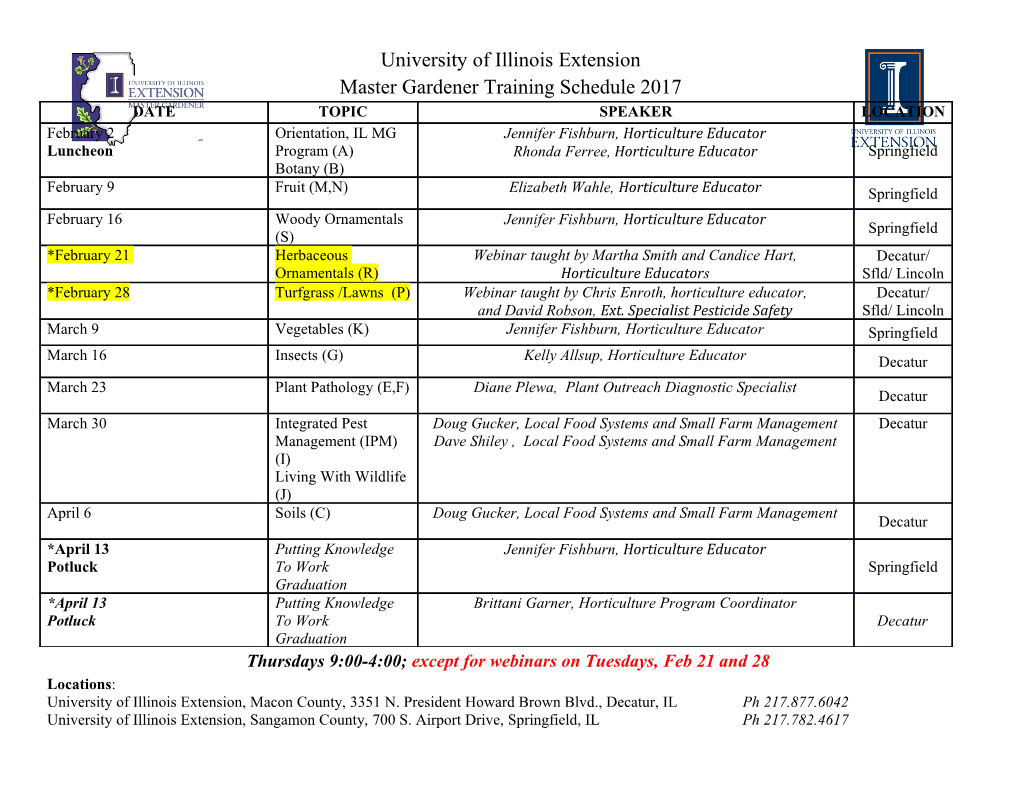
The Road Toward Greener Cars by Using Neuro- Fuzzy Modeling of Spark-Ignition Engines with Variable Valve Overlap Mashhour M. Bani Amer1 and Yousef S. H. Najjar2,* 1Department of Biomedical Engineering 2Department of Mechanical Engineering Jordan University of Science and Technology, P.O.Box 3030, 22110 Irbid, JORDAN. Received May 22, 2013; Accepted June 29, 2013 Abstract: Greening technology is gaining more attention in different aspects, especially the surface transport. This technology aims to improve performance and reduce global greenhouse gas emissions. In this work, a typical automotive spark ignition engine with four cylinders and 1600 cc displacement was considered. This work introduces a neuro-fuzzy approach that can be used to design an intelligent system for controlling the overlap angle in the spark ignition engine cycle. The simulation results showed that the neuro-fuzzy-based control system for varying the overlap angle achieved increased engine power and reduced fuel consumption in comparison with the conventional engine that used fi xed overlap angle. The power was improved by about 2.2–12.6 %, while the BSFC was reduced by about 2%-11%. Keywords: Green cars, neuro-fuzzy modeling, variable valve-timing 1 Introduction Greening technology is gaining more attention in different aspects, especially the surface transport. This technology aims to improve performance and reduce global greenhouse gas emissions. Alternative approaches comprise the use of hybrid vehicles [1, 2], Lithium ion batteries [3], artifi cial neural control of the air conditioning system [4], and improve engine performance by investigating strati- fi ed charge design [5, 6] and using alternative fuels [7] such as ethanol-gasoline [8–19], oxygenated fuels [11], fuels and combustion [12], liquefi ed petroleum gas LPG [13, 14], natural gas [15, 16], and hydrogen [17]. Variable geometry include stroke length and compression ratio [18], as well as variable valve-timing and lift *Corresponding author: [email protected] DOI: 10.7569/JSEE.2013.629518 J. Sustainable Energy Eng., Vol. 1, No. 4, January 2014 275 Mashhour M. Baniamer et al.: The Road Toward Greener Cars by Using Neuro-Fuzzy Modeling to improve the volumetric effi ciency [19]. Detailed studies are being carried out for variable inlet and exhaust valve-timing and valve geometry covering valve lift in addition to variable valve, independently by the author. The volumetric effi ciency is defi ned as the mass of fuel and air induced into the cylinder divided by the mass that would occupy the displaced volume at the den- sity in the intake manifold. It is desirable to maximize the volumetric effi ciency of an engine because the amount of fuel that can be burned, hence power produced for a given engine displacement is maximized (whereas size and weight are mini- mized). The volumetric effi ciency depends on the intake manifold confi guration, valve size, lift, and timing [20–23]. The shape and location of the peaks of the volumetric effi ciency curve are very sensitive to the manifold confi guration, type of fuel delivery system, and the type of cooling system [24, 25]. If the inlet pressure is less than the exhaust pressure, the engine is throttled. In this case, there is fl ow from the cylinder into the intake port when the intake valve opens. In the initial portion of the intake stroke, the induced gas is primarily composed of combustion products that have previously fl owed into the intake port. In the latter portion of the stroke, the mixture fl owing in is fresh charge, undiluted by any combustion products. If the inlet pressure is greater than the exhaust pressure, then there is fl ow from the intake port into the engine until the pressure equilibrates [20, 25]. In actual engines, because of valve overlap, there may be a fl ow of fresh mixture from the inlet to the exhaust port, which can waste fuel and be a source of hydro- carbon exhaust emissions. The second case is when inlet and exhaust pressures are equal; the engine is then said to be un-throttled. The throttling also hurts the volu- metric effi ciency, mainly because of an increase in the residual fraction. The residual fraction decreases with increasing compression ratio, as one would expect [20]. Introducing γ=1.4 and the inlet Mach index Z defi ned by Taylor [24] 2 Z = (π/4)b Up/Af ci (1) For good volumetric effi ciency, one should keep the Mach index down to less than about Z=0.6. Based on the analyses, we can interpret this to mean that the average gas speed through the inlet valve should be less than the sonic velocity, so that the intake fl ow is not chocked. Hence, inlet valves can be sized on the basis of the maximum piston speed for which the engine is designed. Likewise for effi cient expulsion of the exhaust gas, the average effective area Ae, of the exhaust valves should be such that their Mach index is less than about 0.6, in which case, relative to intake conditions. 