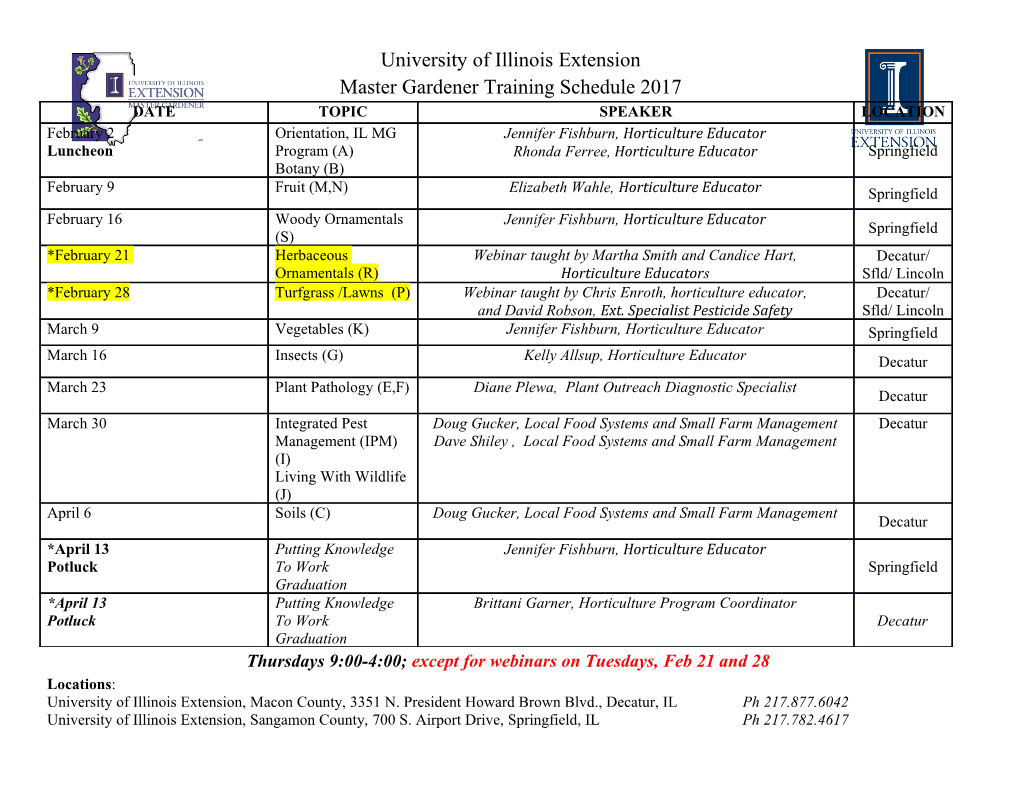
DEPARTMENT OF COMMERCE Technologic Papers OF THE Bureau of Standards S. W. STRATTON. Director No. 142 MATERIALS AND METHODS* USED IN THE MANUFACTURE OF ENAMELED CAST-IRON WARES BY HOMER F. STALEY, Metallurgical Ceramist Bureau of Standards ISSUED DECEMBER 20, 1919 PRICE 20 CENTS Sold only by the Superintendent of Documents, Government Printing Office Washington, D. C. WASHINGTON GOVERNMENT PRINTING OFFICE 1919 MATERIALS AND METHODS USED IN THE MANU- FACTURE OF ENAMELED CAST-IRON WARES By Homer F. Staley CONTENTS P»ge Introduction 6 I. Raw materials—Refractories 7 1. Feldspars 8 (a) Properties of feldspars 8 (b) Occurrence of feldspars 10 (c) Mining and preparation n (d) Effect of composition of feldspar in enamels 13 (e) Tests for feldspar 18 2. Cornwall stone 18 3. White mica 19 4. Cullet 20 5. Quartz and other forms of silica 20 (a) Occurrence and properties of silica minerals 20 (6) Effect of silica in enamels 21 (c) Tests of silica 22 (d) Substitution of flint for feldspar 22 6. Clays 23 (a) Origin and classification 23 (6) Use of clay in enamels 25 (c) Purification of clays 28 II. Raw materials—Fluxes 29 1. Calcium carbonate 29 2. Building lime 31 3. Dolomite 31 4. Magnesium carbonate 32 5. Barium carbonate and hydroxide 32 6. Soda ash 34 (a) Leblanc soda process 34 (6) Ammonia soda process 34 (c) Cryolite soda process 35 (d) Properties and effect of soda ash in enamels 35 (e) Hydrated sodium carbonate 35 7. Sodium nitrate 36 (a) Purification of niter 36 (b) Effect of sodium nitrate in enamels 37 8. Potassium carbonate and nitrate 37 9. Lead compounds '. 39 (a) Red lead 39 (6) Litharge and massicot 39 (c) White lead 39 (d) Effect of lead oxide in enamels 40 3 .. 4 Technologic Papers of the Bureau of Standards II. Raw materials—Fluxes—Continued. page 10. Zinc oxide 41 (a) Occurrence and preparation 41 (b) Effect of zinc oxide in enamels 42 11. Borax and boric acid 42 (a) Occurrence and preparation 42 (6) Effects of borax and boric acid in enamels 44 12. Fluorspar 45 (a) Sources of fluorspar 45 (6) Fluorspar as a flux 46 (c) Fluorspar as an opacifier 46 13. Cryolite 48 (a) Occurrence and preparation 48 (b) Effect of cryolite in enamels 40 14. Sodium silicofluorides 40 15. Barium fluoride 50 III. Raw materials—Opacifying agents 50 1. Theory of opacifying agents 50 2. Tin oxide 51 (a) Method of manufacture 52 (6) Characteristics of tin oxides 53 3. Antimony oxide 55 4. Sodium metantimonate 56 5. Zirconium compounds 57 6. Titanium oxide 57 7. Spinels 58 8. Arsenic oxide 58 9. Fluorides 59 10. Bone ash and other phosphates 59 IV. Enamel-making department 60 1. Storing, weighing, and mixing raw materials 60 2. Melting the enamel 62 (a) Melting furnaces 62 (b) The melting process 64 3. Dryers 65 4. Grinding machinery 66 5. Screens 67 V. Calculation of enamel formulas 68 1. Methods of expressing formulas 68 2 Example of calculation 70 3 The flint equivalent 72 VI. Ground coat enamel compositions 73 1 Materials used in frits 73 2. Raw materials in ground coats 74 3. Cobalt oxide in ground coats 74 4. Flotation of enamels 75 5. Types of ground coats 76 (a) Sintered ground coats 76 (b) Glassy