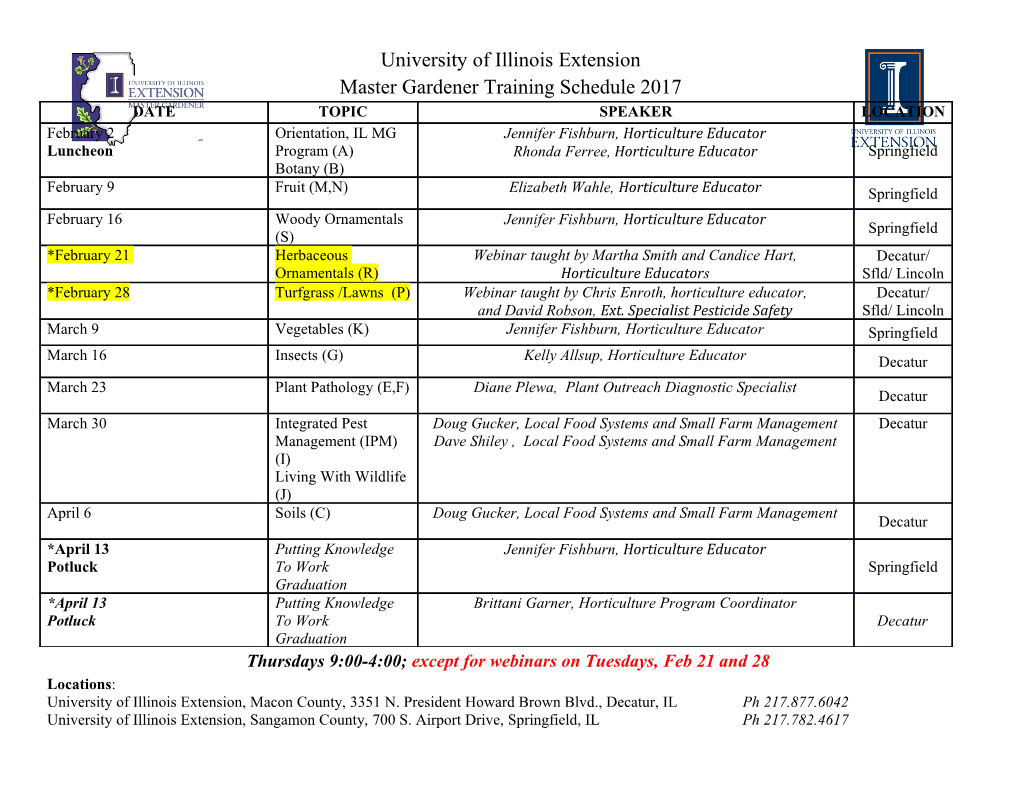
3,595,900 United States Patent Office Patented July 27, 1971 1. 2 BRIEF SUMMARY OF THE INVENTION 3.595,900 Briefly, in one aspect of this invention, a novel class CYANATOPHENYL-TEESTEDTHERS POLYARYLENE of cyanatophenyl-terminated polyarylene ethers are pro Basil L. Loudas, St. Paul, and Herward A. Vogel, Oak vided, the members of which have at least 3 aromatic dale, Minn, assignors to Minnesota Mining and Manu- nuclei (including those in the cyanatophenyl-terminal facturing Company, St. Paul, Minn. groups) linearly linked together by ethereal oxygen atoms. No Drawing. Filed July 1, 1968, Ser. No. 741,303 These dicyanates, in another aspect of this invention, are U.S. C. 2ts C07c 135/00, C07d 55/08 8 Claims prepared by reacting respective hydroxy-terminated poly Vo Vi arylene ethers with cyanogen halide in the presence of a 0 base, such as triethylamine. In another aspect of this in vention, said cyanates are thermally polymerized to form ABSTRACT OF THE DISCLOSURE polyarylene ether cyanurate polymers with the cyanurate Hydroxy-terminated polyarylene ethers are reacted with rings thereof being linked by at least 3 aromatic nuclei cyanogen halides to produce cyanatophenyl-terminated which in turn are linked by ethereal oxygen atoms, said polyarylene ethers which can be thermally polymerized l3 polymers being capable of being readily fabricated in the to produce polyarylene ether cyanurates having outstand- form of shaped articles having improved flexibility and ing strength, toughness, and flexibility and useful in ad- outstanding strength and toughness. hesives, coatings, and binders. DETALED DESCRIPTION OF THE 20 INVENTION FIELD OF THE INVENTION The cyanatophenyl-terminated polyarylene ethers of This invention relates to cyanato-terminatedo polyaryl- formulathis invention, briefly described above, preferably have the ene ethers, such as polyphenylene ethers, and to a method NCO-R-OCN (I) for their preparation. In another aspect it relates to poly- 25 o o arylene ether cyanurate polymers of said cyanates and to where R is a divalent radical having at least 3, and as a method for the preparation of said polymers. In a fur- many as 15 or more, aromatic nuclei linearly linked to: ther aspect it relates to shaped articles made from said gether with ethereal oxygenatoms, such as those nuclei cyanurate polymers. selected from the group consisting of phenylene, diphenyl 30 ene, and radicals of diphenyl ether, 2,2-diphenylpropane, PRIOR ART benzophenone, and diphenylsulfone. These aromatic nu Prior art disclosing cyanato-terminated polyarylene clei have structures shown as follows: ethers and cyanurate polymers thereof is German Pats. TABLE I 1,190,184 and 1,195,764. The cyanates disclosed there have only two phenylene nuclei linked by a single ethereal 35 --- ----- oxygen atom, and the resulting cyanurates thereof consist -KX- -{O-O- of a plurality of cyanurate rings linked by a diphenylene ether linkage. Though these cyanurate polymers have CH some desirable properties, their strength and toughness, ins as well as flexibility, are somewhat limited, thus restricting 40 –{ X-0-{X- -{ X-0-{ X these polymers to applications where such properties are CEI not required. Further, their thermal stability is not as high O astively desired. high Thesevolatility prior at art cure cyanates temperatures generally (because have rela- of Orr-{ X- & -{ X- N- T -{ X their relatively low molecular weight) and therefore