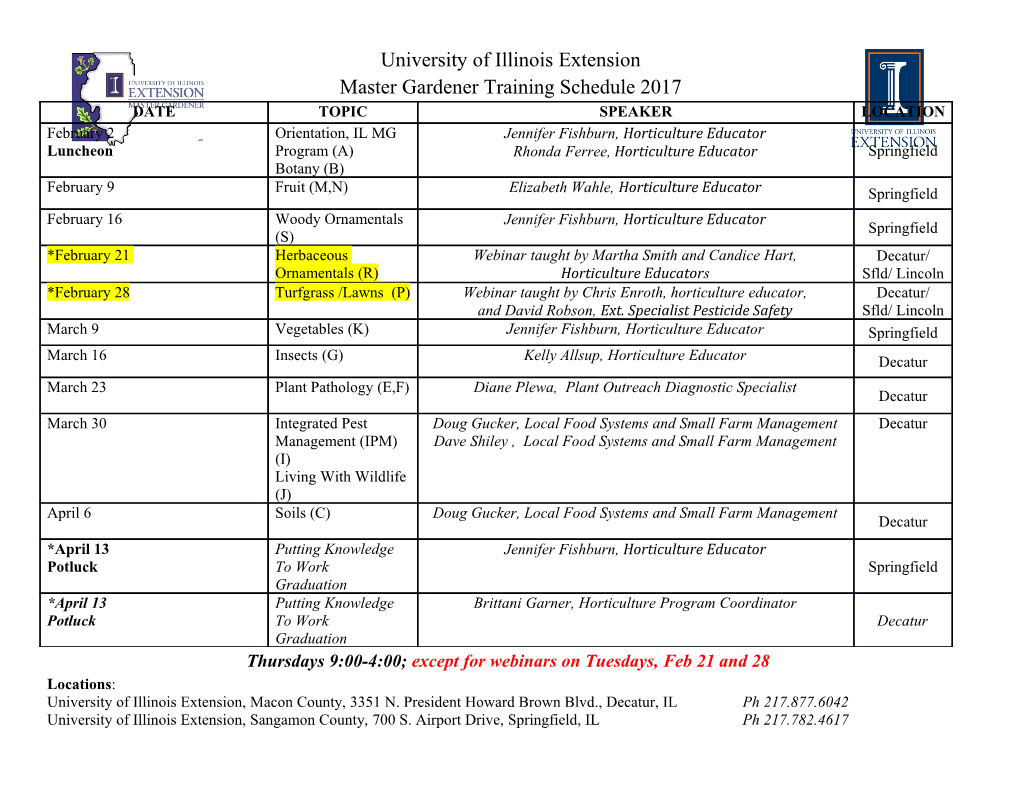
1/2014 Moving towards certification MTU Aero Engines AG Dachauer Straße 665 Customers + Partners Technology + Science Products + Services 80995 Munich • Germany Tel. +49 89 1489-0 Fax +49 89 1489-5500 Pooled expertise Improved ratios for Production parts made [email protected] www.mtu.de tomorrow’s engines by laser melting Contents Cover Story Moving towards certification 6 – 11 Customers + Partners Pooled expertise 12 – 15 Brazilian high-flyer 16 – 19 Servant of two masters 20 – 23 A powerful engine taking off to new horizons 24 – 27 Technology + Science Improved ratios for tomorrow’s engines 28 – 31 Off the beaten track 32 – 35 Pooled expertise Brazilian high-flyer More and more airlines are leasing aircraft and engines. Thanks to two GOL began operations in 2001 with six Boeing 737s, and has grown Products + Services joint ventures with Japanese trading giant Sumitomo Corporation, to become the world’s fourth-largest low-cost carrier. Since the very Production parts made by laser melting 36 – 39 MTU Aero Engines now offers its customers an even wider range of beginning, the carrier has been supported by MTU Maintenance. GOL A good bit of detective work 40 – 43 services, catering to engines throughout their entire lifecycle. is the Portuguese word for “goal”—a perfect match in the year of the Pages 12 – 15 football World Cup in Brazil. Pages 16 – 19 In Brief 44 – 45 Moving towards certification Masthead 45 The PW1100G-JM engine to power the Airbus A320neo is scheduled to obtain certification in 2014. The series of low-pressure turbine stress tests, which were successfully conducted at MTU Aero Engines in Munich early this year, marked a major milestone along the way to approval. Pages 6 – 11 Improved ratios for tomorrow’s Production parts made by laser engines melting Under the EU’s technology program ENOVAL, MTU Aero Engines is Additive processes are rapidly spreading from one industry sector to developing innovative low-pressure turbine technologies for use in the next. In aviation, too, they are playing an increasingly important More REPORT the engines of the future. Very high bypass ratios will make the en- role. In the field of engine construction, MTU Aero Engines has as eMagazine or interactive gines more efficient, quieter and cleaner, but also larger and heavier. achieved a breakthrough: The Munich-based company is among the app for Android tablets and Pages 28 – 31 first engine manufacturers in the world to use additive processes to the iPad. Go to manufacture production parts. www.mtu.de/report Pages 36 – 39 2 3 Editorial Dear Readers: As MTU Aero Engines AG’s new Chief Executive Officer, it gives me great pleasure to present the latest edition of our customer magazine. Growth in commercial aviation continues unabated this year—and will make great demands also on MTU. After all, we are playing a decisive part in the ramp-up for the production of the newest engine generations. At the same time, the aviation industry is stepping up its efforts to opti- mize the use of resources, the aim being to make tomorrow’s aircraft and engines even more fuel-efficient, cleaner and quieter. For its part, MTU, as a manufacturer of propulsion systems, has for many years been working to develop the technologies needed to further enhance the environmental compatibility and eco-efficiency of next-generation engines in a bid to drive innovation. A truly game-changing propulsion system is the Geared Turbofan™ engine jointly developed by Pratt & Whitney and MTU. Its main application is the A320neo, Airbus’s next-generation single-aisle aircraft, which will be powered by a PW1000G-family engine. In this edition of our magazine, we are pleased to report on two key mile- stones MTU has helped achieve in this program. A major milestone on the way to engine certification, which is slated for this year, was the series of low-pressure turbine stress tests successfully completed at MTU in Munich early this year. In terms of precision, these telemetry tests are extremely demanding—not only for the engine, but also for the testing team. Read our cover story to learn more about the test program. Additive manufacturing techniques are rapidly spreading from one industry sector to the next. In the field of engine construction, MTU reached another crucial milestone in May 2013 when the company—as one of the first engine makers worldwide—start- ed applying additive processes to manufacture production parts. At our Munich location, we are using selective laser melting to produce borescope bosses for the PW1100G-JM engine to power the A320neo. Our ongoing investment in new technologies also helps our customers remain at the top of their game. Both aircraft manufacturers and airlines face the challenges to bring engine lifecycle costs down and to reduce the environmental impact of avia- tion. To be able to attain these goals, we