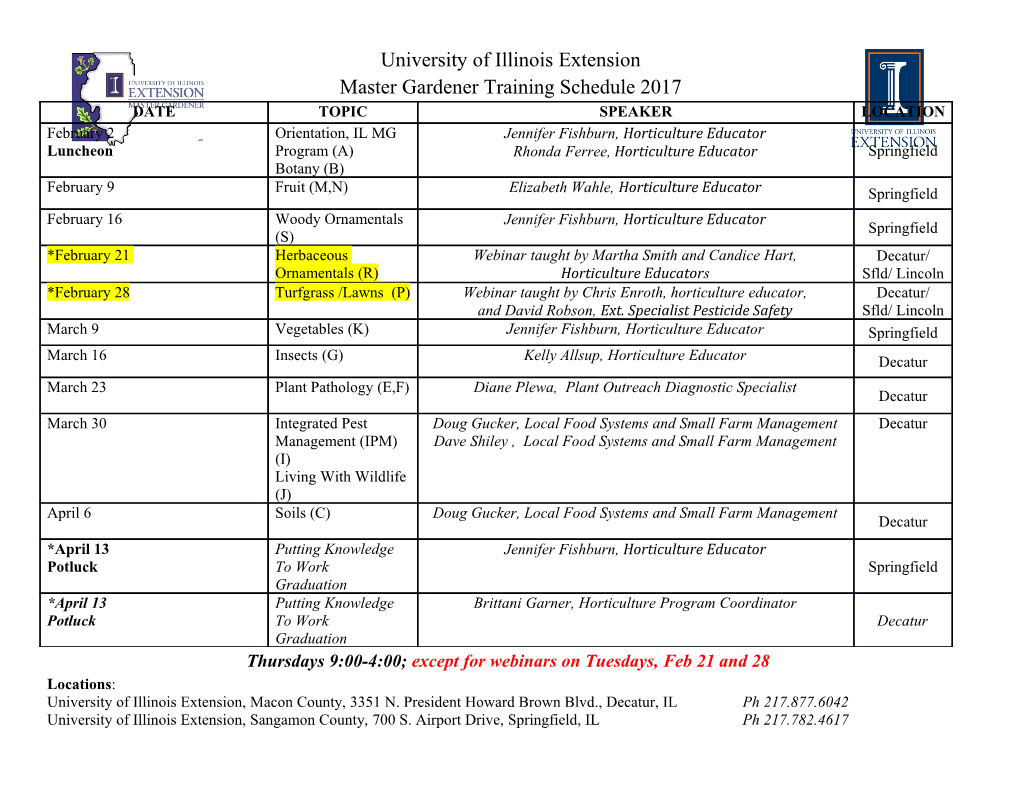
specifications On-Board Imager Confidence in tumor targeting On-Board Imager Confidence in tumor targeting The On-Board Imager® (OBI) kV imaging system is a high-resolution, low-dose digital imaging system that allows users to confidently manage patient and target movement – both before and during treatments, with three modes of kilovoltage (kV) imaging: digital radiographic, cone-beam CT (CBCT), and fluoroscopic imaging. Optimized Positioning Ideal for Dynamic Targeting IGRT The On-Board Imager consists of a kV X-ray source The On-Board Imager makes Dynamic Targeting® and an amorphous silicon panel that can be mounted image-guided radiation therapy (IGRT) more efficient on the Clinac® iX linear accelerator and the Trilogy® and convenient. Once a patient is set up, all system. It is attached by robotically controlled arms subsequent imaging activities can be performed that operate with three axes of motion, optimizing remotely, generating a smooth, convenient clinical the position of the imaging equipment for the best process. The combination of robotic technology and possible view of a target. integrated software control of all treatment parameters offers the automation, speed, and flexibility needed to Versatile Imaging make the IGRT process clinically practical. With the On-Board Imager, you can obtain kV images, adjust A versatile device, the On-Board Imager enables on- patient positioning as needed, and complete the line patient repositioning by visualizing bony anatomy treatment, all within the standard treatment time. or radiopaque markers in pairs of radiographs – or by visualizing soft-tissue and bony anatomy in cone-beam CT images. When used in conjunction with the Varian Real-time Position Management™ (RPM) system, the On-Board Imager enables fluoroscopic pretreatment gating verification and gated radiographic anatomic image matching. And, in combination with the Varian PortalVision™ MV imaging system, the On-Board Imager allows for filmless acquisition of MV and kV radiographic pairs without gantry rotation, essentially speeding up the acquisition process. Specifications* 2.6 Cooling – Housing (maximum) With oil cooling: 162,000 HU/min (2000 W) 1.0 Imager Without oil cooling: 18,000 HU/min (222 W) The imager is a high-performance, high frame rate aSi 2.7 Source spot digital imager designed for kilovoltage operation. Small: 0.4 x 0.6 mm2 1.1 Model: PaxScan® 4030CB flat panel detector Large: 0.8 x 1.1 mm2 1.2 Maximum pixel matrix: 2048 x 1536 2.8 Focal spot superimposition 1.3 Array area: 397 mm x 298 mm X axis: ±0.35 mm 1.4 X-ray detector material: CsI:Tb Z axis: ±0.0 mm 1.5 Maximum frame rate: 15 fps 1.6 Dynamic range: 18,400:1 3.0 X-ray Collimation 1.7 Grid: 10:1 with >70% transmission The X-ray collimation is comprised of a fixed primary (per IEC 60627) beam definer and an adjustable blade collimation system. Symmetric and asymmetric field openings as 1.8 Operating modes well as remote adjustments are supported by the blade 1.8.1 Digital radiography – high quality collimation system. 