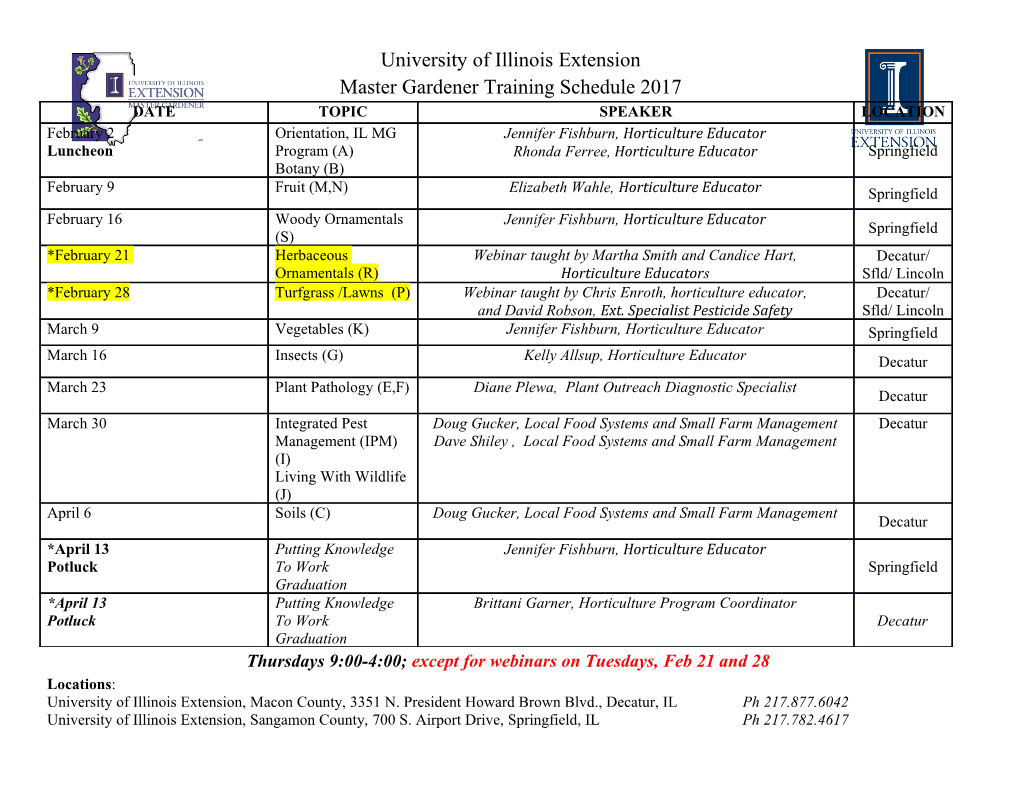
Agric. Bioi. Chern., 51 (9), 2617-2620,1987 2617 Rapid Paper proposed that alcohol oxidase could be used for the oxidation of ethanol to acetaldehyde, Production of Acrolein, as a recovery system for ethanol in fermen­ Acetaldehyde and Propionaldehyde tation medium. 8 ) However, the yield of acetal­ by Cells of a Methanol Yeast, dehyde has not been reported. In this study, allyl alcohol, ethanol or 1- Candida boidinii S2 propanol was oxidized for the production of acrolein, acetaldehyde or propionaldehyde, re­ Downloaded from https://academic.oup.com/bbb/article/51/9/2617/5966698 by guest on 27 September 2021 Yasuyoshi SAKAI* and Y oshiki T ANI spectively, with heat-treated cells of a meth­ anol yeast showing high alcohol oxidase ac­ Research Center for Cell and Tissue Culture and * Department of Agricu/turaIChemistry, tivity. Faculty of Agriculture, Kyoto University, Kyoto 606, Japan MATERIALS AND METHODS Received June 8, 1987 Chemicals. Acrolein was purchased from Tokyo Chemical Industry Co., Ltd. The concentration of acrolein Heat-treated cells of a methanol yeast, showing high in the sample was calculated to be 98.9%, which was alcohol oxidase activity, were used for the production of determined by gas-liquid chromatographic analysis. aldehydes, i.e., acrolein, acetaldehyde and propional­ dehyde, from the corresponding alcohols, allyl alcohol, Strain and cultivation. A methanol yeast, C. boidinii S2 ethanol and I-propanol, respectively. As high a level as strain AOV-1.2) was used in this study. Cells were grown 7.5% acetaldehyde was obtained, in the reaction mixture, in a methanol-limited chemostat culture at the dilution 1 from 8.0% ethanol as a substrate. The acrolein con­ rate of 0.075 hr- as described previously.4) centration reached 3% after 2-hr reaction, from 5% allyl alcohol a's a substrate. The difference in molar yields of Reaction jor aldehyde production. Chemostat-grown these aldehydes is discussed on the basis of inactivation of cells were harvested and then heat-treated as described alcohol oxidase by reaction products. previously.4) The reaction mixture contained 90 mg (as dry cell weight) of heat-treated cells, I mmol of pot<lssium The use of microbial cells for the production phosphate buffer, pH 6.5, for acrolein production, and pH of fundamental chemicals would be attractive 7.5 for acetaldehyde and propionaldehyde production, respectively, and alcohol as a substrate in a final volume of because 1) the narrow specificity of the enzy­ 3 ml. The reaction mixture was put in a 30-ml Erlenmeyer matic reaction could reduce the amount of a flask, which was equipped with a rubber balloon to supply by-product, and 2) the milder reaction con­ pure oxygen, and then shaken reciprocally at 170 rpm. The ditions than those of usual chemical processes reaction was terminated by removing the cells by cen­ might reduce energy costs.1) In preceding trifugation at 4°C. The resultant supernatant was sub­ studies,Z-7) we constructed a reaction system jected to gas-liquid chromatographic analysis. Cation M2-treated cells were prepared as described for 