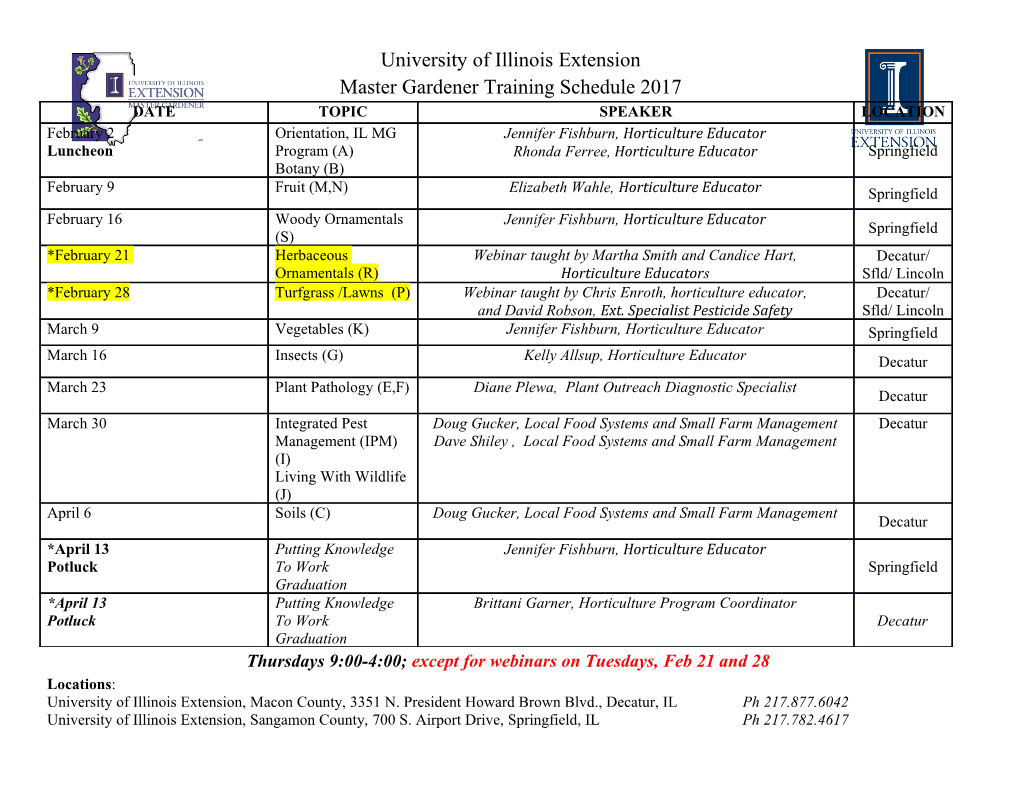
Experiment: Metallography Specimen Preparation and Examination Objectives 1. To learn and to gain experience in the preparation of metallographic specimens. 2. To examine and analyze the microstructures of metals and metallic alloys. Abstract Proper preparation of metallographic specimens to determine microstructure and content requires that a rigid step-by-step process be followed. In sequence, the steps include sectioning, mounting, course grinding, fine grinding, polishing, etching and microscopic examination. Specimens must be kept clean and preparation procedure carefully followed in order to reveal accurate microstructures. Each student will prepare and examine a brass, steel or aluminium sample for metallographic examination. Additionally, a brass, steel or aluminiumsample with different composition, a eutectoid steel sample and a eutectoid Pb-Sn sample will be examined under the metallographic microscope. Photographs will be taken of the samples and the ASTM grain size number determined for each of the specimens if applicable. Background Metallography consists of the study of the constitution and structure of metals and alloys. Much can be learned through specimen examination with the naked eye, but more refined techniques require magnification and preparation of the material's surface. Optical microscopy is sufficient for general purpose examination; advanced examination and research laboratories often contain electron microscopes (SEM and TEM), x-ray and electron diffractometers and possibly other scanning devices. Incorrect techniques in preparing a sample may result in altering the true microstructure and will most likely lead to erroneous conclusions. It necessarily follows that the microstructure should not be altered. Hot or cold working can occur during the specimen preparation process if the metallurgist is not careful. Expertise at the methods employed to produce high-quality metallographic samples requires training and practice. The basic techniques can be learned through patient persistence in a matter of hours. This module takes the student through the metallographic sample preparation process step-by-step with demonstrations and explanations of sectioning, mounting, course & fine grinding, polishing, etching and microscopic examination. Sectioning Operations such as shearing produce severe cold work, which can alter the microstructure of a sample. Abrasive cutting (sectioning) offers the best solution to eliminate these undesirable features; the resultant surface is smooth, and the sectioning task is quickly accomplished. Low-speed cut-off wheels are utilized in cases where the heat created by standard abrasive cutters must be avoided. Ample coolant and proper speed control are essential in all sectioning operations. Abrasive Cut-Off Wheels consist of abrasive grains (such as Aluminum Oxide or Silicon Carbide), bonded together with rubber or other materials in the form of a thin wheel. Rubber bonded wheels are most extensively used for wet operation and resin bonds for dry cutting. When sectioning a piece of metal, the abrasive grains on the cutoff wheel become dull, therefore, the bond must be destroyed at the correct rate so that new grains are always at the edge and are still held firmly by the bonding material. The rate at which the bond breaks down is affected by several different factors, including: 1) The hardness of the bond. 2) The hardness and workability of the metal sample. 3) The size and speed of the wheel. 4) The power of the driving motor. 5) The type and amount of coolant and its method of application. 6) The amount of pressure by which the wheel is applied to the sample. 7) The amount of vibration in the machine. Cutoff wheels are indexed from hard to soft and are referred to by "grade". As a rule of thumb, a hard bonded wheel should be selected when sectioning soft stock, and a soft wheel for sectioning harder material. A reasonable amount of wheel pressure must be applied so the abrasive grains will "bite" and remove the metal 1 ME 3701, Materials of Engineering, LSU in fine chips. An experienced operator can tell whether the wheel is cutting or merely "dragging" by the feel of the control arm and monitoring of the power consumption of the cutting equipment. Proper cutting procedures must be followed; abrasive cut-off wheels will crack and become flying projectiles when used improperly. Lab Procedure - Sectioning 1. Place the sample on the slotted Table so that it is at the center of the swing of the head. 2. Place the Locking Lever in the forward position to allow the Control Rod to be moved to the furthest position. Move the Rear Vise section to contact the rear face of the sample. Move the Front Section to a position near the front face of the sample. 3. Tighten the Nuts that secure the Vise sections to the Table. 4. Push the Control Rod in to make firm contact with the sample and pull back the Locking Level to secure the sample. 