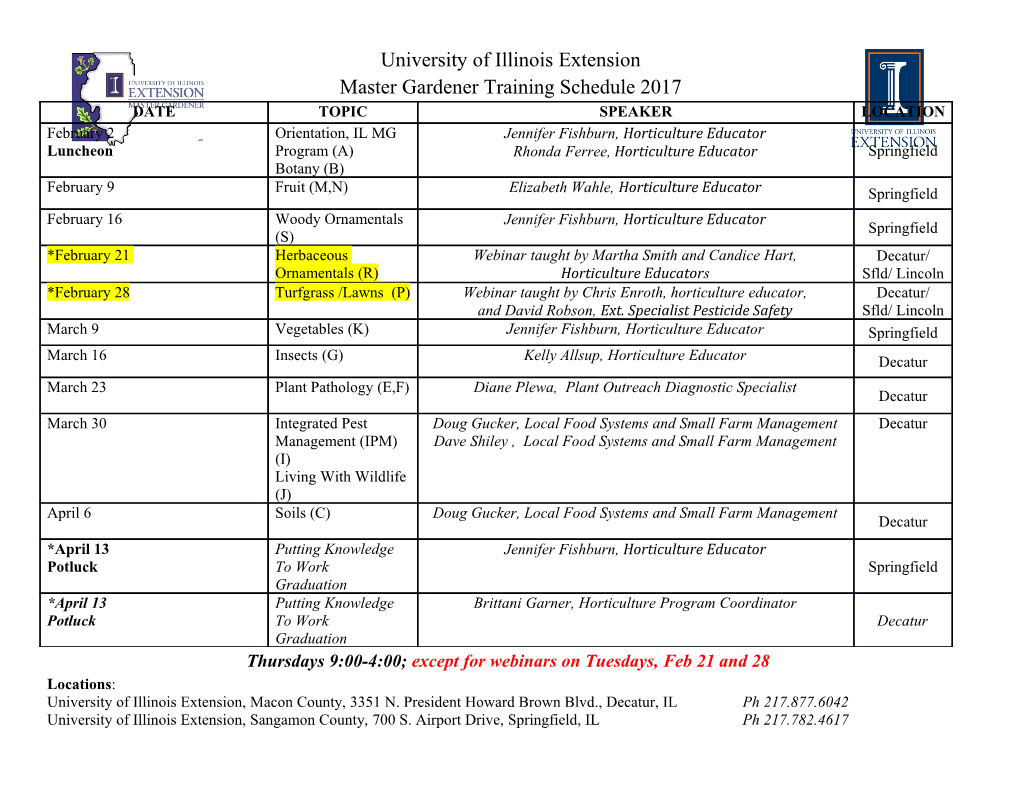
AIAA 2017-0551 AIAA SciTech Forum 9 - 13 January 2017, Grapevine, Texas 55th AIAA Aerospace Sciences Meeting An Experimental Study of Dynamic Ice Accretion Process on Aero-engine Spinners Linkai Li1, Hui Hu2() Department of Aerospace Engineering, Iowa State University, Ames, Iowa, 50011 Ice accretion on aero-engine spinners has posed significant safety and performance concerns when aircraft operate in cold weather. In the present study, a comprehensive experimental study was conducted to investigate the transient ice accretion process on a rotating aero-engine fan with different spinner profiles (i.e., conical, coniptical, and elliptical). The experiments were performed in the Iowa State University Icing Research Tunnel (ISU-IRT) with a scaled aero-engine fan model operated under a variety of icing conditions. The transient details in the unsteady icing processes were resolved using a high-speed imaging technique, while the input power required to drive the fan at constant rotation rate was measured during the ice accretion process. The experiments demonstrated how varying the spinner profiles modifies the ice accretion process. It was found that the elliptical spinner is more sensitive to ice accretion, as indicated by the more dramatic increase in the required input power when ice accretes. Nomenclature δ = blade trailing edge thickness, mm Subscripts θ = half apex angle of spinner, ° Δ = ice thickness, mm 0 = initial value ε = threshold used for ice boundary detection f = fan η = mechanical efficiency of the brush-less motor i = image index ρ = density, kg/m3 ins = instantaneous value σ = standard deviation of boundary detection, mm max = maximum value A = cross sectional area of test section, m2 no-ice = no ice status D = diameter, mm ratio = non-dimensional ratio HE = standard exposure distance, nmi rime = rime ice Ii = ith image in the high-speed image sequence s = spinner J = advance ratio of aero-engine fan water = sprayed water L = length, mm ∞ = freestream LWC = liquid water content, g/m3 MVD = mean volume diameter, μm N = number of blades P = input power of brush-less motor, W R = rotation speed, rpm t = time, s Downloaded by IOWA STATE UNIVERSITY on February 13, 2017 | http://arc.aiaa.org DOI: 10.2514/6.2017-0551 T = temperature, ℃ U = velocity, m/s XLE = ice boundary coordinate at X direction I. Introduction Aero-engine icing is still a common aviation danger for aircraft operation in cold weather. When aircrafts flies in a cold climate, some of super-cooled droplets would impinge and freeze on the exposed surfaces of aero-engines, like the inlet tips, spinners and fan rotor blades. Ice accretions on such components can significantly degrade the 1 Graduate Student, Department of Aerospace Engineering, AIAA Student Member 2 Martin C. Jischke Professor, Department of Aerospace Engineering, AIAA Associate Fellow, Email: [email protected] 1 Copyright © 2017 by the American Institute of Aeronautics and Astronautics, Inc. The U.S. Government has a royalty-free license to exercise all rights under the copyright claimed herein for Governmental purposes. All other rights are reserved by the copyright owner. aerodynamic performances of aero-engines that may cause an unstable compressor operation. Meanwhile, the ice accumulated over the fan blades