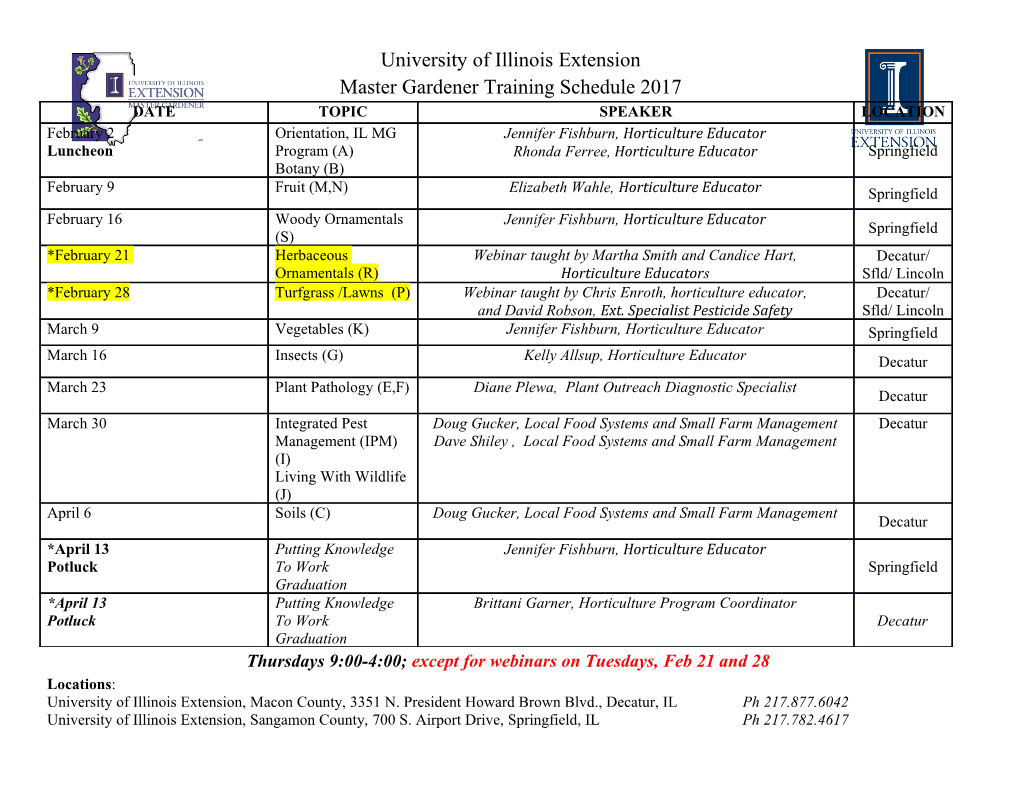
Metal Fabrication Capabilities: A Guide For Fabrication Services Contents An Overview: Metal Fabrication 3 Benefits of 3D CAD Software 4 Machining 5 Waterjet Cutting 6 Welding 7 Finding a Metal Fabrication Company 8 Red Flags to Watch Out For 9 About CAMM Metals 10 2 An Overview: Metal Fabrication Metal Fabrication is complex and cutting corners isn’t an option. Therefore, it’s important to invest in a company that professionally understands and offers every aspect of your intricate metal fabrication or assembly project. This guide highlights the different components of metal fabrication. Fabrication is an industrial term that refers to the processing of raw materials (such as steel or aluminum) for the making of components, machines or structures. Fabrication can be a complex process involving many different processes such as machining, waterjet cutting and welding requiring highly-trained personnel and technology for quality precision. From sheet metal and plate fabrication to structural members to architectural metal work and weldments, there are a lot of markets served by the fabrication process. With the latest 3D CAD program, quality can be enhanced as well as reduce the amount of production time needed. Whether it’s a small sheet metal bracket or large fabrication, 1 piece or 1,000, it’s important to work with a company that has a professional team of fabricators, CNC operators and welders for quality fabricated metal products. 3 Benefits of 3D CAD Software Most metal fabrication businesses still rely Design Better on 2D drawings, even when there is a 3D The direct benefit of designing in 3D is model available. This affects potential the improvement in design accuracy, productivity greatly. The reasons mainly quality and reduced scrap. 3D CAD include the inability of the drawings to modeling tools incorporate sheet metal maintain a tight collaboration between the features that provide the ability for the departments and limited possibility to designer to design a completed communicate design intent clearly. product, as it will look like once it is Besides, 2D drafts are often difficult to manufactured. With few mouse clicks, manage and are prone to errors that the entire sheet metal object can be eventually cause miscommunication and flattened, including all the allowances to production scrap. accurately perform sheet metal operations at the shop floor. This is something that every metal The enhanced visibility of the design fabricator would probably know of, but are intent further allows the engineering somehow stuck with the 2D processes, team to quickly communicate the either due to the fear of losing business design with non-technical staff and while transitioning or due to resistance thereby keep everyone on the same from internal experienced resources. page. It’s critical to work with a metal fabrication company who uses 3D CAD Software. 4 Machining Machining is a form of fabrication with the method of metal removal from another source of material. The range of motion of the cutting head is defined by the number of axes (i.e. a 3-axis or 4-axis machine). Computer numeric control (CNC) machining is a method that automates the operation of CNC machining is machine tools ensuring accurately programmed beneficial for computer commands. CNC machining is the prototyping, form and preferred machining method due to the accuracy and proficiency provided. CNC machining can fit testing, jigs and produce numerous types of complex parts and fixtures, and functional components with a high degree of precision to components for end- complete the job correctly every time. use applications. Parts Machining has evolved with fabrication are manufactured companies using the very latest technology. For through high-speed instance, Haas Super Speed machining centers milling and turning allow the ability to mill aluminum at speeds faster than traditional machining centers while still processes from various maintaining the high quality necessary. Also, the materials used by latest CAD/CAM technology programs all of the engineering parts ran on the milling machines. Whether it’s prototype or short run to large volume production professionals. runs this technology will help you get precision cut parts. 5 Waterjet Cutting Waterjet cutting is an abrasive cutting process that uses high pressure water to cut virtually any material with a high level of precision and no distortion. The water is pressurized and pushed through a .030″ diameter nozzle, concentrating the water stream allowing to cut any material, from steel to plastic, up to 6″ thick. Waterjet cutting services has several advantages for our customers. First, they eliminate the need to buy custom tooling, thereby reducing set up time and unnecessary costs. We use the same set up to cut thin sheet metal as we do to cut 6″ plate. Second, waterjets are capable of cutting a wide variety of materials. We regularly cut Steel, Stainless Steel, Aluminum, high temp and aerospace alloys like Titanium, Inconel, Waspaloy, Hastelloy, reflective metals