5. Turn on the coolant; it should flow readily to both cool and clean the cutting area. 6. Apply steady moderate pressure until the specimen is sectioned; avoid jerking motions that may cause the blade to splinter. Mounting Small samples are generally mounted in plastic for convenience in handling and to protect the edges of the specimen being prepared. Compression-type molding is commonly applied to encase specimens in 1 to 1.5 inch diameter plugs of a hard polymer. Compression molding materials are classified as either thermosetting or thermoplastic: 1) Bakelite is a low cost, relatively hard thermosetting polymer that is commonly utilized. 2) Expensive Transoptic Thermoplastics are utilized when transparency is required. Transoptic materials remain molten at maximum temperature and become transparent with an increase in pressure and a decrease in temperature. By definition, thermosetting materials require heat and pressure during the molding cycle. During mounting, the pressure and molding temperature are generally held constant thus time is the only variable. The metal sample is placed in the mounting cylinder which is then encased in a pre-measured amount of powdered polymers. The mounting cylinder is then sealed, pressurized and heated to complete the polymerization process necessary to solidly encase the metal sample. Although inferior in quality to compression-type molding, cold molding (room temperature) is often used with epoxy to mount samples by simply mixing the epoxy and pouring it over a sample that is positioned face- down in a cold-mounting ring. When the epoxy cures the specimen can be prepared. Caution must be exercised when cold mounting due to relatively poor adhesion between the specimen edges and the epoxy plug; gaps often form which can degrade the quality of the specimen. Lab Procedure Mounting Procedure (Hot-Mounting Equipment Currently Unavailable @ LSU!) Supplies for Cold-Mounting: - KoldMound Kit (Vernon-Benshoff Co.): Mix 2 parts powder with 1 part liquid - Plastic Mounting Ring with Removable Bottom - 8 Ounce Paper Cup with Stirrer - Weight Scale - Liquid Soap 1. Apply liquid soap to the inner walls and base of the mounting ring. 2. Place the specimen in the center/bottom of the plastic mounting ring base with the examination surface face- down. 3. Attach the mounting ring cylinder to the base by simple pressing firmly in place. 2 ME 3701, Materials of Engineering, LSU 4. Mix the appropriate amount of KoldMount (2/1 Powder/Liquid - 15 grams of Powder/7.5 grams of Liquid per Sample) in a paper cup. 5. Simply pour the epoxy mixture into the mounting ring; sample should be approximately 0.75" thick. 6. After one hour, remove the sample from the mounting ring and proceed with course grinding. Coarse Grinding In view of the perfection required in an ideally prepared metallographic sample, it is essential that each preparation stage be carefully performed. The specimen must: 1. Be free from scratches, stains and others imperfections which tend to mark the surface. 2. Retain non-metallic inclusions. 3. Reveal no evidence of chipping due to brittle intermetallic compounds and phases. 4. Be free from all traces of disturbed metal. The purpose of the coarse grinding stage is to generate the initial flat surface necessary for the subsequent grinding and polishing steps. As a result of sectioning and grinding, the material may get cold worked to a considerable depth with a resultant transition zone of deformed material between the surface and the undistorted metal. Course grinding can be accomplished either wet or dry using 80 to 180 grit electrically powered disks or belts, but care must be taken to avoid significant heating of the sample. The final objective is to obtain a flat surface free from all previous tool marks and cold working due to specimen cutting. An important factor throughout the Coarse Grinding and Fine Grinding Stages is that the scratches be uniform in size and parallel to each other in any one grinding stage. Proper grinding involves rotation of the sample by 90o between stages while the grinding angle must be held constant during the grinding at any one stage. The sample MUST be washed thoroughly before proceeding from one grinding stage to the next ! ! ! Failure to follow this basic rule will result in transferring abrasive particles between stages and will cause time- consuming, frustrating problems in removing unwanted scratches. Lab Procedure-Coarse Grinding: *Note: Safety Glasses must be worn when operating the Course Grinding Equipment ! ! ! 1. Label the specimen with your name so that it can be easily identified. 2. Turn the Motor On, then the water, adjust the flow to obtain a good film of water. Too much water will cause a spray when it contacts the sample. 3. Beginning with the 120 grit belt and using both hands to hold the specimen, carefully place the sample face onto the exposed area of the belt being careful not to contact the rotating surface with a sharp edge of the specimen or your hand.
Details
-
File Typepdf
-
Upload Time-
-
Content LanguagesEnglish
-
Upload UserAnonymous/Not logged-in
-
File Pages9 Page
-
File Size-