2048 x 1536 (1 x 1 binning) 3.1 Primary beam definer Readout time: 66 ms Thickness: 20 mm Pb 1.8.2 Fluoroscopy Opening: 50 x 50 cm2 at 1 m 1024 x 768 (2 x 2 binning) 3.2 Adjustable collimator 15 fps Blade thickness: 3 mm Pb supported by 2 mm 1.8.3 Dual gain steel 1024 x 1536 with electronic gain X-ray source to top of upper blades: 91 mm adjustments between each readout line X-ray source to top of lower blades: 107 mm Reformatted to 1024 x 768 Range of motion of each blade: -3 cm to 25 cm 11 fps (maximum 15 fps) (defined at isocenter) 2 2.0 kV Source/X-ray Tube Minimum field opening: 2.5 x 2.5 cm 2 The X-ray source is a general purpose rotating anode Maximum field opening: 50 x 50 cm X-ray source designed for radiographic, fluoroscopic, Reproducibility: ±2 mm (Assumes stationary and pulsed fluoroscopic operation. gantry) 2.1 Model: Varian G242 3.3 Adjustable collimator features 2.2 Anode diameter: 100 mm Symmetrical and asymmetrical field openings 2.3 Target angle: 14° Field opening follows the detector (blade 2.4 Heat capacity tracking) Anode: 600,000 HU (445 kJ) Remote adjustments of field opening Housing: 2,000,000 HU (1480 kJ) Operator (manual) entry of blade settings (X1, X2, Y1, Y2) on OBI workstation 2.5 Cooling - Anode 162,000 HU/min (2000 W) @ 100% anode 4.0 Generator heat storage 4.1 Generator power: 32 kW 81,000 HU/min (1000 W) @ 80% anode heat storage * Applies to OBI Advanced Imaging; Release 1.5 page 4 Varian On-Board Imager specifications Table 1: Generator Operating Ranges*,** Operating Range Radiographic CBCT*** Fluoroscopy*† X-ray Voltage (kVp) 40 – 150 60 – 140 40 – 125 X-ray Current (mA) 10 – 320 10 – 80†† 10 – 40†/ 10 – 80†† Exposure Time or Pulse Length (ms) 2 – 6300 2 – 32 2 – 32††† Exposure (mAs) 0.5 – 630 Defined by CBCT mode N/A * Uncertainties for all quantities ± (5% + 1 unit) ** Combinations of kVp, mA, and ms that can be set simultaneously are limited by the tube characteristics. *** Pulsed operation (11 pulses/s) *† Pulsed operation (15 pulses/s) † Small focal spot †† Large focal spot ††† Limited to 2-8 ms in Japan 4.2 Generator reproducibility 5.4 Grayscale linearity The X-ray generator output complies with the The On-Board Imager is capable of displaying requirements set by the CDRH for eleven uniform shades of gray (from black to reproducibility, which states that the estimated white) using the Nuclear Associates 07-456, or a coefficient of variation for the radiation output Leeds GS2 step wedge penetrometer. must be ≤3.5%. 5.5 Automatic brightness control (ABC) 4.3 Generator linearity ABC controls kVp only in pulsed digital For linearity, the average ratios of mR output as fluoroscopy imaging mode. The ABC will indicated by the exposure delivered (mAs) maintain a constant dose rate to the imager while obtained at any two consecutive mA station imaging the variable-density phantom. While in settings at the same kVp shall be within the ABC mode, kVp reproducibility is within ±2 specification defined ≤8%. kVp, when approached from either maximum or minimum kVp using the step wedge 5.0 Imaging Chain Overall Performance penetrometer as a variable density phantom. The 5.1 Half value layer (HVL) response time for kVp stabilization on an image The half value layer as a function of tube is ≤3 seconds. potential and the total filtration for diagnostic X- 5.6 Typical radiographic exposures ray units are published