ground coats 77 VII. Tin enamel compositions 82 1 Basis of classification 82 2. The leadless type 83 3. The low-lead type 84 4. The high-lead type 84 . Enameled Cast-Iron Wares 5 Page VIII. Antimony enamel compositions 88 i. Control of color 89 (a) Effect of composition 89 (6) Effect of heat treatment 91 a. Dark specks 92 (a) Cause 92 (b) Remedy 94 3. Sodium metantimonate enamel compositions 94 (a) The leadless type 94 (6) The low lead type 95 (c) The medium lead type 95 4. Oxide of antimony enamel compositions 95 IX. Luster of enamels 101 1. Crystallization 101 (a) Effect of viscosity 102 (&) Effect of concentrations 103 (c) Enameling technique 105 2 Sulphur compounds 105 3. Index of refraction 106 X. Crazing in enamels 107 1. Practical control of general crazing 107 (a) Seger's rules 107 (b) Relation of fusibility of the ground coat to that of the enamel 109 (c) Advantages of a thin and uniform coat of enamel no (d) Variations in strength and elasticity of enamels no 2. Causes of general crazing in (a) Physical principles involved 111 (b) Growth of cast iron as a factor in causing stress 112 (c) Inequality of temperature 113 (d) Inequality of expansion coefficients 114 (e) Effect of form and thickness of enamel coating 117 (/) Breaking strength of glasses 118 (g) Elasticity of glasses 118 (k) Ability of glasses to stretch 119 (*) Influence of degree of attachment of enamel to iron 120 (J) Summary of causes of general crazing 120 3. Crazing due to special causes 120 (a) Thick spots in the casting 121 (6) Thin spots in the casting 123 (c) Sharply convex curves and projecting corners 123 (d) Sharply concave curves 124 (e) Rolls ' 125 (/) Beads of enamel 125 (g) Stresses due to apparent warping and bending 126 (h) Stresses due to exterior mechanical restraint 126 (t) Unequal cooling 127 (/') Summary of crazing due to special causes 128 XI. Pinholes and blisters in enamels 128 1 Casting holes 128 2. Improperly cleaned iron 129 3. Dirty iron 130 . 6 Technologic Papers of the Bureau of Standards XI. Pinholes and blisters in enamels—Continued. page 4. Improperly heated ground coat 130 5. Improper thickness of ground coat 131 6. Defects due to enamel composition 132 XII. Making the castings 132 1. Patterns 132 2 Foundry practice 134 (a) Mold facings 134 (b) Molding machines 134 (c) Methods of handling molds 136 3. Composition of iron 140 (a) Silicon 140 (6) Phosphorus 141 (c) Manganese, sulphur, and carbon 141 XIII. Cleaning room practice 142 1. Brushing 142 2. Sand blasting 143 3. Grinding and filing 146 4. Welding 146 5. Annealing or burning out 146 XIV. The enameling process 147 1. Application of the ground coat 147 2. Enameling room equipment 149 (a) Furnaces 149 (6) Supporting the ware 154 (c) Application of the enamel 155 3. Enameling a bath tub 157 INTRODUCTION The enameling of metals is a relatively old art, but its general application to household and industrial articles represents a com- paratively recent development. In the last few years the pro- duction of enameled cast-iron and sheet-steel wares has attained a position of considerable economic importance. It is the purpose of this paper to deal with the materials