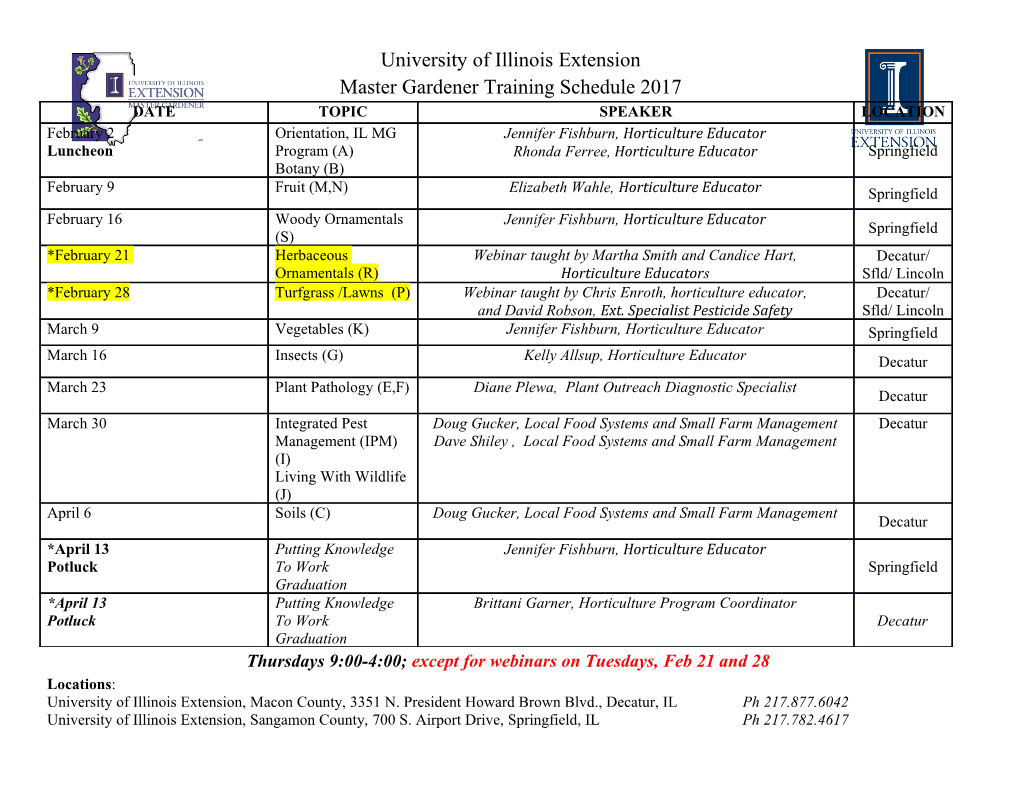
2019 Meat Industry Food Safety Conference Chicago, IL September 4, 2019 A Practitioner’s Reflections on SQC & SPC A Practitioner’s Reflections - On The Use Of SPC/SQC Techniques; or, How much education does a microbiologist, straight out of college, have on the application of SPC/SQC in a manufacturing environment? A Practitioner’s Reflections - On The Use Of SPC/SQC Techniques; or more specifically, why: - Is USDA tagging up my hotdogs? - Are customers complaining? - Is there is so much rework? - Am I addressing the same problem over and over? Statistical Quality Control (SQC) Statistical quality control (SQC) is defined as the application of the 14 statistical and analytical tools (7-QC and 7-SUPP) to monitor process outputs (dependent variables). Statistical Process Control (SPC) Statistical process control (SPC) is the application of the same 14 tools to control process inputs (independent variables). Although both terms are often used interchangeably, statistical quality control includes acceptance sampling where statistical process control does not. ASQ.ORG (2019) 4 SPC SQC Inputs Outputs Raw materials Finished product (lot) Process steps Manufacturer Customer / Consumer Establishment USDA/FSIS, FDA Raw Materials Step 1 Finished Product Step 2 Step # 5 Frederick W. Taylor Promoted “scientific management” principles to significantly increase economic productivity in the factory, by closely observing a production process and then simplifying the process into specific, individualized tasks. Utilizing time and sequential motion studies, autonomy as a “skilled craftsman” was replaced by standard operating procedures conducted by trained workers. “There is always one method and one implement which is quicker and better than any of the rest" “This one implement, then is the adopted as standard in place of the many different kinds before in use and it remains standard for all workmen to use until superseded by an implement which has been shown, through motion and time study, to be still better." Taylor (1911) 6 S I How Many Hogs Can Be D Slaughtered Per Hour? E Pork Industry Wants More B By Julie Creswell, The New York Times – August 9, 2019 The federal government is poised this month to adopt a rule that A would essentially turn the largest pork processing lines in the United States into the autobahn: no speed limit. R Frederick W. Taylor “Close Study of the Process” “There is always one Work / Time Study, by sequence method and one implement which is quicker and better Standard Operating Procedure (SOP) than any of the rest" Emphasis on task specific training Raw Materials Step 1 Finished Product Step 2 Step # 8 Walter A. Shewhart Shewhart identified two categories of variation which he called “assignable‐cause” and “chance‐cause” variation. He devised the control chart as a tool for distinguishing between the two. The various control charts that Shewhart proposed for variables and attributes include mean, range, np, p, c, and u charts. Shewhart reported that bringing a process into a state of statistical control—where there is only chance‐cause (common‐cause) variation—and keeping it in control