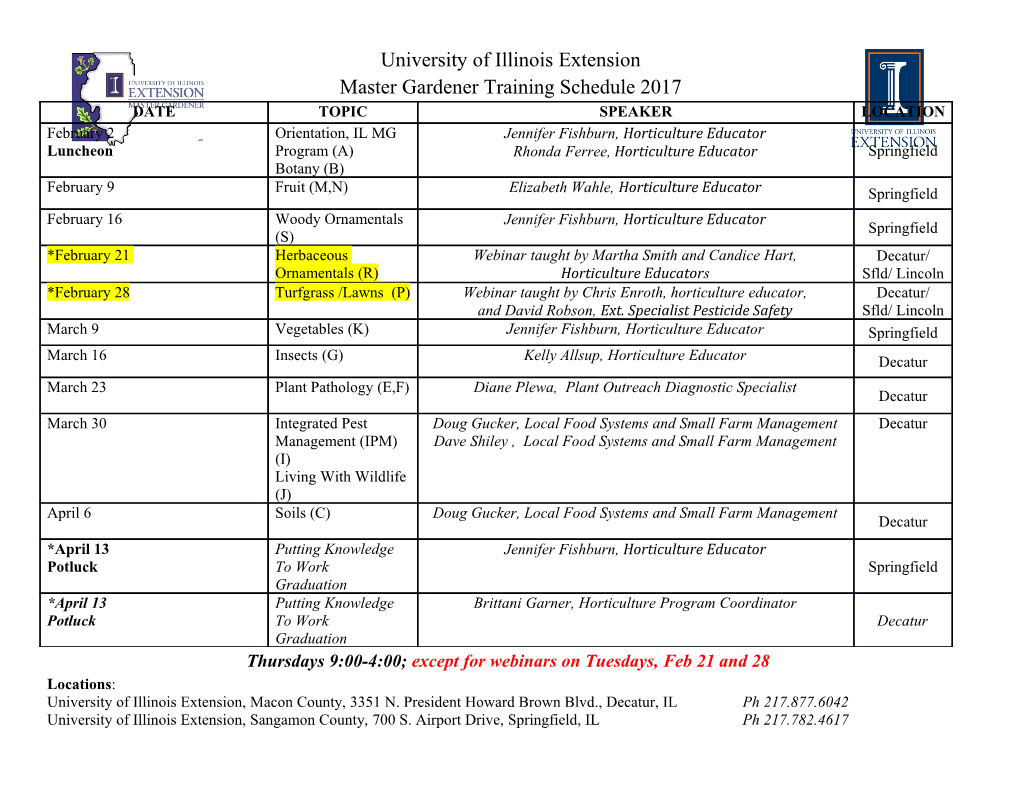
Jan/Feb 2011 Layers of Color Also in This Issue . Totally Tubular Playing Dress-Up Lattice Work America’s Most Trusted Glazes™ Reduction Looks for Electric Kilns Potter’s Choice 30 Colors Cone 5-6 PC-1 PC-2 PC-4 PC-12 PC-20 PC-23 PC-25 PC-27 PC-28 PC-29 PC-30 PC-32 PC-33 PC-34 PC-35 PC-36 PC-37 PC-39 PC-40 PC-41 PC-42 PC-43 PC-46 PC-49 PC-50 PC-52 PC-53 PC-55 PC-59 PC-60 All glazes available in 25 lb. Dry Dipping Form. www.amaco.com/learn-about-potters-choice-glazes PotteryMaking Illustrated | January/February 2011 1 POWERFUL SMOOTH TOUGH www.skutt.com INNOVATIVE ERGONOMIC Chaffey College Rancho Cucamonga, CA. VALUE Brian Kohl Ceramics Instructor Skutt’s unique REMOVABLE WHEEL HEAD makes clean-up at Chaffey College run like clockwork! 2 PotteryMaking Illustrated | January/February 2011 table of contents features 12} Playing Dress-Up 22} Layers of Color by Magda Gluszek by Andrew Gilliatt Getting your ideas to There’s a world of pos- come alive from sketch sibilities when you add to maquette to hol- color to your work in lowed form is a chal- stages with slip, glaze, lenge worth exploring. and decals. 29} Totally Tubular 35} Lattice Work Inspired by Peter King by Margaret Bohls Learn how to slab build When it comes to large round forms you working on the grid, can finish on the wheel Margaret Bohls has without the hassle of the skills to put it all centering and throwing together for a dynamic large pieces of clay. finished product. departments 6} In the Mix 8} Tools of the Trade 10} Supply Room 16} Tips from the Pros All-Weather Clay Texture Molds Stamp Pads Sweet Surface by Jessica Knapp by Margaret Bohls by Holly Goring by Magda Gluszek 41} Instructors File 44} Off the Shelf 48} Pottery Illustrated On the Cover It’s a Wrap Techniques Classic Greek Forms Andrew Gilliatt gets by Bill Shinn Using Slips Illustrated by his color thing going on layer by layer using a by Sumi von Dassow Robin Ouellette variety of techniques. See story on page 22. PotteryMaking Illustrated | January/February 2011 3 fired up Volume 14 • Number 1 Publisher Charles Spahr Recharging Editorial Editor Bill Jones Associate Editor Jessica Knapp Our idea of relaxing is all too often to plop down in Assistant Editor Holly Goring Editorial Assistant Erin Pfeifer front of the television set and let its pandering idiocy [email protected] Telephone: (614) 895-4213 liquefy our brains. Shutting off the thought process Fax: (614) 891-8960 is not rejuvenating; the mind is like a car battery—it Graphic Design & Production Cyndy Griffith Marketing Steve Hecker recharges by running. Ceramics Arts Daily Managing Editor Jennifer Poellot Harnetty —Bill Watterson Webmaster Scott Freshour Advertising Advertising Manager Mona Thiel Advertising Services Jan Moloney [email protected] Telephone: (614) 794-5834 or the legions of us who spend the day in an office or tending to a Fax: (614) 891-8960 Subscriptions daily routine, a bit of downtime is a welcome reward at the end of the Customer Service: (800) 340-6532 day. The only trap to shutting off the thought process is the danger [email protected] F Editorial & Advertising offices in not being able to turn it back on again—something I’ve experienced, or 600 N. Cleveland Ave., Suite 210 Westerville, OH 43082 USA rather perfected. Knowing this has resulted in me not even bothering to sign up for cable TV, hence removing a great temptation. www.potterymaking.org During the holiday season, I managed to get into the studio more in No- Pottery Making Illustrated (ISSN 1096-830X) is published bi- vember and December than during the entire ten months prior. Over these monthly by The American Ceramic Society, 600 N. Cleveland Ave., Suite 210, Westerville, OH 43082. Periodical postage paid two months, I managed to use the drive home to plan what I’d be doing in at Westerville, Ohio, and additional mailing offices. Opinions expressed are those of the contributors and do not the studio that evening, and so was able to alter my routine away from ‘re- necessarily represent those of the editors or The American Ce- laxing’ in a traditional sense to relaxing in the studio, which, as it turns out, ramic Society. Subscription rates: 6 issues (1 yr) $24.95, 12 issues (2 became a very stimulating activity. yr) $39.95. In Canada: 6 issues (1 yr) $30, 12 issues (2 yr) $55. International: 6 issues (1 yr) $40, 12 issues (2 yr) US$70. All In our hopes of recharging you, we’ve once again rounded up some great payments must be in US$ and drawn on a U.S. bank. Allow 6-8 techniques. Our cover features Andrew Gilliatt’s bowls, which he casts in weeks for delivery. Change of address: Visit www.ceramicartsdaily.org to two stages to both color and form the pieces. The entire process is there from change your address, or call our Customer Service toll-free at making the model and mold to adding various layers of colored slips and (800) 340-6532. Allow six weeks advance notice. Back issues: When available, back issues are $6 each, plus $3 decals. Magda Gluszek on the other hand takes an unusual approach to her shipping/handling; $8 for expedited shipping (UPS 2-day air); and $6 for shipping outside North America. Allow 4–6 weeks work in that she adds non-fired materials to achieve dramatic life-like effects for delivery. Call (800) 340-6532 to order. for her figures. And while you may not make figurative work, I’m sure you’ll Contributors: Writing and photographic guidelines are avail- able on the website. Mail manuscripts and visual materials to discover a tip or technique in her article you can use in your own work. the editorial offices. Photocopies: Permission to photocopy for personal or inter- Peter King, author of Architectural Ceramics for the Studio Potter, demon- nal use beyond the limits of Sections 107 and 108 of the U.S. strates how to create forms of any diameter for making tall cylinders, which Copyright Law is granted by The American Ceramic Society, ISSN 1096-830X, provided that the appropriate fee is paid di- are then finished on the wheel. This inspired me to stop by Home Depot to rectly to Copyright Clearance Center, Inc., 222 Rosewood Dr., Danvers, MA 01923; (978) 750-8400; www.copyright.com. Pri- pick up a concrete