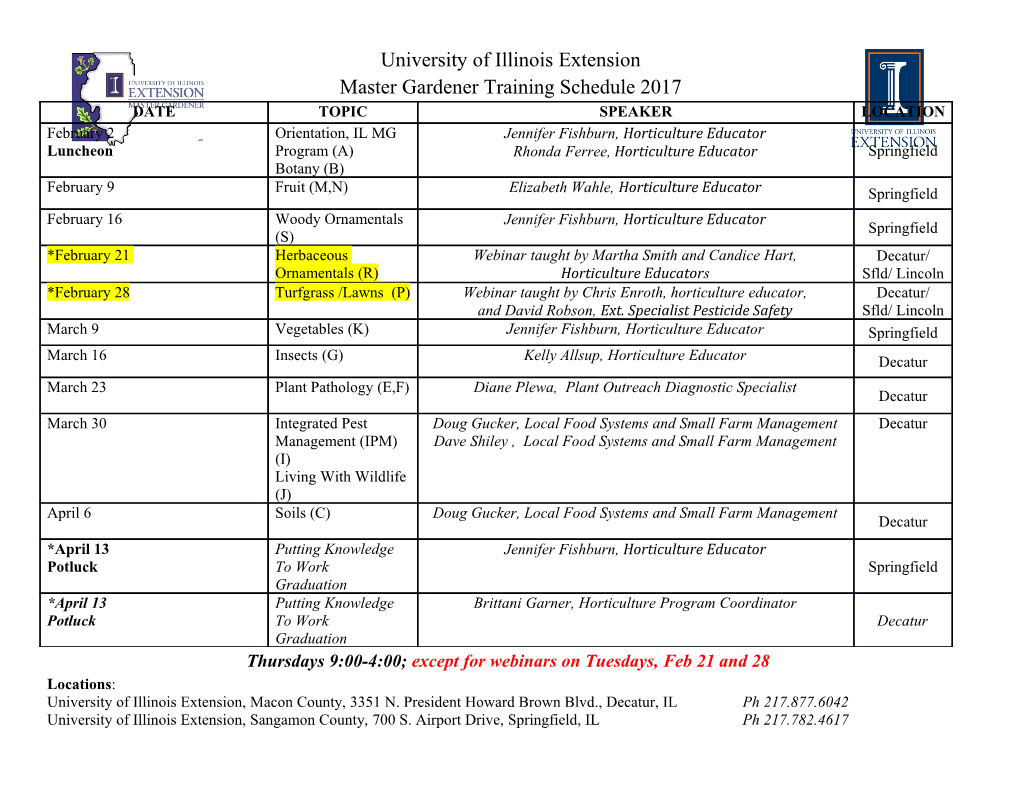
RROBOTICSOBOTICS ININ MMANUFACTURINGANUFACTURING TTECHNOLOGYECHNOLOGY RROADMAPOADMAP November 2006 Prepared for Prepared by: Acknowledgement This Technology Roadmap was prepared as part of a project entitled “Robotically Enhanced Advanced Manufacturing Concepts to Optimize Energy, Productivity, and Environmental Performance.” Funding for this project was provided by the U.S. Department of Energy (Project #DE-FG36-05GO85046). Robotcs n Manufacturng Technology Roadmap Table of Contents Introduction ..................................................................................................................................................1 Background..............................................................................................................................................1 The Role of Robots in Manufacturing Today ....................................................................................1 Trends Impacting the Future Use of Robotics .......................................................................................5 Future Advances in Robotics ................................................................................................................5 Non-Technical Trends and Drivers......................................................................................................6 Barriers and Challenges to the Use of Robotics ....................................................................................9 High Priority Technical Challenges and Barriers to Robotics in Manufacturing .........................9 High Priority Non-Technical Challenges and Barriers to Robotics in Manufacturing ..............11 Research and Development and Other Activities ..............................................................................15 High Priority Research and Development ........................................................................................15 High Priority Non-Technical Activities.............................................................................................20 References ...................................................................................................................................................27 Appendix A: List of Participants ..........................................................................................................29 Appendix B: Acronyms Used in Action Plans .....................................................................................31 Robotcs n Manufacturng Technology Roadmap Robotcs n Manufacturng Technology Roadmap Introducton Background allow for extremely precise manipulation of a tool “hand,” the addition of cameras, and the American manufacturers are facing increased integration of artificial intelligence into gov• global competition, particularly from countries erning software have all enabled more rapid where labor costs are much lower than those and fine-tuned adaptation. in the United States. New technologies that The robotics industry has grown to provide a improve manufacturing cost competitiveness wide range of robots for use in global manu – including those that increase productivity or facturing industries. Precise assembly, repair, reduce energy use – will help meet this chal• demolition, and other crucial manufacturing lenge. Industrial robots, which have been in steps can be accomplished efficiently, quickly, use since 1961, have the potential to make a and at lower cost than human labor. This greater contribution to productivity in manu increased productivity has contributed to an facturing. annual increase in both the number of user This Technology Roadmap for Robotics in Manufac• industries and total robots shipped. turing is the result of a collaborative effort to Since 1990, some applications of robots have assess the future of robotics in manufacturing. enjoyed a cost advantage over human labor. To gain industry input to the roadmap, a work• Falling prices and increasing machine capabili shop was held in June 2006 with emphasis on ties during this period dramatically decreased the application of small lot and flexible robot robot costs. In 2003, robots were being pro systems in manufacturing. In this workshop, duced at a fifth of the cost of a robot built in industry stakeholders outlined critical barriers 1990, with the same capabilities. In addition, to increasing the use of robots, and provided hourly wages have greatly increased since their thoughts on the research, development, 1990, particularly in the automotive industry, and other activities needed to overcome those making robots even more cost-competitive barriers. Contributors to the report are listed [UNECE 2004]. in Appendix A. The largest user of industrial robotics today The Role of Robots n Manufacturng Today is the automotive industry, which was