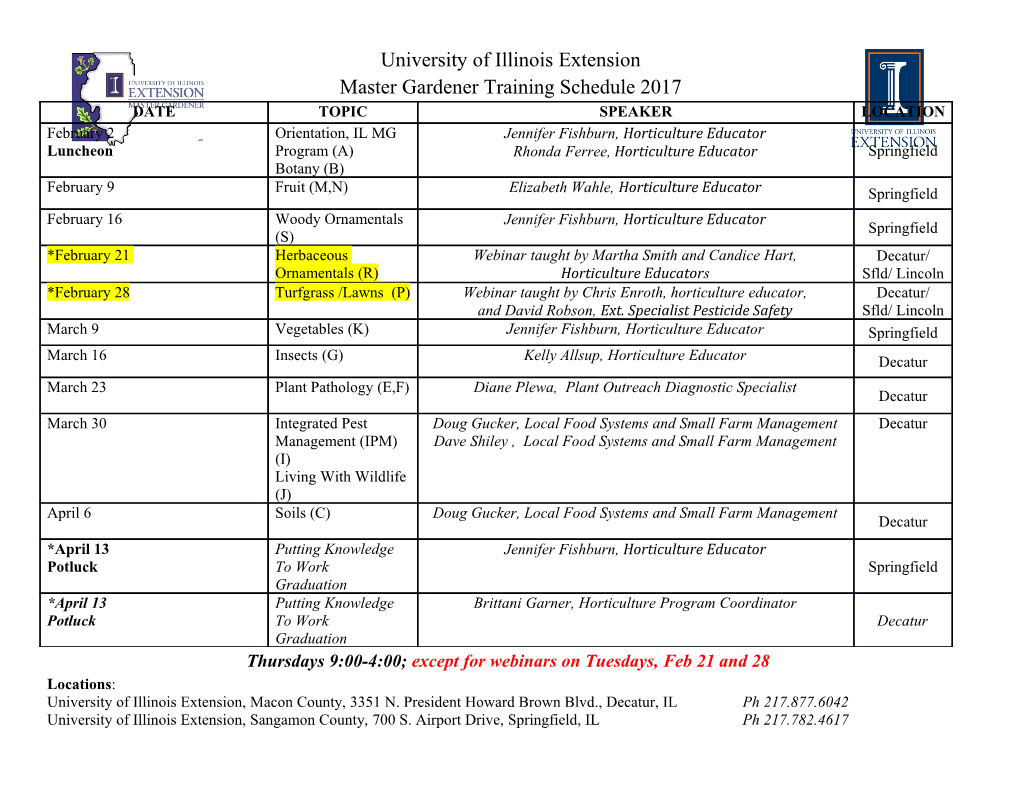
This article has been accepted for inclusion in a future issue of this journal. Content is final as presented, with the exception of pagination. INVITED PAPER Practical Issues in the Use of NdFeB Permanent Magnets in Maglev, Motors, Bearings, and Eddy Current Brakes Design guidelines for these magnets in large-scale transit, braking and magnetic bearing applications are discussed, including mechanical and thermal issues. By Marc T. Thompson, Member IEEE À7 ABSTRACT | In this paper, practical design issues related to the o Magnetic permeability 4  10 H/m use of high-strength neodymium-iron-boron magnets are de- of free space. scribed. These magnets have increasing utility in transporta- m Recoil permeability of a H/m tion systems (maglev, linear and rotary motors), bearings, and permanent magnet. in eddy-current brakes. However, careful design must be done r Relative recoil permeability. — to utilize the full capabilities of these magnets. Magnetic wavelength. m 2 Ag Cross-sectional area of m KEYWORDS | Bearings; eddy-current brakes; EDS; electrody- airgap. 2 namic levitation; EMS; Halbach array; linear motors; linear Am Cross-sectional area of m synchronous motor; magnetic circuits; motors; neodymium- permanent magnet. iron-boron (NdFeB); permanent magnets; permeance Bg Airgap magnetic flux T density. Bm Operating point of T NOMENCLATURE permanent magnet flux Item Description Units density. À1 Temperature coefficient C Br Remnant magnetic flux T of Br: density. À1 Temperature coefficient C Bro Remnant magnetic flux T of Hci: density at temperature T: À1 À1 NdFeB Electrical conductivity m D Magnet height. m of NdFeB. fb Braking force generated by N Èm Magnetic flux inside a Weber an eddy current brake. permanent magnet. Fb;max Maximum braking force N < Magnetic reluctance. A-turns/Weber generated by an eddy current brake at vpk: g Airgap length. g Hc Coercive force. A/m Hci Intrinsic coercive force. A/m Manuscript received July 29, 2008; revised February 18, 2009. Hcio Intrinsic coercive force at A/m The author is with Thompson Consulting Inc., Harvard, MA 01451 USA. He is also with the Electrical Computer Engineering Department, Worcester Polytechnic Institute, temperature T: Worcester, MA 01609 USA (e-mail: [email protected]; [email protected]). Hm Magnetic field inside a A/m Digital Object Identifier: 10.1109/JPROC.2009.2030231 permanent magnet. 0018-9219/$26.00 Ó2009 IEEE Vol. 97, No. 11, November 2009 | Proceedings of the IEEE 1 Authorized licensed use limited to: Worcester Polytechnic Institute. Downloaded on October 27, 2009 at 09:27 from IEEE Xplore. Restrictions apply. This article has been accepted for inclusion in a future issue of this journal. Content is final as presented, with the exception of pagination. Thompson: Use of NdFeB Permanent Magnets in Maglev, Motors, Bearings, and Eddy Current Brakes lm Length of permanent m magnet. lp Magnetic path length in m steel. N Number of blocks per — wavelength in Halbach array. Nlam Number of laminations. — v Linear velocity. m/s vpk Velocity at which force m/s peaks in an eddy current brake. I. INTRODUCTION The year 2008 marked the twenty-fifth anniversary of the introduction of sintered neodymium-iron-boron (NdFeB) magnets. In 1983, this new generation of rare-earth magnet