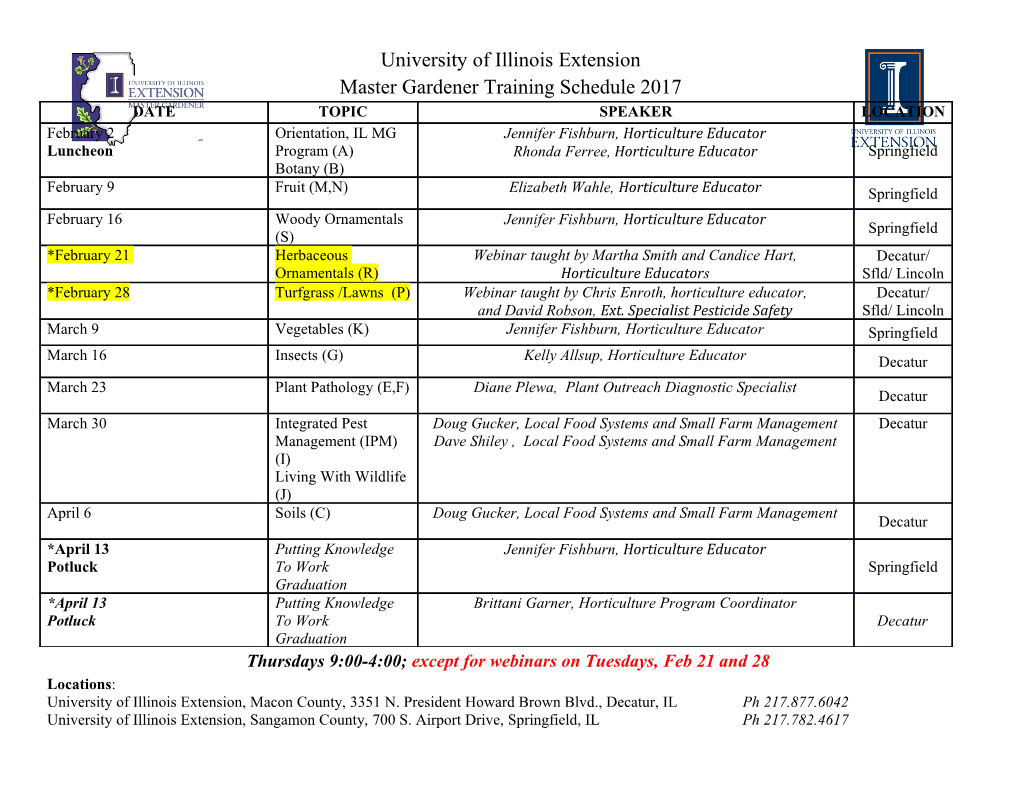
INDUCTION FURNACES Introduction Induction melting of cast iron or steel and their preheating in typical induction crucible furnaces belongs to important and commonly used industrial technologies. Quality of final products strongly depends on homogeneity of metal composition as well as on uniform temperature distribution within all the volume of melt. The process is, however, typical by considerable consumption of electric energy. In order to reach high efficiency of the corresponding device that must, moreover, work reliably and effectively as much as possible, we need to know perfectly all physical phenomena accompanying its operation. And this is an uneasy business, still representing a challenge. The main reason is that these phenomena are characterized by interaction of several physical fields. The dominant one is always harmonic or periodical electromagnetic field producing temperature field and field of flow. All these fields may strongly influence one another, which significantly complicates the situation. The mathematical models of the process [1]–[3] are then usually given by a set of partial differential equations (often nonlinear and nonstationary) whose coefficients are functions of the state variables such as temperature and pressure (and other problems may occur in association with setting of the correct boundary conditions). And even when the model well describes the physical reality, the present knowledge and computational technology allow its solving only under various simplifications. Of course, research in the area of ever more perfect methods and algorithms for solving the above tasks is conducted at a number of universities and other scientific institutions all over the world, but anyway, there still remains much to do to describe the physical reality in its whole complexity. The solution of the task starts from constitution of the basic mathematical model consisting of the Helmholtz elliptical partial differential equation for electromagnetic field, nonlinear Navier-Stokes equation for steady-state flow field and Fourier diffusion parabolic equation supplemented with velocity component for non-stationary temperature field. Meniscus of the free surface boundary is also taken into consideration. The final result of mathematical modelling is the evolution of temperature to the moment when its average value in molten steel reaches the requested value. The simulations are realized by means of the 3D professional FEM-based codes ANSYS supplemented by several codes prepared by the authors. The important point of the paper is represented by an illustrative example describing modelling of 204the process in a particular technological line for casting of iron rolls. The results are discussed in order to establish next research steps. Induction Furnaces The principle of induction melting is that a high voltage electrical source from a primary coil induces a low voltage, high current in the metal, or secondary coil. Induction heating is simply a method of transferring heat energy. Induction furnaces are ideal for melting and alloying a wide variety of metals with minimum melt losses, however, little refining of the metal is possible. There are two main types of induction furnace: coreless and channel. Coreless induction furnaces The heart of the coreless induction furnace is the coil, which consists of a hollow section of heavy duty, high conductivity copper tubing which is wound into a helical coil. Coil shape is contained within a steel shell and magnetic shielding is used to prevent heating of the supporting shell. To protect it from overheating, the coil is water-cooled, the water bing recirculated and cooled in a cooling tower. The shell is supported on trunnions on which the furnace tils to facilitate pouring. The crucible is formed by ramming a granular refractory between the coil and a hollow internal former which is melted away with the first heat leaving a sintered lining. The power cubmicle converts the voltage and frequency of main supply, ot that required for electrical melting. Frequencies used in induction melting vary from 50 cycles per second (mains frequency) to 10,000 cycles per second (high frequency). The higher the operating frequency, the greater the maximum amount of power that can be applied to a furnace of given capacity and the lower the amount of turbulence induced. When the charge material is molten, the interaction of the magnetic field and the electrical currents flowing in the induction coil produce a stirring action within the molten metal. This stirring action forces the molten metal to rise upwards in the centre causing the characteristic meniscus on the surface of the metal. The degree of stirring action is influenced by the power and frequency applied as well as the size and shape of the coil and the density and viscosity of the molten metal. The stirring action within the bath is important as it helps with mixing of alloys and melting of turnings as well as homogenising of temerature throughout the furnace. Excessive stirring can increase gas pick up, lining wear and oxidation of