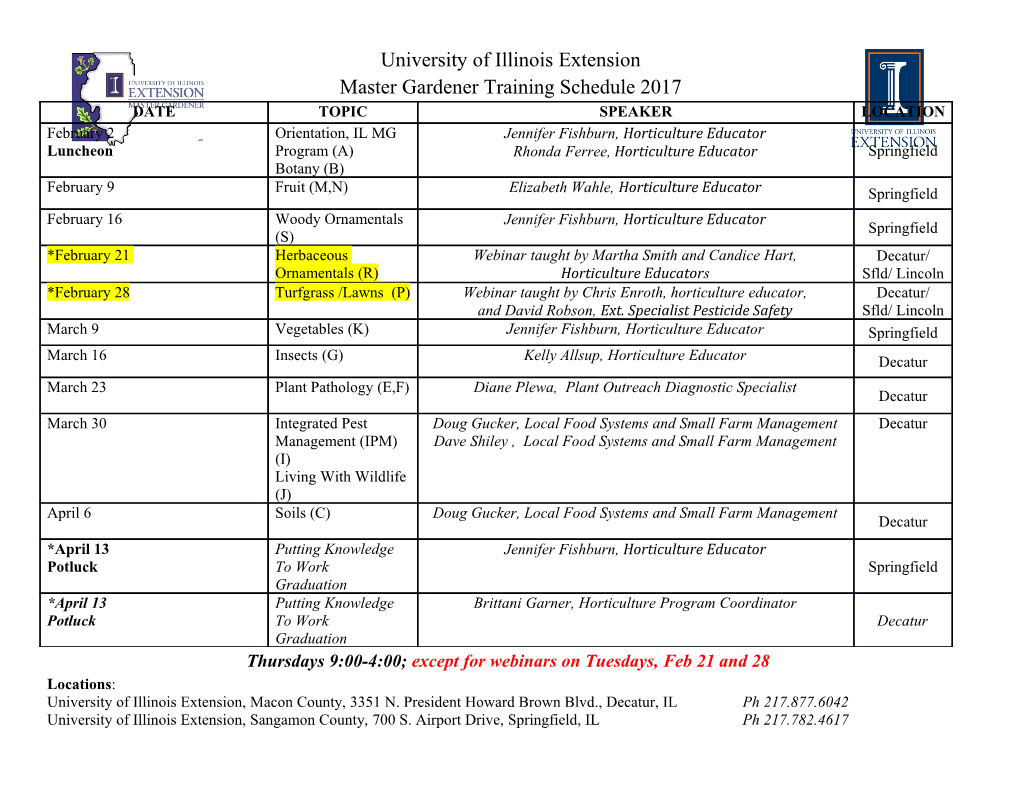
Scaling laws and similarity models for the preliminary design of multirotor drones Marc Budinger, Aurélien Reysset, Aitor Ochotorena, Scott Delbecq To cite this version: Marc Budinger, Aurélien Reysset, Aitor Ochotorena, Scott Delbecq. Scaling laws and similarity models for the preliminary design of multirotor drones. Aerospace Science and Technology, Elsevier, 2020, 98, pp.1-15. 10.1016/j.ast.2019.105658. hal-02997598 HAL Id: hal-02997598 https://hal.archives-ouvertes.fr/hal-02997598 Submitted on 10 Nov 2020 HAL is a multi-disciplinary open access L’archive ouverte pluridisciplinaire HAL, est archive for the deposit and dissemination of sci- destinée au dépôt et à la diffusion de documents entific research documents, whether they are pub- scientifiques de niveau recherche, publiés ou non, lished or not. The documents may come from émanant des établissements d’enseignement et de teaching and research institutions in France or recherche français ou étrangers, des laboratoires abroad, or from public or private research centers. publics ou privés. Open Archive Toulouse Archive Ouverte (OATAO ) OATAO is an open access repository that collects the wor of some Toulouse researchers and ma es it freely available over the web where possible. This is an author's version published in: https://oatao.univ-toulouse.fr/26688 Official URL : https://doi.org/10.1016/j.ast.2019.105658 To cite this version : Budinger, Marc and Reysset, Aurélien and Ochotorena, Aitor and Delbecq, Scott Scaling laws and similarity models for the preliminary design of multirotor drones. (2020) Aerospace Science and Technology, 98. 1-15. ISSN 1270-9638 Any correspondence concerning this service should be sent to the repository administrator: [email protected] Scaling laws and similarity models for the preliminary design of multirotor drones ∗ M. Budinger a, , A. Reysset a, A. Ochotorena a, S. Delbecq b a ICA, Université de Toulouse, UPS, INSA, ISAE-SUPAERO, MINES-ALBI, CNRS, 3 rue Caroline Aigle, 31400 Toulouse, France b ISAE-SUPAERO, Université de Toulouse, 10 Avenue Edouard Belin, 31400 Toulouse, France a b s t r a c t Multirotor drones modelling and parameter estimation have gained great interest because of their vast application for civil, industrial, military and agricultural purposes. At the preliminary design level the challenge is to develop lightweight models which remain representative of the physical laws and the system interdependencies. Based on the dimensional analysis, this paper presents a variety of modelling approaches for the estimation of the functional parameters and characteristics of the key components Keywords: of the system. Through this work a solid framework is presented for helping bridge the gaps between Multirotor drones optimizing idealized models and selecting existing components from a database. Special interest is given Scaling laws to the models in terms of reliability and error. The results are compared for various existing drone Dimensional analysis platforms with different requirements and their differences discussed. Surrogate models Propulsion system Landing gear 1. Context which can be integrated into any optimization tool for rapid pre- liminary design of multirotor drones [8,9]. During the last decade, technological innovations [1–3]have Section 2 places emphasis on the sizing scenarios that influ- significantly contributed to the development of smart and power- ence the design of the components and introduces the concept of ful multirotor UAVs: miniaturization and microelectronic with the dimensional analysis for the creation of estimation models. Mod- integration of inertial sensors, increased computational power of els based on similarities, also called scaling laws, are described in control processors, new battery technologies with higher energy section 3 and applied in section 4 for the electrical components: density, permanent magnet motors with higher torque density and motor, battery, ESC and cables. high power densities electric-converters. Regression models are described in section 5 and can adopt The expansion of drones market has led to the decrease of different forms: polynomial forms exemplified in section 6 for pro- drone sizes and the increase of the availability of drone compo- pellers and variable power law models in section 7 for structural nents at very competitive prices. This has facilitated the exper- components. imentation and optimization of drone designs based on succes- Finally, in section 8 several examples of existing drone plat- sive physical tests. Most of recent designs address very specific forms are compared with the results obtained using the models. application-cases with particular performances/needs for which a design optimization process is needed. The design optimization 2. Needs for prediction models during