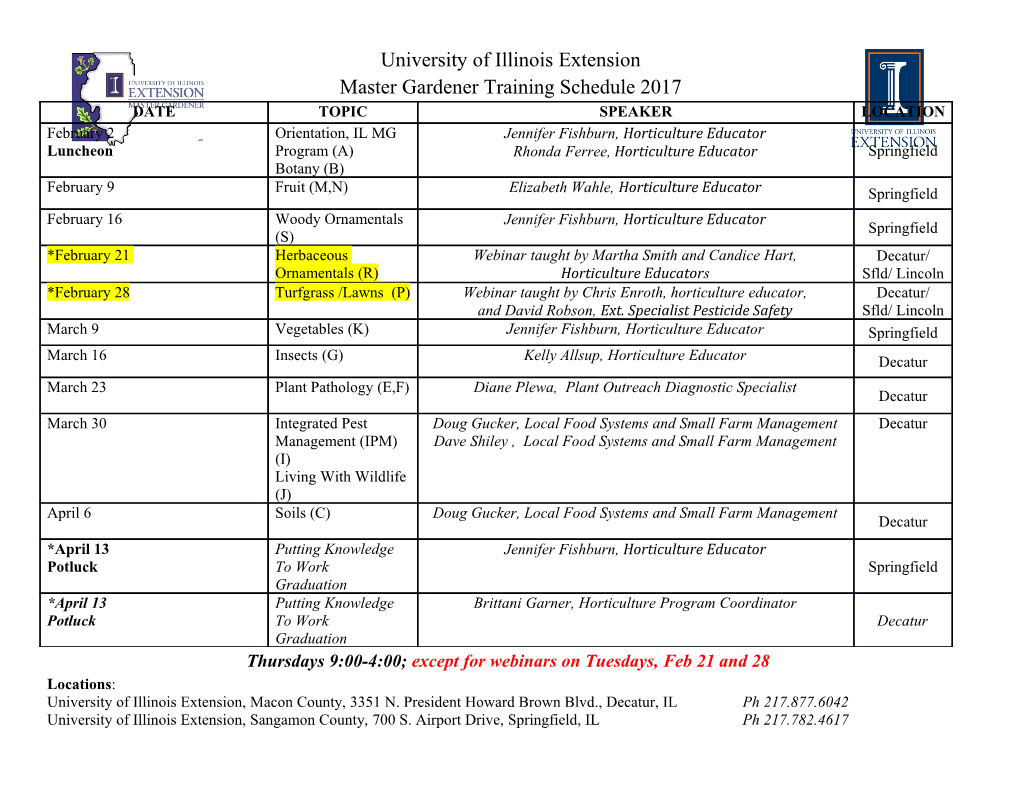
Syngas Purification in Based Ammonia/Urea Plants A new syngas purification process for gasification-based ammonia/urea plants using a UOP Selexol/PSA process sequence is presented. This new process can be used in place of the conventional Rectisol/Nitrogen Wash process. Capital and operating costs and plant performance for a typical coal-based ammonia plant using these two different processes are compared. These results also apply to syngas production from other feedstocks such as coke and residual oil, and other plant sizes. John Y. Mak and David Heaven Fluor-Daniel, Irvine, CA 92698 Introduction study apply to various feedstocks (coal, petroleum coke, and refinery heavy residues) and to different easibility studies of a coal-to-ammonia/urea plant sizes and gasification technologies. fertilizer complex demonstrated that the use of Independent of this work, a 1,000 MTD Fthe UOP Selexol/PSA process technology for ammonia/urea fertilizer based upon Texaco gasifica- synthesis gas purification is superior to the conven- tion of refinery petroleum coke using the UOP tional route of Rectisol/Nitrogen Wash. To completely Selexol/PSA technology for synthesis gas purification evaluate these two gas processing routes, the differ- is currently under engineering/construction in North ences in capital and operating costs, the consequences America. The low value of refinery residue feedstocks of varying operating parameters, and the impacts on and this gasification/syngas purification route to fertil- surrounding units were investigated. Four cases were izer can be competitive with the conventional natural evaluated using Texaco Quench Gasification technology gas reforming processes. to gasify coal, considering the additional CÜ2 co-pro- duction for urea manufacture. Material balances were Case Studies developed for each case on the basis of producing 2,000 MTD of ammonia and, as an option, 1,475 This section describes the fertilizer complex config- MTD of CO2 for urea manufacture. Capital and oper- urations for the four cases of syngas production. ating costs were developed for the entire plant so that Overall block flow diagrams, heat and material bal- the overall effects of the two different synthesis gas ances and process flow diagrams are shown in the sub- purification technology routes could be fully evaluat- sequent sections. The gasification complex is designed ed. The results show that the Selexol/PSA process is to produce a syngas that is further processed to pro- lower in both capital and operating costs than the duce 2,000 MTD ammonia. Illinois No. 6 coal was Rectisol/Nitrogen Wash process. The results of this used as the feed basis for these cases. AMMONIA TECHNICAL MANUAL 319 1999 Case 1: Selexol/PSA without CO2 Production The CO in the syngas from the gasification unit is converted to hydrogen using two stages of sour shift Case 1 is the base case to which all other configura- reactors via the water-shift reaction. tions are compared. This case uses Selexol/PSA for CO + H O->H + CO acid gas removal and hydrogen purification. The coal 2 2 2 feed to the plant is 2,593 MID to produce 2,000 MTD Since