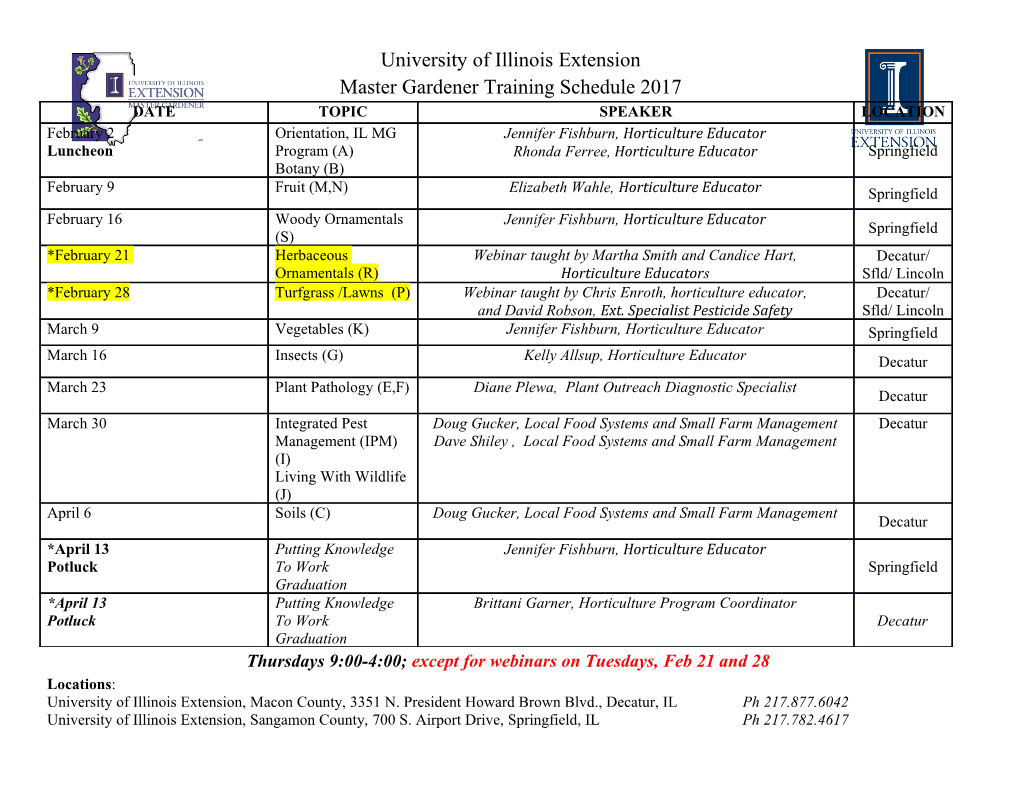
ADDITIVE MANUFACTURING OF NON PLASTIC PORCELAIN MATERIAL BY DIRECT WRITING AND FREEZE CASTING Magali Noemi Peña del Olmo BSc Industrial Design (Hons) MSc Design and Manufacture A Doctoral Thesis Submitted in partial fulfilment of the requirements of De Montfort University for the degree of Doctor of Philosophy 2011 Abstract Two direct consolidation methods usually used for advanced ceramics have been combined in this project in order to develop a novel fabrication route for traditional ceramics. Specifically the method used is based on the Additive Manufacturing extrusion process using direct writing of high solid loading ceramic pastes and then freeze-casting to solidify the deposited material. This novel fabrication method, for which a patent has been granted, has been christened “Direct Writing Freeze- Casting” (DWFC). Although the DWFC process is the subject of investigation by other researchers for a range of different applications, including the production of medical implants with alumina, the research presented in this thesis focuses on its use in the manufacture of white wares, giftware, and applied arts and crafts in general. This new system will provide designers, potters, artists, craft makers and manufacturers with a flexible and automated way of manufacturing porcelain objects. One of the major challenges to be overcome to exploit the DWFC process is the development of suitable slurry material formulations. Initial trials demonstrated that it is not possible to use conventional clay based porcelain materials with a platelet shaped microstructure which inhibits freeze casting. In this thesis the development and characterisation of non plastic porcelain slurry, based on substitution of kaolin (clay) with a calcined clay material (molochite), which can be processed using this new method is presented. The new non plastic porcelain formulation, which has a high solid load of 75.47% wt., has been subjected to detailed analysis to assess its suitability at each stage of the process; extrusion, freeze-casting (solidification) and firing. The next stage of the trials was to characterise the performance of the new slurry formulation in every stage of the DWFC process. The initial formulation was adapted to optimise its performance in the extrusion process. Extrusions trials were performed using a range of nozzle tip diameters and extrusions rates and it was found that it was not possible to successfully extrude using the smallest nozzle and highest extrusion rate. In addition other important extrusion parameters were examined, such as the stand-off distance between the substrate and the nozzle tip, extrusion rate and the velocity of the deposition head. It was found that when the stand-off distance is too small or too big flattening or curling of i the deposited bead respectively occurs. A polynomial equation was used to determine the optimum stand-off distance for a particular nozzle diameter. The material was then subjected to two different (slow and fast) freeze casting regimes and fired at different temperatures. The water absorption, bulk density, apparent porosity and linear shrinkage were measured and the structure of the porosity assessed using both optical and Electron Scanning microscopy. Both raw powders and fired samples were characterized by means of X-ray diffraction (XRD). Interconnected porosity, with a dendritic shape is formed, which is a characteristic of freeze casting. Moreover, although the apparent porosity remains the same, the size of the pores reduces as the freezing rate increases. Rheological testing was performed on the optimised slurry material using a range of methods, including cone & disc and concentric cylinder tests. In addition, a test rig was devised and manufactured which enabled rudimentary rheological testing of the slurry during actual extrusion to be undertaken. The trials showed that the material has a pseudoplastic, thixotropic behaviour. In addition it was found that there is a clear increase in the viscosity of the material as the plunger is displaced in the extrusion trials. This phenomenon is likely to be the result of “locking” of the angular particles in the slurry as pressure is applied to it. This was not observed in the other rheological trials highlighting the importance of testing materials in the mode of actual use. In this research it proved possible to develop a non plastic porcelain material which can be successfully processed using the DWFC process. Unfortunately, the level of porosity in the final samples produced was higher than the 0.5% porosity level usually associated with conventional porcelain. However, it was possible to match the level of porosity encountered with other whiteware pastes, such as stone ware, or any other whiteware with talc as a component within the formulation. ii