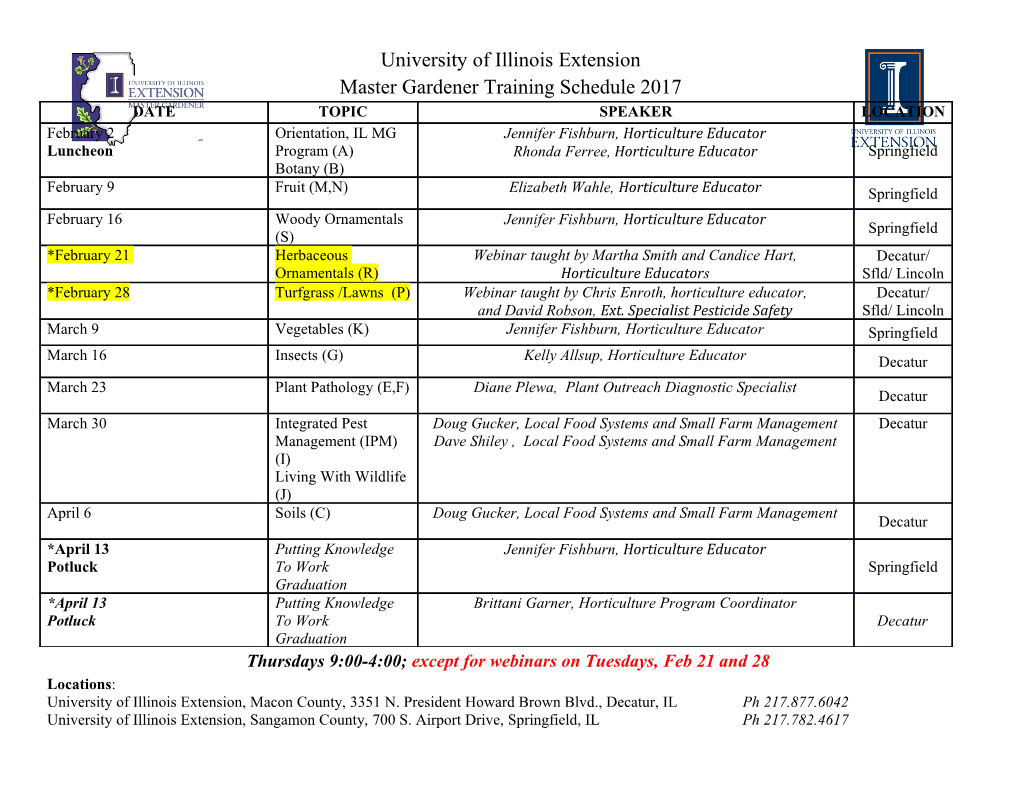
Western Michigan University ScholarWorks at WMU Master's Theses Graduate College 6-2015 Wind Oscillator for Power Genration RS Vewen Ramasamy Follow this and additional works at: https://scholarworks.wmich.edu/masters_theses Part of the Aerospace Engineering Commons, Natural Resources and Conservation Commons, and the Sustainability Commons Recommended Citation Ramasamy, RS Vewen, "Wind Oscillator for Power Genration" (2015). Master's Theses. 600. https://scholarworks.wmich.edu/masters_theses/600 This Masters Thesis-Open Access is brought to you for free and open access by the Graduate College at ScholarWorks at WMU. It has been accepted for inclusion in Master's Theses by an authorized administrator of ScholarWorks at WMU. For more information, please contact [email protected]. WIND OSCILLATOR FOR POWER GENRATION by RS Vewen Ramasamy A thesis submitted to the Graduate College in partial fulfillment of the requirements for the Degree of Master of Science in Engineering (Mechanical) Department of Mechanical and Aerospace Engineering Western Michigan University June 2015 Thesis Committee: Tianshu Liu, Ph.D., Chair Parviz Merati, Ph.D. Javier Montefort, Ph.D. WIND OSCILLATOR FOR POWER GENERATION RS Vewen Ramasamy, M.S.E. Western Michigan University, 2015 This thesis describes in detail the design, mechanical, electrical and software considerations in developing a working model for the non-conventional wind power converter called Wind Oscillator. This was based on the concept developed and patented by Tianshu Liu in the paper “Wind Oscillator and Rotor for Power Generation”[1]. In order to verify the practicality of this idea, a working model of the Wind Oscillator was designed, built and tested in the Western Michigan University wind tunnel facility. LabVIEW data acquisition and photogrammetry was performed on the model so as to evaluate the power generated by the Wind Oscillator and to study the performance and ways to improve the device. The study found that the root-mean-square (RMS) voltage output of the Wind Oscillator had a steady increase for increasing wind speed. The increase in the Angle of Attack (AoA) of the wing, AoA of the arm and the vertical position of the spring also increased the RMS voltage output of the device. The photogrammetric study of the arm and the wing reveals the difference in requested AoA for the arm and the wing by the user through the LabVIEW interface and the actual AoA of the arm and the wing. Finally, the pendulum photogrammetry helped to quantify the power output of the device. Copyright by RS Vewen Ramasamy 2015 ACKNOWLEDGMENTS I would like to extend my heartfelt thanks to Dr. Tianshu Liu, my advisor, for giving me an opportunity to work on this project. Without his support and guidance, this thesis would not have been possible; it has been an honor to have him as advisor. I would like to thank Dr. Javier Montefort for all of his patience in sharing the wind tunnel with me and help by showing me how to conduct photogrammetric studies. I would also like to thank Dr. Parviz Merati for all the guidance and the support he gave monetarily as it would be impossible for me to complete my project without it. I would also like to recognize Patrick Wewengkang for helping me in running the wind tunnel. Many thanks to Mr. Peter Thannhauser for his help with setting up and running the experiment; he helped me with the LabVIEW establishment and supervised me when running the trials. Without his help, I would not have been able to run the experiment. Last, but definitely not least, I would like to thank my friends, parents, and my family for their constant support; who was always there for me with love, support, encouragement, and motivation. RS Vewen Ramasamy ii TABLE OF CONTENTS ACKNOWLEDGMENTS .............................................................................................. ii LIST OF TABLES .......................................................................................................... v LIST OF FIGURES ........................................................................................................ vi CHAPTER I. INTRODUCTION ............................................................................................... 1 II. OBJECTIVE OF THE STUDY ............................................................................ 6 III. CONCEPTUAL DESIGN .................................................................................... 7 IV. MECHANICAL DESIGN .................................................................................. 10 Mechanical Dimension .............................................................................. 14 Mechanical Dynamics ............................................................................... 16 Spring ....................................................................................................... 