'formaldehyde production from methanol previously.7) using cells of a methanol yeast, Candida boi­ dinii 82. In chemostat-grown cells under ap­ Gas-liquid chromatographic analysis. The reaction mix­ propriate culture conditions, alcohol oxidase ture was applied to a Shimadzu gas-liquid chromatog­ raphy GC7-A, equipped with a flame ionization detector. comprised nearly 50% of the total soluble A glass column, FAL-M, 2m, was used for assaying allyl proteins.4 ) alcohol, acrolein, I-propanol and propionaldehyde. For Acrolein is now mainly industrially pro­ the allyl alcohol and acrolein assays, the carrier gas was duced through the direct oxidation of pro­ He 38 mljmin, and the column and injection temperatures pylene. However, the recovery of the product were lOO°C and l30 D C, respectively. For the I-propanol is low and the reaction product contains large and propionaldehyde assays, the carrier gas was He 20 mljmin, and the column and injection temperatures amounts of acetaldehyde and acetone as by­ were lO2°C and l30D C, respectively. To determine the products. Acetaldehyde is used for the syn­ amounts of ethanol and acetaldehyde, a column of thesis of a number of chemicals and is pro­ Porapack Q, 2 m, was used; the carrier gas was N2 duced through ethylene oxidation. Kierstan 50 ml/min, and the column and injection temperatures 2618 Y. SAKAI and Y. TANI were 160°C and 190°C, respectively. Integration and cali­ bration of peak areas were carried out with a Shimadzu Chromatopack C-R 1B. 3 3 ~ The substrate and product concentrations were ex­ > ~ "- pressed as % (wjv). > "- ! ! "0 G) RESULTS AND DISCUSSION "0 2 2 E G) :J c.> OJ :J C "0 0 Heat- or Cation M2-treated cells and intact 0 c.> Downloaded from https://academic.oup.com/bbb/article/51/9/2617/5966698 by guest on 27 September 2021 cells were tested as to acrolein production at a. "0 c 1 J:. 1 0 various temperatures. As shown in Fig. I, "ii c.> ~ to heat-treated cells showed slightly higher acro­ u c( >. lein productivity than Cation M2-treated or 0 0 :;c intact cells. At 4°C, heat-treated cells accumu­ 4 12 28 lated 3.5-fold more acrolein than those at Reaction temperature ('e) 28°C, the optimum temperature for alcohol FIG. 1. Effect of the Reaction Temperature on Acrolein oxidase.3) The consumption of allyl alcohol Production. paralleled the acrolein production at 4°C and The initial acrolein concentration was 3 %, and the re­ 28°e. After similar experiments, heat-treated action was performed at the indicated temperatures for cells were selected also for acetaldehyde and 2 hr with: 0, intact cells; ., heat-treated cells; !'::,., Cation M2-treated cells. Other reaction conditions are given propionaldehyde production. The optimum under MATERIALS AND METHODS. temperature for aldehyde production was 4°C in all cases tested,3) though the highest form­ aldehyde productivity was obtained with ? + ~ Cation M2-treated cells. 3 ) ~ The effect of the initial pH of the reaction ~ 2 ! "0 mixture on aldehyde production was investi­ "0 .. G) E ::I gated using 0.33 M potassium phosphate buff­ c.