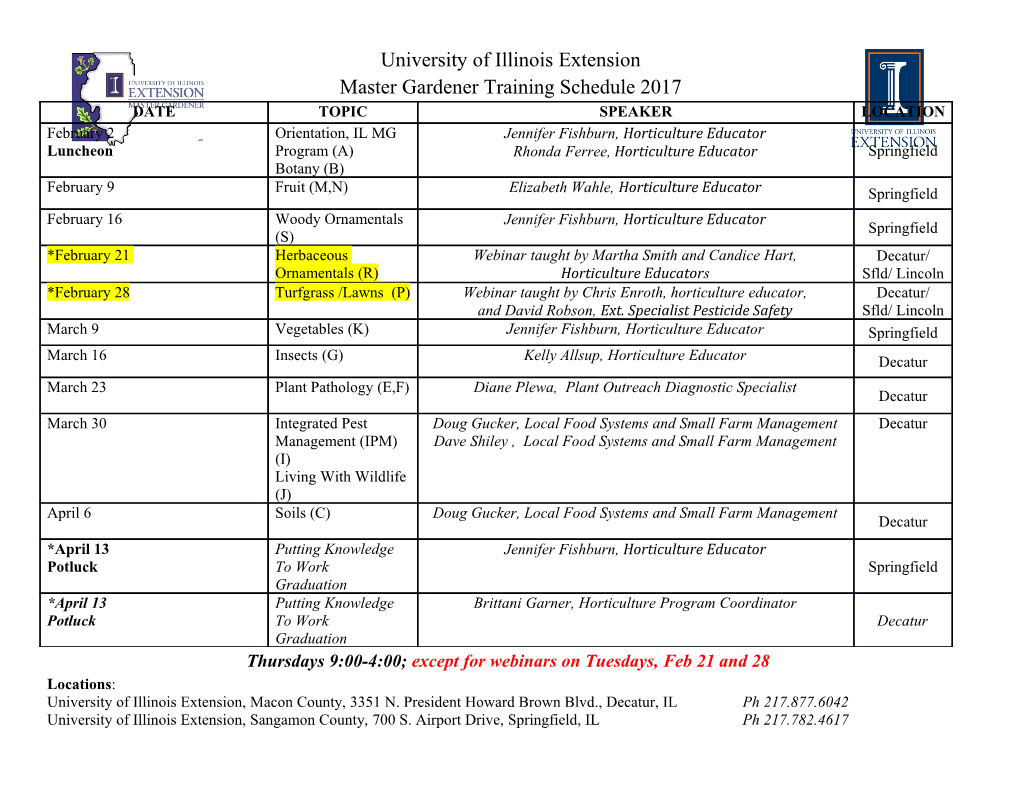
Monitoring bogie performance on straight track Part 1. Wheel set tracking position Grigory Izbinsky1, Gérard Sirois2, Yan Liu3, Denis D’Aoust1 1Wayside Inspection Devices Inc., Montreal, Canada, 2Quebec Cartier Mining Company, Canada, 3Centre for Surface Transportation Technology, National Research Council, Ottawa, Canada Abstract Monitoring of railway traffic on straight track has been successfully used for detection and repair of sub- performing bogies. There are certain advantages of using this method of inspection compared to inspection on curved track. Practical experience is illustrated by the results of monitoring iron ore traffic on Quebec Cartier Mining (QCM) with a laser-based inspection system. Relevance and importance of Tracking Error, one of the bogie performance parameters available with this method, is illustrated by the results of dynamics simulations at Centre for Surface Transportation Technology (CSTT). Wheel wear index is offered as a bogie performance descriptor. This paper is a first instalment of publications planned to discuss other aspects of wayside rolling stock inspection on straight track. Introduction Shifting to predictive rolling stock management has become one of the vital needs of railroads in North America and around the world. Predictive management requires a different approach to inspection of railroad equipment [1]. Methods and technology of inspection for predictive management must be able to evaluate rolling stock performance, to identify equipment that performs inadequately, to predict and report potential failure of components before reaching an “alarm” situation, to assist railroads in improving utilization of rolling stock and repair facilities. In order to achieve these objectives the following qualities are important when selecting inspection methods and technology: · Methods of inspection for predictive management must provide results that are repeatable at the inspection point and reproducible at other locations. Only these methods can help to set uniform standards across the railway network. · Evaluation of performance requires the selection of performance parameters that form a specific and persistent “signature” of individual piece of equipment, reflect the “health state” of equipment, and follow the equipment condition trend. Method of monitoring: Curve vs. Tangent Inspection in curves was a conventional method of monitoring bogie performance. While this method can provide some useful information, it is difficult to adapt for the purpose of predictive management. Bogie performance while negotiating a curve is strongly affected by external, to the bogie, factors. 90 90 60 60 30 30 Force, kN Force, kN 0 0 -30 -30 -10 0 10 20 30 40 -10 0 10 20 30 40 AOA, mrad AOA, mrad Figure 1: Two similar revenue trains on curve R=290 m on the same day with changing top-of-rail conditions Figure 1 illustrates results of monitoring two revenue trains on the same day on a curve with R=290 m. The trains belonged to the same owner and equally maintained . Average bogie performance for these trains was expected to be similar, yet the results were actually very different. The range of values of lateral forces and angles of attack varied due to the changing friction coefficient in the wheel/rail interface caused by changing weather conditions and operation of a nearby rail lubricator. Figure 2 shows the effect of changing of friction in the wheel/rail interface along one train on the same curve (only the leading axles shown). Low friction caused by rail surface contamination resulted in “warping” of the great majority of the bogies at the head of the train (large angles of attack) and low lateral forces. Apparently, burning off the surface contamination by the wheels of the first third of the train had restored friction thereby reducing the number of “warped” bogies and generating larger lateral forces close to the values expected for the curvature. 80 60 lateral force angle 60 50 40 40 20 30 0 20 Angle, mrad Lateral Force, kN -20 10 -40 0 13 53 93 133 173 213 253 293 333 373 Axle Figure 2: Changing top-of-rail conditions along train. Curve R=290 m. Leading axles Similar effect on bogie behavior as a result of changing train velocity is illustrated in Figure 3 that represents the results of monitoring on a shallow non-lubricated curve (R=1500 m) on a day with stable dry weather conditions. 