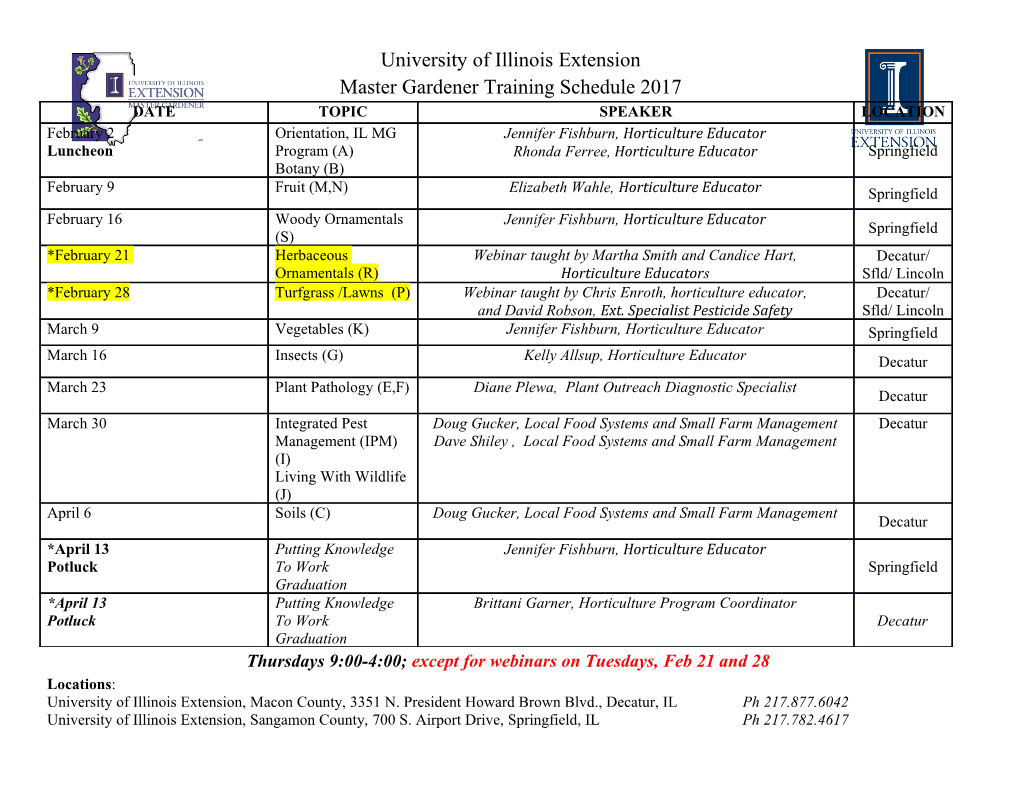
ZINC ELECTROPLATING Zinc Electroplating CHOOSING THE BEST PROCESS FOR YOUR OPERATION By Clifford Biddulph Pavco Inc. Zinc and its alloys have been used for over After fully evaluating how these factors a hundred years as protective and decorative affect your circumstances and referring to coatings over a variety of metal substrates, Table 1, the choice of the most applicable primarily steel. Over the years there have process should be considerably narrowed been a number of processes developed for down. The following sections present applying zinc coatings depending on the more specific information for each of the substrate, coating requirements and cost. Of different basic zinc plating processes. these, electroplating is the most prevalent for functional and decorative applications. ALKALINE CYANIDE ZINC PLATING When choosing a zinc plating process, it is Cyanide zinc plating was for a long time important to know what processes are avail- the workhorse of the industry. Its popularity able and each of their particular advantages has significantly decreased over the years in and disadvantages. Table 1 compares some the U.S. and other countries. The cyanide of the more important factors related to processes are presented here because there these processes. is still a fair amount of cyanide zinc plating done in a number of countries and cyanide FACTORS TO CONSIDER processes are still considered by many to be Listed below, in order of importance, are the benchmark to which all other processes the primary factors that must be considered are compared. when choosing a zinc plating process: Operating requirements for a cyanide n Does the plating specification for the zinc plating process are really minimal when part require a zinc or a zinc alloy deposit? compared to the other zinc plating processes. n Substrate(s) to be plated? Bath analysis, Hull cell testing, and other plat- n Required corrosion protection? ing tests should be done on a weekly basis. n Required deposit thickness uniformity? Cleaning and pickling requirements are not very stringent but should be corrected if an Considering these questions should some- obvious preparation problem exists. what reduce the number of usable plating Bath makeup. Two options are available processes. The next step is to consider the for bath makeup: Using caustic, sodium secondary factors. These factors are listed cyanide and zinc oxide; or using caustic, PLATING/ANODIZING below in no particular order because their sodium cyanide and zinc cyanide. Option importance will vary from shop to shop: A is labor-intensive, but material costs are n Deposit characteristics (appearance, low. Caution must be exercised with this ductility, adhesion, etc.) option as the reaction is highly exothermic n Make-up and operating costs (more than 250°F). n Operating factors (efficiency, pre-plate Option B has higher material costs, but requirements, corrosivity, etc.) is less labor-intensive and faster. n Environmental restrictions (air quality, Process steps. Soak alkaline cleaning heavy metal removal, ammonia, etc.) followed by electro-cleaning is preferred to 106 2011 PF DIRECTORY ZINC ELECTROPLATING PLATING/ANODIZING