and methods employed in the manufacture of enameled cast-iron ware. In order that more general information may be available regarding the raw materials used in the compounding of enamels, considerable attention is given to the sources and methods of preparation of these materials, as well as to their properties and effects when introduced into the enamel composition. Methods of calculating enamel formulas and examples of the compositions of enamels of various types are given. The defects in enamels, their causes, and the remedies to be employed in overcoming them are discussed from both the theoretical and practical standpoints. Manufacturing methods and equipment used in compounding the enamels, making and preparing the castings, and applying the enamels are also discussed. Enameled Cast-Iron Wares 7 This treatise deals with the enameling of cast iron by the dry, or American, process. In this method of manufacture, the thor- oughly cleaned casting is painted with a suspension in water of powdered glass, clay, and other materials. This suspension is known as the ground coat. The casting is then heated until the ground coat is thoroughly fused, forming an extremely thin layer of transparent glass on the casting. The piece of ware is with- drawn from the furnace and immediately coated, by means of long-handled sieves, with a layer of opaque, white, powdered glass, known as the cover-coat enamel. Next, the casting is returned to the furnace for a couple of minutes during which the cover-coat enamel fuses to a smooth layer. Two such layers of cover coat are usually applied, giving a total thickness of from ^ to ^j of an inch. The treatise does not deal with the methods of enameling cast iron by the wet process, in which a relatively thin cover coat is applied to a thick and only partially fused opaque ground coat. I. RAW MATERIALS—REFRACTORIES In order to use his raw materials to the best advantage, the enamel maker should have some knowledge of the method of their manufacture, their physical and chemical properties, the impuri- ties they are liable to contain, and their action in the enamel. Generally he has rather definite opinions in regard to the last point, based on his individual experience, but often his ideas in regard to the other points are very hazy indeed. It seems worth while, therefore, to gather from a great variety of sources the pertinent facts about enamel raw materials and to insert the compilation as one section of this treatise. The materials used for making white enamels for cast iron may be classified as follows: Refractories Fluxes Opacifying agents Calcium carbonate Antimony oxide White mica Dolomite Cullet Zirconium coumpounds Quartz and other forms ol silica. Barium carbonate and hydroxide. Titanium oxide Clays Soda ash Spinels Sodium nitrate Potassium carbonate Potassium nitrate Bone ash and other phosphates Borax and boric acid ... 8 Technologic Papers of the Bureau of Standards 1. FELDSPARS (a) Properties of Feldspars.—The feldspars 1 are hard, crys- talline minerals.
Details
-
File Typepdf
-
Upload Time-
-
Content LanguagesEnglish
-
Upload UserAnonymous/Not logged-in
-
File Pages158 Page
-
File Size-