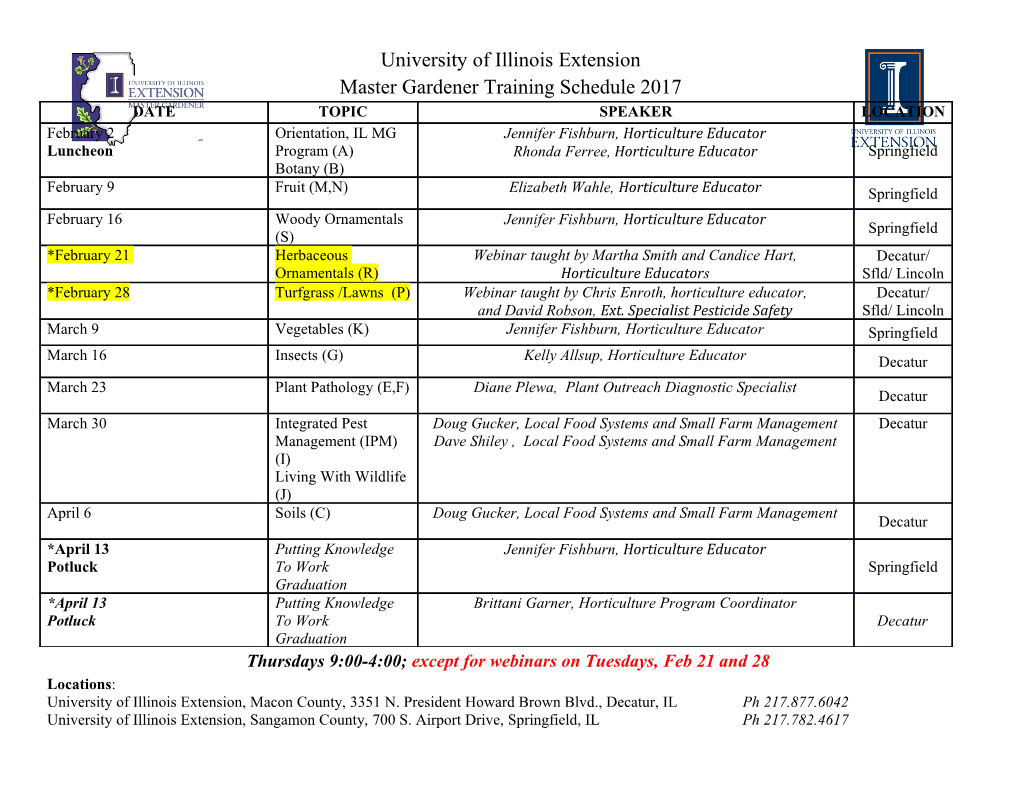
AIAA 93-2415 The RD-170, A Different Approach to Launch Vehicle Propulsion Boris I. Katorgin and Felix J. Chelkis NPO Energomash, Khimky, Russia Charles D. Limerick Pratt & Whitney, West Palm Beach, Florida AlANS A €/AS MWAS E E 29th Joint Propulsion Conference and Exhibit June 28-30, 1993 / Monterey, CA For permisslon to copy or republish, contact the American Instltui. J Aeronautics and Astronautics 370 L'Enfant Promenade, S.W., Washlngton, D.C. 20024 The RD-170, A Different Approach to Launch Vehicle Propulsion 'LJ Boris I. Katorgin' and Felix J. Chelkis** NPO Energomash Khimky. Russia Charles D. Limerick"* Pratt & Whitney West Palm Beach, Florida Abstract Introduction In the early 1960's, the United States and The RD-170 is a mature engine. U.S.S.R. took different paths in developing Development started in 1976 and the first launch vehicle propulsion. The United flight was in 1985. Over 200 engines have States focused on the lower performance been built and over 900 tests accumulating gas generator cycle rocket engine because more than 100,000 sec have been of the less demanding technology involved completed. The RD-170 is a total and the resulting easier development propulsion unit with hydraulics for control process. The U.S.S.R. adopted the high valve actuation and thrust vector control performance staged combustion cycle with gimbaling, pneumatics for valve actuation oxygen rich turbine drive gases and have and purging, and a thrust frame to since striven to perfect that system. The distribute loads all self contained as part of RD-170 is the culmination of over 30 years the engine. The engine was developed to LJ of staged combustion cycle propulsion provide the booster propulsion for the system development. This paper discusses Energia and Zenit launch vehicles. One of the evolution of high pressure the requirements of the Energia application turbomachinery and combustion chamber was reusability, the RD-170 strap-on designs from the RD-253 (the first booster units were intended to be used up operational high pressure staged to 20 times without overhaul or removal combustion rocket engine, introduced in from the booster stage. Hence, along with 1965) to the RD-170. The operating the traditional requirements of high characteristics of the RD-170 will be performance and reliability were reusability explained along with the operability and operability requirements not previously features included as part of the engine demonstrated in rocket engines. It was system. The quality approach used in the required that between flight servicing and manufacturing, component test, and initial flight preparation be accomplished assembly process will be described and the using a minimum of hand operations. unique health monitoring and life prediction system will be unveiled. Potential The engine is the current product of an application of the RD-170 to US. launch engine design philosophy initiated with the vehicle needs has been studied and these RD-253 engine which started development results will also be presented. in the early 1960's. NPO Energomash embarked on a course to develop high General Director and General Designer pressure, staged combustion, oxidizer rich ** Chief Designer turbine drive gas rocket engines, and the ***Manager, SE&I, Russian Programs RD-253 which became operational in 1965 Member AlAA was the first engine of this type. This