> OJ ::I C "0 0 er. As shown in Fig. 2, both the production of 0 u li1 "0 C J:. acrolein and the consumption of allyl alcohol 'iii 0 "0 u were maximum at pH 6.5. On the other hand, t; iii c( ~ a rather alkaline pH 7.5~8.0, was suitable for :;;: acetaldehyde or propionaldehyde production. 0 0 Under the optimal reaction conditions es­ 4 5 6 8 9 pH tablished, acrolein production was performed at various substrate, allyl alcohol, concen­ FIG. 2. Effect of the Initial pH of the Reaction Mixture trations (Fig. 3). On the oxidation of 5% allyl on Acrolein Production. alcohol, the concentration of acrolein in the The initial acrolein concentration was 3%. The reaction was performed under the conditions given under reaction mixture reached 3 % after 2 hr, and MATERIALS AND METHODS using 0.33 M potassium phos­ there after the reaction did not proceed any phate buffer at the indicated pHs. more. In the resultant reaction mixture, about 1.7% allyl alcohol remained, and no other volatile substrates could be detected on gas­ between acrolein (bp 53°C) and allyl alcohol liquid chromatography. This amount of acro­ (bp 96°C) is taken into account, our microbial lein corresponded to that in the case of crude process would exceed in purity of volatile acrolein solution obtained with the chemical products. Reactions for acetaldehyde and pro­ process, which contained nearly 10% acetal­ pion aldehyde production were also performed dehyde (bp 21°C) and acetone (bp 56SC). with various concentrations of ethanol and 1- When the great difference in boiling point propanol, respectively. As shown in Table I, Production of Aldehydes by a Methanol Yeast 2619 2% ethanol was completely oxidized to acetal­ 18-br reaction. On the other hand, 0.5% 1- dehyde after 1.5 hr. As high a level as 8% propanol was completely converted to 0.48% ethanol could be converted to 7.5% acetal­ propionaldehyde on 1.5 hr reaction. (> dehyde, with a yield of nearly 1.0 0.98), on TABLE I. EFFECT OF THE INITIAL ETHANOL CONCENTRATION IN THE REACTION MIXTURE ON ACETALDEHYDE PRODUCTIVITY 3 Acetaldehyde production was performed from various i,Q concentrations of ethanol. Other reaction conditions are Downloaded from https://academic.oup.com/bbb/article/51/9/2617/5966698 by guest on 27 September 2021 > "- given under MATERIALS AND METHODS. ! '1:1 2 Acetaldehyde produced (Yield) GI U Initial concn. (%) :::I of ethanol Reaction time '1:1o li (%) c 1.5 hr 18 hr 'ij 1 '0 0.5 0.48 (> 0.99) ~ c:t: 1.0 0.95 (>0.99) 2.0 1.92(>0.99) 3.0 2.47 (0.86) 2.78 (0.97) o 4 6 8 10 4.0 2.75 (0.72) 3.80 (>0.99) Allyl alcohol (w/v %) 5.0 2.89 (0.60) 4.78 (> 0.99) FIG. 3. Effect of the Allyl Alcohol Concentration on 6.0 2.54 (0.44) 5.75 (>0.99) Acrolein Productivity. 7.0 2.50 (0.37) 6.65 (0.99) 8.0 2.53 (0.33) 7.48(0.98) Acrolein production was performed for 2 hr, from the 9.0 2.65 (0.31) 7.88 (0.92) indicated concentrations of allyl alcohol. Other reaction 10.0 2.84 (0.30) 7.87 (0.82) conditions are given under MATERIALS AND METHODS. TABLE II. PRODUCTION OF VARIOUS ALDEHYDES WITH CELLS OF A METHANOL YEAST Optimum Concn.
Details
-
File Typepdf
-
Upload Time-
-
Content LanguagesEnglish
-
Upload UserAnonymous/Not logged-in
-
File Pages4 Page
-
File Size-