19 Torsional Spring ........................................................................................ 20 Leaf Spring ............................................................................................... 24 Bearing...................................................................................................... 41 Counter Weight ......................................................................................... 44 Gear and Belt ............................................................................................ 47 V. ELETRONIC DESIGN ...................................................................................... 48 Optical Encoder ......................................................................................... 48 Optical Encoder – Arm .............................................................................. 49 Optical Encoder – Wing ............................................................................ 52 Digital IO & Power Drivers ....................................................................... 57 Power Supply ............................................................................................ 60 National Instruments (NI) Data Acquisition (DAQ) Modules .................... 62 Stepper Motor ........................................................................................... 63 VI. GENERATOR DESIGN .................................................................................... 67 Brushed dc Motor ...................................................................................... 67 iii Table of Contents – continued CHAPTER Pendulum .................................................................................................. 69 VII. SOFTWARE DESIGN ....................................................................................... 70 LabVIEW (Laboratory Virtual Instrument Engineering Workbench) ......... 70 LabVIEW - Control ................................................................................... 71 LabVIEW – Data Acquisition .................................................................... 79 VIII. WIND TUNNEL TESTING .............................................................................. 82 Model Set Up and Wind Tunnel Calibration .............................................. 82 RMS Voltage Data Acquisition and Analysis ............................................ 86 Photogrammetry ...................................................................................... 112 IX. CONCLUSION AND FUTURE WORK .......................................................... 128 CONCLUSION ....................................................................................... 128 FUTURE WORK .................................................................................... 130 BIBLIOGRAPHY ....................................................................................................... 132 APPENDICES: Minitab Output ....................................................................................145 A. Full factorial design ......................................................................................... 146 B. DOE for all the factorials ................................................................................. 148 C. DOE for selected factorials .............................................................................. 151 APPENDICES: Matlab Code ....................................................................................... 153 A. Benchmark ....................................................................................................... 154 B. Wind tunnel speed calibration .......................................................................... 156 C. LabVIEW data acquisition analysis 1 (leaf spring height7,8 and 9) .................. 158 D. LabVIEW data acquisition analysis 2 (leaf spring height7in) ............................ 167 E. LabVIEW data acquisition analysis 3 (leaf spring height 8in) ........................... 172 F. LabVIEW data acquisition analysis 4 (leaf spring height 9in) ........................... 177 G. Wing and arm photogrammetry target tracking................................................. 182 H. Wing and arm photogrammetry data analysis ................................................... 186 I. Pendulum photogrammetry target tracking ....................................................... 193 J. Pendulum photogrammetry data analysis ......................................................... 197 iv LIST OF TABLES 1. Number of oscillations the spring allows the system to make with the wind on... 22 2. The number of oscillations spring
Details
-
File Typepdf
-
Upload Time-
-
Content LanguagesEnglish
-
Upload UserAnonymous/Not logged-in
-
File Pages222 Page
-
File Size-