and spinner would result in imbalance of the rotor, which would cause serious mechanical vibrations. More problematically, the ice shedding from the inlet, spinner or rotor blades may damage the fan rotor and the components behind the fan, even be suck into the core of the engine that cause stall and surge.1 Although many efforts have been devoted to icing-related issues on aero-engine since 1940s,2 further studies are stilled needed for a better understanding about the underlying physics pertinent to the icing phenomenon, which would lead to more effective and robust anti-/de-icing strategies that ensure safer and more efficient operation of aero-engine in cold weather. The spinner of the aero-engine is more sensitive to ice accretion due to its relative low spinning velocity and larger imping area for the super-cooled water droplets. A number of previous studies have been conducted in recent years to investigate the icing phenomena on aero-engines, and some anti/de-icing strategies have been suggested as well. Bidwell et al. used NASA’s LEWICE3D code to examine the ice issues on Energy Efficient Engine (E3), and found that an increased water drop size would result in an increased impingement rates on the spinner and fan.3 Dong et al. conducted a numerical study to investigate the ice accretion on rotating aero-engine spinner and found that rotating speed has light effect on the ice shape, but the temperature of freestream would affect the thickness of ice over the spinner.4 Wang et al. studied the ice accretion and shedding on a rotating spinner in an icing wind tunnel, they found that a mixture of different styles of ice grow like a feather on the surface and shed eventually.5 Dong and Hu conducted both numerical and experimental studies to evaluate a newly-developed hot-air anti-icing system applied in a full-scale cone model and they found that the hot-air film anti-icing method works well under designed icing conditions.6,7 Gilchrist et al. invented a nose cone anti-icing system using a rotating heat pipe filling with water or ethanol, which could improve the nose cone anti-icing performance and provide more feasibility.8 Although these methods are effective for anti/de-icing to a certain extent, the heating air or liquids from low-pressure compressor (LPC) or high-pressure compressor (HPC) would inevitably cause performance reduction of the aero-engine. While most of the previous studies focused on ice shape prediction, heat transfer process and performances of anti/de-icing system. Very few can be found in literature to address the effect of spinner’s geometry shape on the dynamics of ice accretion and aerodynamic performance of the engine fan. The shape of the spinner would not only affect the aerodynamic efficiency of the fan, but also determine the tendency for ice accretion on the spinner, which can be leveraged to design more effective anti/de-icing systems for aero-engine. Three typical spinner shapes, which are elliptical, conical and coniptical, are widely used in aero-engines. As described in the chapter of Linke-Diesinger’s,1 although the elliptical spinner is easier to accumulate ice at a lower humidity level in comparison to other spinner designs, it has a better aerodynamic efficiency. Oppositely, the conical spinner requires higher level of humidity to accumulate