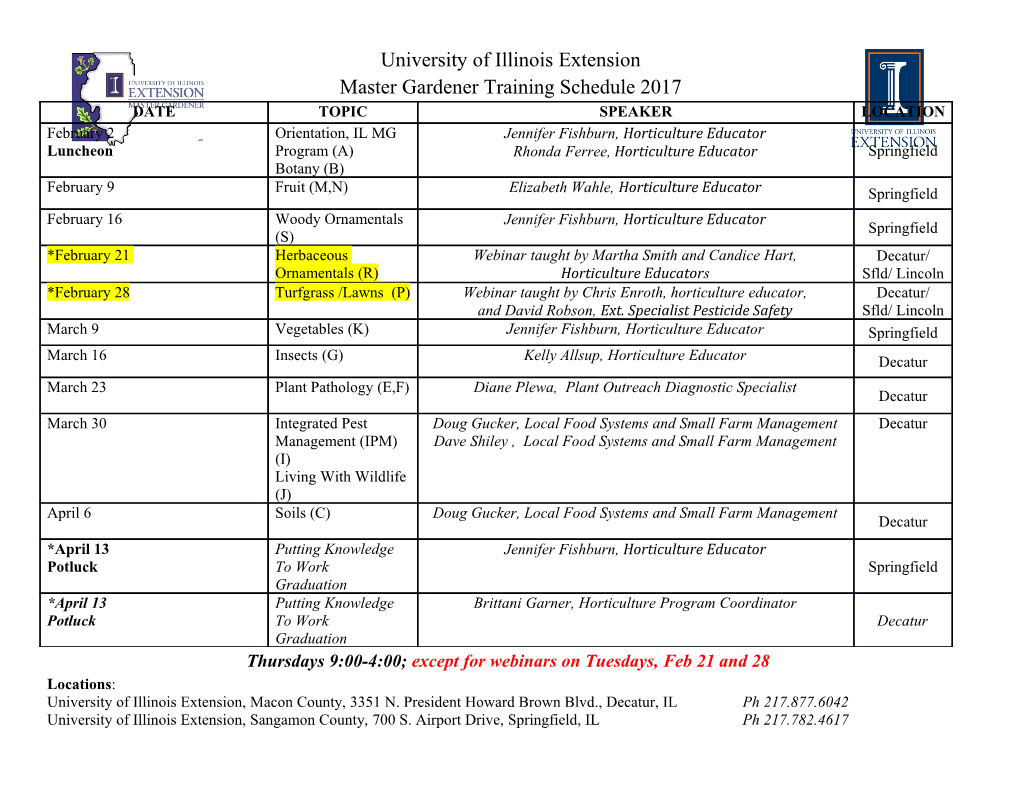
HIGH PERFORMANCE NONWOVENS IN TECHNICAL TEXTILE APPLICATIONS CHRISTOPHER OLARINDE OGUNLEYE (204071852) 2013 HIGH PERFORMANCE NONWOVENS IN TECHNICAL TEXTILE APPLICATIONS By Christopher Olarinde Ogunleye Submitted in partial fulfilment of the requirements for the degree of Philosophiae Doctor in the Faculty of Science at the Nelson Mandela Metropolitan University December, 2013 Promoter: Prof. Rajesh Anandjiwala Co-Promoter: Prof. Lawrance Hunter DECLARATION I, Christopher Olarinde Ogunleye (student No. 204071852) hereby declare that the thesis for Philosophiae Doctor (PhD) in Textile Science is my own work and that it has not previously been submitted for assessment or completion of any postgraduate qualification to another University or for another qualification. Christopher Olarinde Ogunleye. i ACKNOWLEDGEMENTS The author would like to express his profound gratitude to the promoter, Professor Rajesh Anandjiwala and my co-promoter, Professor Lawrance Hunter for their continous support and guidance during my studies. I also appreciate the support given by the entire staff of CSIR and their hospitality. Thank you all!! I am also deeply indebted to Yaba College of Technology, Lagos, Nigeria for releasing me to undertake this study. I am also grateful to Nelson Mandela Metropolitan University for their financial support during my study. The author would also like to thank the technical team of Nonwoven division for their generous contribution and assistance during the project. I also appreciate the patience of my wife, Grace, and my children. Through your support, encouragement and prayers, I am living my dreams. ii ABSTRACT The aim of this research was to establish the optimum processing conditions and parameters for producing nonwoven fabrics best suited for application in disposable and protective wear for surgical gowns, drapes and laboratory coats. Carded and crosslapped webs, of three basic weights (80, 120, and 150g/m2), from greige (unscoured and unbleached) cotton, viscose and polyester fibres, were hydroentangled, using three different waterjet pressures (60, 100 and 120 bars), on a Fleissner Aquajet hydroentanglement machine. An antibacterial agent (Ruco-Coat FC 9005) and a fluorochemical water repellent agent (Ruco Bac-AGP), were applied in one bath using the pad-dry-cure technique, to impart both antibacterial and water repellent properties to the fabrics, SEM photomicrographs indicating that the finished polymers were evenly dispersed on the fabric surface. The effect of waterjet pressure, fabric weight and type and treatment on the structure of the nonwoven produced, was evaluated by measuring the relevant characteristics of the fabrics. As expected, there was an interrelationship between fabric weight, thickness, and density, the fabric thickness and mass density increasing with fabric weight. An increase in waterjet pressure decreased the fabric thickness and increased the fabric density. The water repellent and antibacterial treatment increased the fabric weight and thickness. The antimicrobial activity of the fabrics was assessed by determining the percentage reduction in Staphylococcus aureus and Escherichia coli bacteria population. The maximum percent reduction at 24hrs contact time for both bacteria ranged from 99.5 to 99.6 % for all the fabric types. The standard spray test ratings for the three treated fabrics ranged from 80-90%, whereas that of the untreated water repellent fabric was zero, while the contact angles for all the fabric types exceeded 90 degrees, indicating good resistance to wetting. It was found that the tensile iii strength of the fabric in the cross-machine direction was higher than that in the machine direction, for both the treated and untreated fabrics, with the tensile strengths in both the MD and CD of the treated fabrics were greater than that of the untreated fabrics, the reverse being true for the extension at break. An increase in waterjet pressure increased the tensile strength but decreased the extension at break, for both the treated and untreated fabrics. The finishing treatment decreased the mean pore size of all the fabrics, the mean pore size decreasing with an increase in fabric weight and waterjet pressure. An increase in waterjet pressure and fabric weight decreased the air and water vapour permeability, as did the finishing treatment, although the differences were not always statistically significant. The polyester fabrics had the highest water and air permeability. Hence low weight fabrics of 80 g/m2, which were hydroentangled at low water jet pressures of 60 bars, were suitable for use in this study due to their higher air and water vapour permeability as well as higher pore size distribution. These group of fabrics thus meet the requirements for surgical gowns, drapes, nurses’ uniforms and laboratory