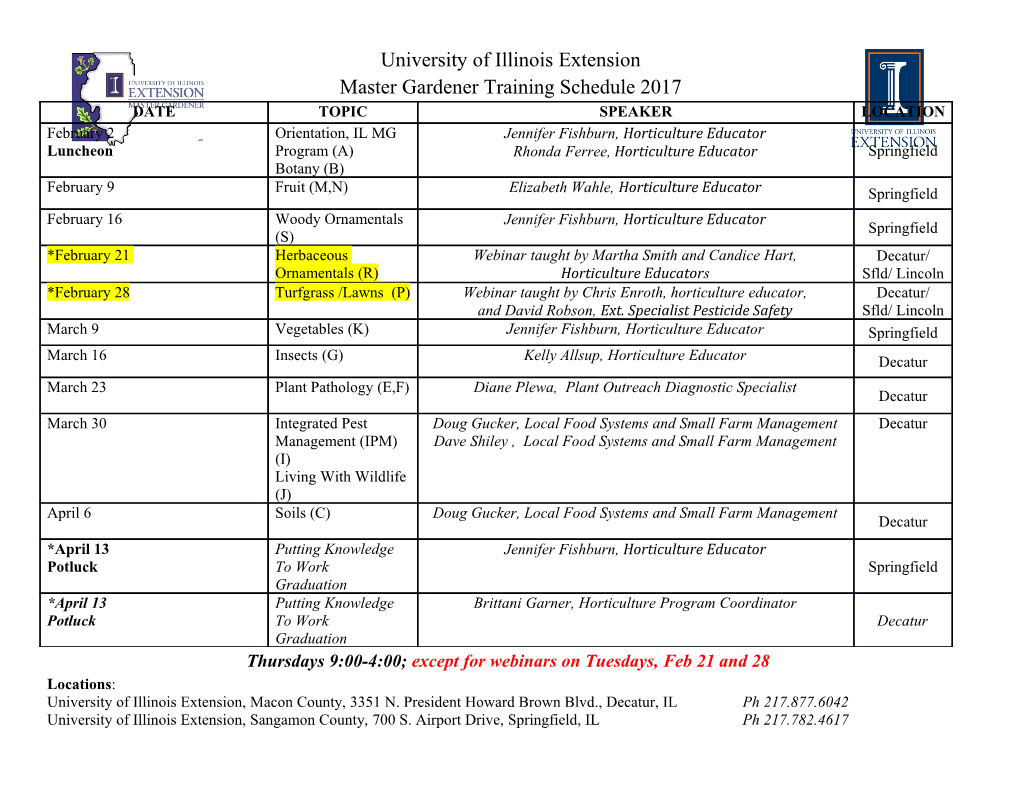
SMART FLUIDS: PROPERTIES AND APPLICATIONS IN VIBRATION CONTROL SYSTEMS Ashwani Kumar1, Bharti2 1 Assistant Professor, Mechanical Engineering Department, Chandigarh College of Engineering and Technology (Degree Wing), Sector-26 Chandigarh, (India) 2Assistant Professor, Applied science Department, Chandigarh University, Gharuan, Punjab (India) ABSTRACT This paper aims to present the properties and application of smart materials which are to be used in vibration control systems. The vibration control can be carried out by three strategies namely passive, semi-active and active control systems. Smart fluids belong to the class of field responsive composites and they have the capacity to undergo significant, reversible and controllable transformations with respect to their material characteristics. These materials have the ability to change from a liquid to a solid almost instantly when subjected to electric or magnetic field. Smart fluid comprises a suspension of micro-meter-sized particles in a dielectric carrier liquid. These smart materials are commonly referred as Magneto-rheological (MR) fluids, Electro-rheological (ER) fluids and Ferro-fluids. MR fluids are the dispersions of fine, magnetically soft, multi- domain particles, in a hydraulic or silicone oil carrier fluid. The apparent yield strength of these fluids can be changed significantly within milliseconds on the application of an external magnetic field. MR fluids possess rheological properties, which can be changed in a controlled way. ER fluid also exhibit changes in their behavior under the influence of an applied electric field. ER fluids are also known as electro-viscous fluids, where rheological effects were used to depict the changes observed in the mechanical properties of the fluid due to electrostatic stress. Ferro-fluids consist of colloidal suspension of mono domain ultra-fine magnetic particles dispersed in either aqueous or non-aqueous liquids. Keywords: Electro-rheological fluids, Ferro-fluids, Magneto-rheological fluids, Semi-active control systems I. INTRODUCTION The vibration control can be carried out by three strategies namely passive, semi-active and active control systems and are shown in Fig. 1. A passive vibration-control unit consists of a resilient member (stiffness) and an energy dissipator (damper) of constant value to absorb vibratory energy of the disturbing vibration and is shown in Fig. 1 (a). This configuration has found to have significant limitations in structural applications where broadband disturbances of highly uncertain nature are encountered. In order to compensate these limitations, active vibration-control systems are designed and utilized. With an additional active force introduced as a part of a suspension unit, u(t), Fig. 1 (b), the vibration-control system is then controlled using different algorithms to 61 | P a g e make it more responsive to sources of disturbance. A combination of active/passive treatment is intended to reduce the amount of external power requirement which is necessary to achieve the desired performance characteristics. In view of the above, if a system is required to be operated over a broadband of frequency range, then it is impossible to operate it with a single choice of stiffness and damping. If the desired response characteristics cannot be obtained, then an active vibration-control system can provide an alternative for such broadband disturbances. However, such active configurations suffer from control-induced instability in addition to the requirement of large control effort. Because of this, it is not in common usage in most of the industrial applications. On the other hand, passive vibration-control systems (especially vibration absorbers) are often hampered by a phenomenon known as „„de-tuning”. Fig. 1 Three versions of vibration-control systems: (a) Passive, (b) Active and (c) Semi-active configuration [1] Semi-active (also known as adaptive-passive) configuration addresses these extreme limitations by effectively integrating a tuning control scheme with tunable passive devices. For this, active force generators are replaced by modulated variable compartments such as variable rate damper and stiffness, Fig. 1 (c). These variable components are referred as „„tunable parameters‟‟ of the vibration-control system, which are re-tailored via a tuning control. Much attention is being paid to these arrangements for their low energy consumption and cost [1]. The behavior of the semi-active devices is often highly nonlinear one, and it poses main challenges in its application. The semi-active control systems are, thus, potentially very good techniques of controlling suspensions and to improve its performance. Recent development of smart materials and structures has led to the design of various semi-active suspension systems. Examples