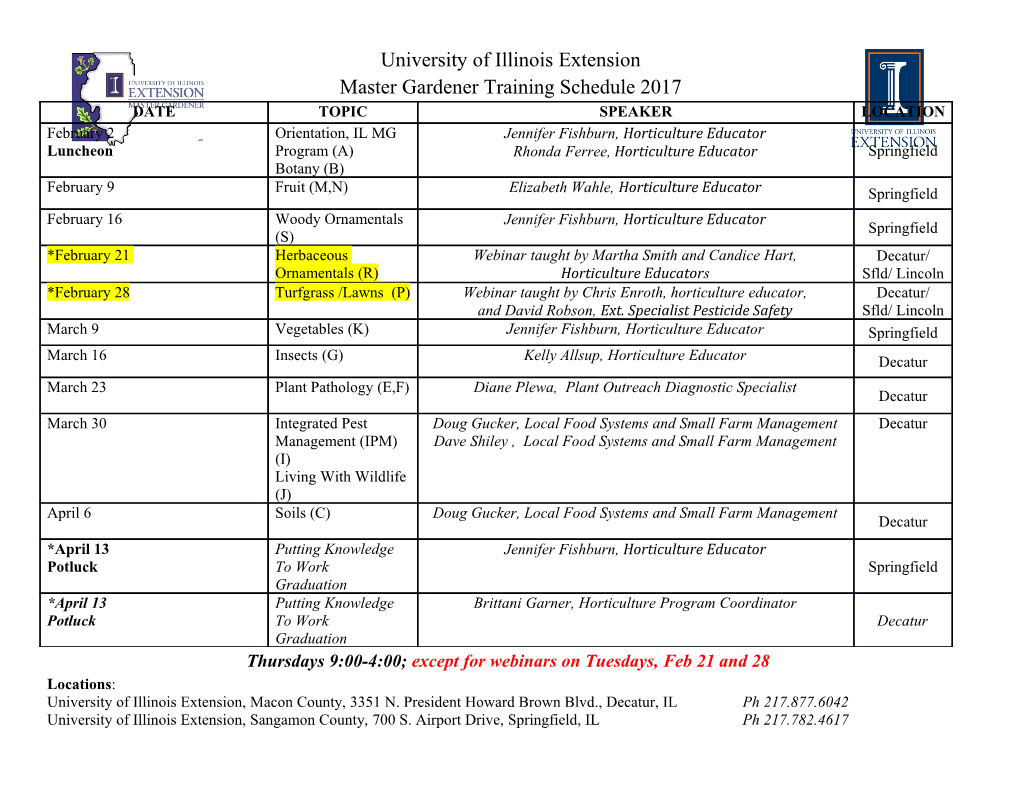
Scrap Tire Recycling A Summary of Prevalent Disposal and Recycling Methods by Kurt Reschner INTRODUCTION The technology to turn a potentially hazardous waste product (i.e., scrap tires) into a valuable resource is available now. This article contains a concise summary of the most common scrap tire recycling methods, as well as a discussion of prevalent uses for recycled tire rubber. Problems associated with uncontrolled or illegal scrap tire disposal As a rule of thumb, the scrap tire generation in industrialized countries is approximately one passenger car tire equivalent (PTE, 20 lbs., 9 kg) per population and year. It is estimated that 2 to 3 billion scrap tires are stockpiled in illegal or abandoned piles throughout the U.S. This figure represents the cumulative scrap tire generation of approximately ten years. For EU member states, it is safe to assume illegal or semi-legal scrap tire piles in the same order of magnitude. The most obvious hazard associated with the uncontrolled disposal and accumulation of large amounts of tires outdoors is the potential for large fires wich are extremely detrimental to the environment. Once a large pile catches fire, it is very hard, if not impossible, to extinguish. In some instances, large tire piles have been burning for several months with the fumes being visible for many miles. Due to the intense heat and smoke generation, fire fighters have a hard time extinguishing these fires with conventional means. Also, air and soil pollution is even worse if attempts are made to extinguish the fire with foam or water. For this reason, scrap tire fires are often allowed to burn out in a more or less controlled manner until the entire pile is exhausted. Even if large outside tire piles do not catch fire, they still pose a serious problem for human health and the environment: Disease carrying mosquitoes, find an ideal breeding ground in the countless little puddles which Figure 1: Tire Fire in Stanislaus Co. form in virtually each tire as it rains. Especially in areas California (September 1999) with warmer climates mosquito-borne diseases like encephalitis and dengue fever have been reported around large tire piles. In response to the environmental problems and health hazards caused the by countless illegal scrap tire piles around the globe, most industrialized countries have instigated legal guidelines addressing this issue. Regulations vary from country to country, but the main purpose of these regulations is to provide for an environmentally safe disposal, limit the amount of tires being stored at any given location, and to encourage the use of tire derived recycling products. While grants and subsidies are sometimes instrumental for the implementation of a recycling project, it is ultimately up to the ingenuity of business community to come up with economically sound and market driven solutions. The key factors for a long term economic success in this field are: · Sound marketing for the recycled product · Judicious selection of the appropriate recycling technology · Innovative product development · A local and national government that is supportive of recycling Copyright: Kurt Reschner, Berlin, Germany Scrap Tire Recycling --- Page 2 HISTORICAL PERSPECTIVE It is commonly believed that recycling