1/2 Ae/Ai ~ ci /ce = (Ti/Te) (2) A smaller exhaust valve diameter and lift (l~d/4) can be used because the speed of sound is higher in the exhaust gases than in the inlet gas fl ow. Current practice dictates that the exhaust to intake valve area ratio is on the order of 70 to 80% [26–27]. DOI: 10.7569/JSEE.2013.629518 276 J. Sustainable Energy Eng., Vol. 1, No. 4, January 2014 Mashhour M. Baniamer et al.: The Road Toward Greener Cars by Using Neuro-Fuzzy Modeling During overlap it is assumed that the gases are pushed into the intake mani- fold only to return later. Notice that heat loss increases the residual fraction and is important here because the exhaust gases are considerably hotter than the cylinder walls. This is the main reason for the discrepancy between fuel-air cycle calcula- tions with ideal intake and exhaust and the experiments. Inlet and exhaust mani- folds are sized or “tuned” to use the pressure waves to optimize the volumetric effi ciency at a chosen engine speed. A tuned intake manifold will have a locally higher pressure when the intake valve is open, increasing the exhaust outfl ow. To minimize engine size and produce a given torque versus speed curve (with torque proportional to the volumetric effi ciency at fi xed thermal effi ciency), it is clearly desirable to be able to vary valve-timing with engine speed. Variable valve- timing (VVT) is a technique that can address the problem of obtaining optimal engine performance over a range of throttle and engine speed. Variable valve- timing allows the intake and exhaust valves to open and close at varying angles, depending on the speed and load conditions. At idle, with a nearly closed throttle, the intake and exhaust valve overlap is minimized to reduce exhaust back fl ow. At low speed, the intake valves are closed earlier to increase volumetric effi ciency and torque. At high speed, with an open throttle, the intake valves are closed later to increase volumetric effi ciency and power. Data obtained from real spark-ignition engines illustrates the effect of varying valve-timing on the volumetric effi ciency versus speed. Earlier than normal inlet η valve closing reduces back fl ow losses at low speed and increases v. The penalty is reduced airfl ow at a high speed later than normal inlet valve closing, which is only advantageous at very high speeds. To date, relatively little attention has been devoted to the modelling and control of variable valve-timing using intelligent techniques, such as artifi cial neural net- works, fuzzy logic, or neural fuzzy approaches [28, 29]. In reference [29], the control of valve-timing is based on conventional (not intelligent) control techniques. In ref- erence [30], the authors used intelligent approach using artifi cial neural network to determine the effects of intake valve-timing on the engine performance. However, they did not suggest an intelligent approach for controlling the valve-timing to achieve optimum engine performance in terms of power and fuel consumption. Furthermore, the combining of neural networks and fuzzy logic to form a hybrid neuro-fuzzy approach enhances the performance of the approach in terms of learn- ing, adaptation and accuracy. This is why attempts have been made, as described in this paper, to develop a neural fuzzy model suitable for designing an intelligent control approach of variable valve-timing in order to improve the performance of the spark-ignition engine in terms of power and fuel consumption [31]. 2 Experimental Results and Discussion There is a valve overlap period at top dead center where the exhaust and intake valves are both open. This creates a number of fl ow effects. With a spark-ignition DOI: 10.7569/JSEE.2013.629518 J. Sustainable Energy Eng., Vol. 1, No. 4, January 2014 277 Mashhour M. Baniamer et al.: The Road Toward Greener Cars by Using Neuro-Fuzzy Modeling engine at part throttle, there will be back fl ow of the exhaust into the inlet mani- fold since the exhaust pressure is greater than the throttled intake pressure. This will reduce the part load performance because the volume available to the intake charge is less, reducing the volumetric effi ciency. Rough idle can also occur due to unstable combustion. On the other hand, because this dilution will reduce the peak combustion temperatures, the NOx pollution levels will also be reduced [32]. At wide open throttle, with both valves open, there will be some short circuit- ing of the inlet charge directly to the exhaust, because, in this case, the intake pres- sure is greater than the exhaust pressure.
Details
-
File Typepdf
-
Upload Time-
-
Content LanguagesEnglish
-
Upload UserAnonymous/Not logged-in
-
File Pages11 Page
-
File Size-