coats. Keywords: Antibacterial, water repellency, nonwovens, hydroentanglement, waterjet pressure. iv CONTENTS DECLARATION .....................................................................Error! Bookmark not defined. ACKNOWLEDGEMENTS ...................................................................................................... ii ABSTRACT ............................................................................................................................. iii CONTENTS .............................................................................................................................. v 1 INTRODUCTION ................................................................................................................. 1 1.1 NONWOVEN ................................................................................................................. 1 1.2 NONWOVENS AND TECHNICAL TEXTILES .................................................... 2 1.3 NONWOVEN MANUFACTURING PROCESS........................................................... 4 1.3.1 Web formation .................................................................................................... 4 1.3.2 Fibre Bonding (consolidation) ................................................................................. 6 1.3.3 Nonwovens in the medical industry ......................................................................... 9 REFERENCES .................................................................................................................. 11 2.LITERATURE REVIEW .................................................................................................... 13 2.1 INTRODUCTION ........................................................................................................ 13 2.2 DEMAND FOR PROTECTIVE CLOTHING FOR HEALTHCARE WORKERS .... 14 2.2.1 Infection control barrier fabrics for healthcare workers ........................................ 15 2.2.2 Mechanisms of infection transmission ................................................................... 17 2.2.3. Criteria requirements for protective clothing .................................................... 18 2.2.4 Comfort of protective garments ............................................................................. 18 2.2.5 Classifications of surgical gowns, drapes and laboratory coats ............................. 19 2.2.6 Characteristics of surgical gowns and drapes ........................................................ 20 2.3.THE IMPACT OF NANOTECHNOLOGY ON PROTECTIVE GARMENTS ......... 23 2.4 FIBRES FOR NONWOVENS ..................................................................................... 24 2.4.1 Fibres for hydroentanglement ................................................................................ 25 v 2.5 THE HYDROENTANGLEMENT PROCESS ............................................................. 27 2.5.1 Introduction ............................................................................................................ 27 2.5.2 Mechanism of hydroentangling ........................................................................ 28 2.5.3 Influence of the nozzle on hydroentanglement ...................................................... 31 2.5.4 The influence of specific energy ............................................................................ 33 2.5.5 The effect of production speed .............................................................................. 35 2.5.6 The effect of the design of the fibre support screen ............................................... 35 2.6 APPLICATION OF HYDROENTANGLEMENT (SPUNLACED) FABRICS. ........ 38 2.6.1 Latest advances in hydroentanglement technology ............................................... 39 2.7 FINISHING OF NONWOVEN FABRICS .................................................................. 40 2.7.1 Mechanical finishing .............................................................................................. 41 2.7.1.1 Classification of mechanical finishes applied to nonwoven fabrics .................. 41 2.7.1.2 Shrinkage ............................................................................................................ 41 2.7.1.3 Wrenching ........................................................................................................... 42 2.7.1.4 Creeping .............................................................................................................. 43 2.7.1.5 Crabbing and Calendering .................................................................................. 44 2.7.1.6 Perforating and Slitting ......................................................................................
Details
-
File Typepdf
-
Upload Time-
-
Content LanguagesEnglish
-
Upload UserAnonymous/Not logged-in
-
File Pages256 Page
-
File Size-