was needed to reduce waste and improve quality. M Best and D Neuhauser (2006) 9 Shewhart Cycle Dr. Shewhart also is credited with the Shewhart cycle or Shewhart learning and improvement cycle which combines management thinking with statistical analysis. The Plan–Do–Study–Act (PDSA) cycle is used to make changes that lead to improvement in a manner of continuous quality improvement. This is a never ending process. After the easy low cost changes are made (the low hanging fruit harvested), the cycle process is repeated for another step, task, or process in the microsystem or system. M Best and D Neuhauser (2006) 10 W. Edwards Deming Deming championed the work of Walter Shewhart, including statistical process control, operational definitions, and what Deming called the "Shewhart Cycle,“ which had evolved into Plan-Do-Study- Act (PDSA). Deming is best known for his work in Japan after WWII, particularly his work with the leaders of Japanese industry. In 1982, Deming's book Quality, Productivity, and Competitive Position was published by the MIT Center for Advanced Engineering, and was renamed Out of the Crisis in 1986. In it, he offers a theory of management based on his famous 14 Points for Management. ASQ.ORG (2019) 11 Shewhart and Deming Plan Act Do Study (Check) 12 Kaoru Ishikawa Noted for his quality management innovations. He is considered a key figure in the development of quality initiatives in Japan, particularly the quality circle. One of Ishikawa's early achievements contributed to the success of quality circles. The cause-and-effect diagram—often called the Ishikawa diagram and perhaps the achievement for which he is best known—has provided a powerful tool that can easily be used by non- specialists to analyze and solve problems. ASQ.ORG (2019) 13 The 7 Quality Control (7-QC) Tools Dr. Kaoru Ishikawa brought together a collection of process improvement tools in his text Guide to Quality Control. They are known around the world as the seven quality control (7-QC) tools: 1. Cause-and-effect diagram (fishbone or Ishikawa diagram) 2. Check sheet 3. Control chart 4. Histogram 5. Pareto chart 6. Scatter diagram 7. Stratification ASQ.ORG (2019) 14 The 7 Supplemental (7-SUPP) Tools In addition to the basic 7-QC tools, there are also some additional statistical quality tools known as the seven supplemental (7-SUPP) tools: 1. Data stratification 2. Defect maps 3. Events logs 4. Process flowcharts 5. Progress centers 6. Randomization 7. Sample size determination ASQ.ORG (2019) 15 Data Collection PRODUCT INSPECTION REPORT FORM Date ID Name Time Check Sheets: Shift Sample Size 20 20 20 20 20 Critical Defects “A check sheet is a structured, prepared form for collecting 1 and analyzing data. This is a generic data collection and 2 3 analysis tool that can be adapted for a wide variety of Total Criticals purposes.” (ASQ, 2019) Major Defects 1 2 Week Of: MM/DD/YYYY 3a 3b 4 Area M Tu W Th F S 5 6 Zone 1 / / / / / NP 7 +/- 0.2 lbs. variance from weight limits Total Majors Zone 2 / / / / / NP Minor Defects 1 Zone 3 / X X X / NP 2 3 NP Zone 4 X / / / / Total Minors NP Zone 5 / / / X / PRODUCT AQL A n=20 Accept Reject B Limits: Individual Criticals 