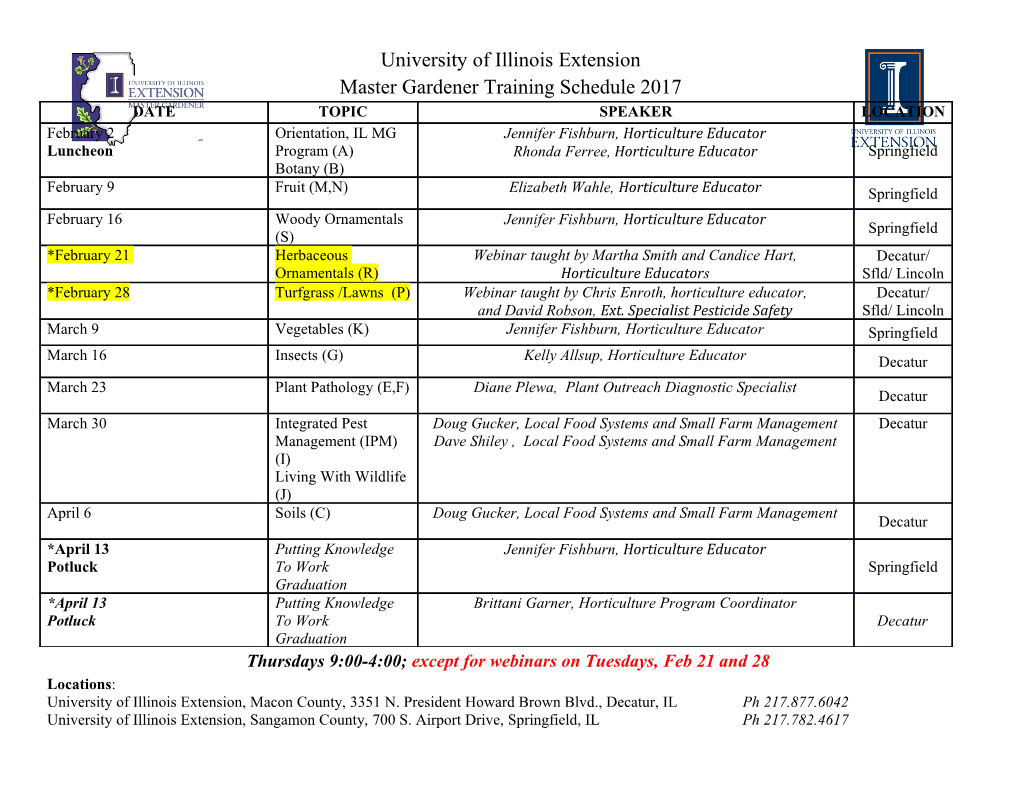
2005-01-2490 Diesel Engine Cold Start Noise Improvement Norbert Alt, Hans-Dieter Sonntag, Stefan Heuer, Rainer Thiele FEV Motorentechnik GmbH Copyright © 2005 SAE International ABSTRACT expected for the U.S. market. The overall improved noise and vibration behavior of modern diesel engines The European as well as U.S. market share of modern has also contributed to this trend. However, during cold Diesel engines has increased significantly in recent start and warm-up at low exterior temperatures, many years, due to their excellent torque and performance diesel engines still produce an unpleasantly noisy behavior combined with low fuel consumption. The knocking sound. overall improved noise and vibration behavior of modern 60 Diesel engines has also contributed to this trend. cold engine 50 hot engine Despite overall improvements in Diesel engine noise and 40 BOI + 6°CA vibration, certain aspects of Diesel engines continue to 30 pRail -70 bar present significant challenges. One such issue is the 20 presence of Diesel knocking that is prevalent during cold 10 cylinder pressure[bar] 0 start and warm-up conditions. This paper discusses a 90 120 150 180 210 240 270 6 technique used to optimize the cold start noise behavior of modern Diesel engines. 4 2 [bar/°CA] 0 The methods used in this study are based on optimizing α -2 the engine calibration to improve the vehicle interior and dp/d -4 exterior (engine) noise, even at low ambient 90 120 150 180 210 240 270 temperatures. Initially, the engine’s combustion noise crank angle [° CA] behavior is characterized by measuring the cylinder pressure (under various operating conditions) and Figure 1: Cylinder Pressure Trace and Gradient for developing appropriate transfer functions. Various Cold and Hot Conditions engine calibration iterations are carried out using a structured Design of Experiments (DOE) and for each As an example, Figure 1 shows the cylinder pressure iteration, the measured cylinder pressure is used to curves and their first derivation over the crank angle of a calculate the combustion noise influence (based on Diesel engine with a common rail injection system and existing transfer functions). At the end of this study, the standard calibration at a cold and warm state, influence of key calibration parameters on improving the respectively. At a cold state, engine temperature cold start noise characteristics is demonstrated. amounts to 10°C and intake air temperature 0°C. At a warm state, it amounts to 85°C and 20°C, respectively. The acoustic optimization achieved in this way has no Both calibration states were using pre-injection and detrimental effects on the engine’s ability to start, main-injection. The difference is caused by 6°C earlier combustion stability, visible black or white smoke and timing as well as a rail pressure increase by 70 bar, emissions. Finally, the potential of using the developed during cold engine operation. Under cold operating technique in conjunction with other new technologies, conditions, a considerably higher cylinder pressure such as exhaust gas after treatment systems and gradient results in a louder and more unpleasant alternative preheating and boosting concepts, is combustion noise. discussed. Recent investigations at FEV Motorentechnik showed INTRODUCTION that careful calibration optimization can significantly improve interior and exterior noise, even at low ambient The excellent