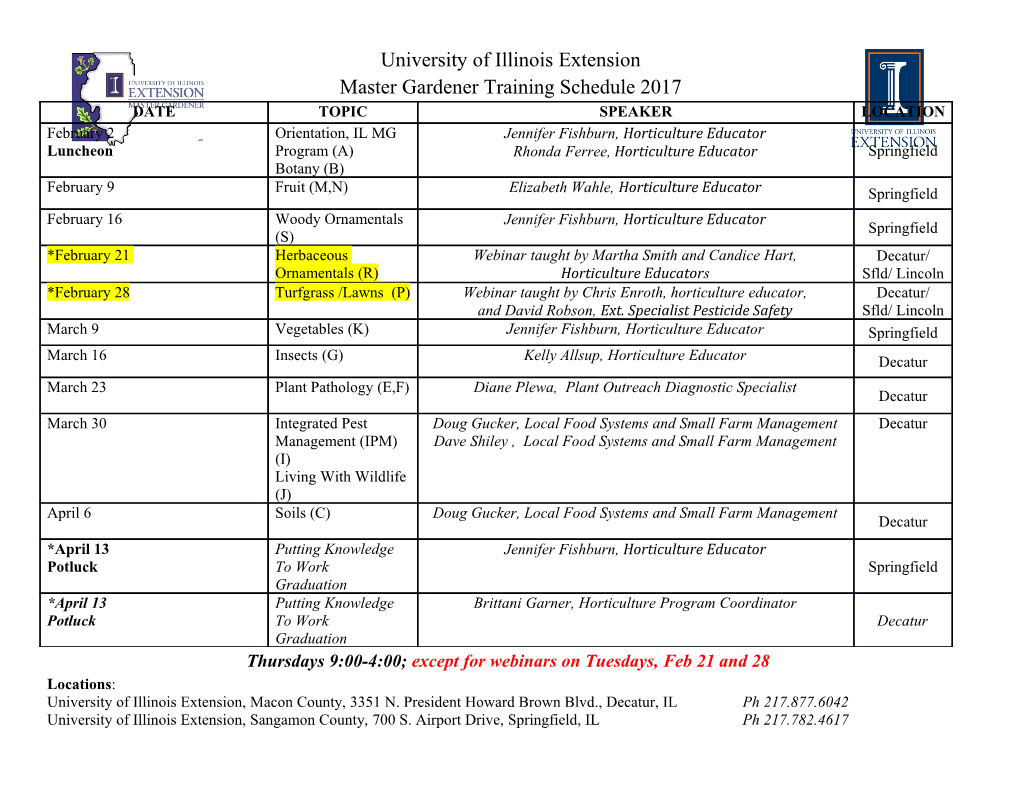
INL/EXT-08-14017 Evaluation of Aqueous and Powder Processing Techniques for Production of Pu-238-Fueled General Purpose Heat Sources Mark Borland Steve Frank Paul Lessing Dennis F. Bickford Roger Cannon Ken Chidester Tom Wheeler Brian Cowell Brad Patton John Brown Jeff Huling Andrew Duncan Linda Seward William West June 2008 The INL is a U.S. Department of Energy National Laboratory operated by Battelle Energy Alliance INL/EXT-08-14017 Evaluation of Aqueous and Powder Processing Techniques for Production of Pu-238 Fueled General Purpose Heat Sources Mark Borland Steve Frank Paul Lessing Dennis F. Bickford1 Roger Cannon1 Ken Chidester1 Tom Wheeler1 Brian Cowell2 Brad Patton2 John Brown3 Jeff Huling3 Andrew Duncan4 Linda Seward – Facilitator William West – Facilitator 1Consultant 2ORNL 3LANL 4SRNL June 2008 Idaho National Laboratory Space Nuclear Systems and Technologies Idaho Falls, Idaho 83415 http://www.inl.gov Prepared for the U.S. Department of Energy Office of Nuclear Energy Under DOE Idaho Operations Office Contract DE-AC07-05ID14517 DISCLAIMER This information was prepared as an account of work sponsored by an agency of the U.S. Government. Neither the U.S. Government nor any agency thereof, nor any of their employees, makes any warranty, expressed or implied, or assumes any legal liability or responsibility for the accuracy, completeness, or usefulness, of any information, apparatus, product, or process disclosed, or represents that its use would not infringe privately owned rights. References herein to any specific commercial product, process, or service by trade name, trade mark, manufacturer, or otherwise, does not necessarily constitute or imply its endorsement, recommendation, or favoring by the U.S. Government or any agency thereof. The views and opinions of authors expressed herein do not necessarily state or reflect those of the U.S. Government or any agency thereof. EXT-08-14017 EXECUTIVE SUMMARY This report evaluates alternative processes that could be used to produce Pu-238 fueled General Purpose Heat Sources (GPHS) for radioisotope thermoelectric generators (RTG). Fabricating GPHSs with the current process has remained essentially unchanged since its development in the 1970s. Meanwhile, 30 years of technological advancements have been made in the fields of chemistry, manufacturing, ceramics, and control systems. At the Department of Energy’s request, alternate manufacturing methods were compared to current methods to determine if alternative fabrication processes could reduce the hazards, especially the production of respirable fines, while producing an equivalent GPHS product. An expert committee performed the evaluation with input from four national laboratories experienced in Pu-238 handling. The objectives of the evaluation are: Objective 1: Minimize the potential for airborne radioactive contamination release during fabrication. Objective 2: Reduce personnel radiation exposure during fabrication. Objective 3: Reduce cracking of the unclad pellets while satisfying impact tests and operating performance requirements. The process alternatives assume an aqueous feed stream of purified Pu-238 nitrate solution and produce an unclad GPHS pellet that meets all material and performance specifications. Thus, the scope of the evaluation specifically did not consider (a) heat generation from isotopes other than Pu-238, (b) alternate heat source geometries, and (c) other fuel matrices. For this evaluation, the process steps were grouped into two subprocesses—production of green granules and pellet production. The current process consists of 10 distinct processing steps. Current granule production includes: (1) oxalate precipitation/filtering/drying, (2) oxide conversion, (3) O-16 exchange, (4) comminution through ball milling, (5) cold pressing, (6) granulation, and pellet production includes: (7) granule seasoning, (8) charge blending and die loading, (9) hot pressing, and (10) sintering. The committee utilized professional judgment and reviewed literature to identify alternative processes that could be used to produce granules or pellets. The committee met April 21-24, 2008, in Idaho Falls, Idaho, to evaluate and prioritize these processes. The evaluation was hindered by the lack of available information on some of the processes. Many of the processes have not been investigated with Pu-238, preventing selection of a single alternative. A weighted set of evaluation criteria was developed considering hazard minimization, process simplicity, process control, chemical purity, and technical risk. Based on the committee’s expertise, the list of process alternatives was winnowed to a small number that warrant further testing as shown in the table below. Granule Production Methods Pellet Production Methods Precipitation methods Hot pressing methods x Improved oxalate