the raw syngas has been saturated with water of ammonia. The overall block flow diagram for this in the scrubbing process, it contains sufficient steam case is depicted in Figure 1. The overall heat and for the shift reaction and no additional steam is material balance is summarized in Table 1. The required. The heat contained hi the reactor effluent is process units are briefly described below. used to generate various levels of steam. A single train Air Separation Unit (2,340 MTD) is A side reaction of the CO shift catalyst converts used to supply high-pressure oxygen at 99.5% purity most of the COS to CO2 and H2S by the catalytic to the gasification unit plus low-pressure oxygen to the hydrolysis reaction, which also occurs in the presence oxygen blown Claus Unit. The use of oxygen in the of steam. Claus Unit reduces the sulfur plant size and improves COS + H2O -> H2S+ CO2 its operating efficiency. The Air Separation Unit also The syngas is then fed to the UOP Selexol unit that supplies high-pressure gaseous nitrogen which is is designed to remove 99.5% of the H S and to pro- mixed with the hydrogen from the Hydrogen 2 duce a CO2 stream suitable for urea manufacture. Recovery Unit (PSA) to make up a stoichiometric feed The process flow diagram for the Selexol unit is to the ammonia plant. The PSA unit, designed by depicted in Figure 2. UOP, uses low-pressure nitrogen for purging, resulting in a substantial improvement in hydrogen recovery. Selexol Unit Coal from storage is conveyed to the coal grinding and slurry preparation system at a rate of 2,593 MTD. Coal The HP Absorber is designed with an inter-cooler and recycle carbon is wet ground with water to produce for controlling the absorption temperature and maxi- a coal-slurry. The slurry and a 99.5% purity oxygen mizing the acid gas loading of the rich solvent. This stream from the air separation plant are fed to the Texaco exchanger results in reducing the lean solvent circula- Quench Gasifier operating at 1,000 psig for the produc- tion. The Selexol solvent reduces the H S content of tion of a raw syngas stream. The particulate-laden 2 the svngas from 0.92 mol. % to 18 ppmv while also quench and scrubber water stream is further treated for removing about 50% of COS. soot removal and recovery of unconverted carbon. Table 1. Case 1: Material Balance for Selexol/PSA Without CO2 Production Stream Number 1 2 3 4 5 6 7 8 9 10 11 12 13 Description Coal Food Coal Slimy Oxygen To Raw Syngas Scrubbed Shifted Sulfur From Treated Tola! Purge LP Nitrogen HP Nitrogen Hydrogen Syngas To ToGaaftara Gaslftets To Syngas Syngas Syngas To Oxygen Syngas To Gas FromASU FromASU From PSA Ammonia Scrubbing Setexol Claus Unit PSA Synthesis Component Ib/hr Mir Lbmol/hr Lbmol/hr Lbmol/hr Lbmol/hr Lbmol/hr Lbmol/hr Lbmol/hr LbmoMir Lbmol/hr Lbmol/hr Lbmol/hr CO 9,722 9,722 445 444 445 Hydrogen 8,065 8,065 17,330 17,315 1.053 16,276 16,276 CO2 3,751 3,751 12,941 9,522 12,941 Methane 22 22 22 22 19 3 3 Argon 25 33 33 33 33 22 12 12 Nitrogen 9 97 97 97 97 4,168 4,240 5,216 169 5,385 H2S 286 286 293 1 1 COS 7 7 0 0 0 H20 145,973 5,777 34,169 65 64 64 Oxygen 6,685 Sulfur 293 Coal 238,167 238,167 Total 238,167 