preliminary design process becomes mandatory when the payload scale factor dif- fers from market trend. Particularly in research projects of large Within the whole product development process, the purpose of multirotor UAVs designed for the transport of commercial loads or preliminary design phase is the evaluation of architecture feasibil- passengers [4–7] where expensive prototypes are used, it is sug- ity, technology selection and components high-level specifications gested to perform advanced design studies before manufacturing, definition based on product requirements and operational scenar- integration and testing. To accelerate the design process, a general ios. Yet, to do so, the critical scenarios should be identified and the trend is to extend the role of modelling in design and specification. associated main components characteristics identified. The present paper proposes a set of efficient prediction models 2.1. Multirotor main components * Corresponding author. Fig. 1 shows a typical mass distribution for the different compo- E-mail address: [email protected] (M. Budinger). nents of a drone according to several examples [10–12]. This paper https://doi.org/10.1016/j.ast.2019.105658 2 Nomenclature N ABS Acrylonitrile Butadiene Styrene k Equivalent stiffness................................. eq m2 DC Direct Current Nm K T Torque constant.................................... A DoE Design of Experiments rpm K V Velocity constant.................................. V EMF ElectroMotive Force L Characteristic length................................. m ESC Electronic Speed Controller larm Arm length........................................... m FEM Finite Element Method M Mach number IGBT Insulated Gate Bipolar Transistor M Mass................................................. kg LiPo Lithium-Polymer np Parallel branches LG Landing Gear ns Series branches MTOW Maximum Takeoff Weight nT Coil turns MOSFET Metal Oxide Semiconductor Field Effect Transistor P iron Iron losses........................................... W PBS Product Breakdown Structure Pon Conduction losses................................... W RSM Response Surface Model P switch Commutation losses................................. W UAV Unmanned Aerial Vehicle r Diameter ratio....................................... m VPLM Variable Power Law Metamodel R Resistance............................................ Latin formula symbols U Voltage............................................... V U DC DC voltage............................................ V B Flux density.......................................... T T f Friction torque..................................... Nm Br Magnetic remanence................................. T Tnom Nominal torque.................................... Nm C Capacity............................................. Ah V Flight speed......................................... m −1 s Crate C-rate.............................................. h m V impact Impact speed........................................ s C P Power coefficient C T Thrust coefficient Greek formula symbols D Blade diameter....................................... m β Ratio pitch-to-diameter E No-load voltage...................................... V rad δ Rotational speed.................................... W s h Convection coefficient............................. m2 K Average relative error................................ % Harm Arm height........................................... m rad ω Rotational speed.................................... s I O No-load current...................................... A π Dimensionless number J Advance ratio ρ Resistivity.......................................... m A J Winding current density........................... m2 σ Standard deviation................................... % N K Air compressibility................................. θ Maximum admissible temperature................... K m2 edge of the technology or physical-domain. The so-called compo- nents design drivers are summarized in Table 1 with the corre- sponding scenarios for which they should be assessed as well as literature references. 2.3. Dimensional analysis and Buckingham’s theorem Some references [19]or tools [20]directly use databases to evaluate the performance resulting from the association of defined components. The explosion of combinatorial solutions which in- crease with the databases size may lead to very high computation time. This is why, most of the design methodologies, despite the wide variety of implementations [9,16,8], are based on analytical Fig. 1. Multirotor drone average mass distribution based on [10–12]. expressions or catalogue data regressions and benefit, as most con- tinuous problems, of numerical
Details
-
File Typepdf
-
Upload Time-
-
Content LanguagesEnglish
-
Upload UserAnonymous/Not logged-in
-
File Pages17 Page
-
File Size-