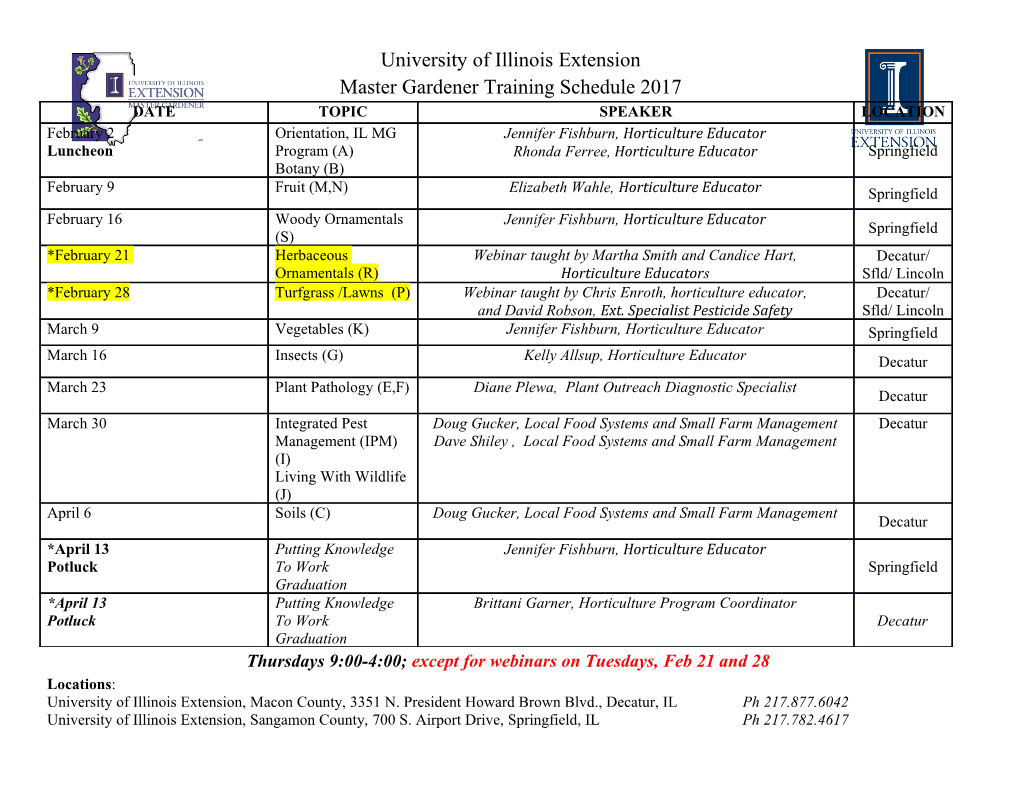
Chapter 2. Laminate theory 9 Chapter 2 Laminate Theory This chapter aims to give a brief description of the type of mechanical analysis applied to determine the behaviour of the proposed structure which is made up of laminate composite panels. The analysis includes the fundamentals required to understand the mechanical behaviour of a deformable solid through the application of the theory of elasticity. From here the elastic behaviour of the composite material is described through stress-strain relations and visa versa , in terms of its engineering constants from a three dimensional state to the more representative two-dimensional state of the composite plate. The effects of ply orientation are examined with corresponding transformations between principal axis and orientated coordinates outlined and their subsequent application and relevance in the project mentioned. The analysis determines the conditions required to be met by the laminas so as to constitute a laminate. If the laminas meet the conditions required, the classical theory outlined can be appropriately applied to the laminate. The theory attempts to find effective and realistic simplifying assumptions that reduces the three dimensional elastic problem to a two dimensional one. It determines the response of the laminate to forces and moments acting on the laminate by applying the hypothesis of thin laminates where a number of deformed geometrical occurrences are assumed. Finally, other types of mechanical behaviour are outlined in this chapter. These behaviours are considered worthy in presenting for discussion as they are directly related to the project in terms of geometry and service conditions. These topical mechanical behaviours include the presence of holes in laminates, vibration and fatigue. 2.1. Elastic Theory Composite materials, as with all deformable solids, change shape at different points of the material when a system of external loading is applied on the solid in equilibrium, giving rise to a new geometric or deformed configuration. Figure 2.1 shows a deformable solid subjected to the application of a system of forces indirectly where external loading is applied on some arbitrary zones of the solid’s boundary but with limited displacement in another zone which generates forces necessary to equilibrate the external applied system. Chapter 2. Laminate theory 10 The physical magnitudes that are incurred in the deformation of a solid are the external loading: applied in the body Xi and/or on the boundary ti. The second type of physical magnitudes is the displacements ui of the body. The objective of the mechanical behavioural analysis of a deformable solid is to determine its displacement when external loading is applied. However, the solid’s displacement cannot be determined directly from the applied external loading. It is therefore necessary to define internal variables that are related to the physical magnitudes in equilibrium, these include the stresses σij and strains εij of the deformable solid. Figure 2.1 represents the elastic problem in terms of its forces, displacements, stresses and strains. Given that the stresses are related to the external loading, the same as the strains are related with displacements and given the relation between the displacements and the loads, it must exist a material relation between the stresses and the strains. This material relation is known as the Behavioural Law or the constitutive equations of the material. Figure 2.1: The problem of deformable solids Analysing the elastic problem in the above figure, the relation between the exterior loads Xi and ti (i =1,2,3) and stresses σij (i, j = 1,2,3) are the equations of internal equilibrium. σ + = (2. 1) , jij X i 0 σ = (∂ ) (2. 2) n jij ti Dt Between displacements εij (i, j = 1,2,3) and strains are the equations of compatibility. 1 (2. 3) ε = ()u + u ij 2 , ji ,ij Chapter 2. Laminate theory 11 = (∂ ) (2. 4) ui ui Du Between the stresses and strains are the constitutive equations or the Behavioural Law. σ = ε + λε δ (2. 5) ij 2G ij ijkk + ε = 1 vσ − v σ δ ij ij ijkk (2.6) E E The elastic problem is therefore made up of a system of 15 differential equations which include three equilibrium equations, six strain-displacement relations, and six constitutive equations. In total, there are 15 unknowns, made up of six components from the stress tensor, six from the strain tensor and three displacements [4]. 