70 70 60 60 50 50 40 40 30 30 20 20 10 10 Lateral force, kN Lateral force, kN 0 0 -10 -10 -20 -20 -2 0 2 4 6 8 -2 0 2 4 6 8 AOA, mrad AOA, mrad Figure 3: Two similar revenue trains on curve R=1100 m at 70 km/h (balance speed) and 30 km/h As shown in the above examples, the influence of external factors can be overwhelming and completely mask the performance parameters and specific characteristics of bogies negotiating a curve, regardless of the monitoring technology employed. In contrast, the behavior of bogies on the straight track is much more stable. Figures 4 and 5 illustrate repeatable bogie performance in changing operating conditions. The measured parameters are the angle of attack (AOA) and the tracking position (TP) of each axle (see inset in the next section and [2] for definitions). The range of deviations of the parameters measured from pass to pass is small, which allows recognition of the specific “signature” of each bogie determined by the bogie geometry in dynamics of main line conditions with actual lading and motion. angle-08-08 angle-08-12 angle-08-14 angle 201km/h angle 67km/h position-08-08 position-08-12 position-08-14 position 201km/h position 67km/h 12 30 10 30 20 20 8 9 10 10 6 0 6 position, mm -10 position, mm 4 0 -20 3 2 -30 -10 -40 0 -20 0 angle, mrad -50 angle, mrad -2 -60 -3 -30 9 13 17 21 25 29 33 9 13 17 21 axle # axle # Figure 4: Segment of train – 3 passes in one week Figure 5: Segment of train at different speeds Bogie parameters on tangent track The results of bogie inspection shown in this paper are obtained on tangent track with TBOGI™, a laser- based inspection system manufactured by WID Inc. The TBOGI scans trains AOA passing at track speed to determine by optical means both the angle of attack (AOA) and the tracking position (TP) of each wheel set. The TBOGI detects TP geometric faults in the alignment and tracking of bogie wheel sets on tangent track [3], which characterize a bogie behavior on tangent track and have a strong influence on the bogie steering in curves. Repeatability of results obtained from monitoring on straight track allows detecting the trend in a bogie condition. Figure 6 illustrates the results of monitoring of two bogies during the ~ 5 months interval with the most unstable weather in Eastern part of Canada. Bogie A of car QCM3082 is an example of a bogie in good condition: small AOA and TP for both wheel sets testify that both axles of the bogie are well aligned and are tracking close to the track center. The main feature of Bogie A Car QCM 3082 Bogie A, Loaded Car QCM 3125 Bogie A Loaded angle 3 angle 4 position 3 position 4 angle 3 angle 4 position 3 position 4 4 42 4 42 2 35 2 35 0 28 0 28 -2 21 angle, mrad A-end -2 21 B-end B-end angle, mrad B-end A-end B-end leading leading leading leading leading leading -4 14 -4 14 -6 7 -6 7 -8 0 -8 0 -10 -7 -10 -7 position, mm position, mm -12 -14 -12 -14 2005-08-06 2005-09-05 2005-10-05 2005-11-04 2005-12-04 2006-01-03 2005-08-06 2005-09-05 2005-10-05 2005-11-04 2005-12-04 2006-01-03 date date Figure 6: Two QCM cars. 3082 – “good actor”, 3125 – large tracking error, wheels replaced Oct 12 car QCM3125 are deviation s of both wheel sets from the track center line in opposite directions. This difference in the tracking positions of the leading and the trailing wheel sets is called the tracking error (TE). It was measured ~ 14 mm at the beginning of the monitoring interval and steadily grew to ~ 20 mm in 60 days (~0.2 mm in one 400 km round run, empty and with 93.4 tonne load). One of the main objectives of inspection for predictive management is prediction of component failure in order to proactively schedule checks and repairs to vehicles before they suffer extra damage and stress track and structures [1]. Inspection on straight track can be successfully used for this purpose. Bogie geometry defects that can be detected on straight track include angular and lateral misalignments of wheel sets, reduced steering ability manifested by improper rotation of a bogie relative to the car body or shifting to one side of the track, and lateral instability. The information contained in accurate bogie geometry measurements made on straight track facilitates finding the root cause of the problem. The volume limitation of this paper does not allow for a detailed discussion of all the features of this method. The following material will focus on one of the bogie performance parameters – the tracking position of each wheel set. Wheel set tracking position and bogie tracking error The position of each axle in relation to the track centerline is not only very repeatable at the inspection point located on the straight section of the track but also is closely reproducible at different locations along the route. It is a permanent feature of a bogie; it reflects the bogie mechanical conditions.
Details
-
File Typepdf
-
Upload Time-
-
Content LanguagesEnglish
-
Upload UserAnonymous/Not logged-in
-
File Pages7 Page
-
File Size-