precipitation x Improved hot pressing and sintering x Hydroxide precipitation x Spark plasma sintering x Granat flocculation x Superplastic forming x Ammonium plutonyl carbonate precipitation Alternate granule methods Alternate pressing methods x Modified direct denitration x Preforming and pressureless sintering x Sol-gel microsphere x Resin bead loading and calcination v EXT-08-14017 The committee considered pairing the granule and the pellet production processes to define an optimum integrated process, but determined that most of the granulate processes would work with any of the pellet production processes. The committee developed the following findings and recommendations. Finding 1 – The existing product specifications are essentially process specifications. Physical characteristics of the GPHS product are not specifically measured and controlled. Rather, the fabrication process and operating parameters are tightly controlled to ensure consistency between new batches and the original product, and thus tie to the flight-qualification database. The physical characteristics require additional research if the reference process is to be modified. Finding 2 – Several processes potentially can achieve the objectives. The preferred granule and pellet process alternatives are (a) the improved oxalate precipitation granule production and (b) the improved hot pressing pellet production. Finding 3 – Other alternative processes entail higher risk but offer potentially higher rewards. Further reduction in dust generation, simpler operations and improved stress distributions may be achieved. Recommendation 1 – Characterization should be performed on the current LANL Pu-238 process to document the physical characteristics of GPHS in-process material and final products as soon as possible. Recommendation 2 – Final selection of a new Pu-238 process should be based on (1) test results from cold surrogate, Pu-239 surrogate, and Pu-238 testing, (2) optimized process parameters that produce the most repeatable product with the highest quality and (3) ability to produce GPHS pellets that can be readily qualified for space flight. The committee therefore recommends a staged test program, eliminating at each stage any processes that do not warrant further consideration. Recommendation 3 – Investigate the processes identified in the table. Approximately $5 M over a two year period is needed for university/laboratory studies to complete initial cold surrogate testing. Funding would be used to conduct literature reviews, to perform testing, including impact testing, to answer key technical uncertainties; and to further downselect alternatives. Recommendation 4 – Prepare for Pu-239 and follow-on Pu-238 testing of the preferred alternatives following down selection of process alternatives. These preparations will require a year or more and can be performed in parallel with surrogate testing. The figure below depicts a timeline for selecting a final Pu-238 GPHS fabrication process and qualifying the new process for space flight. Phase I Phase II Hot Testing Phase-III Cold Test Phase II-A Phase II-B Flight Qualification ( 18 months ) ( 12 months ) ( 12 to 24 months ) ( 12 months ) Characterization of current GPHS process Granule Production Input to granule requirements Precipitation tests Alternate granule tests Feedback loop Pellet Production Initial granules ready for pressing Hot pressing tests Alternate pressing and sintering tests Impact tests Cold impacts Hot impacts Downselect evaluations Downselect evaluation Final downselect Preparation for Phase-II testing Prep for Phase II-A Prep for Phase II-B This report is the consensus of the evaluation committee and the four concerned DOE laboratories: Idaho National Laboratory, Los Alamos National Laboratory, Oak Ridge National Laboratory and Savannah River National Laboratory. vi EXT-08-14017 CONTENTS EXECUTIVE SUMMARY .......................................................................................................................... v ACRONYMS.............................................................................................................................................. xv 1. PURPOSE/OBJECTIVE .................................................................................................................1-1 1.1 Scope.....................................................................................................................................1-2 2. BACKGROUND.............................................................................................................................2-1 2.1 Fuel Forms ............................................................................................................................2-1
Details
-
File Typepdf
-
Upload Time-
-
Content LanguagesEnglish
-
Upload UserAnonymous/Not logged-in
-
File Pages222 Page
-
File Size-