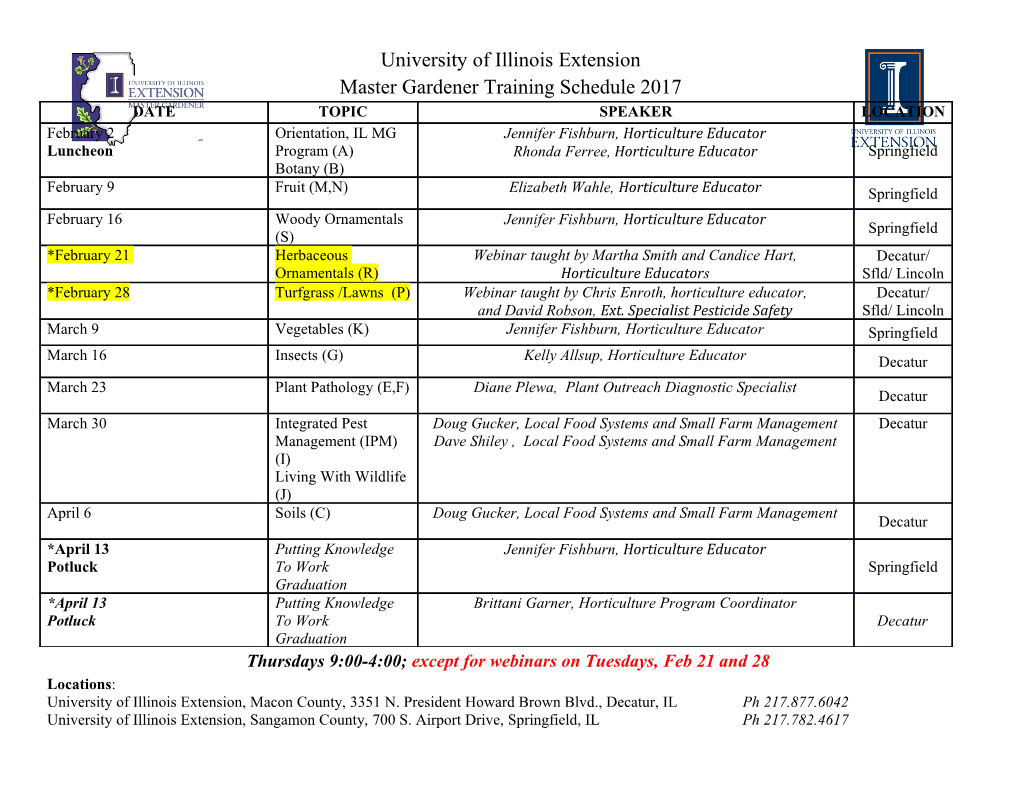
Split-hopper barges Workability of a split-hopper barge in irregular seas S.T.M Mensch Technische Universiteit Delft Split-hopper barges Workability of a split-hopper barge in irregular seas by S.T.M Mensch to obtain the degree of Master of Science at the Delft University of Technology, to be defended publicly on the 16th of October 2017 Student number: 4150503 Project duration: November 14, 2016 – Oktober 16, 2017 Chairman: Prof. Dr. Ir. A. Metrikine, TU Delft Thesis committee: Ir. J. S. Hoving, TU Delft Dr. Ir. K. N. van Dalen, TU Delft Ing. H. Duba, Royal Boskalis Westmister An electronic version of this thesis is available at http://repository.tudelft.nl/. Abstract A split hopper barge is a dredging vessel that can split over its longitudinal axis to discharge its cargo. To allow for such an operation, the barge consists of two half-hulls that are connected by hinges at the top and hydraulic cylinders at the bottom. Any forces that act at the interface between the half-hulls have to be trans- ferred by the hinges and cylinders as a result. The aim of this thesis is to develop a method to determine the workability limits of split hopper barges in irregular seas. For this workability of the barge, the design limits of the hinges and hydraulic cylinders are assumed to be governing. A quasi-static model is formulated to determine the effects of roll, different types of cargo, opening the barge and discharging the cargo on the forces in the hinges and cylinders. The results of the quasi-static model are a set of governing load cases for the split hopper barge. From the quasi-static model, it is found that the forces of interest are the largest for a closed split hopper barge and that either a solid or a liquid cargo will yield the governing load case. To account for the dynamics in irregular sea conditions, a calculation method is proposed based on Ansys AQWA. Since AQWA is not able to account for liquid cargo motions, its effects are incorporated separately. Using WAMIT simulations, the influences of the liquid cargo to the added mass and stiffness of the barge are determined. Based on the WAMIT results the AQWA model is adjusted. Superimposing the results from the quasi-static and dynamic models, the maximum forces in the hinges and hydraulic cylinders are obtained for the governing load cases. By comparing the obtained maximum forces to the design forces, a conclusion on the workability limits of the split hopper barge is drawn. For the barge carrying a solid cargo only one resonance frequency is found, while, due to the liquid cargo motions, the barge with a liquid cargo has two resonance frequencies. As a result, a larger number of com- binations of wave directions and periods yield considerable forces. For a 3-hour-extreme with a significant wave height of 3 meters, the governing hydraulic cylinder forces are found for a barge carrying a liquid cargo. The maximum resulting hinge forces however, are found for a barge carrying a solid cargo. Because the limits of the hinges are exceeded before the limits of the hydraulic cylinders, it is concluded that the workability lim- its of the split hopper barge in irregular waves are most limited, and therefore governing, for a barge carrying a solid cargo. iii Preface S.T.M Mensch Bergambacht, October 2017 This report presents the study that I have done as a part of my thesis for the finalization of my master study in Offshore Engineering at the Delft University of Technology. The research has been conducted at the R&D department of Royal Boskalis Westminster and covers the topic of the workability of split hopper barges in irregular seas. It is a topic that has become very dear to me and has challenged me repeatedly over the past months. I would like to thank my graduation committee Prof. Dr. Ir. A. Metrikine, Ir. J.S. Hoving and Ing. H. Duba for their guidance, effort and confidence that they putt into me and my project. In particular I feel obliged to thank Hans for his full and daily support over the duration of the project. It is really appreciated that he was willing to putt this amount of time of effort in this project next to his daily activities. Next to Hans, I would like to thank the other engineers of the R&D department as well, in special Oscar Sainz Avila and Gert-Jan Grundlehner for their ideas and support in the realization of the research goals. Next to the supervisors and colleagues I would like to thank my fellow (graduate) students at Boskalis for the pleasant cooperation and working environment. Off course my graduation would not have been successful without the support of my family, friends and other relatives. Thank you all! v Summary