respon sible for about 50 percent of all domestic Since the first industrial robot—essentially, a industrial robot purchases in 2004 [UNECE mechanical arm—received a patent in 1954, 2004]. Robots have been used since the late radical changes in global competition and 1970s in car production for welding, paint advancements in computer technology have ing, and assembly. Despite a recent down• led the way for increased sophistication and turn in the American car industry, auto parts capability of this technology. The addition producers are growing and driving a surge in of three more axes (pitch, roll, and yaw) that robot orders, even when global automotive Robotcs n Manufacturng Technology Roadmap end producers are lightening their demand. Furthermore, growth in industries such as The Robot Advantage: semiconductors, electronics, plastics, food, Accuracy, Speed, Increased Productivity, consumer goods, and pharmaceuticals assures and Flexibility the robotics industry an important place in Robots have several advantages over worldwide manufacturing [UNECE 2004, IFR humans which make them excellent for 2005]. Increased automation in these and other working in environments such as assem• industries, such as off-road vehicles, applianc bly and manufacturing plants, hazardous es, aerospace, and metal fabrication, are also mines, and in situations where the work is contributing to the increased use of robots. mundane or monotonous. Most industrial robots worldwide are used Ro in welding and material handling or moving. Productivity and Cost Benefits bots can consistently produce more high- As shown in Figure 1, these two tasks com• quality products than humans, never tire mand 88 percent of all robotic activity, while and can work nonstop without breaks, other tasks like painting, sanding, and assem• and do not require benefits. This trans• bly filling make up the remaining 12 percent lates into increased productivity, lower [Vincent 2006]. This range of tasks capitalizes manufacturing costs, and in some cases, on the advantages robots hold over human reduced use of energy and raw materials. labor in high-volume and harsh manufacturing environments. Advances in technology are also Doing Hazardous or Mundane Jobs beginning to allow complex, variable tasks to Robots can do the work that no one else be conducted robotically. wants, such as mundane, dangerous, bor• ing or repetitive jobs. Robots can take In 2004, the majority of installed robots over in situations where work is extremely worldwide were multi-purpose articulated hazardous to human health, and can work robots, accounting for 62.5 percent of sales with humans to make their jobs easier. [IFR 2005]. Other more specialized varieties make up the difference (see Figure 2). Asia has Consumer Benefits Robots can pro• the largest market for industrial robotics. Japan duce high quality goods quicker, which and Korea, long the market leaders in robot significantly reduces poorly-made goods ics production and purchasing, are experienc and lowers the cost of goods to the con• ing healthy expansion, although the robotics sumer. industries in North America and Europe are catching up. North American robot sales are expected to show strong growth through 2008, as critical growth engines. In Europe, a num in part because of heavy Japanese automotive ber of synergistic projects are bringing togeth• investment. Worldwide, the robotics industry er industry and academia to further develop is predicted to continue to grow through 2008 the robotics industry. The European Robotics [Vincent 2006]. Platform (EUROP) was recently approved at a level of $100 million per year. Similar initia• Investment in robotics research and develop• tives do not exist in the U.S., and currently ment is stronger and more coordinated in Asia there is no national strategy that focuses on and Europe than in the U.S. Both Japan and robotics. R&D outside of the U.S. has focused Korea are implementing a national agenda in primarily on legged mobility, perception, robotics, and both countries include robotics and autonomy to support manipulation and Robotcs n Manufacturng Technology Roadmap Fgure . New Robot Sales Based on Expected Use [Vncent 006] Assembly < 10 lbs Other, Inspection & 3% Assembly > 10 lbs Material Removal 1% 3% Spot Welding 24% Material Handling >10 lbs 36% Arc Welding 20% Dispensing/ Material Coating Handling <10 lbs 5% 8% Fgure . Worldwde Dstrbuton of Newly Installed Robots, 004 [IFR 005] Scara 12% Cylindrical 10% Linear/ Cartesian/ Articulated Gantry 63% 15% Robotcs n Manufacturng Technology Roadmap other tasks. In the U.S., R&D has emphasized wheeled mobility, perception, and autonomy in navigation; the U.S. also leads in efforts to improve
Details
-
File Typepdf
-
Upload Time-
-
Content LanguagesEnglish
-
Upload UserAnonymous/Not logged-in
-
File Pages36 Page
-
File Size-