www.pfonline.com 107 ZINC ELECTROPLATING TABLE I— Attributes of Zinc Electroplating Processes 5 = Excellent Alkaline Zinc Acid Zinc 3 = Good 1 = Poor CN NCN CHLORIDE SO4 LC HC LC HC* NAm LAm Am Substrate1 2 3 3 4 5 5 5 4 Ecological Concerns2 2 1 5 5 5 4 4 5 Make-up Cost 5 3 5 4+ 3 4 4 3 Operating Cost3 3 2 4 4+ 3 3 3 3 Pre-Plate4 5 5 2 3 3 3 3 3 Soln. Corrosivity 4 4 4 4 3 2 2 1 Soln. Conductivity 2 3 2 3 4 4 4 3 Soln. Rinsability 2 2 4 3+ 3 3 3 3 Ease of Operation 4 5 4 3 3 3 4 4 Plating Speed 2 3 2 4 5 5 5 5 Throwing Power 4 4 3 5 3 3 3 2 Covering Power 2 2 3 3 4 4 5 3 Deposit Ductility 4 5 4 4 3 3 3 3 Deposit Adhesion 5 5 3 3 4 4 4 4 Appearance 3 3 3 4 5 5 5 2 Chromate Receptivity 5 5 4 5 4 4 4 4 Corrosion Protection 2 2 2 3 2 2 2 2 1) Ability to plate a wide variety of substrates i.e. hardened steels, cast iron or low carbon stampings 2) Toxicity, waste-treatability, etc. 3) Direct bath operating cost including waste treatment, not pre or post plating costs or equipment costs. 4) Bath's ability to tolerate or compensate for poor preparation. *Sodium and potassium baths are available. Using a potassium based bath can affect the values shown below. The superscript (+ or -) indicates the effect of using a potassium based bath over a sodium based bath. avoid contamination of the plating bath. If line is preferred to avoid the introduction PLATING/ANODIZING parts are not completely cleaned, however, of chromium contamination and to extend the plating bath itself will clean them so the life of the acid. Parts can, however be cleaner maintenance is not quite as critical stripped on-line if necessary. Proprietary as with other plating processes. Cleaning acid additives and/or fluoride salts may be should be followed by pickling in hydro- beneficial in cleaning and activating parts, chloric acid (20–30%) at room tempera- as well as increasing acid longevity. ture or sulfuric acid (5–15%) at 105–120ºF Chromate and passivate coatings and (40–50°C) to activate, descale, etc. steel parts lacquers are the usual post plate treatments prior to plating. Stripping rejected parts off- for any zinc deposit. Chromate conversion 108 2011 PF DIRECTORY ZINC ELECTROPLATING coatings that can provide up to 500 hr to white salt formation are available, as are a wide variety of passivates in colors from clear to black. Equipment and operating parameters. Tanks for zinc cyanide plating can be made of either low-carbon steel, polypropylene, PVC or rubber-lined steel. Low-carbon steel tanks should be insulated from the electri- cal circuit to avoid stray current. For barrel plating, rectifiers operating at –6 15 V, 5–10 asf are recommended. Operating range for rack operations is 3–9 V, 10–40 asf. Most baths operate at a range of tem- peratures, but cooling equipment is rec- ommended and heating equipment may be desirable in colder climates. Steel is the material of choice for any equipment in contact with the plating solution. Agitation is optional for zinc rack operations. Zinc generation tank—overhead view. Special high-grade zinc anodes are pre- ferred, but lower grades have been used thus making the deposit less ductile and with moderate success by some platers. If more stressed. Thus brighter