0 1 Key: / Acceptable X Unacceptable Individual Majors 2 3 Individual Minors 5 6 NP No Production Total Majors 7 8 Understanding the Process via Flow Charts 3. Other variations (often combined with a risk assessment tool) System: Raw Mtrl - Preparation Prepared By: T. Member Failure Mode and Effects Analysis Subsystem: Grinding Date Created: 10/1/2005 Potential Foreign Material Contamination Last Revision Component(s): Grinder; Augers; Blender 11/7/2005 Date: Action Results S Potential Responsibility Potential R E Item / Potential Cause(s) / Current Design Recommended & Target Effect(s) S P D P Actions Taken Function Failure Mode(s) Mechanism(s) Controls Action(s) Completion New D New P Q of Failure N New S of Failure Date New RPN 1 Augers Misaligned auger Metal 3 Fatigue 1 Visual inspection 1 3 PM task W. Next 11/9/06 Implemented Improper assembly; Informal (verbal) SOP for Develop w ritten SOP; w ritten assembly 2 Grinder Knife breaks Metal 7 4 3 84 J. Doe 01/01/06 8 2 2 32 Fatigue assembly Train team members SOP; Trained team members Improper assembly; Informal (verbal) SOP for Develop w ritten SOP; 2 Grinder Plate breaks Metal 8 4 2 64 J. Doe 01/01/06 Fatigue assembly Train team members Install oil sight gage; SOP Hydraulic Seal failure due to 3 Blender Shaft seal failure 4 2 Visual inspection 9 72 to inspect seals and oil W. Next 11/9/06 Oil (H1) fatigue level daily Don't apply high pressure directly to Rubber door Damage during gaskets during 3 Blender gasket drops into Rubber 3 6 Visual inspection 1 18 W. Next 11/9/06 sanitation; Fatigue sanitation; Visual exit auger inspection - replace as necessary 9 CFR 417.2 (a)(2) A flow chart describing the steps of each process …… 1, 2: ASQ (2019) 3: Coble (2019) Control Charts: Shewhart proposed various control charts that for variables and attributes; including mean, range, np, p, c, and u charts. • Were designed for long run, low variation manufacturing processes • Work well for “physical processes” that tend to fit a normal distribution • Phase II Charts assume process is in a state of “statistical control” 18 Traditional Shewhart Control Charts: Shewhart found that the use of three-sigma limits “seems to be an acceptable economic value,” and that the choice of three sigma was justified by “empirical evidence that it works.” (Hunter, 2015) “The control chart does a marvelous job under a wealth of applications. It works.” W. Edwards Deming 19 4 Shewhart 2 Control 4.5 5.5 score og 6.5 0 Charts 7.5 8.5 -2 9.5 10.5 11.5 -4 12.5 I MR 13.5 1 9 17 25 33 41 49 57 65 73 81 89 97 14.5 bser ation 15.5 4 16.5 17.5 18.5 19.5 3 2 og o ing range o range ing 1 0 1 9 17 25 33 41 49 57 65 73 81 89 97 bser ation WECO (classic) rules: 1, 2, 3, 4 applied to Individual statistic. 20 4 Shewhart 2 Control 4.5 5.5 0 og score 6.5 Charts 7.5 8.5 -2 9.5 10.5 11.5 Xbar R -4 12.5 1 4 7 10 13 16 19 22 25 28 31 34 13.5 14.5 bgro p 15.5 4 16.5 17.5 18.5 3 19.5 2 og 1 0 1 4 7 10 13 16 19 22 25 28 31 34 bgro p WECO (classic) rules: 1, 2, 3, 4 applied to standardized Xbar statistic.
Details
-
File Typepdf
-
Upload Time-
-
Content LanguagesEnglish
-
Upload UserAnonymous/Not logged-in
-
File Pages31 Page
-
File Size-