gained momentum only in the past decades. At least in the case of rubber recycling, this is not entirely true. In the early 1900s, the average recycled content of all rubber products was over 50%. In fact, is fair to say that the rubber reclaiming industry is as old as the industrial use of rubber itself. Figure 2 shows the advertisement of a rubber recycling business in Leipzig, Germany dating back to the year 1909. It reads: “Grinding and separation of scrap rubber of all kinds. Low rates. The largest company in the industry. Custom grinding. Specialty: hard rubber dust” One reason for the flourishing rubber grinding and reclaiming industry lies in the comparatively scarce supply of rubber at that time. In 1910, one pound of natural rubber cost nearly as much as one pound of silver and it made perfect sense to reuse as much of this valuable commodity as possible. By 1960, the recycling content in the traditional rubber manufacturing industry dropped to around Figure 2: Advertisement of a Rubber 20%. Cheap oil imports, the more widespread use Reclaiming Company from 1909 of synthetic rubber and the development of steel belted radial tires have led to a steady decline of rubber recycling. By the time the steel belted radial tire was introduced in the late 1960ies and early 1970ies, it became increasingly difficult to grind or slice old tires. As a consequence, the old infrastructure for regrinding and reusing waste tires has been almost completely lost. As of 1995, the traditional tire and rubber industry used only about 2% recycled material. The low recycling content in conventional rubber products does not tell the whole story, however. Technical developments in the past decade (like effective ambient and cryogenic grinding methods and new environmentally friendly devulcanizing methods) make it very likely that the use of recycled tire materials will increase significantly. Many new uses for recycled tire rubber outside the traditional rubber manufacturing industry have become increasingly important. The author is of the opinion that rubber recycling not only has a long past, but also a bright future. Scrap Tire Disposal Statistics The publicly available information on scrap tire generation and disposal is fairly intransparent. Table 2 shows disposal and recovery data for scrap tires published by the European Tyre and Rubber Manufacturers Association. Copyright: Kurt Reschner, Berlin, Germany Table 2: Scrap Tyre Statistics for Europe 2006 Trade with Used Tyres Recovery Disposal Scrap Tyre Generation in 1,000 t/a Sale Export Retread Material Energy Landfill* Austria 55 - - 4 16 35 - Belgium and Lux. 82 - 2 3 28 35 14 Bulgaria 10 - - - - - 10 Croatia 15 - - - - - 15 Cyprus 5 - - - - - 5 Czech Republic 80 - - 12 - - 68 Denmark 45 1 - 5 38 1 - Estonia 11 - - 2 2 - 7 Finland 45 - - 10 35 - - France 398 20 20 55 157 106 40 Germany 585 15 38 60 124 310 38 Greece 48 1 - 2 5 8 32 Hungary 46 - - 5 18 16 7 Ireland 40 1 1 1 3 - 34 Italy 380 30 50 50 83 148 19 Latvia 9 - - 2 - - 7 Lithuania 9 - - 2 - - 7 Malta 1 - - - - - 1 Netherlands (car tires only) 47 - 13 - 13 21 - Norway 47 - 1 7 23 16 - Poland 146 1 1 21 10 56 57 Portugal 92 1 15 16 26 34 - Romania 50 - - 5 10 10 25 Slovakia 20 - - - 5 2 13 Slovenia 23 - - 4 - - 19 Spain 305 10 20 37 42 52 144 Sweden 90 1 7 16 32 34 - Switzerland 54 1 13 7 - 25 8 U.K. 475 32 34 55 212 72 70 Total: 3,213 114 215 381 882 981 640 Source: European Tyre and Rubber Manufacturers Association 2006. Summary by Kurt Reschner *) This figure also includes unknown means or disposal Copyright: Kurt Reschner, Berlin, Germany Energy Recovery The use of tire derived fuel (TDF) in cement kilns, paper mills or power plants is a perfectly reasonable use for scrap tires, if recycling is not a viable option. While uncontrolled fires cause substantial air and ground pollution, the incineration of whole tires or tire chips in a controlled furnace is environmentally safe. On average, the BTU value of scrap tires or TDF exceeds that of coal, while the sulfur content is in the same order of magnitude or even lower. Cement kilns are by far the largest users of TDF. Some cement companies have the capacity to incinerate whole tires, thus being able to omit the comparatively expensive size reduction process. Rubber Recycling A concise definition of recycling would be the re-use of a material for its originally intended purpose, e.g. old aluminum cans are used to make new ones. In the case of scrap tires, recycling would mean the use recycled tire rubber as a compounding ingredient for new tires. In a broader sense, recycling is referred to as grinding scrap tires into crumb rubber while removing steel, fiber and other contaminants. In North America, the markets and applications for recycled tire rubber (“crumb rubber”) have developed tremendously in the past decade. The different markets and uses for recycled tire rubber are discussed in greater detail in the section Products and Applications. Landfilling Most landfills accept whole scrap tires only at a hefty tipping fee because tires are awkward to handle and difficult to compact. In some instances, scrap tires have worked their way to the top of a closed landfill, causing costly damages to the landfill cover. Nonetheless, a significant part of the current scrap tire generation still ends up in landfills. Since a ban on landfilling whole tires was implemented in most States, scrap tires are usually cut into pieces or shredded before landfilling in the U.S. The EU Landfill Directive similarly bans whole tires from landfills by 2003. By 2006, tires in any shape or form will be banned from landfills in EU Member States. In order for the EU Landfill Directive to be implemented in a timely manner, new disposal routes for scrap tires need to be developed with great urgency in all EU Member States. A variation of landfilling is monofilling, which means that scrap tires are not mixed with other waste materials, but stored at a dedicated, licensed location. Once the monofill has reached its capacity, it is covered like any other landfill to reduce the fire hazard and also prevent mosquito breeding. Civil Engineering Applications Tire derived products, mostly 1” tire chips are sometimes used to replace conventional construction material, e.g., road fill, gravel, crushed rock or sand. The benefits of using tire chips instead of conventional construction materials are amongst others: reduced density, improved drainage properties and better thermal insulation.
Details
-
File Typepdf
-
Upload Time-
-
Content LanguagesEnglish
-
Upload UserAnonymous/Not logged-in
-
File Pages16 Page
-
File Size-