parts may look anode bags are used to avoid roughness be better but their performance in other areas sure that the tops of the bags remain above may suffer. This observation is true for all of the plating solution. the zinc plating systems. Covering power, throwing power and bath efficiency. Covering power is the ability of ALKALINE NON-CYANIDE ZINC a plating bath to deposit metal in a deeply In early cyanide-free alkaline zinc plating recessed area. Throwing power is the abil- systems, cyanide was replaced by complexing ity of a plating bath to deposit a uniform or chelating agents such as sodium glucon- PLATING/ANODIZING thickness of metal on areas of high and low ate, triethanolamine, or polymeric amines. current density. The throwing power of a The resulting baths presented problems with cyanide bath is significantly better than that both waste treatment and co-deposition of of a chloride zinc bath. Plating efficiency of iron. A second generation of organic addi- cyanide zinc baths varies greatly depending tion agents eliminated chelating agents, but on the bath chemistry, plating temperature had other drawbacks. and the plating current. The efficiency can Most of the currently available processes vary anywhere from 40–85%. have eliminated these problems with the Deposit properties. Zinc deposit ductil- use of an entirely new family of organic ity, uniformity, and chromate receptivity reaction products. Platers have a choice from a cyanide zinc bath is better than that of low-chemistry alkaline non-cyanide zinc achieved by chloride zinc baths and in some (low-metal bath) or high-chemistry alkaline cases better than an alkaline non-cyanide non-cyanide (high-metal bath). In addition, baths. The deposit exhibits no chipping or potassium-based baths have been introduced star-dusting. The brighter the zinc deposit, that offer faster plating speeds and higher the higher the organic level in the deposit, efficiencies. www.pfonline.com 109 ZINC ELECTROPLATING Operating requirements for alkaline tanks are preferred but should be insulated non-cyanide zinc plating processes are as from the electrical circuit. For barrel opera- follows: tions, power of 6–15 V at density of 5–10 asf n Perform bath analysis, Hull cell testing, is recommended; for rack operations, 3–9 V and other plating tests daily. and 10–40 asf. Most baths operate at a broad n Analyze, maintain and dump cleaners range of temperatures, but cooling equip- and acids on a regular basis. ment is essential and heating equipment n Perform preventive maintenance to may be needed in colder climates. Steel is reduce production problems and mini- the material of choice for any equipment in mize costs. contact with the plating solution. n Install automatic feeders for liquid com- Filters are essential for an alkaline non- ponents to eliminate human error. cyanide zinc process. One to two turnovers n For troubleshooting, follow the supplier’s of the plating solution per hour are practical recommendations carefully. in most installations using polypropylene cartridges and 10–15 μm screens.
Details
-
File Typepdf
-
Upload Time-
-
Content LanguagesEnglish
-
Upload UserAnonymous/Not logged-in
-
File Pages10 Page
-
File Size-