torque and performance behavior of temperatures. Based on these findings, a time effective modern diesel engines combined with low fuel method to optimize Diesel knocking was developed. It consumption and exhaust emissions has increased their utilizes Design of Experiments (DoE), the prediction of market shares especially in Europe, but it is also combustion noise by FEV-CSL (FEV-Combustion Sound Level, procedure will be described later) as well as a new and main injection, the rail pressure as well as the combination of the latest engine and vehicle cold-test rig exhaust recirculation rate was also varied. In total, five capabilities. (5) representative operation points from the load and rpm range were examined. A 15°C engine temperature and The acoustic optimization achieved in this way does not 0°C intake air temperature were defined as the base. have and detrimental effects on the engine’s ability to Pre-injection was activated in all operation points. Aside start, combustion stability, visible black or white smoke from exhaust gas raw emissions (HC, CO, NOx and and emission behavior. In the future, improved exhaust particulates), the cylinder pressures were measured to gas aftertreatment systems and alternative preheating predict the engine noise level by the CSL. and boosting concepts are expected to reduce Diesel Engine test cell for cold testing cold start noise even further. CO engine HC No intake air intake air x smoke EFFECTIVE METHOD FOR NVH ORIENTATED boosting heating / cooling catalyst CALIBRATION OPTIMIZATION The disturbing diesel knocking is caused by hard -15°C → +60°C combustion, as explained earlier. Therefore, cold start 1 → 1.4 bar abs optimization must aim at reducing combustion excitation. By using modern measurement and analysis methods engine oil heating / cooling (engine or vehicle cold test bench, noise prediction by 10°C → 90°C CSL and DoE guided measurement programs), calibration adjustment and thus noise quality can be engine water heating / cooling considerably improved. However, apart from the 10°C → 90°C dependence on the quality of the base calibration, the acoustic optimization potential is also limited by Figure 2: Boundaries of the Engine Cold Test Cell requirements (e.g. reliable start-up at 30°C) and the combustion calibration data set is processed based on Figure 3 shows the effects of varying oil/cooling water the pre-optimized mapping points. It is then verified and temperature, intake air temperature, boost pressure and fine-tuned on the vehicle, using a cold test bench with start of main injection (BOI) on engine noise (CSL) and regard to NVH and emission behavior, stability, cold start relevant carbon monoxide and hydrocarbon acceptable black and white smoke quantities as well as emissions. relevant emissions (e.g. like European or American test T [°C] T [°C] p [bar ] BOI [°CA ] oil/water intake air boost abs BTDC cycles like NEDC- / U.S. Tier-II, III, IV, …..). 