was introduced and patented independently by Sumitomo Special Metals and General Motors (later Magnequench). Sumitomo and Magnequench later cross- licensed their patents. In subsequent years, the NdFeB divisions of GE and Sumitomo were bought and sold sev- eral times; the current incarnations are Neomax (a 2003 merger of Hitachi and Sumitomo Specialty Metals) and the Magnequench division of AMR Technologies, which be- came Neo Material Technologies in 2005. Fig. 1. Construction of a load line in a circuit containing a NdFeB In the past 20 years or so, significant improvements magnet and steel. (a) Characteristic demagnetization B/H curve of have been made in the magnetic strength and thermal the magnet. (b) A magnetic circuit containing a permanent magnet, stability of these permanent magnet materials [1]–[6], high-permeability steel, and an airgap. (c) Load line showing operating point of the permanent magnet. opening up new applications in large-scale systems such as motors, bearings, maglev, and eddy-current brakes, as well as other transportation applications such as hybrid vehi- Material parameters (which are further discussed in cles. A key figure of merit is the maximum energy product, following sections) are the coercive force (H ,withunits given in megagauss-oersteds (MGOe), but equally impor- c of A/m) and remnant flux density (B ,withunitsofT).The tant are the issue of thermal stability and the resistance of r permanent magnet constrains the operating point ðB ; H Þ the permanent magnets to demagnetization. Currently, m m of the magnet to be somewhere on the line shown. By NdFeB with maximum energy product of greater than constructing a load line by analyzing the external circuit 50 MGOe is commercially available [7]. NdFeB is replac- surrounding the magnet, we can predict the operating ing samarium cobalt (SmCo) and alnico in many applica- point of the magnet at the intersection of the magnet B/H tions, but for very high-temperature applications, SmCo is curve with the load line. still a competitor to NdFeB. This paper focuses on the use We will consider the magnetic circuit of Fig. 1(b). of high-strength NdFeB magnets in large-scale applica- The permanent magnet has length l and cross-sectional tions where temperatures are modest and describes some m area A and is wrapped with high-permeability steel. The of the design challenges unique to NdFeB design, m steel has magnetic path length l , and an airgap of length including specifically mechanical and thermal design p g is also shown. Using Ampere’s law around the dashed issues. path (and noting that our approximation of infinite per- meability assures that magnetic field H ¼ 0inthesteel), II. ANALYTICAL APPROXIMATE we note MODELING OF NdFeB SYSTEMS Hmlm þ Hgg ¼ 0(1) A. Use of Ampere’s and Gauss’ Laws and Load Line An NdFeB magnet has the characteristic B/H curve shown in Fig. 1(a), where Bm is the flux density inside the where Hg is the magnetic field in the airgap. Next we use magnet and Hm is the magnetic field inside the magnet. Gauss’ magnetic law, which says that flux is continuous 2 Proceedings of the IEEE |Vol.97,No.11,November2009 Authorized licensed use limited to: Worcester Polytechnic Institute. Downloaded on October 27, 2009 at 09:27 from IEEE Xplore. Restrictions apply. This article has been