of various semi-active suspension systems include electro-rheological (ER), magneto- rheological (MR) fluid dampers variable orifice dampers controllable friction braces, controllable friction isolators and variable stiffness devices including pneumatic isolators etc. 62 | P a g e Science and technology have made marvelous developments in the design of electronics and machinery using standard materials, which do not have particularly special properties. The range of applications is still wider for special materials whose properties scientists, engineers can manipulate. Some of these materials have the ability to change shape or size simply by adding a little heat or to change from a liquid to a solid almost instantly when placed near a magnet; these materials are commonly called Smart materials/fluids. These materials have multiple properties (chemical, electrical, magnetic, mechanical and thermal) or can transform energy which can be altered or tuned using external fields. Most everyday materials have physical properties, which cannot be significantly altered; for example if oil is heated it will become a little thinner, whereas a smart material with variable may turn from a liquid state which flows easily to a solid. Each individual type of smart material has a different property which can be significantly altered, such as viscosity, volume or conductivity [2]. As each smart material has a different properties which can significantly be altered. Thus, the property that can be altered significantly determines what type of applications a particular smart material can be used most effectively. Varieties of smart materials exist and are still being researched extensively. These include piezoelectric materials, magneto-rheostatic materials, electro-rheostatic materials and shape memory alloys. Some everyday items have already incorporating smart materials and the number of application is still growing steadily. There are some smart fluids; MR fluids, ER fluids and Ferro-fluids which under the influence of applied magnetic/electric fields change their rheological properties [3]. The smart fluids i.e. MR fluids, ER fluids and Ferro-fluids are used in the dampers to achieve the objective of vibration control. These smart fluids have been reviewed in terms of their properties and applications in this paper. II. MAGNETO-RHEOLOGICAL FLUIDS AND ITS PROPERTIES Magneto-rheological (MR) fluids are one of the smart fluids that exhibit dramatic reversible change in its rheological properties (elasticity, plasticity or viscosity) either in solid-like state or free-flowing liquid state depending on the presence or absence of a magnetic field. The discovery of MR fluids is credited to Jacob Rabinow at the US National Bureau of Standard in 1948 [4]. (a) (b) (c) Fig. 2 Activation illustration of MR fluid: (a) No magnetic field applied, (b) Magnetic field just applied and (c) ferrous particles chains formed after full activation of magnetic field Figure 2 shows the activation of the MR fluid. The MR fluids consist of magnetically permeable micron-sized particles dispersed throughout the carrier medium either a polar or non-polar fluid, which influence the viscosity of the fluids under no external magnetic field. The Figure 2(a) shows that the particles in the fluid are randomly 63 | P a g e dispersed in the medium when there is no magnetic field applied. In the presence of a magnetic field, the particles start to move to align themselves along the lines of magnetic flux i.e. Fig.2 (b). Fig.2 (c) shows the formation of chains of the particles thus creating yield strength. As this change in its rheology occurs instantly and also reversible in nature, the MR fluids are attractive for real-time control applications [5]. The magneto-rheological fluids are the suspensions of micron sized, magnetizable particles (mainly iron) suspended in an appropriate carrier liquid such as mineral oil, synthetic oil, water or ethylene glycol. The carrier fluid serves as a dispersed medium and ensures the homogeneity of particles in the fluid. A variety of additives (stabilizers and surfactants) are used to prevent gravitational settling and promote stable particles suspension, enhance lubricity and change initial viscosity of the MR fluids. The stabilizers serve to keep the particles suspended in the fluid, whilst the surfactants are absorbed on the surface of the magnetic particles to enhance the polarization induced in the suspended particles upon the application of a magnetic field. In the absence of an applied field, the MR fluids are reasonably well approximated as Newtonian liquids. For most engineering applications a simple Bingham plastic model is effective at describing the essential, field- dependent
Details
-
File Typepdf
-
Upload Time-
-
Content LanguagesEnglish
-
Upload UserAnonymous/Not logged-in
-
File Pages9 Page
-
File Size-