are relying on a close-knit network among all the key players in our industry. MTU has taken on leading roles in all major national and international research and development programs. One of these, the ENOVAL research project, is featured in an article in this magazine. I hope you will enjoy reading about the interesting topics covered in this issue. Sincerely yours, Reiner Winkler Chief Executive Officer 4 5 Cover Story Moving towards certification By Patrick Hoeveler The PW1100G-JM engine to power the Airbus A320neo is scheduled to obtain certification in 2014. The series of low-pressure turbine (LPT) stress tests, which were suc- cessfully conducted at MTU Aero Engines in Munich early this year, marked a major milestone along the way to approval. This telemetry testing is extremely demanding on both the engine and the testing team, as it really puts the Geared Turbofan™ (GTF) engine through its paces. fter months of preparation, there is a palpable sense of nervous anticipation in the air. Every- Athing has to run like clockwork, because the engineers don’t have much time: Their highly sensi- tive instrumentation has a limited useful life. The de- velopment test cell at MTU Aero Engines in Munich is where the action is, and all eyes are on the PW1100G-JM engine, the engine to power the Airbus A320neo. A quick glance at the hustle and bustle in the control room is enough to get an idea of just how important these tests are; there are ten times as many people at work there now than for a normal endurance run. After all, this stress testing is part of the mandatory certification process for the low-pres- sure turbine developed and produced by MTU. This is where engineers measure the vibrational stresses acting on the blades, along with the thermal load and temperature distribution for the individual engine components. 6 7 Cover Story Non-contact The engine arrived in Munich in early January, but much of the work on the high-speed low-pressure turbine was vibration done a good three months earlier. MTU’s specialists set up the low-pressure turbine in a laborious manual process, making sure it was fitted with the necessary instrumen- measurement tation—special measurement sensors on the stationary Prior to carrying out the strain gage telemetry tests, and rotating components. These strain gages are ultra- MTU Aero Engines in Munich also conducted tests thin strips of metal some three by five millimeters in size. using its non-contact blade vibration measurement They connect to the shaft via fine soldered wires that system (BSSM). This method allows vibrations to be then lead on to the telemetry transmission unit, which measured without making physical contact. Instead, sends the data to the stationary receiving unit. There are sensors are fitted in the casing around the rotor to a total of around 1,500 measuring points on the engine measure the time of arrival of the blade tips at the to be tested. “Given the limited useful life of the strain sensors and generate a signal. If a blade is vibrating, gages, the engine has to be up and running immediately it will pass the sensors either slightly earlier or and the telemetry to function straight away,” explains slightly later than it should—depending on its deflec- Kurt Scheidt, Senior Manager, Engine and Flight Testing tion at the time. An analysis of these time differ- at MTU. “It gets very hot inside the turbine, and since the ences then provides information on the vibrational extremely sensitive measurement sensors are exposed amplitude and frequency. Compared with the strain to high thermal and mechanical loads, we need to cap- gages, then non-contact technique has the advan- ture the signals as quickly as possible.” As part of the tage that it senses all blades, and not only some of tests, the engine must also be accelerated to an over- them. In the long term, the BSSM could replace the speed condition. The tests, which were scheduled to take costly and time-consuming process of applying 20 hours in all, included temperature measurements in the strain gages—provided the regulatory authorities turbine—or, more specifically, measurements of the com- agree. This latest series of tests will provide a basis ponent temperatures in stationary operation and when for comparison with the procedure currently used. subjected to load cycles. “This allows us to see whether our calculations are correct,” says Oskar Schnell, Director, The PW1100G-JM will power A320neo family aircraft from the fourth quarter of 2015. Program Management, PW1100G-JM engine at MTU. “The lent. It’s very important for the engineers to be here with results allow us to make an assessment as to the in-serv- us on site, so we can reach decisions quickly if need be,” ice life of the components.” he adds.
Details
-
File Typepdf
-
Upload Time-
-
Content LanguagesEnglish
-
Upload UserAnonymous/Not logged-in
-
File Pages23 Page
-
File Size-