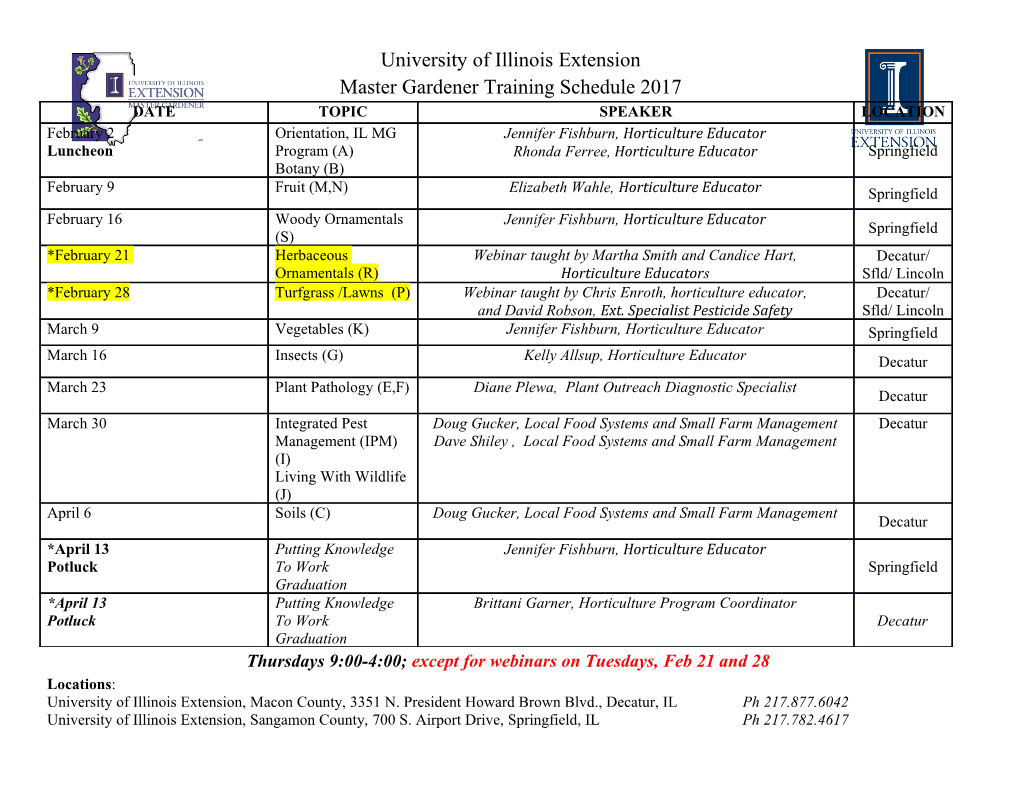
Composite Bridge Design Analysis of Realizing Composite Action in an FRP-Steel Bridge Peter Flink December 2015 Page 2 of 293 December 7, 2015 Master’s Thesis Delft University of Technology Civil Engineering and Geosciences: Structural Engineering Stevinweg 1 2628 CN Delft Netherlands Peter Flink 4007034 Thesis Committee: Prof. Dr. Ir. J.G. Rots (Chairman), Professor at Delft University of Technology, Faculty of Civil Engineering and Geosciences, Department of Structural Engineering, Section Structural Mechanics Dr. M.H. Kolstein, Associate Professor at Delft University of Technology, Faculty of Civil Engineering and Geosciences, Department of Structural Engineering, Section Structural and Building Engineering: Steel, Hybrid, and Composite Structures Ir. R. Abspoel, Assistant Professor at Delft University of Technology, Department of Structural Engineering, Section Structural and Building Engineering: Steel, Hybrid, and Composite Structures Ir. L.J.M. Houben, Associate Professor at Delft University of Technology, Department of Structural Engineering, Section Pavement Engineering Ing. M. van Almen, Senior Constructor at Iv-Infra B.V., Section Movable Bridges Page 3 of 293 Abstract Many old moveable bridges have exceeded their technical lifetime. Replacement of the foundations is expensive and often unnecessary if the new bridge superstructure is lighter than the old one. With stricter design guidelines being in effect nowadays, a conventional orthotropic steel deck design will end up being heavier. A lightweight fiber reinforced polymer deck supported by steel girders is proposed as a solution. In this thesis the potential mass reduction resulting from a lightweight FRP deck is analyzed. Analyses are initially performed under the assumption that realizing composite action will generate the best results. However, a finite element model of a bolted connection between an FRP deck and steel girders indicates that the strength of such a connection is too low to efficiently realize composite action. An alternate solution where the deck is draped over the main girders with a thin FRP layer is considered and outperforms the composite action design. The design with FRP but without composite action is compared with a standard orthotropic steel design. The FRP design weighs order of magnitude 10% less than its orthotropic counterpart. However, it is still significantly heavier than the original component in need of replacing. Page 4 of 293 Preface The thesis before you has been established as one of the requirements for the master structural engineering at the Technical University Delft. The subject was offered by Iv-Infra, following their experience with a project with a fiber reinforced polymer deck. The purpose of this thesis was to design an FRP-steel hybrid bridge with composite action, with the hope of showing that significant weight savings could be obtained by designing bridges in this manner. Along the way a large portion of this paper became dedicated to the design and modeling of a bolted connection in FRP. The subject of FRP was foreign to me at the start of this project. Therefore, this thesis gave me the opportunity to familiarize myself with a new material; one gaining in popularity in civil engineering. While not all information was transferred to paper, hopefully the reader can learn about FRP, its benefits, and its limitations from this thesis. Page 5 of 293 Acknowledgements At this point I would like to take the time to offer my gratitude to the people who have supported me throughout the completion of my thesis and my studies. To start, I would like to thank Matthijs van Almen, who acted as my daily supervisor at Iv-Infra. He was always available made time for any and all questions I wanted to ask him and his advice and practical approach were instrumental in guiding this thesis to completion. I am grateful for the exertion of my thesis committee. Prof. Rots, Ir. Abspoel, and Dr. Kolstein have added invaluable professional knowledge to this thesis. I would like to distinguish everyone in the place where I worked. Erika, Harris, Stephan, Yirui, Dirk, Jeremy and Dennis welcomed me to the offices in Sliedrecht and made my time there more enjoyable. I would also like to thank Michel Koop, who provided me with the topic of this thesis as well as the opportunity to carry it out. I would like to acknowledge my appreciation for my friends in Delft, who have ensured that my studies have been filled with entertainment and enjoyment. Finally, I would like to thank my family. They have been loving and supportive throughout my studies, and have always pushed me to do my best. Page 6 of 293 Summary Fiber reinforced polymers (FRP) are recognized for their high strength and low weight. While, typically used in specialized functions where price is of the second order, their use is slowly becoming more prevalent in civil engineering. Considering the large quantities of material needed for structures, the relatively cheap E-glass fiber composites have dominated the market. Within civil engineering FRP is still only applied in situations where reduced mass will lead to