Acknowledgment I would like to acknowledge and thank Prof. Wimpenny not only for his technical supervision but also for his support, patience and encouragement during all these years of my research on this subject. I would like to genuinely thank my supervisors Dr. Khalil and Dr. Gibbons for their guidance and setting an example for myself. I would also thank Roy Carter for his help and advice in resolving the technical difficulties faced in this research. My sincerest appreciation to all members of the Additive Manufacturing Technology Group at De Montfort University, Leicester for their help and collaboration. A special thanks to the Department of Geology, University of Leicester for their help and advice and also to the Glass and Ceramic Workshop, De Montfort University for their help and use of facilities. Special thanks to the National Council of Science and Technology of Mexico, (CONACYT) for its support in my professional career. My earnest thanks go to my parents, sisters, family and friends for their love and moral support throughout all my studies. iii Table of Contents ABSTRACT ........................................................................................................................................... I ACKNOWLEDGMENT ......................................................................................................................... III LIST OF ACRONYMS .......................................................................................................................... VII TABLE OF FIGURES .......................................................................................................................... VIII LIST OF TABLES .................................................................................................................................. XI 1. INTRODUCTION .......................................................................................................................... 1 1.1 THESIS OUTLINE ........................................................................................................................... 1 1.2 RESEARCH BACKGROUND ............................................................................................................. 3 1.3 PROJECT AIM AND OBJECTIVES .................................................................................................... 6 1.4 OVERALL PROJECT ........................................................................................................................ 8 2. THEORETICAL BACKGROUND ..................................................................................................... 9 2.1 ADDITIVE LAYER MANUFACTURING ........................................................................................... 9 2.1.1 Introduction ..................................................................................................................... 9 2.2 AM OF CERAMICS METHODS: AN OVERVIEW ............................................................................. 13 2.2.1 Polymerization ............................................................................................................. 14 2.2.1.1 Stereolithography of ceramic-filled resin ................................................................... 14 2.2.1.2 Paste Polymerization .................................................................................................. 17 2.2.1.3 Direct Photo Shaping (DPS) ........................................................................................ 20 2.2.1.4 Indirect Stereolithography .......................................................................................... 22 2.2.2 Sintering or Bonding of Ceramic Powders ..................................................................... 22 2.2.2.1 Laser Sintering ............................................................................................................ 22 2.2.2.2 Laser Engineering Net Shaping (LENS)....................................................................... 25 2.2.3 Ink Jet Printing based methods ..................................................................................... 27 2.2.3.1 3-Dimensional Printing of Ceramics ......................................................................... 27 2.2.3.2 Direct Ceramic Ink-jet Printing (DCIJP) ...................................................................... 36 2.2.4 Laser Cutting of Ceramic Sheets .................................................................................... 38 2.2.4.1 Laminated Object Manufacturing (LOM) ................................................................... 38 2.2.4.2 Computer-Aided Manufacturing of Laminated Engineering (CAM-LEM) ..................
Details
-
File Typepdf
-
Upload Time-
-
Content LanguagesEnglish
-
Upload UserAnonymous/Not logged-in
-
File Pages267 Page
-
File Size-