accepted for inclusion in a future issue of this journal. Content is final as presented, with the exception of pagination. Thompson: Use of NdFeB Permanent Magnets in Maglev, Motors, Bearings, and Eddy Current Brakes around a loop, to get BmAm ¼ BgAg (2) where Ag is the cross-sectional area of the airgap. Noting that the airgap flux density Bg ¼ oHg, we next solve for Bm as a function of Hm,resultingintheloadline equation lmAg Bm ¼o Hm: (3) gAm WeplottheloadlineonthemagnetB/Hcurveresulting in Fig. 1(c). We see the intuitive result that the operating point of the magnet is at a higher Bm if the magnet is longer or if the airgap is smaller. Conversely, if the airgap grows, the magnetic flux density produced by the magnet is lower and the airgap flux density is lower. The magnetic flux density predicted by the load-line Fig. 2. Magnetic circuit modeling of a permanent magnet. method, and following methods, is approximate and (a) Geometry of a permanent magnet. (b) Magnetic circuit model of should be used with care. a permanent magnet. (c) Closed magnetic circuit with steel and an airgap. (d) The magnetic circuit model. B. Magnetic Circuits Rough order-of-magnitude modeling of the amplitude of the magnetic field produced by a high-strength mag- Next, we approximate the magnet flux density ðÈmÞ and net can be done by using magnetic circuit modeling in airgap flux Bg as cases where airgaps are relatively small. Using magnetic circuit modeling, magnetomotive force (MMF) is anal- ðÈÞ Hclm ogous to voltage, flux is analogous to current, and Èm the proportionality constant relating MMF and flux is <m þ<1 þþ<2 þ<3 þ<g þ<4 þ<5 þ<6 magnetic Breluctance.[ The magnetic circuit model of a Èm Bg (6) permanent magnet [Fig. 2(a)] of length lm and cross- Ag sectional area Am is shown in Fig. 2(b). The MMF source is Hclm,whereHc is the coercive force of the magnet. The magnetic reluctance inside the magnet is where Ag is the cross-sectional area of the airgap. Note that given by this is an approximate method, which ignores leakage flux and three-dimensional (3-D) end effects, but is useful for generating rough estimates of flux density. The reluctances lm of leakage paths can be approximated by adding other <m ¼ (4) mAm reluctances to the circuit model [8], [9] to model flux leakage through the air. where m o is the recoil magnetic permeability of the C. Method of Images permanent magnet material. We can use the method of images to simplify the anal- A closed magnetic circuit is shown in Fig. 2(c), where ysis of structures containing permanent magnets where we see a permanent magnet, steel (with six labeled legs), there are magnet–steel interfaces. Referring to the struc- and an airgap. Using magnetic circuit analysis, we replace ture of Fig. 3(a), we see a permanent magnet of length lm each leg and airgap with reluctances of value attached to a piece of steel with high magnetic perme- ability. The boundary condition at the plane defining the magnet–steel interface is that the magnetic field is Path length perpendicular to the steel, assuming that the magnetic <¼ (5) ðÞðCross-sectional areaÞ: permeability of the steel is much higher than that of free Vol.
Details
-
File Typepdf
-
Upload Time-
-
Content LanguagesEnglish
-
Upload UserAnonymous/Not logged-in
-
File Pages10 Page
-
File Size-