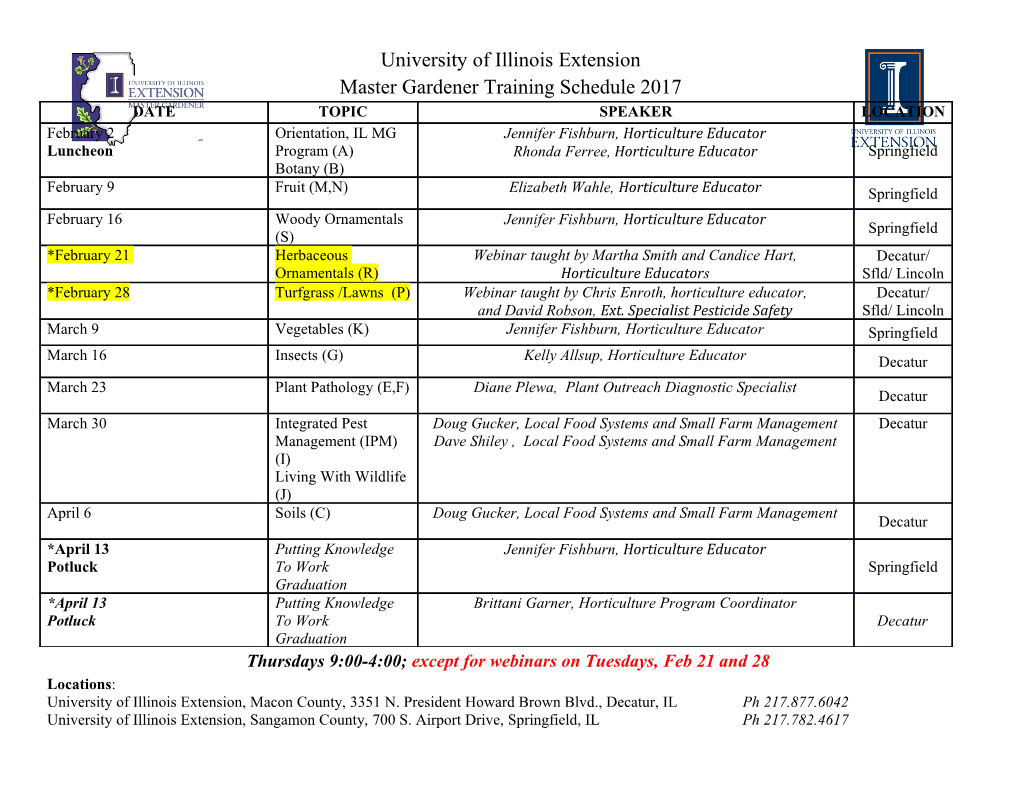
CIS 681/MEAM 520 V. Kumar Spring 1999 8. Force Analysis 8.1 Introduction We will use the principle of virtual work, which is a very fundamental statement about static equilibrium. It allows us to formulate the equations of static equilibrium of a mechanical system without having to draw free body diagrams of each member of the system and having to consider internal forces and moments. Its origins date back to Galileo (1594) and Bernoulli (1717), although Aristotle appears to have written about it. However, it was Lagrange (1788) who developed it into a powerful tool. The principle of virtual work is a fundamental postulate that enables us to transition from Newtonian mechanics to analytical (Lagrangian) mechanics. 8.2 Definitions Generalized coordinates: Any set of coordinates that completely specify the configuration of the system. For a n degree of freedom manipulator, the generalized coordinates can be the joint displacements, q1, q2, ..., qn. We generally prefer that this set of generalized coordinates be a minimal set. Thus if a system has m degrees of freedom, such a minimal set of coordinates will necessarily consist of m generalized coordinates. For example, for a five degree of freedom manipulator, three coordinates that specify the position of the end effector and three Euler angles that specify the orientation of the end effector constitute a set of six generalized coordinates. But the five joint displacements would give us a minimal set of generalized coordinates. Virtual displacements: Any set of infinitesimal displacements that are consistent with the kinematic constraints on the system are called virtual displacements. They are different from “real” infinitesimal displacements because they occur without passage of time. The virtual displacement of a joint (whose displacement is denoted by qi) is denoted by δqi. Virtual work: The work done by any force during a virtual displacement is the virtual work done by that force. Thus if r is the position vector of a particle and a force F acts on that particle, the virtual work done by that force on the particle is simply δW=F. δr. -1- Applied forces: All forces which do non zero virtual work are called active forces. Some texts will use the terms “active” or “external” instead of “applied”. Equilibrium: A state where the resultant force and moment on each member of the system is zero. Generalized forces: In a n degree of freedom mechanical system, with generalized coordinates q1, q2, ..., qn, the net virtual work due to all the applied forces (the sum of the virtual work done by each applied force) can be written in the form: δW= Q1 δq1 + Q2 δq2 + ... + Qn δqn The coefficient Qi is the generalized force corresponding to the ith generalized coordinate. The principle of virtual work: A mechanical system is in equilibrium if and only if the net virtual work of all the applied forces vanishes for every set of virtual displacements. 8.3 Application of the principle of virtual work Since virtual displacements are infinitesimal displacements, the calculations needed for virtual displacements are similar to those required for velocity analysis. Since in robotics, we generally deal with time-invariant, holonomic systems, the relationship between two virtual displacements is exactly the same as the relationship between the corresponding velocities. For example, the ratio between δq1 and δq2 is the same as the ratio between q&1 and q&2 . Under such simplifying conditions, the principle of virtual work is essentially a statement of conservation of power. A mechanical system is in equilibrium if and only if the net power associated with all the applied forces vanishes. In other words, the total power associated with the forces applied on the mechanical system must be equal and opposite in sign to the total power associated with the forces applied by the system. -2- 8.3.1 Example: A 2R planar manipulator Mz P (Fx, Fy) l2 C2 τ2 θ2 y l1 τ1 C1 θ1 x Figure 1 A planar two-degree-of-freedom manipulator. a. Generalized coordinate(s): (θ1, θ2) b. Virtual displacements: δθ1 and δθ 2 c. Applied forces (forces and moments that do work): τ1, τ2, Fx, Fy, Mz. d. Virtual work (forces acting on the manipulator do positive work): δW = τ1 δθ1 + τ2δθ2 + FxδxP + Fy δyP + Mz δφ e. Kinematics: e.1 Velocity analysis: -3- = − θ − (θ + θ ) x&P l1&1s1 l2 &1 & 2 s12 = θ + ()θ + θ y& P l1&1c1 l2 &1 & 2 c12 (1) φ = ()θ + θ & &1 & 2 e.2 Elimination: δ = − δθ − ()δθ + δθ xP l1 1s1 l2 1 2 s12 δ = δθ + ()δθ + δθ yP l1 1c1 l2 1 2 c12 δφ = ()δθ + δθ 1 2 f. Principle of virtual work: δ = (τ − ()()+ + + + )δθ W 1 Fx l1s1 l2s12 Fy l1c1 l2c12 M z 