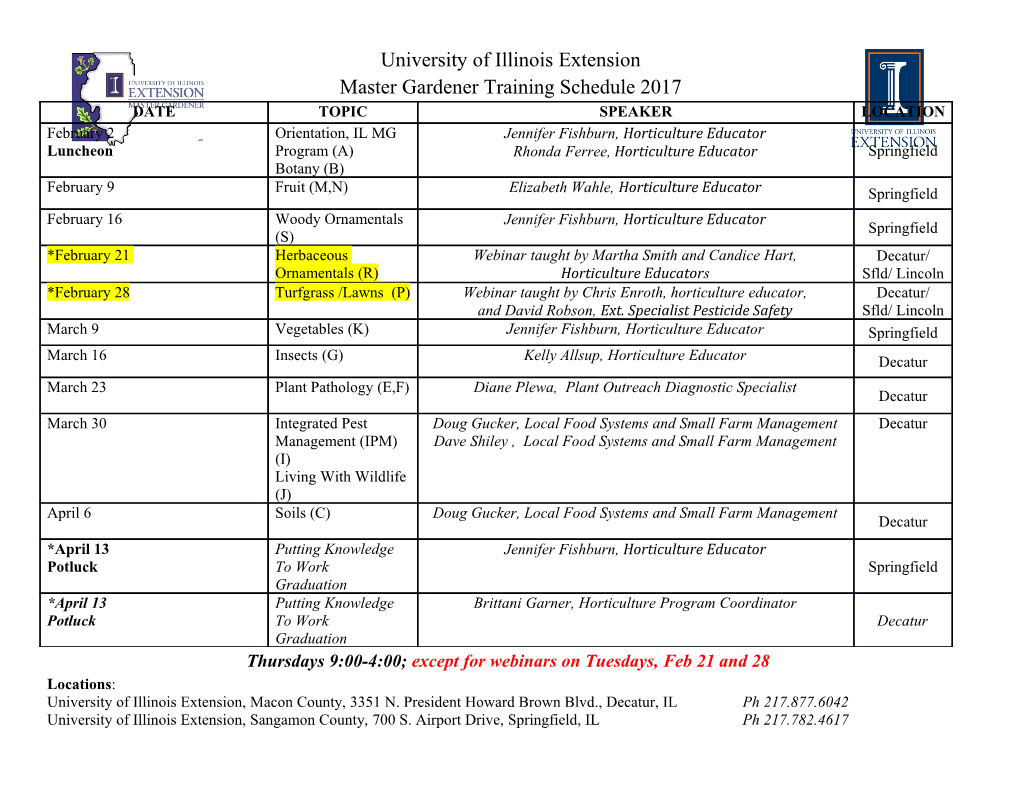
February 13, 2019 MASTER THESIS FRAMEWORK FOR COMPARING AND OPTIMIZING OF FULLY ACTUATED MULTIROTOR UAVS Jelmer Goerres (s1381644) Faculty of Engineering Technology (CTW) Mechanics of Solids, Surfaces and Systems (MS3) Exam committee: Prof. Dr. Ir. A. de Boer R.A.M. Rashad Hashem MSc Dr. Ir. R.G.K.M. Aarts Dr. Ir. J.B.C. Engelen Document number: Mechanics of Solids, Surfaces and Systems (MS3)– ET.18/TM-5843 Abstract Multirotor UAVs (unmanned aerial vehicles) have seen a great growth in popularity in the past years. However the application of these UAVs has been limited to simple flying tasks. For these tasks the optimal UAV design is very straightforward: an in-plane rotor configuration with parallel rotors. Although this design is inherently underactuated, it is able to fly in all required directions by tilting itself towards the desired direction. The application of multirotor UAVs could be expanded when full actuation of the six degree’s of freedom (DoFs) could be achieved by the UAV. These applications include: object ma- nipulation, assembly, contact inspection tasks, etcetera. To achieve full actuation, the UAV needs to be able to produce thrust in all directions and the thrust generated by only parallel rotors will no longer suffice. The optimal rotor configuration is no longer straightforward, but depends on the requirements of the application. In order to find the optimal rotor configuration for any application, a framework is presented that compares available fully actuated UAV concepts with a set of qualitative criteria, such as: design complexity and flying stability, as well as a set of quantitative criteria that compare the wrench and accelerations of the concepts. These criteria are general and are used to evaluate the strengths and weaknesses of a number of concepts found in literature. In this way the framework can be applied for any application, as a first step to determine the optimal rotor configuration. To demonstrate the usability of the framework, two UAVs have been developed for two different applications that require full actuation. The first application is a large crop spraying UAV. Due to the great width and low flying height, this UAV can only roll very little before colliding with the ground. To be able to withstand side-wind dis- turbance, this UAV needs to be able to translate in sideways direction without changing orientation, so horizontal actuation is required. The optimization of this UAV yielded a UAV with optimized rotor positions and a number of rotor tilt configurations that can be applied for different wind speeds. This optimization shows how the framework can be used to create a multirotor design with very specific re- quirements and limitations. The second application is a human interacting UAV. This UAV needs to be omnidirectional to re- sponse to any wrench applied to it by humans. The optimization of the rotor configuration of this UAV has been done for six, eight and ten rotors, using a scalar measure for the entire achievable accelera- tion called the dynamic manoeuvrability. The optimization yielded a number of solutions for coupled and decoupled dynamic manoeuvrability, as well as a solution with high thrust efficiency. These solutions have been compared extensively, resulting in a UAV