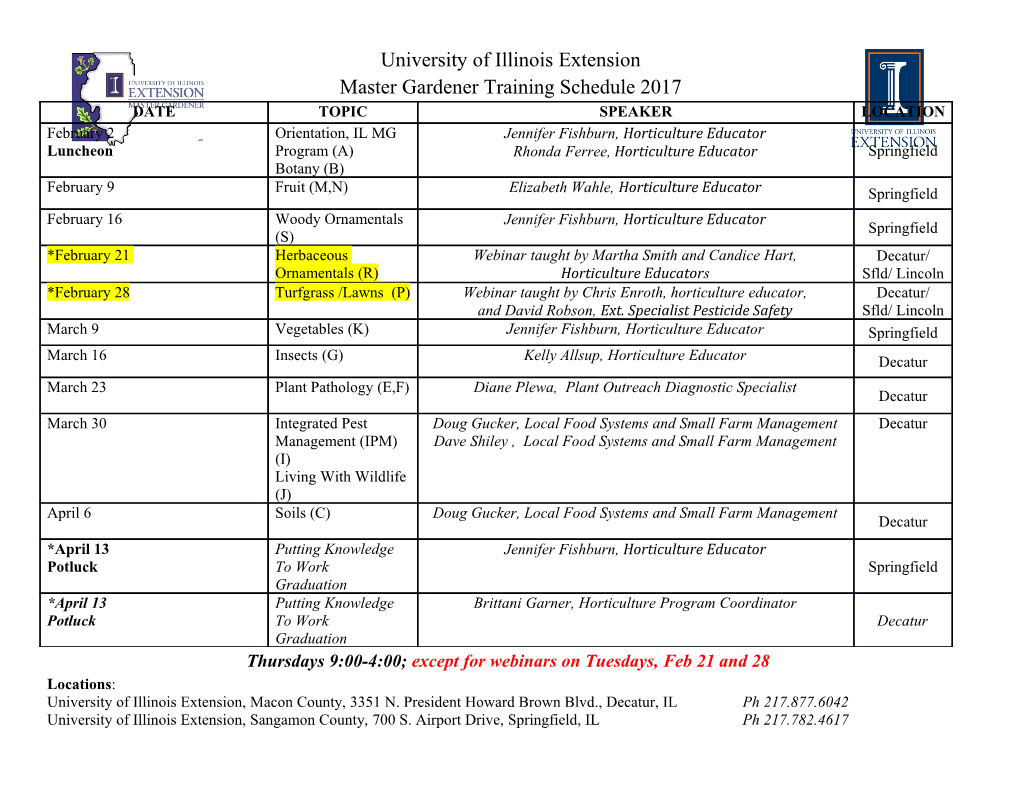
The Future of Aero Engines is Now. Annual Report 2007 2008 The challenges. The skies are crowded and they are not set to get any less so. Quite the contrary: Experts predict that the volume of air traffic will double by 2020. Good prospects for the aviation industry, but bad news for the environment? In order to ensure that this growth does not come at the expense of our climate and that rising fuel prices do not affect ticket sales, aircraft and engines must become greener and more economical. New ideas and concepts are needed to reduce aviation fuel consumption, bring down manufacturing and maintenance costs, and make aircraft quieter and more environmentally compatible. Since 2002, these objectives have been clearly expressed in numbers: The targets defined by the Advisory Council for Aeronautical Research in Europe (ACARE) call for a 50 % gain in fuel efficiency, a 50 % cut in carbon dioxide emissions, and an 80% reduction in the output of nitrogen oxides by the year 2020. Perceived noise levels, too, are to be reduced by half. Aircraft engines will play a key role in achieving these goals. New technologies and innovative compo- nents will be needed to meet these demanding requirements. For decades, MTU has been working on new propulsion concepts for the future, and has now shaped them into a concrete program called ‘Claire’ – the company’s answer to the tomorrow’s needs. 2008 2015 2025 2035 CLAIRE MTU’s new technology program. When it comes to the issue of climate change, MTU plans to take concrete action. The aim is to drastically reduce the carbon dioxide emissions of engines in three stages – first by 15, then by 20, and finally by 30% by 2035. These are the milestones that Germany’s leading engine manufacturer has set itself for the coming years. Together with the futurologists at Bauhaus Luftfahrt, the engine experts devised a plan of action that resulted in the technology program Clean Air Engine (Claire), in which a new engine is to be developed. Claire combines several key components that have already been developed and tested, or for which proof of principle has been demonstrated, to form an inno- vative engine concept. It fulfills all expectations concerning energy efficiency and economic viability. The innovative engine is based on the geared turbofan design, which has two crucial advantages: It lowers carbon dioxide emissions and generates less noise. The geared turbofan engine is additionally equipped with a counter- rotating propfan and MTU’s innovative heat exchanger technology, which reduce its environmental footprint still further. 2015 The geared turbofan. -15% At the heart of MTU’s three-stage concept is the geared turbofan, which promis- es to reduce carbon dioxide emissions by about 15 %. The aim is to reach this mark by 2015. The key components of the geared turbofan are a high-speed low-pressure turbine made by MTU, a high-pressure compressor jointly built by MTU and Pratt & Whitney, and a gear unit developed specially for this applica- tion by the Italian gear specialist Avio. What is special about the gear unit is that it decouples the fan from the low-pressure turbine, unlike in conventional engines, where the two compo- nents are rigidly connected to one shaft. This enables each of them to run at their optimum speeds, thus improving efficiency, lowering fuel consumption and consequently reducing carbon dioxide emissions. In addition, the geared turbofan reduces perceived noise by as much as half. This is a clear strength compared to today’s modern engines. Rather than having to choose between carbon dioxide and noise reduction, the Claire concept implements both simultaneously. 2025 Geared turbofan with counter-rotating propfan. -20% In the second phase of the Claire program, the aim is to reach a 20% reduction in carbon dioxide output by 2025. This is to be achieved mainly by equipping the geared turbofan with a two-stage counter-rotating shrouded propfan. MTU already developed and tested a fan of this type back in the 1980s. In close collaboration with scientists at the German Aerospace Center (DLR), it set up a technology program called Crisp (Counter Rotating Integrated Shrouded Propfan). The result was a two-stage, counter-rotating propfan which proved to be highly efficient. Acoustic measurements revealed that the shrouded fan beats the alternative concept of the open fan hands down in terms of noise development. The propfan would have saved a considerable amount of fuel thanks to its high efficiency, especially on long-haul flights. However, the time was not ripe, as fuel prices were not a cause