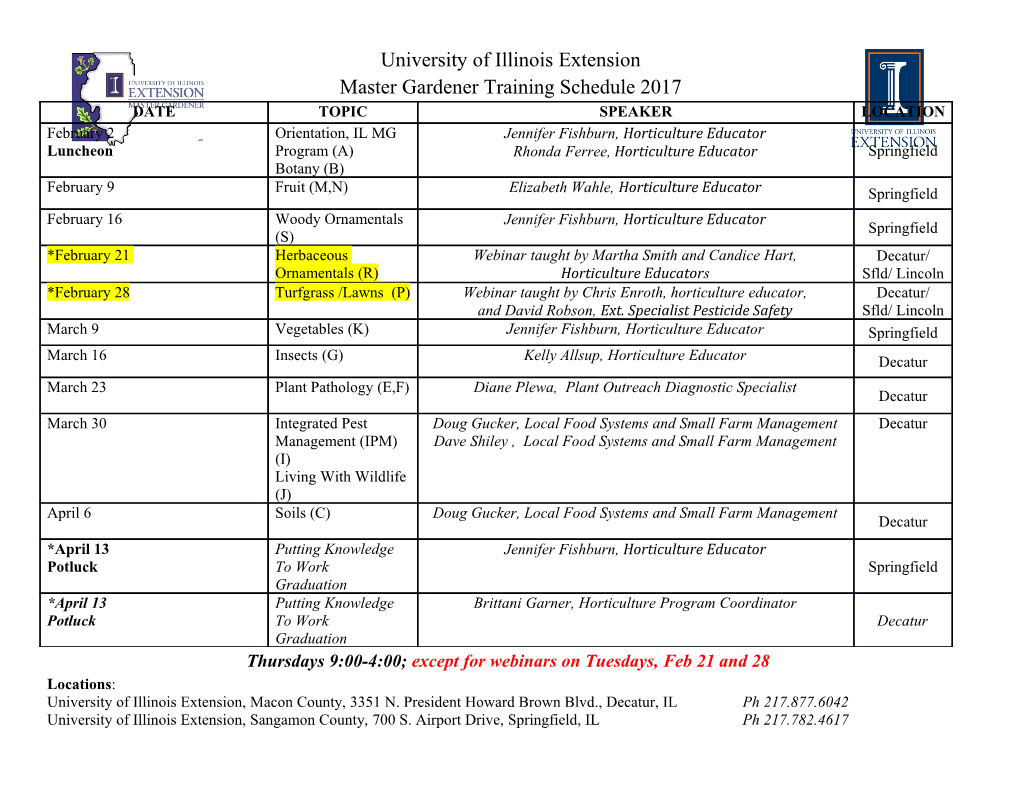
Linkoping Studies in Science and Technology Thesis No. 872 The Use of Platform Dampers to Reduce Turbine Blade Vibrations Martin H. Jareland INSTITUTE OF TECHNOLOGY LINKOPINOS UNIVERSITET Division of Machine Design Department of Mechanical Engineering LinkopingUniversity, SE-581 83 Linkoping, Sweden Linkoping2001 ISBN 91-7219-990-3 ISSN 0280-7971 LiU-TEK-LIC-2001:09 Printed in Sweden by UniTryck Linkoping, 2001 DISCLAIMER Portions of this document may be illegible in electronic image products. Images are produced from the best available original document. ABSTRACT Friction damping is commonly used in jet engines to reduce the vibration level of the blades and thereby increase the reliability of the engine. This thesis deals with a specific type of friction damper denoted platform damper, which is frequently used in turbine stages. A platform damper is a piece of metal located in a cavity underneath two adjacent blade platforms. It is pressed against the platforms by centrifugal force and friction forces arise in the contacts when a relative motion between the platforms occurs. In this thesis, a number of phenomena regarding platform dampers are investigated and discussed. This is performed both experimentally and theoretically. In the simulations, friction interface models valid for both macroslip and microslip are used. Macroslip means that slipping occurs in the whole contact interface and microslip means that slipping occurs in only part of the interface. The latter is most likely in the contacts between the platform damper and the blade platforms due to the high normal force and the small motions. The first paper deals with mistuning of bladed disks due to variations in the properties of the platform dampers and the closely related topic wear of the dampers. This study indicates that damper mistuning can greatly affect the blade vibrations and that damper and blade mistuning constitutes a more severe case than blade mistuning alone. It is also found that wear of the contact areas can lead either to an increase or decrease in the resonance amplitude of the blades in the studied configuration. In the second paper, so-called cottage-roof dampers are studied. Cottage-roof dampers are a type of platform damper with inclined contact surfaces. The inclination leads to a varying normal load, which complicates the analysis. A model including this effect is presented and simulations are performed both in the time and frequency domain. A parametric study is performed with the aim of finding the optimal damper design with respect to damper mass, inclination of contact surfaces, damper body stiffness and coefficient of friction. It is found that an increase in the inclination and the coefficient of friction results in a lower optimal damper mass, which is beneficial. The third paper presents a series of experiments performed for tuning a simulation model for a platform damper with curved contact areas. The model is tuned by selecting a suitable coefficient of friction and tangential stiffness for the friction interface model. A number of other topics are also investigated, such as repeatability of an experiment, comparison of new and used platform dampers and the change in surface structure on the contact areas. The overall conclusion is that wear of the contact areas probably leads to a decrease in the coefficient of friction, which implies a change in damper performance. i } PREFACE 'd This thesis is part of the research project “Friction damping of blade vibration. Part 2” carried out during the period January 1998 - December 2000 at the Division of Machine Design, Department of Mechanical Engineering, Linkoping University. The project was performed in co-operation with Volvo Aero Corporation, Trollhattan, and was financially supported by the National Aeronautical Research Program under grant NFFP-348. I am deeply grateful to my supervisor, Professor Karl-OIof Olsson, head of the Division of Machine Design for his encouragement and enthusiasm. I have appreciated all the interesting discussions we have had and the critical review of my work that he has performed. Dr Gabor Csaba, my project leader at Volvo Aero Corporation during 1998­ 1999, has supported and encouraged my work. I appreciate his great knowledge within the field of friction damping. Dr Gabor Csaba has also collaborated on Paper 1.1 would also like to thank Dr David Lindstrom, Volvo Aero Corporation, who has been my project leader during 2000. A great advantage in this research project has been access to experimental data A for validating the simulations. Mr Magnus Andersson and Mr Kent Holmedahl, Volvo Aero Corporation, have provided experimental data as well as many valuable answers to the questions that have arisen. I would also like to thank Mr Anthony Stanbridge, Imperial College, London, for his support and assistance during the experimental work presented in Paper HI. The reference group for my research project has provided a unique frame of i expertise and I wish to thank all the members