Introduction Split hopper barges (SHB) are dredging vessels that are used to transport and discharge dredged materials. A typical split-hopper barge is only used for transportation of dredged cargo, the dredging itself is done using other types of dredging equipment. Therefore, split hopper barges will always work together with other types of dredging vessels in a project. The SHB is build up from two half-hulls that are connected by hinges and hydraulic cylinders. Any forces that act at the interface between the half-hulls have to be transferred by the hinges and cylinders as a result. In this research the limits of the hinges and hydraulic cylinders are of con- cern. The aim of this thesis is to find a calculation method to determine the technical workability limits of split hopper barges in irregular seas. The assumption is made that these limits follow from the design limits of the hinges and hydraulic cylinders. In this thesis first the design/classification regulations are used to get familiar with the barge and its design. Using the obtained knowledge, a simple model is built to determine which load cases are of the most interest. For these load cases a model is built to study the dynamics. Using this model, the resulting maximum forces in the hinges and hydraulic cylinders can be found. By comparing the determined forces to the design forces that were used, a first conclusion on the limits of the barge can be made. Design regulations for a split hopper barge In the static design/classification regulations for the SHBs by Bureau Veritas (Bureau Veritas, 2016), a cal- culation method for the forces in the hinges and cylinder is presented. The reactions in the hinges and hydraulic cylinders are determined based on the equilibria of forces and moments around the hinges. Both equilibria are found using the splitting forces that act in the splitting plane of the split hop- per barge, they follow from the summation of the different loads that act on one half-hull. The opening moment around the hinges of the barge is counteracted by the cylinders. The required force in them, Fc yl , follows directly from the mo- Figure 1: Static calculation method by Bureau Veritas ment equilibrium around the hinges. In general the hydraulic cylinders have an overcapacity, the super- fluous force in them pre-loads the barge resulting in a force in the bottom chocks. Hence, the bottom chock forces, Fb, can be obtained from the difference between the cylinder capacity and the required cylinder force. Using the cylinder and bottom chock force, a complete horizontal force equilibrium in the hinges can be made, using this it is possible to determine the reactions in the hinges. Quasi-static model of the split hopper barge In order to study more interesting load cases, the model from the design regulations is expanded. The result is a quasi-static model of the SHB in Matlab. In this model, again the reactions in the hinges and cylinders are determined based on the splitting forces in the splitting plane. The barge is loaded by forces resulting from hydrostatics, the cargo and its own weight. Using the quasi-static model, the effects of roll, different types of cargo, opening the barge and discharging of the cargo are determined. Using the results, the most governing load cases for the SHB are identified to model their dynamic influences. vii viii Summary Using the quasi-static Matlab model, first the effect of roll is considered. The barge is modelled carry- 3 ing a liquid cargo (½c = 1450kg/m ) under fixed an- gles of roll varying between 0 and 25 degrees. The static roll is found to result in a decrease of the re- quired cylinder forces,Fc yl , which is an effect of the additional closing moment due to the weight of and the hydrostatic force acting on the SHB. Through the bottom chock forces, the hydraulic cylinder force is found to have an important effect on the hinges forces. The decrease of the required cylinder forces results in an increase of the superfluous force that Figure 2: Quasi-static Matlab model excites the hinges and the bottom chocks. This in combination with a decrease of the cargo forces due to outflow over the coaming, causes the horizontal hinge forces,Fhge,y0 , to increase slightly for an increasing angle of roll. The vertical hinge forces,Fhge,z0 , are found to increase as well. For an increasing angle of roll, the uphill half-hull of the barge starts to rest on the hinges. As a result, the weight of the lifted half-hull has to be supported by the hinges, which causes an increase of the vertical hinge reactions.
Details
-
File Typepdf
-
Upload Time-
-
Content LanguagesEnglish
-
Upload UserAnonymous/Not logged-in
-
File Pages133 Page
-
File Size-