0 20 40 60 80 100 -20 0 20 40 60 1,0 1,1 1,2 1,3 1,4 1,5 6 4 2 0 -2 -4 75 74 PRE-STUDY ON ENGINE TEST BENCH - BASED 73 ON AN INTERNAL RESEARCH PROJECT 72 FEV-CSL [dB(A)] FEV-CSL 71 70 2500 The combustion noise is mainly determined by the cylinder pressure excitation, which in turn is 2000 characterized (aside from fuel characteristics) by the 1500 CO injection parameters (quantity and timing of pre- and 1000 main injection respectively, injection pressure, etc.). Also 500 raw emission [ppm] raw emission HC of significant importance is the engine structure as a 0 transfer system; therefore, in the engine design process Figure 3: Basic Engine Test Cell Investigations for a careful acoustic optimization is necessary to Cold Testing specifically avoid structural weaknesses with respect to combustion excitation. The variation of cooling water, intake air and boost The influence of different injection parameters was pressure shows no significant influence on noise; investigated in this research project for a turbocharged 4- whereas, hydrocarbon and carbon monoxide emissions cylinder common rail Diesel engine (2.0L displacement) are considerably diminished, especially by increased on a cold engine test bench. The test bench allows the oil/water temperature and intake air temperature. This variation of intake air, oil and cooling water temperature, creates additional freedom for acoustic optimization. By as well as load pressure (for a schematic test bench delaying BOI, combustion noise is - as expected – layout, see Figure 2 ). Cooling water and oil reduced; however, HC and CO emissions are temperatures can be freely adjusted between -25°C and simultaneously increased. 90°C and intake air temperature between -30°C and The minor dependency of combustion excitation on 60°C. Boost pressure could be increased up to 1.4 bar intake air and combustion chamber wall temperature (absolute). The time of injection and the quantity of pre- (oil/water temperature), as well as boost pressure, Additionally, the increased flexibility of injection systems seems to contradict literature (/3/, /4/) and also the and the possibility to control the combustion process common understanding. However, it can be explained by even more precisely promises more freedom for further pre-injection, which currently has become customary. acoustically orientated calibration optimization in the Respectively, the injection timing delay is predominant, future. In this context, multi-injection and injection curve not the ambient temperature. Especially at low shaping needs to be mentioned. Increased processor temperatures, ignition delay is drastically reduced by pre- and storage capacity of the control units also contribute injection. With the start of pre-injection, the first pre- to this trend. In the heat-up behavior, more advanced reactions (for instance radical formation) occur, which at heating elements can improve conditions for a smooth the onset of main injection facilitate a quick ignition of the starting and running combustion process. induced fuel with a subsequent smooth combustion Nevertheless, the calibration potential is limited. process. Therefore, non-engine approaches for the exploitation of additional NVH optimization potentials are discussed in The results of the basic investigations on the engine cold the following text. test bench show that boost pressure and intake air temperature increase and both exhibit a significant Considering that some exhaust system components act potential for the reduction of exhaust gas raw emissions, against combustion excitation and thus combustion which can be used for acoustic calibration (Figure 4). noise, even more efficient exhaust aftertreatment Combustion excitation acts against HC and CO raw systems (particulate filters, oxidizing catalysts etc.) are emissions.
Details
-
File Typepdf
-
Upload Time-
-
Content LanguagesEnglish
-
Upload UserAnonymous/Not logged-in
-
File Pages6 Page
-
File Size-