L, Copyright 0 American Institute of Aeronautics and Astronautics, Inc., 1993. All rights reserved. / engine which operated at over 2000 psia advanced health rnonitoring/life prediction " using the staged combustion cycle was as system. Development of the engine was far in advance of other engines of that initiated in the mid 1970's with the first flight generation as the RD-170 is relative to the occurring in 1985. The quality control current generation of engines. Figure 1 system and specifications were developed shows the chamber pressure versus time from strong requirements close to U.S. characteristics of some representative NPO standards. The extensive NPO Energomash developed engines with the Energomash experience, the 4 chamber US. developed F-I and SSME noted for modular configuration of the engine, and reference. development of a wide range of similar turbopumps of different thrust sizes provides confidence in low risk, low cost development of Derivative Configurations (1 chamber, 2 chamber, uprating, etc.). 4000 The RD-170 engine assembly shown in Figure 2 consists of a single high-pressure 3000 turbopump assembly driven by two Engine preburners, four injector/thrust chamber chamber assemblies, integral fuel and oxidizer boost pressure 2040 pumps, helium bottles for valve actuation 1000 and start and shutdown purging, thrust structure, gimbal actuators, propellant ducting, hypergolic-fuel cartridges, 0 sequencing and control valves, shielding, w- and telemetry systems. 20996A Figure 1 Rocket Engine Development History RD-170 Enqine Characteristics The RD-170 is a high performance lox/kerosene rocket booster propulsion system with operability and reusability features not previously demonstrated on rocket propulsion systems. The engine was designed to provide a minimum of 20 reuses before overhaul and enable lj between flight servicing and initial flight preparation with automated operations. The operability of the RD-170 is a major contributor to the less than 7 day launch timeline of the Zenit launch system. The engine is >IO% higher in performance than other loxlkerosene booster engines and Figure 2 v has a fully developed, operational, RD- 170 Propulsion Assembly 2 The RD-170 is a staged combustion cycle LodKerosene booster rocket propulsion assembly producing 1.6 million Ibs sea level thrust and a sea level impulse of 309 sec at an overall mixture ratio of 2.6 to 1. It has a 2 to 1 throttling range, an assembly dry weight of 26,575 Ibs and overall dimensions of 157.9 inches length and 146 28'JWA inches diameter. The single high-pressure Figure 4 turbopump assembly feeds four identical RD-170 Flow Schematic injector thrust chamber assemblies. Two preburners are used to drive the single The fuel and oxidizer boost pumps are stage turbine with oxidizer rich combustion integrated into the inlet lines and are driven products. with turbine discharge gas (oxidizer) and recirculated fuel (fuel) that reenters the The high pressure turbopump assembly, propellant flow upstream of the high- shown in Figure 3, consists of two rotors pressure pumps. The four injector/thrust connected by a quill shaft. One rotor has chambers are each integrally the turbine and oxidizer pump and the other welded/brazed assemblies with hypergolic the fuel pumps. Both shafts operate with ignition and a combination of film and subcritical rotor dynamics. regenerative cooling (shown in Figure 5). All