1 + ()τ − + + δθ 2 Fxl2s12 Fyl2c12 M z 2 In order for the mechanical system to be in equilibrium, τ = ()()+ − + − 1 Fx l1s1 l2s12 Fy l1c1 l2c12 M z (2) τ = − − 2 Fxl2s12 Fyl2c12 M z Alternatively we can use a “power conservation” approach and simply write: τθ++ τθ + += φ 11&& 2 2 FxxP&& Fy yP M z& 0 From the velocity analysis, this immediately gives us: (τ − ()()+ − + − )θ 1 Fx l1s1 l2s12 Fy l1c1 l2c12 M z &1 (3) + ()τ − − − θ = 2 Fxl2s12 Fyl2c12 M z & 2 0 Since this expression must be true for all joint velocities, we get the same result as in (2). This analysis can be extended to accommodate other external forces such as gravitational forces. You are recommended to work through the case in which the robot manipulator’s links have masses m1 and m2 and you need to account for the weight of the links. -4- 8.4 The equations for static equilibrium for a n degree of freedom robot manipulator We make the following assumptions in order to derive a simple expression relating the joint forces and the end effector wrench. 1. Frictionless manipulator - the power loss associated with frictional forces and moments is absent. 2. No gravitational forces - the gravitational forces do no work on the manipulator. 3. Only forces are joint forces (or torques), τ, and the wrench (forces and moments) exerted by the end effector, w. Let the joint displacements be q1, q2, ..., qn, and the joint forces or torques be given by τ1, τ2, ..., τn. The end effector twist, the twist of the end effector relative to the manipulator base, is denoted by the vector: (1) We have left out the leading superscript and the trailing subscript that indicate the base reference frame, with respect to which the motion is observed, and the end effector fixed reference frame, the frame attached to the moving body. It should be noted that the point O is a point on the end effector that is instantaneously at the origin of the base reference frame. All components are with respect to the x-y-z axes of the base reference frame. As we will see shortly, it is productive to rewrite the twist vector by rearranging the angular and linear components in the vector. We will define a new 6×1 vector, -5- (2) where ∆ is the 6×6 matrix that reorders the twist vector so that the angular and linear subvectors are swapped. The external forces and moments are given by the vector of joint forces/torques, and the end effector wrench, the wrench exerted by the end effector on the environment, w: (3) w consists of the net force exerted on the end effector, and the net moment of all external forces and couples acting on the end effector. The trailing superscript O indicates that the moment is about the origin of the base reference frame O. Once again, all components are with respect to the x-y-z axes of this base reference frame. Analogous to the reordered twist vector, we can define a new 6×1 vector, -6- (4) which consists of the same elements with a reordering of the angular and linear parts of the wrench vector. From the velocity analysis, we know we can relate the end effector twist to the joint velocities via the manipulator Jacobian J in the fixed frame: t = J q& (5) The power associated with the actuator forces/torques and the end effector wrench is given by: Since the joint velocities are independent, the manipulator is in equilibrium if and only if (6) This is the main equation that relates the end effector wrench to the joint forces and torques. This statics equation is equivalent to the kinematics equation in Equation (5). While the equation is only valid under the assumptions stated in the beginning of this section, it also finds use in more complex situations where there are other forces acting on the manipulator. Finally, it is important to note the need for introducing the new notation, t , w , and the matrix ∆∆.. This new notation is required only because we have chosen to write wrenches with linear quantities first followed by the angular quantities, while we write the angular velocity first followed by the linear velocity in the twist vector. The rationale for the ordering used in assembling the twist vector t and the wrench vector w is two- fold. First, the two vectors t and w bear a natural resemblance to the 6×1 Plucker line vectors used to describe lines and the geometry of the screw axis geometry underlying the -7- twist and wrench becomes very apparent. Second, as we will see in the next section, the two vectors t and w have the same transformation law, and they transform in exactly the same way line vectors do.
Details
-
File Typepdf
-
Upload Time-
-
Content LanguagesEnglish
-
Upload UserAnonymous/Not logged-in
-
File Pages11 Page
-
File Size-