ice. Its aerodynamic efficiency, however, is not as high as the elliptical one. Hu et al. investigated the effect of spinner angle on ice accretion of a scaled rotating conical spinner, and demonstrated that the tip angle of the spinner would significantly affect the ice accretion over the spinner.9 Both these previous studies, however, lack enough quantitative measurement data to support the conclusions and the fundamental physics behind experimental observations is still unclear. In this study, a comprehensive experimental investigation was conducted to examine the dynamic transient ice accretion process over different kinds of aero-engine fan spinners. The experiments were performed in an icing research tunnel available at Iowa State University (i.e., ISU-IRT) with a scaled aero-engine fan model under different controlled icing conditions. In addition to recording the transient behavior of water runback and dynamic ice accretion Downloaded by IOWA STATE UNIVERSITY on February 13, 2017 | http://arc.aiaa.org DOI: 10.2514/6.2017-0551 process on the rotating spinners by using a high-speed imaging system, instantaneous input power of the driving motor was acquired through a DAQ system. From the acquired time-resolved image sequences of icing events, the important microphysical processes, including the impingement area of the super-cooled water droplets and ice accretion shape on the rotating spinner, were revealed in detail. Moreover, based on the high-speed images quantification method from Waldman and Hu,10 one images processing technique used to identify the ice profiles of rime ice accretion and extract the development of ice thickness on the spinners is demonstrated in present study. II. Experiments A. Aero-engine Fan Model The model aero-engine fan used in the present study is designed based on the Boeing 18-inch fan rig11 and its design parameters are summarized in Table 1. 2 Table 1. Design parameters of the aero-engine fan model Fan Diameter, Df (mm) 200 Hub/Tip Ratio 0.402 Spinner Diameter, Ds (mm) 80 Aspect Ratio 1.65 Number of Blades, N 18 Tip Max Thickness/Chord 0.025 Thickness of trailing edge, δ (mm) 0.18 Hub Max Thickness/Chord 0.100 Figure 1 shows the schematic of the three kinds of aero-engine spinners examined in the present study. The test models are made of a hard plastic material (i.e., VeroWhitePlus, RGD835, manufactured by Stratasys, Inc.) by using a rapid prototyping machine (i.e., 3D printer) that builds the model layer-by-layer with a resolution of about 25 lm. The external surface of the test models was processed with fine sandpaper (i.e., up to 2000 grit) to achieve a very smooth, glossy finish. Figure 1. Design of three types of spinners and the aero-engine fan tested in the present study B. Experimental Setup and Instruments The experimental study was performed in ISU-IRT located in the Aerospace Engineering Department of Iowa State University. The ISU-IRT, which was originally donated by UTC Aerospace System (formerly Goodrich Corporation) to Iowa State University, is a newly refurbished research-grade multifunctional icing research tunnel.10 The test section is 2.0 m long with 400mm (height) × 400 mm (width) in cross section.
Details
-
File Typepdf
-
Upload Time-
-
Content LanguagesEnglish
-
Upload UserAnonymous/Not logged-in
-
File Pages15 Page
-
File Size-