four injector chamber assemblies can gimbal in two directions or can be limited to -i/ a single direction by installing a fixed link. The linear actuators are powered by fuel- supplied by the high pressure fuel pump. The two parallel preburners are ignited by a unique single-shot hypergolic ignition system. Figure 3 High Pressure Turbopump Assembly All oxidizer flows through the preburners but the fuel is split between the preburners and chambers (fuel cooled). Thrust control is achieved by regulating fuel flow to the 20987A preburners, and mixture ratio by regulating fuel flow to the chambers. An engine flow schematic with only two chambers shown is Figure 5 presented in Figure 4. Injectorflhrust Chamber Assembly 3 Control valve command signals are Table 2 " generated by a vehicle computer running sofhrvare generated during engine RD-170 Characteristics acceptance testing. Heated helium is supplied from the engine for oxidizer tank . Nominal thrust (S.L.) 1,632,000 Ib pressurization. The engine is reusable and . (Vacuum) 1,777,000 Ib over 20 repeat firings have been performed . Specific impulse (S.L.) 309 sec on ground test engines. The health . (Vacuum) 337 sec monitoring system automatically assesses . Chamber pressure 3,560 psia engine health and defines/tracks remaining . Nozzle area ratio 36.4:l engine life. The RD-170 has completed 28 . Mixture Ratio 2.6 flight firings (20 ZENIT and 8 ENERGIA) . Length 157.9 inches and over 900 test firings with an . Diameter (148.8 frame/ accumulated total of over 100,000 146 nozzles) inches operational seconds. Throttle range 50-105 Yo Total system dry weight 26,575 Ibs Table 1 provides a general description of . the RD-170 and characteristics are presented in Table 2. Operability Features Table 1 The RD-170 was designed for operability, RD-170 General Description wherever possible flight preparation, and between flight operations (for reusable w0 Staged combustion cycle engine applications) have been minimized and . LoHkerosene propellants automated. After installation in the vehicle, . 4 thrust chambers (gimbal+W) all engine operations are automated . 2 oxygen rich prebumers through the launch phase. The engine . High pressure turbopump assembly requires minimal preparation for launch as - 2 stage fuel pump shown in Table 3. - single stage oxygen pump - single turbine Hydraulic system (valves, TVC) Interfaces are minimized and there are no powered with kerosene from fuel pump flexible interfaces with the vehicle. The . Hypergolic ignition hydraulics systems for the control valves . Operational certification 1985 and thrust vector control are self contained . 200+ engines produced as part of the engine with hydraulic power . > 100,000 sec and > 900 firings furnished with kerosene from the high . 28 flight firings (December 1992) pressure fuel pump. There are no - 20 Zenit hydraulic interfaces with the vehicle or pad. - 8 Energia . Qualified for 10 mission reusability . Fully developed health monitoring/life prediction system 4 Table 3 be used to provide real time trajectory L/ matching during the boost phase. This RD-170Launch Preparation would enable a significant reduction in avionics programming, significantly At the engine factory before shipping improving the operability of the launch Line closeouts.
Details
-
File Typepdf
-
Upload Time-
-
Content LanguagesEnglish
-
Upload UserAnonymous/Not logged-in
-
File Pages10 Page
-
File Size-