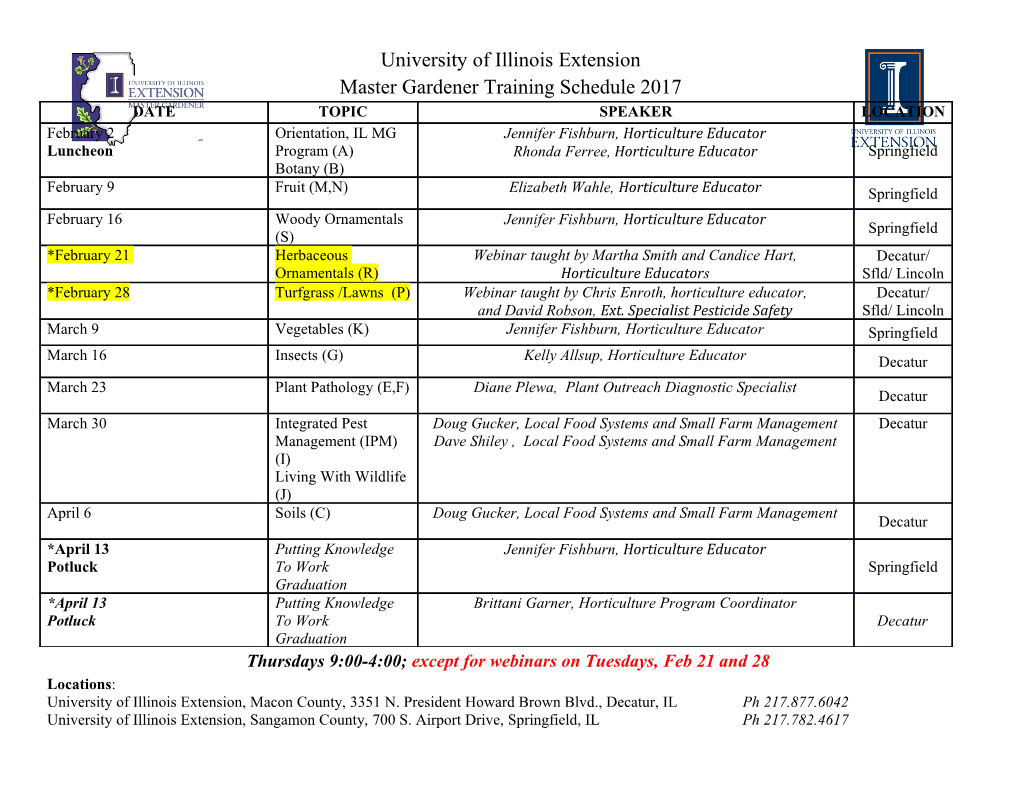
Oriented Strand Board The wood composition boards Jyh-Horng Wu Jyh-Horng Wu The wood composition boards Oriented Strand Board Flakeboard is a term that also includes waferboard WHAT IS OSB? (WB) and oriented strandboard (OSB). Oriented strand board (OSB) is a performance- They are structural panels produced from wafers obtained from logs. rated structural wood-based panel engineered for uniformity, strength, versatility The first waferboard plant was opened in 1963 by and workability (可加工性). MacMillan Bloedel in Canada. Aspen was the raw material, and the wafers were randomly oriented. It is utilized internationally in a wide array of In the late 1980s, most wafers were oriented, applications including residential and resulting in oriented waferboard (OWB). commercial construction and renovation, packaging/crating, furniture and shelving, and Long and narrow strands are now used in OSB, which do-it-yourself projects. typically have 3 or 5 layers. Jyh-Horng Wu Jyh-Horng Wu 1 Oriented Strand Board Oriented Strand Board WHAT IS OSB? Because it is engineered, OSB can be custom manufactured to meet specific requirements in thickness, density, panel size, surface texture, strength and rigidity. This engineering process makes OSB the most widely accepted and preferred structural panel among architects, specifiers and contractors. Jyh-Horng Wu Jyh-Horng Wu Oriented Strand Board Oriented Strand Board Jyh-Horng Wu Jyh-Horng Wu 2 Oriented Strand Board Oriented Strand Board In fact, in many areas of North America, OSB has virtually replaced other panels in new residential construction. Today, all model building codes in the U.S. and Canada recognize OSB panels for the same uses as plywood. Since the early 1980s, the North American OSB industry has experienced a period of tremendous growth. Jyh-Horng Wu Jyh-Horng Wu Oriented Strand Board Oriented Strand Board One limitation with OSB is edge swelling. Although the edges are coated during transport, subsequent cutting causes limitations in high humidity applications. Jyh-Horng Wu Jyh-Horng Wu 3 Oriented Strand Board Oriented Strand Board One advantage, however, is that OSB is more OSB is increasing its market share as a result of its lower cost as compared with plywood. consistent than plywood. lower cost (Soft spots caused by overlapping knots do not OSB is now used for about 70 percent of all floor, exist, nor do knot holes at edges, and delamination wall and roof sheathing in North America. does not take place) Since one OSB sheet may consist of 50 strands, properties are homogeneous, and there are only minor stiffness variations with location in the panel. Through-thickness shear strength is approximately twice as high with OSB. Jyh-Horng Wu Jyh-Horng Wu Structural Panels Structural Panels OSB production OSB production Log Sorting After harvest, whole logs are hauled to the mill's wood yard (貯材場 ), then sorted. Jackladder Logs are soaked, to remove ice and prepare wood for stranding, then sent up the jackladder. Jyh-Horng Wu Jyh-Horng Wu 4 Structural Panels Structural Panels OSB production Debarking The principal reasons used to justify debarking are: Debarking The principal reasons used to justify debarking are: Logs are run through the 1. To remove bark from wood that is to be chipped debarker to remove bark. for board use since any substantial quantity in the Bark is later used as fuel in chips is detrimental to board quality. the mill's energy supply. 