for concern back then. This has now changed, which is why the Crisp concept has become more attractive than ever. 2035 Geared turbofan with heat exchanger. -30% In the third phase, Claire will prepare for the final sprint to achieve the goal of 30% less carbon dioxide by 2035. In this phase, the focus will shift to MTU’s heat exchanger technology. The innovative Claire geared turbofan with its integrated counter-rotating propfan will be retrofitted with a recuperator that recovers the heat of the exhaust gas stream and feeds it back into the process cycle upstream of the combustion chamber. In combination with various other technological features designed to optimize engine performance – such as the use of active systems and cooling-air cooling – the heat exchanger is expected to achieve the final 10 % cut in carbon dioxide. The recuperator is further proof of MTU’s power of innovation. The underlying technology was developed and tested by MTU in the context of a European technology program called Clean (Component validator for environmentally friendly aero engine). The Clean program resulted in a new, green engine con- cept capable of producing fuel savings of 15 to 20%. MTU’s heat exchanger, with its lancet-like exchange tubes, was a major contributing factor. Its advan- tages are now being put to use in the Claire program – for the benefit of the environment and aviation. Table of contents 2 Table of contents 3 Selected consolidated financal information and key figures at a glance 4 Highlights 2007 6 Foreword by the Chief Executive Officer 8 The Board of Management 10 The MTU share 16 Corporate social responsibility Group mangement report 23 The operating environment 31 Financial situation 53 Employees 56 Environmental report 57 Subsequent events 57 Management compensation report 58 Risk report 64 Forecasts 66 Note concerning the required disclosures pursuant to Section 289 (4) and Section 315 (4) of the German Commercial Code (HGB) 70 Value added statement Consolidated Financial Statements 73 Consolidated Income Statement 74 Consolidated Balance Sheet 76 Consolidated Statement of Changes in Equity 77 Consolidated Cash Flow Statement Notes to the Consolidated Financial Statements 78 Accounting Policies and Principles 99 Notes to the Consolidated Income Statement 112 Notes to the Consolidated Balance Sheet 149 Other disclosures 165 Segment information 170 Events after the balance sheet date 171 Reconciliation of group net profit with net profit of MTU Aero Engines Holding AG 174 Independent Auditor’s Report Corporate Governance 176 Corporate Governance Report 180 Management Compensation Report 186 Report of the Supervisory Board 190 The Supervisory Board 192 Glossary of engine terms 196 Overview of Engines 197 Contacts/Financial Calendar 2008 2 Selected consolidated financal information and key figures at a glance Change 2007 2006 2005 2004 1) in € million (unless otherwise specified) 2007 – 2006 € million in % Revenues and earnings Revenues 159.7 6.6 2,575.9 2,416.2 2,182.7 1,918.0 thereof: commercial and military engine business (OEM) 116.4 7.8 1,599.5 1,483.1 1,434.8 1,375.6 thereof: commercial maintenance business (MRO) 50.0 5.2 1,004.7 954.7 766.9 575.9 Gross profit 93.7 26.6 446.4 352.7 288.0 290.4 Gross profit in % 17.3 14.6 13.2 15.1 Earnings before interest, tax, depreciation and amortization (EBITDA) 57.3 17.1 392.9 335.6 295.3 214.1 EBITDA in % 15.3 13.9 13.5 11.2 Net profit 65.0 73.0 154.1 89.1 32.8 0.2 Revenues and earnings (adjusted) Earnings before interest, tax, depreciation and amortization (EBITDA) 74.7 23.5 392.9 318.2 238.7 172.2 EBITDA in % 15.3 13.2 10.9 9.0 Underlying net income 26.4 21.7 148.2 121.8 53.1 13.0 Balance sheet Total assets 99.5 3.3 3,085.5 2,986.0 2,808.2 2,719.1 Equity -0.3 -0.1 562.0 562.3 528.0 217.0 Equity ratio in % 18.2 18.8 18.8 8.0 Financial liabilities -12.3 -3.6 326.5 338.8 326.7 866.5 Cash flow Cash flow from operating activities 26.4 12.6 236.2 209.8 273.3 72.9 Cash flow from investing activities 2) -10.4 -11.1 -104.5 -94.1 -83.9 -59.8 Free cash flow 2) 16.0 13.8 131.7 115.7 189.4 13.1 Free cash flow as % of revenues 5.1 4.8 8.7 0.7 Cash flow from financing activities 2) -128.1 -339.8 -165.8 -37.7 -207.5 -190.7 Number of employees at year-end Commercial and military engine business (OEM) -130 -2.7 4.610 4.740 4.805 5.469 Commercial maintenance business (MRO) 183 7.8 2,520 2,337 2,125 1,948 Share data Earnings per share (in €) Basic (undiluted) earnings per share 1.31 79.9 2.95 1.64 0.60 n.a.
Details
-
File Typepdf
-
Upload Time-
-
Content LanguagesEnglish
-
Upload UserAnonymous/Not logged-in
-
File Pages208 Page
-
File Size-