are 45 O relatively toxic and inconvenient to handle. Also, they Representative cyanatophenyl-terminated polyarylene tend to exhibit runaway reaction during cure since the cy- ethers coming within the scope of general Formula I, anate groups are present as a relatively large portion of and preferred members of same, include those shown in the overall cyanate molecule. Table II. TABLE E Melting Dicyanate point, C. NC o–{ X-0-{ X-0-{ X-0-{ X-0 CN 110-15 ro- -> or CN 98-00 NCO-K X- (C) { } OCN 100 3,595,900 TABLE II-Continued Melting Dicyanate point, C. 100 139-140 rav120 The dicyanates of this invention can be prepared by cyanates to effect their thermal polymerization. Homo reacting the dihydroxy polyarylene ether precursors with polymers of the cyanates as well as copolymers of two cyanogen halide in the presence of a base, such as tri or more of Said cyanates can be prepared in this fashion. ethylamine. U.S. Pat. 3,219,670 is representative of art The thermal polymerization of the cyanates, in ac which discloses such hydroxy precursors. Cyanation of 25 cordance with this invention, involves trimerization of these hydroxy precursors, according to this invention, is terminal cyanato groups to form a cyanurate that has a generally carried out by reacting the hydroxy precursors three-dimensional network structure with polyarylene with a stoichiometric amount of cyanogen halide. Because ether linkages between cyanurate rings, the polymeriza of the exothermic nature of the reaction and the desire tion being illustrated as follows: to prevent side reactions, and because of the volatility 30 of the cyanogen halide, low temperatures below the boil N. ing points of the reactants are maintained during cyana nNCO-R-O CN --> -g o-it-or ro-it-og tion. Generally, low temperatures in the range of -40 to A -N N N N 40 C., preferably -20 to 0° C. will be used and the N/ reaction carried out in an inert liquid organic solvent. Ó-R-0 g Solvents useful for this purpose representatively include acetone, ether, tetrahydrofuran, aromatic hydrocarbons N- n/3 Such as benzene, toluene, and Xylene, and halogenated where n is a multiple of 3 and can be as large as the aliphatic or aromatic hydrocarbons. The cyanation re number of molecules of dicyanate employed, and R is action is carried out in the presence of a base such as 40 as defined in Formula II above. tertiary amines like triethylamine or an alkyl metal hy Generally, the polymerization or curing of cyanates, droxide such as sodium hydroxide, the amount of base in accordance with this invention, will be carried out by used being sufficient to neutralize the hydrogen halide first melting the cyanate monomeric material to obtain produced in the reaction (see German Pat. 1,190,184). It a homogeneous melt and then raising the temperature in is preferred to adjust the addition rate of the base during a range of 50 to 200° C., preferably 100 to 150° C. the cyanation process such that always an excess of Alternatively, this polymerization can be carried out at cyanogen halide over the base is present. lower temperatures, preferably 25 to 100° C., with the Cyanogen halides which can be used include cyanogen aid of activators, initiators or catalysts. These polym chloride (the preferred cyanating agent) and cyanogen erization promoting agents representatively include Lewis bromide, these cyanating agents being well-known com acids, such as aluminum chloride, boron trifluoride, ferric pounds which are commercially