benefits greater than solely a reduction in dead weight. The expected reduction in mass offered so many additional benefits, that it drove the use of FRP in the renovation of the Julianabrug in Alphen aan den Rijn. The Julianabrug had reached the end of its life, as it was plagued by fatigue damage and corrosion. The use of FRP was specified under the belief that a bridge with an FRP deck could be executed lighter than the old bridge, and hence the foundations could be reused. The reuse of the foundations would easily compensate for the use of expensive composite materials. The current design of the Julianabrug features a glass fiber reinforced polymer deck that does not act compositely with the steel girders below. This represents an inefficient use of material. Using the theory of inhomogeneous cross sections, the influence of compositely connecting the deck to the girders was analyzed. This was followed by a mass minimization procedure, focused on reducing the mass of the steel profiles, while maintaining the stiffness and strength of the current design. The mass minimization was repeated for three variants in which the material properties of the deck were altered to correspond to different lamination directions. This process indicated that realizing the optimal laminate stiffness in longitudinal direction led to the largest mass reduction of the considered variants. In order to realize composite action between the two materials, a connection method needed to be designed. Adhesive connections were rejected based on questions regarding longevity. A bolted connection was decided upon, based on its simplicity and the widespread experience with such a joint. Hand calculations indicated that such a connection would be possible, but required an extremely thick laminate, with many connections. However, a finite element analysis of the joint was desired in order to determine whether the hand calculation was accurate or not. A calibration study was performed to set up a failure criterion for the finite element results. This was done in order to establish a failure criterion which corresponds to reality. Both in reality, and numerically, peak stresses arise along the contact interface between a bolt and the laminate, so that looking at maximum values in models would lead to extremely low failure loads. The process to establish a failure criterion was started by finding a set of laboratory experiments from literature which thoroughly detailed the material and specimen properties. Models were made for these experiments, and the Tsai-Wu failure criterion was calculated within the laminate. The results of the experiments were set against trial failure criteria which accounted for distance from the interface and different Page 7 of 293 measurement methods in the cross section. The trial failure criterion which best matches the experimental results was then set as the failure criterion for the full scale model of the connection. A full scale model of the bolted connection was created. This was tested against the failure criterion established with the small scale model. However, this indicated that the strength of the connection was significantly lower than the hand calculations had indicated. This meant that the design based on the hand calculations was no longer feasible, as too many bolts would be needed. The construction was redesigned taking into account the modeled strength of the joint. Taking into account the joint strength led to an increase in thickness and height of the steel profile, and a reduction in height of the FRP deck. However, this design became so focused around the connection that the gains of establishing composite action were nearly entirely nullified. A comparison was made between how much mass could be saved in the composite action variant, and a variant in which composite action was not realized but the steel profile was increased to nearly the entire available construction height. The variant without composite action could be executed significantly lighter. Additionally, this variant would have a reduced complexity, since the connections were not necessary. A problem with designing the construction in such a manner that the height of the steel profile is maximized, is that the deck and steel profile must be continuous. In other words, no relative vertical displacement between the two is allowed. To solve this, a detail was created in which a layer of FRP was draped over the top flange of the steel profile, guaranteeing a continuous displacement field. With wheel loads expected to pass over the bridge in close proximity to this detail, it is highly sensitive to fatigue loading. A design with glass fibers proved to be impractical due to the required thickness. This was solved through the application of a CFRP layer, which has been demonstrated to have significantly better properties under fatigue loading. With the better fatigue properties, the detail can be executed as a layer of the same thickness as the top layer of the deck draped over the girder.
Details
-
File Typepdf
-
Upload Time-
-
Content LanguagesEnglish
-
Upload UserAnonymous/Not logged-in
-
File Pages293 Page
-
File Size-