2.2. Elastic Material Behaviour In Composite Materials 2.2.1. Stiffness Matrix C The generalised Hooke's Law relating stresses to strains can be written as the following expression σ = C .ε (2.7 ) i ij j Where σi are the stress components, Cij is the stiffness matrix, and εj are the strain components. The stress-strain relationship and the corresponding stiffness matrix for the anisotropic or triclinic (no planes of symmetry for the material properties) linear elastic case are shown below. σ ε 11 C11 C12 C13 C14 C15 C16 11 σ ε 22 C21 C22 C23 C24 C25 C26 22 σ C C C C C C ε 33 31 32 33 34 35 36 33 = (2.8) σ C C C C C C 2ε 23 41 42 43 44 45 46 23 σ C C C C C C 2ε 13 51 52 53 54 55 56 13 σ ε 12 C61 C62 C63 C64 C65 C66 2 12 where the stiffness matrix itself is symmetric, implying that only 21 of the 36 are independent elastic constants. According to the material type, different extents of symmetry of material properties occur and subsequent reduction in the number of elastic constants in the stiffness matrix is observed. One of such is the stiffness matrix shown below which describes the case of Chapter 2. Laminate theory 12 the stress-strain relations in coordinates aligned with the principal material directions i.e., the directions that are parallel to the intersections of the three orthogonal planes of the material property symmetry. This matrix defines an orthotropic material which is fundamental in the composite analysis in this project. It is important to note also that orthotropic materials can exhibit apparent anisotropy when stressed in non-principal material coordinates [3]. σ ε 11 C11 C12 C13 0 0 0 11 σ ε 22 C21 C22 C23 0 0 0 22 σ C C C 0 0 0 ε 33 31 32 33 33 = (2.9) σ 0 0 0 C 0 0 2ε 23 44 23 σ 0 0 0 0 C 0 2ε 13 55 13 σ 0 0 0 0 0 C 2ε 12 66 12 2.2.2. Compliance Matrix S For ease of resolving the elastic material behaviour we define the inverse of the previous stress- strain relation such that ε = σ (2.10 ) i S ij . j where Sij is the compliance matrix which contains more reduced expressions of the elastic constants. The complete 6x6 compliance matrix is given as ε σ 11 S11 S12 S13 S14 S15 S16 11 ε σ 22 S21 S22 S23 S24 S25 S26 22 ε σ 33 S31 S32 S33 S34 S35 S36 33 = (2.11) γ S S S S S S σ 23 41 42 43 44 45 46 23 γ S S S S S S σ 13 51 52 53 54 55 56 13 γ σ 12 S61 S62 S63 S64 S65 S66 12 For an anisotropic material, there exists a significant coupling effect between the applied stress and the resulting deformation. The types of coupling for above the strain-stress expression are shown in figure 2.2. S11 , S22 and S33 represent the coupling due to the individual applied stresses σ1, σ2 and σ3, respectively, in the same direction. S44 , S55 and S66 represent the shear strain response due to the applied shear stress in the same plane. S12 , S13 and S23 represent the Chapter 2. Laminate theory 13 extension-extension coupling or coupling between the distinct normal stresses and normal strains, also known as the Poisson effect. S 15 , S16 , S24 , S25 , S26 , S34 , S35 and S36 represent the shear-extension coupling or a more complex coupling of the normal strain response to applied shear stress than for the preceding compliances. S45 , S46 and S56 represent shear-shear coupling or the shear strain response to shear stress applied in another plane. The remaining terms of compliance matrix are a result of symmetry [3]. Extension -Extension Coupling ε σ 11 S11 S12 S13 S14 S15 S16 11 Extension Shear -Extension ε S S S S S S σ Coupling 22 21 22 23 24 25 26 22 ε σ 33 S31 S32 S33 S34 S35 S36 33 = γ σ 23 S41 S42 S43 S44 S45 S46 23 Shear -Shear γ S S S S S S σ 13 51 52 53 54 55 56 13 Coupling γ σ 12 S61 S62 S63 S64 S65 S66 12 Shear Figure 2.2: Physical significance of anisotropic stress-strain relations For an anisotropic material, the compliance matrix components in terms of the engineering constants are shown in equation (2.12), using the reduced index notation of Voigt (1910). The values of the compliance matrix can be physically measured by specimen testing. The elastic constants that can be physically measured include Young’s Modulus E, Poisson’s ratio v, shear modulus G, and analytically measured constants include shear-extension coupling or mutual influence coefficients η (Lekhnitskii), and shear-shear coupling coefficients μ (Chenstov). ν ν η η η 1 − 21 − 31 41 51 61 E E E G G G ε 1 2 3 4 5 6 σ 11 ν 1 ν η η η 11 − 12 − 32 42 52 62 ε E1 E2 E3 G4 G5 G6 σ 22 ν ν η η η 22 13 23 1 43 53 63 ε − − σ 33 33 (2.12) = E1 E2 E3 G4 G5 G6 η η η µ µ .
Details
-
File Typepdf
-
Upload Time-
-
Content LanguagesEnglish
-
Upload UserAnonymous/Not logged-in
-
File Pages26 Page
-
File Size-