available or which can be chloride, titanium chloride, and zinc chloride; protonic prepared by well-known methods. Stoichiometrically, one acids, such as hydrochloric and other mineral acids; salts mole of cyanogen halide is reacted with one equivalent of of Weak acids, such as sodium acetate, sodium cyanide, a hydroxyl group in the hydroxy polyarylene ether re Sodium cyanate, potassium thiocyanate, sodium bicar actant; however, we prefer to use an amount in excess 55 bonate, sodium boronate, and phenylmercuric acetate; and of stoichiometric e.g., cyanogen halide up to 10% excess. bases, such as sodium methoxide, sodium hydroxide, pyri After cyanation is completed, the cyanate product can dine, triethylamine, and the like. Preferred catalysts are be recovered from the reaction mixture by any suitable non-ionic coordination compounds, such as cobalt, iron, recovery procedure, such as precipitation, extraction, dis zinc, and copper acetyl acetonates. The amount of catalyst tillation, crystallization, etc. Preferably, the product is re 60 used can vary, and generally will be 0.05 to 5 mole per covered by mixing the reaction mixture with a water-im cent, preferably 0.05 to 0.5 mole percent. miscible liquid organic solvent in which the cyanate is The polymerization of the cyanates can also be carried Soluble, such as methylene chloride, chloroform or ben out by polymerizing them in solution or in suspension, Zene. The resulting solvent mixture is then poured into using as a solvent or suspension medium the common ice Water. The non-aqueous phase containing the cyanate organic solvents such as hydrocarbons, ketones, halo is separated from the aqueous phase containing the neu genated hydrocarbons, nitrated hydrocarbons, dimethyl tralized halide, for example, by decanting, and can be Sulfoxide, dimethylformamide or ether. The solvent can dried, for example, over anhydrous magnesium sulfate, be removed by distillation or simple evaporation during and filtered. The solvent can then be removed from the course of or at the end of the polymerization. cyanate by stripping, for example, under vacuum at room 70 The cyanatophenyl-terminated polyarylene ethers of this temperature. invention are crystalline or amorphous solids which melt We have found that above-described cyanates are par to flowable liquids at convenient working temperatures. ticularly useful as monomers, intermediates, or prepoly They are soluble in a variety of organic solvents such as mers for the prepartion of cyanurate polymers. Polym methylene chloride, chloroform, benzene, toluene, chlo erization of the cyanates is accomplished by heating the robenzene, acetone, methyl ethyl ketone, ethylbenzoate, 3,595,900 5 6 ethylcellulose, dimethylformamide, etc. They provide When the cyanates of general Formulas IV and V are excellent bases for solvent-diluted coatings such as brush, copolymerized with the cyanato-terminated polyarylene spray, and dip coatings, particularly in the case of the ethers of this invention, the resultant copolymers will higher molecular weight prepolymer type of dicyanates. have improved chemical resistance and thermal stability, The cyanatophenyl-terminated polyarylene ethers can such properties being imparted by the fluorocarbon be used as one-component cured-in-place resins which monomeric units incorporated into the polymers.
Details
-
File Typepdf
-
Upload Time-
-
Content LanguagesEnglish
-
Upload UserAnonymous/Not logged-in
-
File Pages7 Page
-
File Size-