alloys. The coreless induction furnace has largely replaced the crucible furnace, especially for melting of high melting point alloys. The coreless induction furnace is commonly used to melt all grades of steels and irons as well as many non-ferrous alloys. The furnace is ideal for remelting and alloying because of the high degree of control over temperature and chemistry while the induction current provides good circulation of the melt. Channel induction furnaces The channel induction furnace consists of a refractory lined steel shell which contains the molten metal. Attached to the steel shell and connected by a throat is an induction unit which forms the melting component of the furnace. The induction unit consists of an iron core in the form of a ring around which a primary induction coil is wound. This assembly forms a simple transformer in which the molten metal loops comprises the secondary component. The heat generated within the loop causes the metal to circulate into the main well of the furnace. The circulation of the molten metal effects a useful stirring action in the melt. Channel induction furnaces are commonly used for melting low melting point alloys and or as a holding and superheating unit for higher melting point alloys such as cast iron. Channel induction furnaces can be used as holders for metal melted off peak in coreless induction induction units thereby reducing total melting costs by avoiding peak demand charges. Inductotherm removable crucible melting furnaces are quick and efficient nonferrous melters. For the greatest flexibility when changing alloys, Inductotherm offers several styles of removable crucible furnaces. Single, Double & Multiple Pushout Furnaces: The Double Push-Out furnace is about 8% more efficient than the lift-swing because its coils are tapered to the crucible shape for improved energy transfer and more even heating that extends crucible life. And, because power can be switched from one coil to the other in just seconds, thousands of additional castings per year can be obtained. Lift Swing Furnaces: The Lift-Swing furnace is a free-standing unit that installs right on the factory floor and is an excellent alternative to the push-out furnace when sub-surface conditions or foundation restrictions make it impractical to provide a pit for the push-out furnace’s cylinders. Heat treatment Induction heating is often used in the heat treatment of metal items. The most common applications are induction hardening of steelparts,induction soldering/brazing as a means of joining metal components and induction annealing to selectively soften a selected area of a steel part. Induction heating can produce high power densities which allow short interaction times to reach the required temperature. This gives tight control of the heating pattern with the pattern following the applied magnetic field quite closely and allows reduced thermal distortion and damage. This ability can be used in hardening to produce parts with varying properties. The most common hardening process is to produce a localised surface hardening of an area that needs wear-resistance, while retaining the toughness of the original structure as needed elsewhere. The depth of induction hardened patterns can be controlled through choice of induction-frequency, power-density and interaction time. There are limits to the flexibility of the process - mainly arising from the need to produce dedicated inductors for many applications. This is quite expensive and requires the marshalling of high current-densities in small copper inductors, which can require specialized engineering and 'copper-fitting'. Electric arc furnace An electric arc furnace (EAF) is a furnace that heats charged material by means of an electric arc. Arc furnaces range in size from small units of approximately one ton capacity (used in foundries for producingcast iron products) up to about 400 ton units used for secondary steelmaking. Arc furnaces used in research laboratories and by dentists may have a capacity of only a few dozen grams. Industrial electric arc furnace temperatures can be up to 1,800 ° C, (3272 °F) while laboratory units can exceed 3,000 °C. (5432 °F). Arc furnaces differ from induction furnaces in that the charge material is directly exposed to an electric arc, and the current in the furnace terminals passes through the charged material. History In the 19th century, a number of men had employed an electric arc to melt iron. Sir Humphry Davy conducted an experimental demonstration in 1810; welding was investigated by Pepys in 1815; Pinchon attempted to create an electrothermic furnace in 1853; and, in 1878–79, Sir William Siemens took out patents for electric furnaces of the arc type. The first electric arc furnaces were developed by Paul Héroult, of France, with a commercial plant established in the United States in 1907. The Sanderson brothers formed The Sanderson Brothers steel Co. in Syracuse, New York, installing the first electric arc furnace in the U.S.
Details
-
File Typepdf
-
Upload Time-
-
Content LanguagesEnglish
-
Upload UserAnonymous/Not logged-in
-
File Pages15 Page
-
File Size-