of this group. I would like to thank all my colleagues at the Division of Machine Design for providing an inspiring and friendly environment. Dr Bjorn Larsson and Dr Hakan Wettergren have assisted in a large part of this work by acting as discussion \ partners and providing wide knowledge in the field of structural dynamics. I would also like to thank Dr Hakan Wettergren for his ability to see solutions to any kind of question. Finally, this thesis could not have been written without the support and encouragement given by my parents, my Ingela, my brother and my sister. I also like to thank all my friends for encouraging my research. , i Martin Jareland /j. Linkoping University February 2001 v im t CONTENTS Introduction 1 Jet engine 1 Blade design 2 Platform dampers 5 Modelling of friction interfaces 7 Simulation of bladed disk assemblies 11 Summary of Appended Papers 13 Paper I: Friction Damper Mistoning of a Bladed Disk and Optimization with Respect to Wear 13 Paper II: A Parametric Study of a Cottage-Roof Damper and Comparison with Experimental Results 13 Paper HI: Experimental Investigation of a Platform Damper with Curved Contact Areas 14 References 15 Appendix 17 Nomenclature 17 Paper I: 19 Friction Damper Mistiming of a Bladed Disk and Optimization with Respect to Wear Paper II: 43 A Parametric Study of a Cottage-Roof Damper and Comparison with Experimental Results Paper III: 67 Experimental Investigation of a Platform Damper with Curved Contact Areas APPENDED PAPERS Paper I: Jareland M. H., Csaba G., Friction Damper Mistiming of a Bladed Disk and Optimization with Respect to Wear, presented at ASME Turbo Expo ‘00, Munich, Germany, May 8-11 2000, paper 2000-GT-363 Paper II: Jareland M. H., A Parametric Study of a Cottage-Roof Damper and Comparison with Experimental Results, accepted for presentation at ASME Turbo Expo ‘01, New Orleans, Louisiana, USA, June 4-7 2001, paper 2001-GT-275 Paper III: Jareland M. H., Experimental Investigation of a Platform Damper with Curved Contact Areas, submitted to ASME 2001 Design Engineering Technical Conferences, Pittsburgh, Pennsylvania, USA, September 9-12 2001 Printing errors found in the original versions of the papers have been corrected and the layout of the text and figures has also been changed in some papers. 1 INTRODUCTION This chapter provides a short introduction to the field of blade vibrations in jet engines and the use of friction damping to control vibration levels. The most common types of friction damping device are presented and the simulation models most frequently used are discussed. JET ENGINE An example of a military jet engine is shown in Fig. 1. This engine, the RM12, is used in the Gripen fighter aircraft, manufactured by SAAB Aerospace, Linkoping, Sweden. It is based on the General Electric F404 and is further developed and manufactured by Volvo Aero Corporation, Trollhattan, Sweden. High pressure Low pressure Afterburner turbine turbine High pressure Exhaust ;1 Fan compressor Combustor nozzle Figure 1. The RM12 jet engine manufactured by Volvo Aero Corporationfor the Gripen fighteraircraft developed by SAAB Aerospace. The principle of a jet engine is that the inlet air is compressed by the fan and the high pressure compressor, see Fig. 1. Fuel is injected and the mix of air and fuel is •X burned in the combustor. The fan and compressor are driven by the turbines, which are powered by the exhaust from the combustor. The remaining exhaust passes out through the exhaust nozzle and generates the thrust that drives the aircraft forward. Some of the inlet air is only compressed in the fan and mixed with the exhaust after the turbines. The amount of air that is not active in the combustor is defined by the I 2 The Use of Platform Dampers to Reduce Turbine Blade Vibrations by-pass ratio. The military jet engine shown in Fig. 1 has a low by-pass ratio compared to commercial jet engines, which often have a high by-pass ratio. Military jet engines are commonly equipped with an afterburner, see Fig. 1. In this case, fuel is injected into the mix of exhaust and by-pass air, after the turbines. The mix is combusted in the afterburner, which leads to a significant increase in thrust and also fuel consumption. Guide vanes are located in front of each stage to control the flow. These may be fixed or variable. The guide vanes generate the main excitation mechanism of the blades, a periodic excitation force. This is also often referred as rotor/stator interaction. It is commonly assumed that the excitation force is monofrequent and that its angular velocity is a multiple of the angular velocity of the rotor. The number of excitation periods during one revolution of the bladed disk is denoted the engine order. The excitation force on an arbitrary blade, j, is given by the following expression e/o = (i) where Qa is the excitation force amplitude, co is the excitation frequency and cp is the interblade phase angle.
Details
-
File Typepdf
-
Upload Time-
-
Content LanguagesEnglish
-
Upload UserAnonymous/Not logged-in
-
File Pages28 Page
-
File Size-