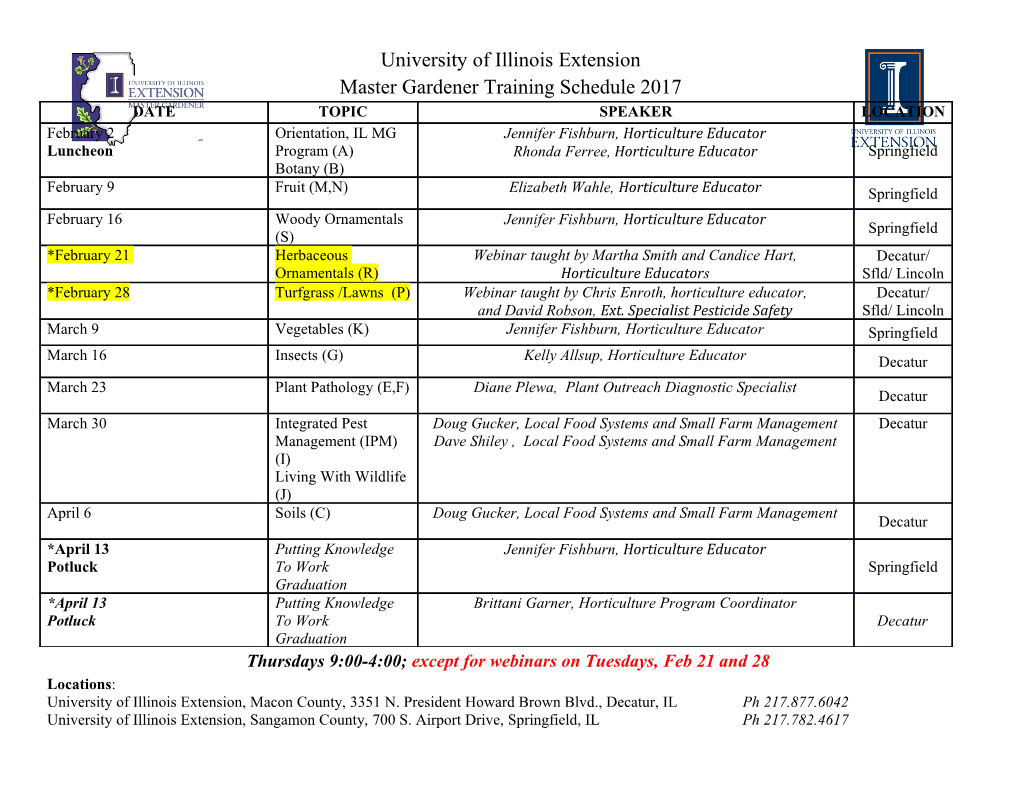
Name ///sr-nova/Dclabs_wip/Metallurgy/5224_279-302.pdf/Chap_16/ 3/6/2008 10:15AM Plate # 0 pg 279 Elements of Metallurgy and Engineering Alloys Copyright © 2008 ASM International® F.C. Campbell, editor, p 279-302 All rights reserved. DOI: 10.1361/emea2008p279 www.asminternational.org CHAPTER 16 Deformation Processing METALWORKING PROCESSES are com- temperature, which is approximately 0.5 Tm. monly classified as either hot working or cold Cold working processes are conducted at or near working operations. Primary metalworking room temperature, while warm working pro- processes, such as the bulk deformation pro- cesses are conducted at intermediate tempera- cesses used to conduct the initial breakdown of tures. Hot working produces a recrystallized cast ingots, are always conducted hot. The term grain structure, while the grain structure due to bulk deformation implies large amounts of cold working is unrecrystallized and retains the material movement, such as in hot rolling or effects of the working operation. forging. Secondary processes, which are used to Bulk deformation changes the shape of a produce the final product shape, are also con- workpiece by plastic deformation through the ducted either hot or cold. Some secondary pro- application of compressive forces, as for the cesses, such as sheet forming, do not involve typical bulk deformation processes in Fig. 16.1. large amounts of deformation. In addition to shaping the metal, bulk defor- Hot working processes are conducted at mation is used to refine the structure that temperatures above the recrystallization results from solidification. To refine the F Roll F Workpiece v v Die Workpiece Die Roll F Rolling Forging Ram Workpiece Workpiece v v F F Die Die Extrusion Wire Drawing Fig. 16.1 Bulk deformation processes. Source: Ref 1 Name ///sr-nova/Dclabs_wip/Metallurgy/5224_279-302.pdf/Chap_16/ 3/6/2008 10:16AM Plate # 0 pg 280 280 / Elements of Metallurgy and Engineering Alloys inhomogeneous structure resulting from solidi- followed by holding the workpiece at an fication, cast ingots and continuously cast slabs elevated temperature causes static recovery and and blooms are typically hot worked into inter- recrystallization, resulting in a fine grain size. mediate product forms, such as plates, bars, and This may occur during hot rolling (Fig. 16.2) sheet. Large plastic deformation in combination where there is time between roll passes, or after with heat is very effective in refining the hot forging, where the workpiece slowly cools to microstructure, breaking up macrosegregations, room temperature. collapsing and sealing porosity, and refining the Very large deformations are possible in hot grain size. This product may be suitable for its working, and since recovery processes keep intended application, but in many cases, it pro- pace with the deformation, hot working occurs at vides the starting material for secondary defor- essentially a constant flow stress (the shear stress mation processes such as drawing, hot or cold required to cause plastic deformation of the forging, and sheet metalworking. metal). Since the flow stress decreases with Because most processes involve sliding con- increasing temperature, metals become more tact between the workpiece and a tool or die, malleable, and less energy is needed to produce friction affects material flow, die pressures, and a given amount of deformation. However, as the the force and energy requirements. In many temperature increases, the strength also de- instances, lubricants are used to minimize fric- creases. Therefore, hot working processes tion. Lubricants also reduce die wear, help in usually involve the use of compressive forces to providing temperature control, and minimize prevent cracking or failure. Because recovery high-temperature oxidation. processes take time, flow stress, sf, is a function of strain rate, e_: m 16.1 Hot Working sf=Ce_ (Eq 16.1) Hot working normally takes place at where C is the strength coefficient (decreasing approximately 70 to 80% of the absolute melting with increasing temperature), and m is the strain- temperature. During hot working, the strain- rate sensitivity. hardened and distorted grain structure produced A high value of m means that any incipient by deformation is rapidly eliminated by the neck that develops becomes stronger and formation of new strain-free grains as a result spreads to neighboring material, allowing more of recrystallization. Dynamic recrystallization deformation in tension. In some very fine- occurs during deformation, while static recrys- grained metals, the value of m may reach 0.4 to tallization occurs after deformation is complete 0.5 but only at very low strain rates and within a but while the workpiece is still hot. For pro- limited temperature range. cesses such as hot rolling, hot extrusion, and hot Because hot working processes may hold a forging, the time within the deformation zone is workpiece at a high temperature for a long time, usually short, and grain refinement is usually grain growth can occur. In fact, in an extended accomplished by static recrystallization