2. To prolong the life of cutting tools in the sawmill. The sand, grit, and rocks in bark cause dulling and Stranding tool wear. The strands are cut from 3. To reduce debris in the mill that otherwise would whole logs into precise require more frequent cleanup and higher dimensions of up to six maintenance. inches long. 4. To enable the sawyer to see and evaluate the log for breakdown. Jyh-Horng Wu Jyh-Horng Wu Structural Panels Structural Panels Debarking Debarking Cambio debarker Mechanical ring debarker Jyh-Horng Wu Jyh-Horng Wu 5 Structural Panels Structural Panels Debarking Debarking Rosserhead debarker Drum debarker Jyh-Horng Wu Jyh-Horng Wu Structural Panels Structural Panels Debarking OSB production Hydraulic debarker Debarking Logs are run through the debarker to remove bark. Bark is later used as fuel in the mill's energy supply. Stranding The strands are cut from whole logs into precise dimensions of up to six inches long. Jyh-Horng Wu Jyh-Horng Wu 6 Structural Panels Structural Panels OSB production OSB production Blending Wet Bins Strands are blended with resin Strands are deposited binders and a small amount of into wet bins. wax, which improves the efficiency of the resin binder and enhances the panel's resistance to moisture and water absorption. Drying Strands are then dried Forming Line until the appropriate Strands go through the forming moisture content is line where cross-directional reached. layers are formed. Jyh-Horng Wu Jyh-Horng Wu Structural Panels Structural Panels OSB production OSB production Finishing Line Pressing Panels are cooled, cut to size, grade Layers of cross-directional strands are stamped, stacked in bundles and edge pressed under intense heat and coated. All graded panels bear a pressure to form a rigid, dense structural mandatory certification agency stamp, panel of oriented strand board (OSB). plus the SBA logo if applicable. Presses are primarily multiple opening allowing 8 to 16 master panels to be Shipping pressed in one operation for increased Finally, the panels are ready to be efficiency. loaded and shipped to destinations Since 1997, continuous presses around the world. Panels can be producing a ribbon of OSB ordered smooth sanded for special uses commenced operation on certain sites. or with tongue and groove edges. Jyh-Horng Wu Jyh-Horng Wu 7 Structural Panels Oriented Strand Board OSB production Cutting the strands Log Hauling Debarking and Sorting Jackladder It advances into side of clamped bolts cutting long strands parallel to the long axis Blending Wet Bins Drying Stranding Strand length of 15 cm common and four of these can be produced by the 60 cm long knife Thickness is 0.75 mm (provides a reasonable balance between board properties) Width 2 to 5 cm Forming Line Pressing Finishing Line Shipping Jyh-Horng Wu Jyh-Horng Wu Oriented Strand Board Oriented Strand Board Cutting the strands Cutting the strands A commercial disk strander Strands Jyh-Horng Wu Jyh-Horng Wu 8 Oriented Strand Board Oriented Strand Board Drying of the strands Blending and forming Blending For good adhesion, MC must be 2 to 6% Rotary (like tumble clothes dryer) and flat Addition of wax, resin