like Brass and Copper, Plastics, Composites and they are especially good at cutting laminated materials like Carbon Fiber. Waterjets can be used in several different ways. First, to cut flat sheet metal and plate to feed any fabrication work. The precision from the waterjet is just as good as laser cutting and better than plasma cutting. Second, the machines can be used to process thick plates, precut shapes and blanks for CNC Machining. Third, water jet cutting can also be used as a service to from a professional fabrication company for those who do not have this type of capability. Lastly, these machines can can cut round and rectangular tubes and pipes. Click on this YouTube link at the top of this page you’ll see a video of a water jet cutting a 8″ diameter stainless steel pipe. 6 6 Welding There are various types of welding but here are two efficient types used Welding is a joining process in which by quality pulsed welding machines: metals are heated, melted and mixed to produce a joint with properties similar to MIG Welding (Metal Inert Gas) those of the materials being joined. Many MIG welding runs the filler material fabrication companies have started to from a wire coil through the MIG utilize pulsed welding to increase accuracy torch. This wire carries the electrical and efficiency. current, and does the actual welding. Pulsed welding is simply alternating TIG Welding (Tungsten Inert Gas) between a peak (high) and a background TIG welding uses a Tungsten (low) current. Metal is transferred through electrode to superheat the parent the arc during the peak current. Simply put, metals. Then the welder will apply the filler material onto the weld Pulsed MIG and TIG technology improves puddle once the two metals have first-pass yield rates, lower cycle times and reached a liquid state reduce piece costs. 7 Finding a Metal Fabrication Company You should be able to do your job stress free and therefore work with a single metal fabrication company that is a one-stop shop for every aspect of your intricate metal fabrication or assembly project. When you have complete confidence in your steel fabricator from the start, you can rest assured knowing that every project will meet or exceed all of your expectations. The following are some qualities to look for when finding the right metal fabrication company: • Diverse Services: Many fabrication companies offer limited services and therefore may not have the capability to handle the intricacies of your project. Look for a company with a diverse portfolio and can act as a one-stop shop for the majority of your fabrication needs. • Proper Facility And Equipment: When seeking a potential fabricator for your job, don’t forget to scale the size of your project to see if the company has the proper facility and equipment available for efficient services. • Quality: Along with having the tools and staff required for different projects, research the quality of their services. What are others saying? What technology and fabrication equipment do they use? • Pricing: Make sure to do the proper research to find a fabricator that offers reasonable pricing. Some fabricators may offer you estimates that are extremely overpriced. Therefore, through detailed comparisons and breakdowns, you’ll be able to see an estimate of reasonable prices and fabrication companies who offer such. 8 Red Flags to Watch Out For When selecting a fabrication partner, there are considerations other than cost, which should be taken into account. Selecting a fabrication partner is the start of a relationship, one that affects your business and clients directly. Your relationship with your metal fabrication partner should be based on trust, communication, and support. Like any good relationship, these elements will allow your partnership to thrive. With many fabrication firms offering more options to potential partners, taking the time to research your fabricator will be extremely beneficial. In addition, there are a few red flags you should be aware of before selecting a fabrication partner: Questionable Management How are the people behind the work? An effective partnership does not stop at the quality of the work. If you cannot work with the people on the team, the work can suffer. What is the average tenure of employees at the shop? What are the company’s core values? Do their values align with yours? Capacity Do they have a history of handling larger workloads? With growth often comes larger orders. Take a few moments to make sure that your potential partner has the capability to manage large orders. Limited Flexibility Your organization may be focused on working with the most cutting-edge technology and innovative minds. Is your potential partner flexible and willing to explore options that are representative of your vanguard? Working with a partner that understands your need to move forward and to embrace new techniques and products is essential to the success of your relationship.
Details
-
File Typepdf
-
Upload Time-
-
Content LanguagesEnglish
-
Upload UserAnonymous/Not logged-in
-
File Pages10 Page
-
File Size-