after hot hot working process such as ingot break- working. A high level of hot deformation down during rolling, a cyclic history of grain Fig. 16.2 Recrystallization during hot rolling Name ///sr-nova/Dclabs_wip/Metallurgy/5224_279-302.pdf/Chap_16/ 3/6/2008 10:16AM Plate # 0 pg 281 Chapter 16: Deformation Processing / 281 deformation, recrystallization, and grain growth The workability, or the ease with which a occurs for each deformation step. The ability to metal is shaped by plastic deformation, is lower put work into the grains at a level sufficient to for cast structures than for wrought structures cause recrystallization is the reason that fine (Fig. 16.3). Workability is also dependent on grains can be developed from a coarse-grained grain size and grain structure. When the grain structure by hot working. Thus, hot working size is relatively large, as in cast structures, processes must balance recovery and recrys- workability is lower because cracks can initiate tallization against grain growth. and propagate along grain boundaries. Also, At temperatures above the equicohesive with cast structures, impurities frequently seg- temperature, the grain interiors are more resis- regate to the center, to the top, or to the surface of tant to deformation than the grain boundaries, the ingot, creating areas of low workability. and the grain boundaries can sustain substantial Because alloying elements are not distributed deformation. If a very fine grain size can be uniformly, the temperature range over which an achieved and maintained during deformation at ingot structure can be worked is somewhat a low strain rate, grain-boundary sliding can limited. occur. Creep forming, hot die forging, iso- The upper limit for hot working is determined thermal forging, and isothermal rolling are pro- by the temperature at which either melting or cesses that rely in part on grain-boundary sliding excessive oxidation occurs. Generally, the and other thermally activated deformation maximum working temperature is limited mechanisms. to approximately 40 C (100 F) below the Fig. 16.3 Relative workabilities of wrought and cast metals. Source: Ref 2 Name ///sr-nova/Dclabs_wip/Metallurgy/5224_279-302.pdf/Chap_16/ 3/6/2008 10:16AM Plate # 0 pg 282 282 / Elements of Metallurgy and Engineering Alloys melting temperature to prevent the occurrence of a high K require large forces for deformation. hot shortness. The melting point of an alloy in Work hardening is a measure of how the resist- the as-cast condition is usually lower than that of ance to plastic flow increases as the metal is the same alloy in the fine-grain, recrystallized deformed. Typically, n has values of 0.1 to 0.5 condition, because of chemical inhomogeneities for cold working, with 0 being a perfectly plastic and the presence of low-melting-point com- metal that will not work harden. A high n value pounds that frequently occur at grain bound- allows more tensile deformation before a aries. Deformation at temperatures too close to localized neck develops. A metal with a high the melting point of these compounds may lead work-hardening exponent but a low strength to grain-boundary cracking when the heat coefficient will achieve a high strength level developed by deformation increases the work- after a large amount of deformation. Examples piece temperature and produces local melting, a include coppers, brasses, and low-carbon steels fracture mode called hot shortness. Hot short- that are cold worked to produce higher hardness ness can be prevented by using a sufficiently low and strength in the formed part. The value of K deformation rate that allows the heat developed increases and n decreases in the course of cold by deformation to be dissipated by the tooling, working; thus, ductility is reduced and the forces by using lower working temperatures, or by increase. Intermediate process anneals can subjecting the workpiece to a homogenization restore ductility and reduce forces but at an heat treatment prior to hot working. The inter- additional cost. Warm working in an inter- mediate temperature region of low ductility mediate temperature range can combine some of shown in Fig. 16.3 can occur at temperatures that the benefits of hot and cold working. Some are sufficiently high for grain-boundary sliding values of K and n are given in Table 16.1. For to cause grain-boundary cracking but are not steels, K increases with carbon content, while n high enough for the cracks to be healed by generally decreases. Both copper and brass have dynamic recrystallization. a much higher work-hardening exponent than The advantages of hot working include: steels. Over the range of strain rates at which cold deformation processes are conducted (0.1 Flow stresses are low; hence, forces and to 100/s), the sensitivity to strain rate for most power requirements are relatively low. Even metals is low. Rather, the strain level and the very large workpieces can be deformed with strength coefficient, K, control the flow stress.
Details
-
File Typepdf
-
Upload Time-
-
Content LanguagesEnglish
-
Upload UserAnonymous/Not logged-in
-
File Pages24 Page
-
File Size-