in CFR, volume 21, µGy/mAs @ 75 kVp = 57 1020.30, paragraph ‘M,’ table 1. For 100 kVp, the minimum HVL is equivalent to 2.7 mm of µGy/mAs @ 100 kVp = 98 aluminum (Al). For 70 kVp, the minimum HVL µGy/mAs @ 125 kVp = 150 is equivalent to 1.5 mm of aluminum. (Measured with the X-ray detector 100 cm from 5.2 Filtration X-ray source; measurement uncertainty ±15%) The X-ray beam path has inherent filtration of 5.7 Low contrast sensitivity 0.7 mm plus 2.0 mm of added Al filtration. Using the Leeds test object type TOR [18FG] or 5.3 Spatial resolution N3, the imager is capable of resolving a With no obstructions in the X-ray beam, the minimum of 2.33% sensitivity when using a spatial resolution of the 4030CB aSi panel is: technique of 75 kVp; 50 mA; 6 ms (2 x 2 binning; 15 fps). • 1.29 lp/mm (2 x 2 binned mode) Skin exposure (@ 100 cm): 213 µGy/s • 2.58 lp/mm (1 x 1 binned mode) Detector exposure (@ 140 cm; 1 mm Cu filtration): 4.5 µGy/s page 5 Varian On-Board Imager specifications Table 2: Exact Arm Motion Ranges Motion kVD Arm kVS Arm Vertical* @ Beam Axis -2 / +80 -80 / -100 Lateral** -18 / +16 N/A Longitudinal*** @ Isocenter -4 / +5 -7 / +45 Longitudinal 30-50 cm Below Isocenter -20.5 / +24 N/A Longitudinal 77 cm Below Isocenter -19 / +24 N/A * “Vertical” motion: Motion toward or away from the MV beam path ** “Lateral” motion: Motion parallel to the path of the MV beam *** “Longitudinal” motion: Motion away from or towards the gantry 6.0 Mechanical Specifications – Exact® Arms 6.5 Arm controls The Exact arms are fully motorized assemblies that 6.5.1 Hand pendant support and position the image detector unit and kV When in the treatment room, the arms source used with the On-Board Imager. The Exact are controlled by an infrared hand arms offer fully automated motion from either inside pendant, powered by a rechargeable the treatment room or remotely from the control battery. There are five preset target console. All arm motion is fully motorized, with a positions and the arms can be controlled separate drive assembly for each arm part: hand, individually, as a pair (OBI) or all arms forearm, and upper arm. There is also a separate at once (OBI plus PortalVision arm). assembly for hand lateral motion on the image 6.5.2 On-Board Imager console detector support arm. Each motorized joint has active servo feedback control to assure the arm When at the treatment control room, reaches/maintains the desired position, regardless of the OBI console provides the following gantry angle. remote motion capabilities: 6.1 Arm motion velocities • Motion enable button Retracted to deployed: 21 or 23 s* • Retract MV arm Mid to deployed: 11 or 13 s* • Retract kV arms 6.2 Arm position accuracy: ±2 mm • Auto go MV arm 6.3 Arm position reproducibility: ±0.5 mm • Auto go kV arms 6.4 Collision detection • Out kV arms kV source rear cover 6.6 Emergency features kV source face plate cover There is a backup motion control in case the Exact arm or its controller becomes defective or kV detector cover when communication with the hand pendant kV source and detector arms cannot be established.
Details
-
File Typepdf
-
Upload Time-
-
Content LanguagesEnglish
-
Upload UserAnonymous/Not logged-in
-
File Pages12 Page
-
File Size-