form tube, which I cut in half and got to work pretty suc- or to photocopying items for educational classroom use, please contact Copyright Clearance Center, Inc. cessfully for making a 20-inch tall textured vase. Margaret Bohls returns to This consent does not extend to copying items for general distri- round out the features with her quilted 2-tier vase and lattice stand. As with bution, for advertising or promotional purposes, or to republish- ing items in whole or in part in any work and in any format. Please all the features in this issue, Margaret covers several techniques and also direct republication or special copying permission requests to the Ceramic Publications Company, The American Ceramic Society, includes really sound advice on making and using plaster texture molds. 600 N. Cleveland Ave., Suite 210, Westerville, OH 43082. Postmaster: Send address changes to Pottery Making Illus- So, for 2011 you’ve got an entire year to look forward to in the studio trated, PO Box 15699, North Hollywood, CA 91615-5699. recharging your batteries. Think of PMI as a set of jumper cables ready to Form 3579 requested. spark your imagination. And as we begin our 14th year of publication, we’re excited about keeping you running. ceramic artsdaily.org Bill Jones Copyright © 2011 The American Ceramic Society Editor All rights reserved 4 PotteryMaking Illustrated | January/February 2011 PotteryMaking Illustrated | January/February 2011 5 in the mix All-Weather Clay by Jessica Knapp t’s winter for those of us in the northern hemisphere, clay bodies made using these materials along with an ap- and in places where the temperatures get below propriate grog have a higher ratio of large spaces between Ifreezing, that means bringing in clay flower pots and particles after being fired to vitrification. It may be coun- protecting any outdoor clay sculptures with a waterproof terintuitive, but this means that the fired piece absorbs less cover to prevent frost damage. If you can’t take these water. It also means that whatever water is absorbed will preventative measures, or are making outdoor work for likely only partially fill the larger spaces, leaving room for someone else and can’t guarantee that they’ll take these expansion as the water turns to ice. steps, there are ways to make a clay body that is frost resistant, or to test your own clay body to see how resis- Putting Your Clay to the Test tant it would be to freezing conditions. Whether you develop your own clay body or use a com- mercial clay body, there’s a simple test you can use to de- Starting from Scratch termine if it’s likely to be frost resistant once it’s been fired. Making a clay body that’s frost resistant requires research It’s called the freeze-thaw test, and it’s used in industry for and testing. The goal is to create a clay body that’s highly tile, brick, pipes, and other ceramics that need to withstand vitrified after glaze firing, has low water absorption, and a severe weathering.
Details
-
File Typepdf
-
Upload Time-
-
Content LanguagesEnglish
-
Upload UserAnonymous/Not logged-in
-
File Pages52 Page
-
File Size-