384,140 6.718 27,761 56,153 31,228 293 27,498 18,714 4,240 5,216 16,460 21,876 MolWt 32 21 19 20 32 17 36 28 28 2 9 AMMONIA TECHNICAL MANUAL 320 1999 Figure 1. Case 1 (base case): coal to ammonia complex selexol case without C(>2 production. The rich Selexol solvent from the HP Absorber is let PSA Unit down to 450 psia, and the flash gas is recycled back to the absorber so that its hydrogen content is recovered. The PSA unit is designed to purify the treated gas The solvent is then heated in the lean/rich exchangers to from the Selexol unit and produce 99% purity hydrogen 244°F and is then flashed to 200 psia. The LP flash for the ammonia plant. This PSA unit is a new design vapor is sent to the H2S Concentrator, which is designed offered by UOP that improves the overall hydrogen to reject the bulk of the CO2 thereby concentrating the recovery in the gasification-to-ammonia plants. H2S content of the acid gas feed to the Claus unit The PSA unit uses conventional multibed adsorp- The H2S Concentrator uses a pre-saturator to pro- tion/desorption cycle design, with nitrogen being used duce a CO2 stream with a very low H2S content. The for purging the bed in the desorption cycle. lean Selexol is first mixed with the overhead vapor Conventional design uses hydrogen for purging during and is cooled to 0°F in an overhead heat exchanger. the desorption cycle, which results in loss of hydrogen Most of the CO2 absorption occurs in this exchanger in the purge gas. In a gasification/ammonia plant, very and the solvent becomes saturated with CO2. The CO2 pure nitrogen is available from the Air Separation saturated liquid is pumped back to the column for H2S Plant and purging the beds using nitrogen improves absorption. the overall hydrogen recovery, typically from 88%-90% to 92%-94%. The tail gas from the PSA unit contains a substantial amount of nitrogen and AMMONIA TECHNICAL MANUAL 321 1999 Table 2. Case 2: Material Balance for Selexol/PSA With CO2 Production Stream Number 1 2 3 4 5 6 7 8 9 10 11 12 13 14 15 Description Coal Fond Coal Sluny Oxygen To Raw Scrubbed Shifted SuftirFrom Treated Total Purg» LP tttragin HP Hydrogen Syngas To LP(Qas) HP(Uqu«i) ToGasHai» QasHera Syngas To Syngas Syngaa To Oxygan Syngas To Gas Fran ASU Nitrogen From PSA Ammonia COZTo COZTo Syngas Seta) Claus Unil PSA FromASU SynUunlt UnaPtM* Una Plant Scrubbing COMPONENT Ib/tu Ib/hr Lbmot/hr Lbmol/hr Lbmol/hr Lbmol/hr Lbmol/hr Lbmol/hr LbrnoVhr LbmoVhr Lbmol/hr LbmoWir Lbmol/hr LbrnoVhr Lbmol/hr CO 9,722 9,722 445 444 444 Hydrogen 8.065 8,065 17,330 17,315 1,039 18,276 18.276 CO2 3,751 3.751 12.S41 9,522 9,861 1,232 1,848 Methane 22 22 22 22 19 3 3 Arg«) 25 33 33 33 33 22 12 12 0 0 Nitrogen S 97 97 87 97 4,168 4,240 5,216 169 5,385 0 0 H2S 286 286 293 1 1 COS 7 7 0 0 0 H20 145,973 5,777 34,169 65 64 64 Oxygen 6,685 Sulfur 293 Coal 238,167 238,167 TOTAL 238.167 384,1«) 8,718 27,761 56,153 31,226 293 27,498 15,634 4,240 5,216 16,460 21,676 1,232 1,848 Moiwt 32 21 19 20 32 17 36 28 28 2 9 44 44 requires supplementary natural gas for combustion.
Details
-
File Typepdf
-
Upload Time-
-
Content LanguagesEnglish
-
Upload UserAnonymous/Not logged-in
-
File Pages13 Page
-
File Size-