adhesive, is called screen driers are used blending Flat screen driers cause less strand breakage, Wax 0.25 to 2% to add water repellency retain better strand surface quality Resin 2 to 5 % by weight Hot air enters the dryer (540oC) Resin applied by spray – like “spot welding” Evaporating moisture cools the air Blending of surface and core furnish often Exiting temperatures are lower (200oC) done separately Jyh-Horng Wu Jyh-Horng Wu Oriented Strand Board Oriented Strand Board Blending and forming Blending and forming Blending Forming The resin is applied in a drum that rotates Process of depositing strands onto surface to form a mat is called “forming” A “fog” of resin coats the strands Try to make it uniform Traditionally have used liquid resins To align the strands parallel to the belt they Modern technology allows use of powder drop through series of spinning discs (like farmers harrow) onto belt below adhesives, which are cheaper to ship, do not add water to the strand, increases resin To align strands perpendicular to the belt shelf life. they drop onto a series of spinning discs (like paddle wheel) where they self align and land on the belt Jyh-Horng Wu Jyh-Horng Wu 9 Oriented Strand Board Oriented Strand Board Blending and forming Blending and forming Formation of the mat Forming Common to use four forming heads First aligns strands 25% parallel Next two deposit the flakes 50 % perpendicular Fourth deposits strands 25% parallel Final board thickness, dimension and density determined during forming To produce a 12.5 mm thick panel, loose mat is 100 mm thick Jyh-Horng Wu Jyh-Horng Wu Oriented Strand Board Oriented Strand Board Blending and forming Pressing OSB Lay-up In batch processed OSB loose strand mat is transferred to press charger Multi-opening presses used 3.66 x 12.2 m platen size and can produce sheets 2.74 x 7.62 m Platens conduct heat to mat (175 to 205oC) Press times are generally between 3 and 6 min depending on board density and thickness Conductive heat transfer is approximately a function of the square of panel distance (Press time for 38 mm OSB is 4x 19 mm OSB) Jyh-Horng Wu Jyh-Horng Wu 10 Oriented Strand Board Oriented Strand Board Pressing Pressing Long, hot press cycles damage board surfaces and substantially impede production volumes To accelerate the cure of thicker mats, both high-frequency curing and steam injection are sometimes used Pressures 4,800 to 5,500 kPa After pressing, panels are hot stacked in bulk for about twenty-four hours to assure complete adhesive cur Jyh-Horng Wu Jyh-Horng Wu Oriented Strand Board Oriented Strand Board Adhesives Adhesives Only thermosetting resins used for structural panels Phenol-formaldehyde (PF) is primary resin in North America used for plywood and OSB Diphenylmethane diisocyanate (MDI) is used for OSB Both form water proof bonding necessary for structural panels Jyh-Horng Wu Jyh-Horng Wu 11 Oriented Strand Board Oriented Strand Board Adhesives Adhesives Both derived from petroleum industry Plywood resins are not pure Cost of PF is 25% of MDI and is available in powdered form Includes fillers and extenders MDI is clear, and does not contain any water Extenders have adhesive value (e.g.
Details
-
File Typepdf
-
Upload Time-
-
Content LanguagesEnglish
-
Upload UserAnonymous/Not logged-in
-
File Pages14 Page
-
File Size-