with high flying efficiency and high omnidirectional accelerations, as well as a better insight in the applicability of dynamic manoeuvrability in the optimiza- tion of UAVs. The optimization for the crop spraying UAV and the the human interacting UAV shows that the frame- work can be applied for a wide range of applications. Page 2 Contents 1 Introduction 6 1.1 Problem description . .7 1.2 Contributions . .7 1.3 Organization . .7 2 Background 9 2.1 Coordinate Frame . .9 2.2 Rotor Configuration . 10 2.2.1 Cant and Dihedral Angle . 10 2.3 Static Wrench Analysis . 10 2.3.1 Rotor Thrust generation . 11 2.3.2 Redundancy . 11 2.3.3 Omnidirectional . 11 2.4 Accelerations . 11 2.5 Variable Tilt Rotors . 12 2.5.1 Manoeuvrability . 13 2.5.2 Decoupling . 14 2.5.3 Unit . 15 2.6 Airflow Interference . 15 3 Fully Actuated UAV Concepts 17 3.1 Fully Actuated UAV Categories . 17 3.1.1 Fixed Tilt UAVs . 17 3.1.2 Variable Tilt UAVs . 17 3.2 Fixed Tilt Concepts . 18 3.2.1 Quadrotor with four horizontal rotors . 18 3.2.2 Hexarotor with Canted Rotors . 19 3.2.3 Hexarotor with canted and dihedral rotors . 20 3.2.4 Coaxial Hexagon with Twelve Canted Rotors . 21 3.2.5 Double Tetrahedron Hexarotor . 21 3.2.6 Heptarotor with Minimized Frame . 22 3.2.7 Heptarotor with Maximized Wrench . 23 3.2.8 Octorotor Cube . 23 3.2.9 Octorotor Beam . 24 3.3 Variable Tilt Concepts . 24 3.3.1 Trirotor with One Horizontal Rotor . 25 3.3.2 Quadrotor with Variable Cant Rotors . 25 3.3.3 Quadrotor with Variable Dihedral Rotors . 26 3.3.4 Quadrotor with Variable Cant and Dihedral Rotors . 27 3.3.5 Quadrotor with Coupled Variable Cant and Dihedral Rotors . 27 3.3.6 Hexarotor with Variable Cant Rotors . 28 3.3.7 Hexarotor with Coupled Variable Cant Rotors . 28 3.3.8 Ducted Pentarotor with Two Coaxial Rotors and Three Variable Dihedral Rotors . 29 4 Criteria for Comparing Fully Actuated UAVs 30 4.1 Qualitative Criteria . 30 4.1.1 Flying stability . 30 4.1.2 Design complexity . 30 4.1.3 Downscaling Ability . 30 4.1.4 Upscaling Ability . 31 4.1.5 Redundancy . 31 4.1.6 Costs . 31 4.2 Quantitative Criteria . 31 Page 3 4.2.1 Static Comparison . 31 4.2.2 Dynamic Comparison . 33 5 Comparison of Fully Actuated UAVs 36 5.1 Abbreviations . 36 5.2 Comparison Limitations . 37 5.3 Fixed Tilt versus Variable Tilt Concepts . 37 5.4 Preliminary Design Considerations . 37 5.5 Comparison of Fixed Tilt Concepts . 38 5.5.1 Qualitative Comparison . 38 5.5.2 Static Comparison . 40 5.5.3 Dynamic Comparison . 42 5.5.4 Conclusion . 45 5.6 Variable Tilt Concepts . 46 5.6.1 Qualitative Comparison . 46 5.6.2 Static Comparison . 48 5.6.3 Dynamic Comparison . 49 5.6.4 Conclusion . 52 6 Application of Fully Actuated UAVs: Crop Spraying 53 6.1 Traditional Crop Spraying Methods . 53 6.2 Currently Available Crop Spraying UAVs . 54 6.3 Requirements . 55 6.4 Preliminary Design Consideration . 56 6.4.1 Rotor Type . 56 6.4.2 Power Source . 56 6.4.3 Pesticide Storage . 56 6.5 Concept Choice . 56 6.5.1 Proposed Concept . 57 6.5.2 Comparison of Proposed Concept with the Framework . 57 6.6 Pesticide Atomization . 59 6.7 Optimization . 59 6.7.1 Rotor Configuration . 60 6.7.2 Design Simplifications . 60 6.7.3 Objective Function . ..
Details
-
File Typepdf
-
Upload Time-
-
Content LanguagesEnglish
-
Upload UserAnonymous/Not logged-in
-
File Pages97 Page
-
File Size-